Oil and Gas Industry Workers and Employers
Given the evolving nature of the pandemic, OSHA is in the process of reviewing and updating this document. These materials may no longer represent current OSHA recommendations and guidance. For the most up-to-date information, consult Protecting Workers Guidance.
This guidance is not a standard or regulation, and it creates no new legal obligations. It contains recommendations as well as descriptions of mandatory safety and health standards. The recommendations are advisory in nature, informational in content, and are intended to assist employers in providing a safe and healthful workplace. The Occupational Safety and Health Act requires employers to comply with safety and health standards and regulations promulgated by OSHA or by a state with an OSHA-approved state plan. In addition, the Act's General Duty Clause, Section 5(a)(1), requires employers to provide their employees with a workplace free from recognized hazards likely to cause death or serious physical harm.
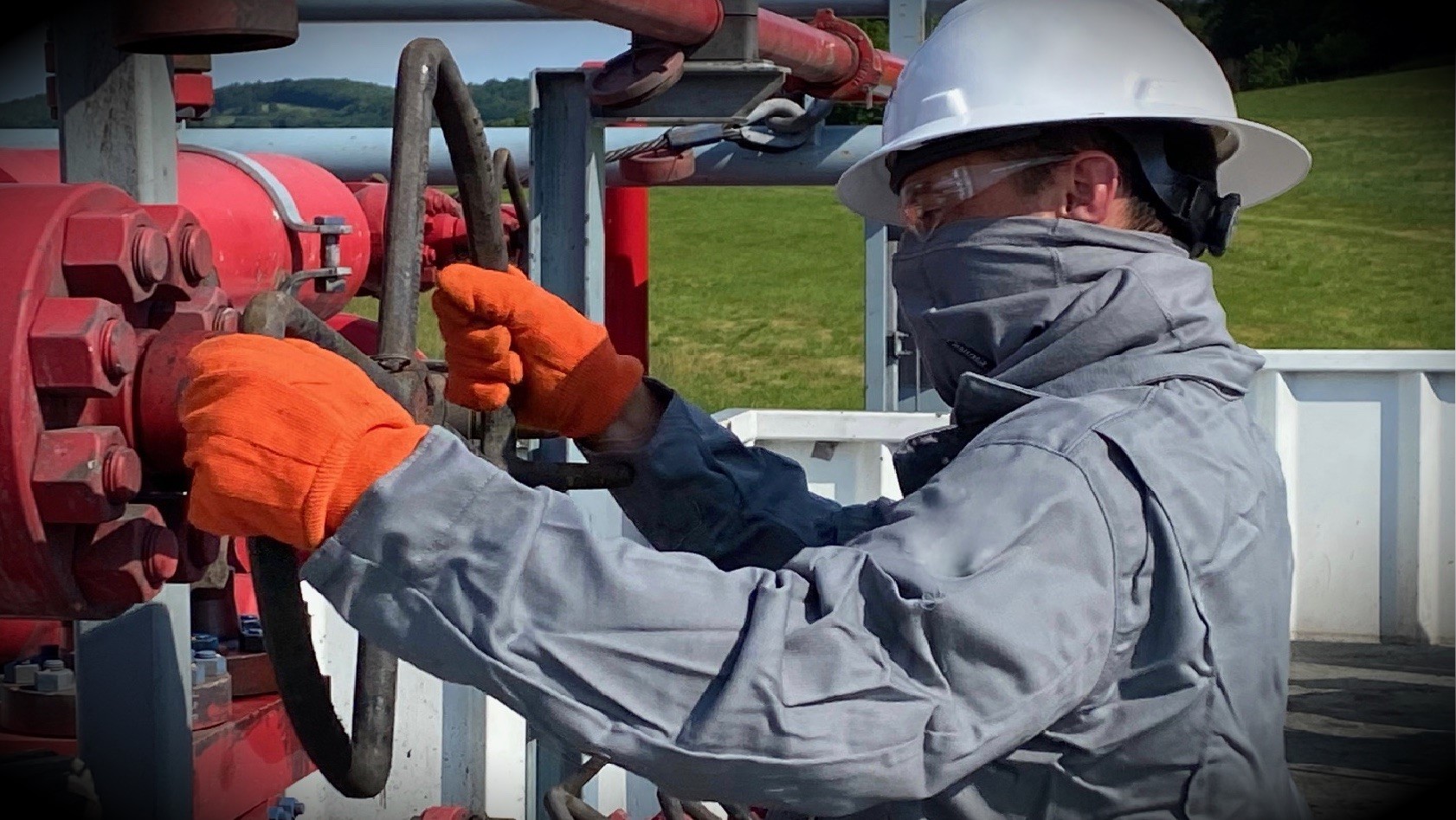
This page provides guidance for oil and gas industry workers and employers – including those in the sub-industries and tasks that make up the broader oil and gas industrial sector (see Table 1). This guidance supplements the general interim guidance for workers and employers of workers at increased risk of occupational exposure to SARS-CoV-2.
