B. Braun Allentown 939 Expansion Project
Strategic Partnership Agreement
Between
Occupational Safety and Health Administration
Allentown Area Office
And
Alvin H. Butz, Inc.
And
PA/OSHA Consultation Program
at
Indiana University of Pennsylvania
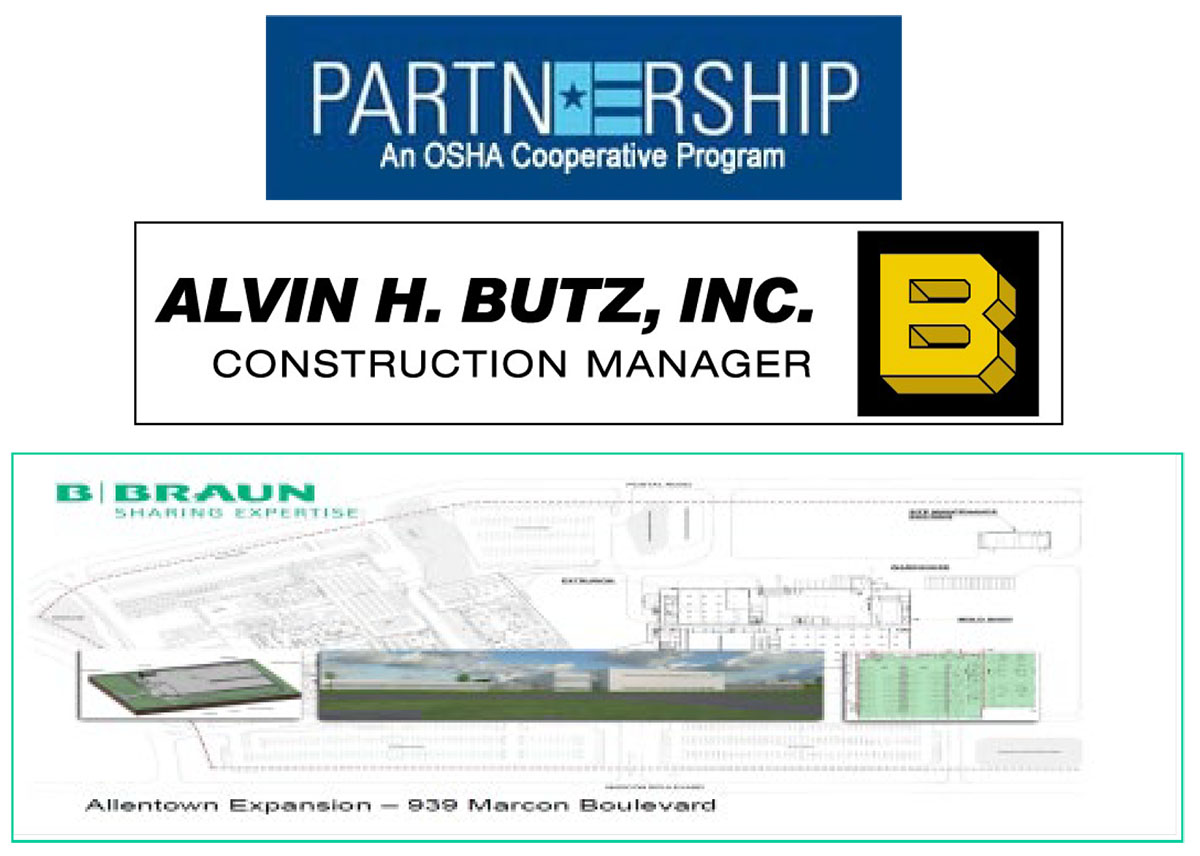
Partnership Agreement
-
General
The Allentown Area Office of the Occupational Safety and Health Administration (hereafter referred to as "OSHA") and Alvin H. Butz Inc., (hereafter referred to as "AHB"), have agreed to implement an OSHA Strategic Partnership (hereafter referred to as "Partnership") during construction of the B. Braun 939 Expansion Project (hereafter referred to as "Project").
The goal of this Partnership is to encourage joint cooperation between OSHA, AHB, OSHA Consultation Program and trade contractors to foster a safe work environment for all project employees.
The Partnership calls for the Project to be managed in accordance with OSHA's 1989 Safety and Health Management Guidelines or its equivalent. OSHA will provide timely responses to requests for information, requests for clarification of OSHA standards and assist as resources and/or OSHA Policy allow. To show their commitment to the Partnership, participating contractors will voluntarily sign a pledge (Appendix C).
This Partnership will not relieve any trade contractors from, lessen their safety responsibilities, nor change any contractual obligations between AHB, B. Braun (Owner), or trade contractor, nor does it lessen any/all affirmative defenses, legal rights or due process afforded with respect to OSHA enforcement action.
This Partnership will not in any way affect employees' ability to exercise rights under the Occupational Safety and Health ("OSH") Act and OSHA regulations. The Partnership supports OSHA's long-range effort to develop a contractor/government Partnership approach to safety management. It allows for better use of OSHA resources and for innovation in safety management, and it encourages more participation in the safety process by each stakeholder.
Partners recognize that it does not include any exemption from OSHA inspections or penalties. However, the contractors expect that OSHA will acknowledge superior performance by providing timely responses to requests for information and requests for clarification of OSHA standards.
-
Identification of Partners
The following organizations are the primary participants in this Partnership:
- Alvin H. Butz, Inc. ("AHB")
- Occupational Safety and Health Administration, Allentown Area Office ("OSHA")
- Pennsylvania OSHA Consultation at Indiana University of Pennsylvania ("PA OSHA Consultation")
The following organizations pledge to support this Partnership:
- Contractors and Subcontractors
- Union and Local Building Trades
-
Project Overview
The 939 Expansion Project is located at 939 Marcon Boulevard, Allentown, Pennsylvania. As previously described above this project will consist of the construction of a new manufacturing space, which will include a two-story office building with a Data Center, a single story pedestrian link to the existing manufacturing facility, and a two-story Injection Mold room (ISO 8 Clean Room). Additionally, there will be a two-story Extrusion facility, a single story Component Assembly room (also an ISO 8 Clean Room), a Warehouse, a Mold Shop and a standalone Maintenance building
Over the life of the project (approximately 24 months) contractors will employ approximately 400 individual construction tradespersons at peak construction. Site work has already involved demolition of unused structures, removal of existing concrete foundations, shoring of kept properties, building site preparation including micropiles, and removal of an existing data line. The new construction work will include site improvements including new buildings, parking area, road and walkway paving and utility services construction. Additionally, there will be some excavation, foundation installation, concrete end reinforcing steel installation, structural steel and miscellaneous metalwork, electrical, mechanical/plumbing, painting and other interiors finish work. The activities for this construction will incorporate the use of cranes, aerial and scissor lifts and other specialized construction tools and equipment.
-
Goals, Strategies, Measures
The primary objective of this Partnership is to create a working relationship that focuses on preventing work-related injuries and fatalities, controlling or eliminating serious workplace hazards, and establishing a foundation for the development of an effective safety and health program. The goals employed to achieve these results will include the following:
Goal Strategy Measures/Products 1. Reduce the total number of injury and illness cases, thereby providing a safer and healthier work environment for workers at the Project. - Review the OSHA 300 data of all project contractors on this project.
- Calculate the Project's Days Away From Work, Restricted, Or Job Transferred (DART) rate and Total Case Incident Rate (TCIR).
- Partners will meet quarterly to review injury and illness statistics and work together to resolve workplace safety and health issues and reduce injury and illnesses.
- The Partnership will use 2017 Bureau of Labor (BLS) baseline TCIR and DART rate of 3.1 and 1.8, respectively.
- Reduce the DART rate and TCIR rate each year of agreement.
- Quarterly meetings throughout the life of the Project.
2. Control workplace hazards by assisting contractors with the implementation of an effective safety and health management systems. - AHB will conduct evaluations of each trade contractor's safety and health management system in accordance with Appendix B.
The Partners will meet quarterly to review: - The number of trade contractors that have completed AHB's safety evaluation and have pledged both support and cooperation to the Partnership.
3. Conduct effective self-inspections, and assist trade contractors with training resources and technical assistance in areas where workers might be exposed to hazards. - AHB will document all self-inspections, the number of hazards corrected, and any additional safety training conducted by AHB or trade contractors for workers on this Project.
The Partners will meet quarterly to review: - The number of self-inspections performed, the number of hazards identified and corrected.
- The number of training sessions conducted and the number of training hours provided for workers and supervision.
4. Develop a working relationship with OSHA to maintain a continuing dialogue that supports various safety and health campaigns and initiatives. - AHB and all on-site participating contractors will hold an annual event to support the OSHA National Fall Prevention Safety Stand-Down (May) until the Project is completed. AHB and all participating trade contractors will display a stand-down poster (provided by the Allentown Area Office (AAO)) on site.