For the most up-to-date information on OSHA’s guidance see Protecting Workers: Guidance on Mitigating and Preventing the Spread of COVID-19 in the Workplace.
Assess the hazards to which your workers may be exposed; evaluate the risk of exposure; and select, implement, and ensure workers use the hierarchy of controls to prevent exposure. The table below describes oil and gas work tasks associated with the exposure risk levels in OSHA's occupational exposure risk pyramid, which may serve as a guide to employers in this sector.
Examples of oil and gas work tasks associated with exposure risk levels
Lower (caution) |
Medium |
High |
Very High |
---|---|---|---|
Note: For activities in the lower (caution) risk category, OSHA's Interim Guidance for Workers and Employers of Workers at Lower Risk of Exposure may be most appropriate. |
Note: Working and living together in close quarters where social distancing is not always feasible may increase exposure risk compared to other activities in this category. |
Note: Most oil and gas drilling, servicing, production, distribution, and/or processing tasks are associated with lower or medium exposure risks; see the other columns of this chart. |
Note: Most oil and gas drilling, servicing, production, distribution, and/or processing tasks are associated with lower or medium exposure risks; see the other columns of this chart.
|
Conducting a hazard assessment (sometimes called a job hazard analysis) can help you to determine whether work activities require close contact (within six feet) between workers and other people (e.g., coworkers, supervisors, or others at the job site). When a hazard assessment identifies activities with higher exposure risks, and those activities are not essential, consider delaying them until they can be performed safely (e.g., when appropriate infection prevention measures, as discussed on this page, can be implemented or once community transmission subsides).
Further guidance for employers and workers in oil and gas, including refinery, operations can be found in the Interim Guidance from CDC and OSHA for Manufacturing Workers and Employers. The manufacturing guidance applies generally to all types of manufacturing operations, of which some operations in the oil and gas industry, are a part.
Engineering Controls
Current information about the asymptomatic spread of SARS-CoV-2 supports the need for social distancing and other protective measures (including those described on this page) within an oil and gas production or processing work environment. Changes in production practices may be necessary in order to maintain appropriate distances among workers.
Configure communal work environments (such as control rooms, jobsite trailers and/or doghouses) so that workers are spaced at least six feet apart, if possible.
Modify the alignment of workstations, including control panels/boards, if feasible, so that workers are at least six feet apart in all directions (e.g., side-to-side and when facing one another). Ideally, modify the alignment of workstations so that workers do not face one another and can still maintain communications. Consider using markings and signs to remind workers to maintain their location at their station away from each other and practice social distancing on breaks.
Use physical barriers, such as strip curtains, plexiglass, or other impermeable dividers or partitions, to separate workers from each other, if feasible, and where doing so does not create additional safety hazards (e.g., reduced visibility in/around work vehicles or other equipment).
Facilities should consider consulting with a heating, ventilation, and air conditioning engineer to ensure adequate ventilation in work areas to help minimize workers' potential exposures. Opening windows, when possible, is a simple measure that can help disperse and dilute any virus that might be present in the air.
If fans, such as pedestal fans or hard mounted fans, are used in the facility, take steps to minimize air from fans blowing from one worker directly at another worker. Personal cooling fans should be removed from the workplace to reduce the potential spread of any airborne or aerosolized SARS-CoV-2. If fans are removed, employers should be aware of, and take steps to prevent heat hazards.
Administrative Controls
Use administrative controls, when feasible, to reduce or eliminate the risk of exposure. Additionally, employers should do the following, if possible, to promote social distancing:
- Stagger workers' arrival and departure times to avoid congregations of workers in parking areas, locker and shower rooms, smoking areas, control rooms and other common areas.