- AHB and all on-site participating trade contractors will hold an annual event (June) to support the NUCA Trench Safety Stand-Down until the Project is completed. AHB and all participating trade contractors will display the stand-down poster on the site.
- AHB and all on-site participating trade contractors will participate in the NIOSH/OSHA annual Heat Stress Prevention campaign (Friday before Memorial Day) until the Project is completed. AHB and all participating trade contractors will use the OSHA/NIOSH Heat Safety Tool App and display Heat Stress Prevention posters (provided by AAO) on site.
- AHB and all on-site participating trade contractors will participate in the OSHA Safe + Sound campaign (August) until the project is completed.
- AHB and all on-site participating trade contractors will participate in the Region III Focus Four Campaign (March through June).
The Partners will meet quarterly to verify and/or review: - The use of OSHA's "National Fall Safety Stand-Down" webpage to log their event, provide information about their stand-down activity and complete the survey.
- The use of NUCA's "National Trench Safety Stand-Down" webpage to log the event(s), provide information about their stand-down activity and complete the survey.
- The number of workers trained on the annual Heat Stress Prevention "Water, Rest, Shade" campaigns.
- The number of workers trained and/or participate in the Safe + Sound annual campaign.
- The number of workers trained in each safety talk that is associated with the Region III Focus Four Campaign.
-
Partnership Management and Operation
A Partnership committee will be formed to manage the operation of this Partnership agreement. It will consist of the AHB Representatives, the OSHA Compliance Assistance Specialist, and as resources permit a representative from the OSHA Consultation Program. The AHB Site Safety Director will serve as the chairperson and will serve as OSHA's primary contact. The AHB Site Safety Director will review contractor compliance and involvement in the Partnership, analyzes job site audits, make Partnership improvements, evaluate Partnership modifications, achievements and success. The AHB Site Safety Director will have the authority to ensure safety and health corrections and to shut down operations that pose an imminent danger risk.
AHB agrees to:
- Serve as a safety resource in support of all of the Project's subcontractors and tiered subcontractors.
- Provide notice to all subcontractors and tiered subcontractors that the 939 Expansion Project is subject to this strategic Partnership with OSHA. All employees will be informed of the Partnership and provided a fact sheet during orientation. (Appendix A).
- Administer the overall Partnership program including, but not limited to, the initial contact and evaluation of subcontractor applications to determine whether the subcontractor meets the criteria specified within this Partnership initiative under Section VI, Contractor Eligibility.
- Notify the Allentown OSHA Area Office on a regular and recurring basis of the names of subcontractors that have met the Partnership criteria.
- Maintain a dedicated competent Site Safety and Health Coordinator available to assist subcontractors and tiered subcontractors with all safety and health issues.
- Act as liaison for subcontractors with OSHA.
- Offer on-going information on safety or health topics of importance for subcontractors, especially on the focused four construction hazards. The focused four construction hazards are falls; caught-in or between; struck-by; and electrocutions.
- Provide OSHA's interpretations of standards so that subcontractors may better understand and properly comply with standards.
- Maintain a site injury and illness log of all injuries and illnesses reported by all subcontractors and tiered subcontractors.
- Meet with OSHA quarterly to examine the injury and illness data of the worksite and to make corrections and adjustments as needed.
- Manage the following site safety or health issues common to all areas of the site and be accessible to all subcontractors and tiered subcontractors to reduce the potential for injury or illness in accordance with this Partnership agreement:
- emergency action plan
- hazard communication plan and inventory of site chemicals reported by subcontractors and tiered subcontractors
- fall protection plan and perimeter guards
- personal protective equipment, including equipment specified by National Fire Protection Association (NFPA) 70 E, where applicable
- Assist in promoting OSHA's national and regional safety and health campaign efforts by hosting activities or promoting the ongoing dialogue during the duration of this Partnership agreement that support the initiatives, including but not limited to:
NOTE: Anniversary dates for the campaigns and initiatives listed above are subject to change. OSHA will provide AHB with dates that correspond with the campaigns and initiatives are official.
- Regional focus:
- regional focus four campaign which address fall, struck-by, caught-in between and electrical hazards and is conducted from March through June
- National annual campaigns and initiatives:
- ladder safety month, March
- national work zone awareness week, which during the first year of this agreement is April 8 - 12, 2019,
- national fall hazard campaign, which during the first year of this agreement is being held May 6 - 11, 2019,
- national heat illness prevention campaign, which during the first year of this agreement is being held on Friday, May 24, 2019 ("No-Fry Day"),
- national trench safety initiative, which during the first year of this agreement is being held June 17 - 22, 2019,
- national safe and sound campaign, which during the first year of this agreement is being held August 12 - 18, 2019,
- Regional focus:
AHB and its subcontractors and tiered subcontractors agree:
- To apply all relevant components of their respective comprehensive safety and health programs to the 939 Expansion Project. These programs shall include:
- Analysis of all new and acquired work, materials, chemicals, and equipment before construction activity begins to determine potential hazards and to plan for their prevention or control.
- Routine examination and analysis of hazards associated with individual jobs, processes, or phases of construction.
- Routine self-inspections and hazard abatement.
- A reporting system for project workers to notify management, without fear of retaliation, about conditions that appear hazardous.
- A system for investigating accidents and near misses, including procedures for guidance, reports of findings and the tracking of hazard correction to completion.
- A system to analyze trends through a review of site injury and illness data, and the hazards identified through inspections so that patterns of common causes can be identified and eliminated.
- To comply with all current OSHA standards.
- To implement and enforce a 6 foot fall protection policy.
- To have supervisors provide visible leadership in implementing the safety and health program. This includes:
- Establishing clear lines of communication with project workers.
- Setting an example of safe and healthful behavior.
- Creating an environment that allows project workers access to their top management and for tiered subcontractor management to have access to AHB's management.
- To report all site injuries and illnesses to AHB immediately so that the site injury and illness log may be accurately maintained.
- To report all program deficiencies or damage to protective equipment, specifically site fall protection, immediately upon discovery and to take appropriate interim protective measures for protection of their employees
- All subcontractors and tiered subcontractors will submit to AHB, at least monthly, records of their site recordable injury and illness rates, days away from work rates, restricted workdays, and the subcontractor's and tiered subcontractor's OSHA history.
- All subcontractors and tiered subcontractors must have a person on site that is responsible for, possesses the authority over, and is capable of effectively implementing the overall site safety and health program.
- All subcontractors and tiered subcontractors must complete a successful assessment of their site safety and health program. This assessment shall consider:
- the comprehensiveness of the program
- the degree to which it has been implemented
- the presence of competent persons as required by relevant standards
- the means by which the program is enforced
- Verify that a comprehensive written safety and health program exists or that it will be implemented prior to the starting work, which is at least equivalent to the criteria referenced within the AHB Site-Specific Safety, Health and Management Plan. The plan must include the subcontractors and tiered subcontractor's implementation of policies and procedures to ensure that safety rules and procedures are enforced at the site.
- Confirm that the written safety and health program holds supervisors and workers accountable for following established safety and health rules (per AHB's written Site-Specific Safety, Health and Management Program) and OSHA regulations. If this element is deficient or missing and until documented modifications are-made to the written program, the AHB site-specific policies will be followed.
- Ensure that employee training covers the applicable site hazards (as referenced in the Site-Specific Safety, Health and Management Plan) and the means to correct them, as well as pertinent standards and regulations. Provide appropriate safety information and training to non-English speaking employees in their native language.
- Strive to ensure that within one year after obtaining acceptance into this Partnership program that a designated safety representative or other person serving in the capacity as a competent person on the project will have completed the OSHA 10-hour course for the construction industry (or its equivalent).
- Provide safety related data or statistics, as requested, concerning such issues as hours worked, OSHA recordable injuries and illnesses, including but not limited to: cases involving days away from work and/or restricted work activity and medical treatment cases, accident records and OSHA inspection results. AHB will provide a summary of and analysis of pertinent safety and health related information for review by OSHA. The purpose of such summary information will assist in preparing an annual report necessary for the evaluating the merits of the program and making recommendations for continuous improvement.
- Emergency response procedures will be in written form and then communicated to the 939 Expansion Project workers and site visitors. The procedures will list emergency telephone numbers, emergency routes, emergency exits, staging (muster) areas, requirements for personal protective equipment, training and evacuation drills.
OSHA agrees to:
- Help identify programmatic needs at this site by reviewing the documented safety and health management system and providing practical guidance for implementation. The review will be performed by AHB Site Safety Director (or other AHB Safety Representative) and a Compliance Assistance Specialist (CAS).
- Help identify, through the review of OSHA 300 logs, accident or near miss reports, primary causal factors in injuries and illnesses, in particular the four top hazards at this site, and recommend the appropriate corrective actions.