- Encourage s single-file movement with six feet between each worker through the facility/site, where possible.
- Provide visual cues (e.g., floor markings, signs) as a reminder to workers to maintain social distancing (six feet).
- Designate workers to monitor and facilitate distancing.
- Limit the number of personnel allowed in doghouses, control rooms, and other operating areas.
- Limit meeting sizes and/or hold meetings virtually or using social distancing outside, if possible.
- Stagger break times or provide temporary break areas, including for water breaks, and restrooms to avoid groups of workers gathering during breaks. Workers should maintain at least six feet of distance from others at all times, including on breaks.
- Remove or rearrange chairs and tables, or add partitions to tables, in break rooms, control rooms, and other areas workers may frequent to increase worker separation. Identify alternative areas to accommodate overflow volume, such as training and conference rooms, or using outside tents for shaded break and lunch areas.
- Encourage workers to avoid carpooling to and from work and job sites.
- If carpooling or using company shuttle vehicles is a necessity for workers, the following control practices should be used:
- Limit the number of people per vehicle as much as possible. This may mean using more vehicles and increasing the frequency of trips.
- Encourage cohorting (grouping together) of workers to keep exposure groups as small as possible.
- Encourage workers to maintain social distancing as much as possible.
- Encourage workers to practice proper hand hygiene, such as hand washing or, if soap and water are not readily available, use hand sanitizer that contains at least 60% alcohol, before entering the vehicle and when arriving at the destination.
- Encourage workers to open vehicle windows when possible.
- Encourage workers in a shared van or car space to wear cloth face coverings.
- Make hand hygiene facilities and/or supplies available and encourage workers to use them before entering and upon exiting shared vehicles.
- Clean and disinfect commonly touched surfaces after each carpool or shuttle trip (e.g., door handles, handrails, seatbelt buckles).
- Encourage workers to follow coughing and sneezing etiquette when in the vehicle.
- If carpooling or using company shuttle vehicles is a necessity for workers, the following control practices should be used:
Consider cohorting workers into shifts and shared shuttle vehicle assignments. Keeping the same group of workers assigned to the same shift may reduce the spread of SARS-CoV-2 by minimizing the number of different individuals who come into close contact with each other at work and during shared rides. Cohorting may reduce the spread of workplace SARS-CoV-2 by minimizing the number of different individuals who come into close contact with each other over the course of a week. Cohorting may also reduce the number of workers quarantined if there is exposure to the virus.
Establish a system for employees to safely alert their supervisors if they are experiencing signs or symptoms of COVID-19 or if they have had recent close contact with a suspected or confirmed COVID-19 case. Provide training on COVID-19-related safety protocols for workers.
An employer plans and policies for addressing COVID-19 could include: developing back-up staffing plans, specific policies for a worker who was ill with COVID-19 returning to work, and implementing flexible sick leave policies if they do not already exist. COVID-19 related policies should be revised as needed and communicated clearly to workers.
Encourage hand hygiene:
- Providing workers handwashing stations equipped with soap, running water, and single-use paper towels in multiple locations. If possible, choose hand washing stations that are touch free.
- Providing alcohol-based hand sanitizers containing at least 60% alcohol if soap and water are not immediately available.
- Placing hand sanitizers in multiple locations. If possible, choose hand sanitizer stations that are touch-free.
- Considering other workplace policies and programs to promote personal hygiene, such as:
- Building additional short breaks into staff schedules to increase how often staff can wash their hands with soap and water or use hand sanitizers with at least 60% alcohol;
- Providing tissues and no-touch trash receptacles for workers to use;
- Providing information on cough and sneeze etiquette; and
- Educating workers that cigarettes and smokeless tobacco use can lead to increased contact between potentially contaminated hands and their mouth, and that avoiding these products may reduce their risk of infection.
- See OSHA's Sanitation standard (29 CFR 1910.141) for information about requirements for handwashing facilities for workers.
Clean and disinfect shared common equipment such as communications headsets, operating terminals and other routinely touched items between shifts. Refer to List N on the EPA website for EPA-registered disinfectants that have qualified under EPA's emerging viral pathogens program for use against SARS-CoV-2.
Provide disposable drinking water cups or individual bottles of water in hydration stations and disposable plates, bowls, etc. in break and dining areas along with discouraging the use of shared condiment bottles.