- Provide information on training resources including available OSHA Training Institute courses and information on other available sources of training.
- Assist partners in accessing OSHA interpretations and clarifications as to the meaning and application of OSHA standards and policy.
- Participate in training sessions and meetings, as resources permit.
- Designate an experienced safety and health specialist (Allentown Area Office CAS and/or Assistant Area Director) to serve as a resource and liaison person for the Partnership.
- Meet with AHB quarterly to review Partnership issues and to examine updated TCIR and DART rates as well as the focused four injury and illness experiences of AHB and its subcontractors at this site. OSHA shall provide feedback on any noted incident trends and patterns.
PA OSHA Consultation agrees to:
- Meet with AHB quarterly, as resources permit, to review Partnership issues and to examine updated TCIR and DART rates as well as the focused four injury and illness experiences of AHB and its subcontractors at this site. PA OSHA Consultation shall provide feedback on any noted incident trends and patterns. Efforts will be made to conduct these site visits with the OSHA non-enforcement verification visits.
- PA OSHA Consultation will strive to ensure that any subcontractor (and/or tiered subcontractor) who requests the services from the OSHA funded free consultation program (through their prime contractor (AHB)) will receive priority service. This service is part of the PA OSHA Consultation program and can be requested by calling 1-800-382-1241.
-
Contractor Eligibility
Subcontractors wishing to take advantage of this opportunity to partner with OSHA must:
- Sign a letter of agreement (Pledge) with AHB indicating their intent to participate in this Partnership initiative and to take steps to adopt into their safety program all of the provisions of the Partnership agreement. Appendix C.
- Verify that a comprehensive written safety and health program exists or will be implemented within 30 days of signing which is based on the OSHA 1989 Safety and Health Program Management Guidelines (or their equivalent), and has site specific safety plans for all of the contractor's work sites.
- Certify that their policy and procedures hold supervisors and workers accountable for established safety rules and OSHA regulations.
- Provide the level of training required by OSHA regulations to their workers through their own training personnel or other consultants or trainers.
- Provide periodic safety-related statistics (jobsite hours worked, injury and illness data, including, recordable and first aid incidents, accident records and OSHA inspection results). AHB is to provide a summary and analysis for review by OSHA to track the progress of the Partnership in meeting its goals to reduce injury and illness rates and to prepare an annual report to evaluate the merits of the Partnership.
-
OSHA Onsite Verification and Inspections
-
OSHA Non-enforcement Verification
In order to assist in measuring the success of this Partnership, a non-enforcement verification consisting of a review of the written program elements and site visit, will be conducted after the signing of this agreement.
After the initial non-enforcement, quarterly non-enforcement verification visits will focus on the most serious hazards that have been previously identified pursuant to the procedure herein.
OSHA will meet with AHB quarterly to review Partnership issues and to examine updated TCIR and DART rates and the injury and illness experience of AHB and its subcontractors at this site. OSHA shall provide feedback on any noted incident trends and patterns.
-
OSHA Inspections and/or Investigations
This Partnership provides for the timely response to each allegation of a safety or health hazard brought to each contractor's attention by any person. Upon a finding that an allegation is valid, the responsible trade contractor shall promptly abate the hazard.
OSHA agrees that a copy of each non-formal complaint related to the Project and filed with OSHA will be forwarded by fax or mail to the Project office. In accordance with applicable law, the identity of a complainant requesting confidentiality will not be revealed. AHB agrees to investigate these complaints regardless of the contractor involved and provide OSHA with a written response within five working days of receiving the non-formal complaint/referral.
OSHA personnel will continue to conduct investigations and inspections in any event or circumstance that may warrant the opening of an OSHA inspection, pursuant to the policy set forth in Field Operations Manual (FOM). These may include but are not limited to local or national emphasis programs, formal complaints, referrals, fatalities, catastrophes, or other accidents or significant events. OSHA will also investigate contractors whose employees are exposed to or are creating plain view hazards at the Project. These investigations will be conducted outside of this Partnership agreement in accordance with established OSHA enforcement policy. Violations documented during such investigations may result in the issuance of citations and penalties. OSHA reserves the right to issue citations and penalties for violations including but not limited to regulatory violations for which mandatory penalties are established.
-
-
Employee and Employer Rights and Responsibilities
This Partnership does not preclude employees and/or employers from exercising any right provided under the OSH Act (or, for federal employees, 29 CFR 1960), nor does it abrogate any responsibility to comply with rules and regulations adopted pursuant to the OSH Act.
-
Leveraging
This Partnership seeks to leverage the resources of both AHB and OSHA by encouraging subcontractors to develop safety and health programs, implement them in an effective manner, complete self-inspections, and evaluate worksite conditions and near misses to prevent accidents. By combining resources, AHB and OSHA expect to have a greater and more positive impact on safe working conditions at this site than could be achieved otherwise.
-
Annual Evaluation
The partners will prepare a joint evaluation of the Partnership annually. The evaluation will review the success of the Partnership, lessons learned, and changes that will be made to meet the goals of the Partnership. The annual performance evaluation report format from Appendix C of the OSHA Strategic Partnership Program (OSPP) Directive CSP 03-02-003, dated November 6, 2013, will be used (see Appendix D of this agreement). Performance measures listed in the goals and objectives section of this agreement will be collected and analyzed to determine the Partnership's progress toward meeting its goals.
-
Term of Partnership
This agreement will terminate two years from the date of the signing or upon completion of the 939 Expansion Project. If either OSHA or AHB wishes to withdraw its participation prior to the established termination date, the agreement will terminate upon receiving a written notice of the intent to withdraw from either signatory.
OSHA will terminate the Partnership if any participant employer is issued a citation related to workplace hazards which resulted in a fatality.
-
Paperwork Reduction Act
OSHA Strategic Partnerships are part of OSHA's available voluntary cooperative programs. As per the Paperwork Reduction Act of 1995 (PRA OMB CONTROL NO. 1218-0244, expires March 31, 2019), the public reporting burden for this Partnership's collection of information is estimated at 11 hours per participant, per year. If you have any comments regarding this collection of information, including suggestions for reducing the burden or revising the burden estimate, please direct them to:
Occupational Safety and Health Administration
Attention: Director, Office of Partnerships and Recognition
Directorate of Cooperative and State Programs
200 Constitution Avenue, NW - Room N3700
Washington, DC 20210 -
Primary Partnership Contacts
Scott G. Shimandle
Compliance Assistance Specialist
USDOL/OSHA
Allentown Area Office
Stabler Corporate Center
3477 Corporate Parkway, Suite 120
Center Valley, Pa 18034
Office Phone: (267) 429-7542Craig K. Berrier
Safety Director
Alvin H. Butz, Inc.
840 Hamilton Street, Suite 600
P.O. Box 509
Allentown, Pa 18105-0509
Phone: (610) 395-6871
Cell Phone: (484) 225-4577
Signature Page
B. Braun 939 Expansion Project
Strategic Partnership Agreement between OSHA, AHB and PA/OSHA Consultation Program
All undersigned Parties mutually agree to the terms and conditions of this document and commencement of this Partnership Agreement.
Date:__________________________
- Jean G. Kulp, CIH
- Area Director
- USDOL/OSHA
- Allentown Area Office
Date:__________________________
- John M. Mulroy, CSP
- Director
- PA OSHA Consultation Program
- Indiana University of Pennsylvania
Date:__________________________
- Greg L. Butz
- President and Chief Executive Officer
- Alvin H. Butz, Inc.
APPENDIX A
939 Expansion Project
Strategic Partnership Fact Sheet
A strategic Partnership agreement has been developed by the United States Department of Labor, Occupational Safety and Health Administration - Allentown Area Office ("OSHA"), Alvin H. Butz, Inc. ("AHB") and the Pennsylvania OSHA Consultation Program at Indiana University of PA.
The goal of this Partnership is to encourage cooperation between OSHA, AHB, OSHA Consultation and trade contractors to foster a safe work environment for all project employees as described in this Partnership.
The Partnership between AHB and OSHA calls for the Project to be managed in accordance with OSHA's 1989 Safety and Health Management Guidelines or its equivalent.
OSHA will provide timely responses to requests for information, requests for clarification of OSHA standards and other assistance as resources and/or OSHA Policy allow. To show their commitment to the Partnership, contractors will voluntarily sign a pledge (Appendix C).
This Partnership will not relieve any trade contractors from or lessen their safety responsibilities nor change any contractual obligations between AHB, Project Owner (B. Braun), or trade contractor, nor does it lessen any/all affirmative defenses, legal rights or due process afforded with respect to OSHA enforcement action.
This Partnership will not in any way affect employees' ability to exercise their rights under the OSH Act and OSHA regulations.