Workers in this industry should wear cloth face coverings. See the box on wearing cloth face coverings (below) in common areas such as the drill deck, doghouse, control rooms, and office spaces in the trailers.
Cloth Face Coverings in Oil and Gas
CDC recommends wearing cloth face coverings as a protective measure in addition to staying at least six feet away from others. Cloth face coverings may be especially important when social distancing is not possible or feasible based on working conditions. A cloth face covering may reduce the amount of large respiratory droplets that a person spreads when talking, sneezing, or coughing. Cloth face coverings may prevent people who do not know they have the virus that causes COVID-19 from spreading it to others. Cloth face coverings are intended to protect other people—not the wearer.
Cloth face coverings are not PPE. Cloth face coverings should not be used as a substitute for a respirator or surgical mask in workplaces where such equipment is needed to protect the wearer.
While wearing cloth face coverings is a public health measure intended to reduce the spread of COVID-19 in communities, it may not be practical for workers to wear a single cloth face covering for the full duration of a work shift (e.g., eight or more hours) in oil and gas operations if they become wet, soiled, or otherwise visibly contaminated during the work shift. If cloth face coverings are worn in these worksites, employers should provide readily available clean cloth face coverings (or disposable facemask options) for workers to use when the coverings become wet, soiled, or otherwise visibly contaminated.
Employers who determine that cloth face coverings should be worn in the workplace, including to comply with state or local orders, should ensure the cloth face coverings:
- Fit over the nose and mouth and fit snugly but comfortably against the side of the face;
- Are secured with ties or ear loops;
- Include multiple layers of fabric;
- Allow for breathing without restriction;
- Can be laundered using the warmest appropriate water setting and machine dried daily after the shift, without damage or change to shape (a clean cloth face covering should be used each day);
- Are not used if they become wet or contaminated;
- Are replaced with clean replacements, provided by employer, as needed.
- Are handled as little as possible to prevent transferring infectious materials to the cloth; and
- Are not worn with or instead of respiratory protection when respirators are needed.
Safe Work Practices
Workers should avoid touching their faces, including their eyes, noses, and mouths, until they have thoroughly washed their hands upon completing work and removing PPE. Workers should be careful not to touch their eyes, nose, and mouth when removing a cloth face covering or other facial PPE.
Flexibilities Regarding OSHA’s PPE Requirements and Prioritization of PPE During COVID-19
Some employers may experience shortages of PPE, including face shields and respirators, as a result of the COVID-19 pandemic.
See information on PPE flexibilities and prioritization in the Personal Protective Equipment Considerations section within the Interim Guidance for U.S. Workers and Employers of Workers with Potential Occupational Exposures to SARS-CoV-2.
Personal Protective Equipment
Most oil and gas workers in normal work environments are unlikely to need PPE beyond what they use to protect themselves during routine job tasks. Conduct a hazard assessment (sometimes called a job hazard analysis) to determine the proper PPE for industrial hazards. Reminder – face masks and cloth face coverings are not substitutes for respiratory protection from industrial hazards
Employers should consider whether their hazard and risk assessments warrant the use of items such as gloves or eye and face protection, if not already in use. For example, workers may need eye and face protection (e.g., goggles, face shields) when work requires being within six feet of other workers and when other engineering and administrative controls cannot prevent worker exposure to potentially infectious respiratory droplets.
Consider possible additional hazards (e.g., PPE catching in machinery, limiting worker dexterity or vision) that can be created by new PPE in the work environment.
The sharing of PPE, such as gloves, aprons, and face shields, including equipment used for hazards other than SARS-CoV-2 (e.g., for mixing mud-drilling fluids that contain hazardous chemicals), should be avoided, if possible. If the PPE must be shared, it needs to be cleaned and disinfected according to manufacturer recommendations before being used by another person. Follow proper donning and doffing procedures for PPE.
Note that workers who perform tasks involving hazardous chemicals may also require PPE and/or other controls to protect them from chemical hazards. Employers may need to adapt guidance from this section, and the Interim Guidance for Workers and Employers of Workers at Increased Risk of Occupational Exposure, in order to fully protect workers performing activities in oil and gas drilling, servicing, production, and/or processing workplaces that involve work with hazardous chemicals.