This agreement supports OSHA's long-range effort to develop a contractor and government Partnership approach to safety management. It allows for better use of OSHA resources and for innovation in safety management, and it encourages more participation in the safety process by each stakeholder.
APPENDIX B
Safety and Health Program Evaluation
- Contractor has implemented a comprehensive written safety and health program based on ANSI A10.38-1991 or the OSHA 1989 Safety and Health Program Management Guidelines, and has site-specific safety plans for all of the contractor's work sites.
- Contractor maintains a copy of its specialty contractor's safety and health plan, hazard communication plan, and fall protection plan (where applicable) or contractor requires specialty contractor to follow participant's plan.
- Contractor has designated safety personnel at each site who conduct documented safety inspections of all work on the contractor's projects, and through training and experience, can recognize hazards and have authority to take prompt corrective action.
- Contractor has trained all field supervisory personnel and has provided additional training for competent persons in such areas as scaffolding, excavation, fall protection, crane operations, etc. (This additional training will be dictated by the type and scope of the work the contractor routinely conducts).
- Contractor provides a safety and health program orientation for all new employees and trains employees for hazard recognition specific to the contractor's work sites.
- Contractor has evidence of employee involvement including, but not limited to, participation in self-audits, site inspections, job hazard analyses, safety and health program reviews, safety training and mishap investigations.
- Contractor conducts and documents weekly employee safety meetings.
- Contractor conducts and documents self-audits.
- Contractor uses a six-foot fall protection policy.
- Contractor has a written enforcement program.
APPENDIX C
LETTER OF INTENT TO PARTICIPATE (PLEDGE)
939 EXPANSION PROJECT - STRATEGIC PARTNERSHIP
Name of Subcontractor:______________________________________________________________________________________
Subcontractor Site Representative:_____________________________________________________________________________
Anticipated Number of Workers:________________________________________________________________________________
We have read the requirements to participate in the 939 Expansion Project Strategic Partnership and agree with all aspects of the program, including the submission of the required information. Specifically, we recognize the need to meet the following requirements:
- Establishment of a written safety and health program including the following elements: management leadership, worker involvement, worksite analysis, hazard prevention and control, and safety and health training.
- Compliance with all current OSHA standards.
- Provision of visible leadership by supervisors in implementing the safety and health program.
- Planning for safety and health as part of the overall management planning process, including the development of appropriate job safety analyses for high hazard work, as defined in the Site-Specific Safety, Health and Management Program for this project.
- Establishment and communication of all safety and health program responsibilities to all project workers.
- Evaluation of safety and health programs at least annually.
- Reporting all site injuries and illnesses so that a site log may be maintained.
- Reporting all deficiencies or damage to site wide programs or protective measures, specifically site fall protection, immediately upon discovery and taking appropriate interim protective measures for protection of their employees.
Based upon the mutual interest to protect construction workers at the 939 Expansion Project, we agree to the terms of the OSHA Partnership Agreement.
Signed this __________ day of ____________________________
Name (PRINT): _____________________________ Signature: _________________________________
Appendix D
OSHA Strategic Partnership Program
Annual Partnership Evaluation Report
Partnership Name | ||
Purpose of Partnership | ||
Goals of Partnership | ||
Goal | Strategy | Measure |
Anticipated Outcomes | ||
Strategic Management Plan Target Areas (check one) | |||
Construction | X | Amputations in Manufacturing | |
Non-Construction | |||
Strategic Management Plan Areas of Emphasis (check all applicable) | |||
Amputations in Construction | Oil and Gas Field Services | ||
Blast Furnaces and Basic Steel Products | Preserve Fruits and Vegetables | ||
Blood Lead Levels | Public Warehousing and Storage | ||
Concrete, Gypsum and Plaster Products | Ship/Boat Building and Repair | ||
Ergo/Musculoskeletal | Silica-Related Disease | X | |
Landscaping/Horticultural Services |
Section 1 General Partnership Information
Date of Evaluation Report | |||
Evaluation Period: | |||
Start Date |
End Date |
Evaluation Contact Person | |||
Originating Office |
Partnership Coverage | |||
# Active Employers | # Active Employees | ||
|
Industry Coverage (note range or specific SIC and NAICS for each partner) | |||
Partner | SIC | NAICS | |
|
Section 2 Activities Performed
Note whether an activity was required by the OSP and whether it was performed | ||||
Required | Performed | |||
a. Training |
X |
|||
b. Consultation Visits | ||||
c. Safety and Health Management Systems Reviewed/Developed |
X |
|||
d. Technical Assistance |
X |
|||
e. VPP-Focused Activities | ||||
f. OSHA Enforcement Inspections | ||||
g. Offsite Verifications | ||||
h. Onsite Non-Enforcement Interactions |
X |
|||
i. Participant Self-Inspections |
X |
|||
j. Other Activities |
2a. Training (if performed, provide the following totals) | ||||
Training sessions conducted by OSHA staff | ||||
Training sessions conducted by non-OSHA staff | ||||
Employees trained | ||||
Training hours provided to employees | ||||
Supervisors/managers trained | ||||
Training hours provided to supervisors/managers | ||||
Comments/Explanations (briefly describe activities, or explain if activity required but not performed) | ||||
|
2b. Consultation Visits (if performed, provide the following total) | ||||
Consultation visits to partner sites | ||||
Comments/Explanations (briefly describe activities, or explain if activity required but not performed) | ||||
|
2c. Safety and Health Management Systems (if performed, provide the following total) | ||||
Systems implemented or improved using the 1989 Guidelines as a model | ||||
Comments/Explanations (briefly describe activities, or explain if activity required but not performed) | ||||
|
2d. Technical Assistance (if performed, note type and by whom) | ||||
Provided by OSHA Staff | Provided by Partners | Provided by Other Party | ||
Conference/Seminar Participation | ||||
Interpretation/Explanation of Standards or OSHA Policy | ||||
Abatement Assistance | ||||
Speeches | ||||
Other (specify) | ||||
Comments/Explanations (briefly describe activities, or explain if activity required but not performed) | ||||
|
2e. VPP-Focused Activities (if performed, provide the following totals) | ||||
Partners/participants actively seeking VPP participation | ||||
Applications submitted | ||||
VPP participants | ||||
Comments/Explanations (briefly describe activities, or explain if activity required but not performed) | ||||
|
2f. OSHA Enforcement Activity (if performed, provide the following totals for any programmed, unprogrammed, and verification-related inspections) | ||||
OSHA enforcement inspections conducted | ||||
OSHA enforcement inspections in compliance | ||||
OSHA enforcement inspections with violations cited | ||||
Average number of citations classified as Serious, Repeat, and Willful | ||||
Comments/Explanations (briefly describe activities, or explain if activity required but not performed) | ||||
|
2g. Offsite Verification (if performed provide the following total) | ||||
Offsite verifications performed | ||||
Comments/Explanations (briefly describe activities, or explain if activity required but not performed) | ||||
|
2h. Onsite Non-Enforcement Verification (if performed provide the following total) | ||||
Onsite non-enforcement verifications performed | ||||
Comments/Explanations (briefly describe activities, or explain if activity required but not performed) | ||||
|
2i. Participant Self-Inspections (if performed provide the following totals) | ||||
Self-inspections performed | ||||
Hazards and/or violations identified and corrected/abated | ||||
Comments/Explanations (briefly describe activities, or explain if activity required but not performed) | ||||
|
2j. Other Activities (briefly describe other activities performed) | ||||
|
Section 3 Illness and Injury Information
Year |
Hours |
Total Cases |
TCIR |
# of Days Away from Work Restricted and Transferred Activity Cases |
DART |
2019 |
|||||
2020 |
|||||
2021 |
|||||
Total | |||||
Two-Year Rate (2019-2021) | |||||
BLS National Average for 2017 (NAICS 236) | 3.1 | 1.8 | |||
Baseline | 3.1 | 1.8 |
Comments | |||||
|
Section 4 Partnership Plans, Benefits, and Recommendations
Changes and Challenges (check all applicable) | ||
Changes | Challenges | |
Management Structure | ||
Participants | ||
Data Collection | ||
Employee Involvement | ||
OSHA Enforcement Inspections | ||
Partnership Outreach | ||
Training | ||
Other (specify) | ||
Comments | ||
|
Plans to Improve (check all applicable) | ||
Improvements | N/A | |
Meet more often | ||
Improve data collection | ||
Conduct more training | ||
Change goals | ||
Comments | ||
|
Partnership Benefits (check all applicable) | ||
Increased safety and health awareness | ||
Improved relationship with OSHA | ||
Improved relationship with employers | ||
Improved relationship with employees or unions | ||
Increased number of participants | ||
Other (specify) | ||
Comments | ||
|
Status Recommendations (check one) | |
Partnership Completed | |
Continue/Renew | |
Continue with the following provisions: | |
Terminate (provide explanation) | |