Solutions for Electrical Contractors eTool
Installation and Repair » Using Tools
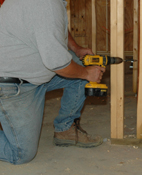
Electrical employees use a variety of tools, such as nut drivers, conduit benders, electric drills, and pliers. For more information about tools with ergonomic advantages, visit the tool index.
Potential Hazards
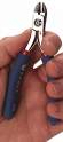
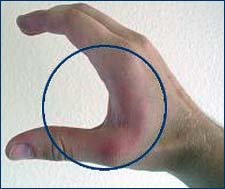
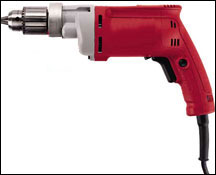
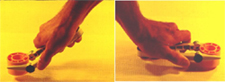
-
Poorly designed or improperly used hand tools may require excessive force and cause awkward postures resulting in tendonitis in hands, wrists and elbows.
-
Short handles may press or rub against the palm and fingers (Figure 1) causing contact stress. Small handle diameter may increase force requirements of tool leading to fatigue, discomfort and pain.
-
Tools with wide handle spans require extended thumb and finger positions (Figure 2) to activate the tool. These postures require increased finger force to provide adequate activation force increasing fatigue, discomfort and pain.
-
Improper orientation of the tool handle may result in awkward position of the hand, wrist, or arm and increase force requirements of the task.
Possible Solutions
-
Use power tools (Figure 3) to do the job when repetitive or prolonged force exertion is required.
-
Use a properly designed tool to promote neutral posture of the wrist and hand. (Figure 4). Generally, an inline tool is best on horizontal surfaces at about waist height, and a pistol grip is preferable for vertical surfaces at about waist height. Bent-handled tools can be designed to accommodate differing work positions and angles.
-
Use tools with padded grips and handles that extend across the whole palm of the hand to minimize contact pressure.
-
Ensure that tools such as screwdrivers have appropriately sized and shaped handles. Generally, handles should be about 1 1/2 inches to 3 inches in diameter. Triangular handles with rounded edges provide a better grip.
-
Use tools that do not require an extended grip. The hand should be in the shape of a "C" while gripping the tool. A span of 2 1/2 to 3 1/2 inches is best.
-
Ergonomic Design for People at Work, Volume 2. Eastman Kodak Company, (1986).
-
-
Replace tools if handles are damaged.
-
Take regular breaks and rotate tasks when using a hand tool for an extended period of time.
-
Use fitted gloves which protect the hands from contact stress.
-
Keep tools well maintained and in good repair.
-
A Guide to Selecting Non-Powered Hand Tools. US Department of Health and Human Services (DHHS), National Institute for Occupational Safety and Health (NIOSH) and California Occupational Safety and Health Administration (Cal/OSHA), (2004, August).
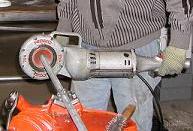
Potential Hazards
-
Some portable power tools, such as pipe threaders (Figure 5), may be heavy or require extreme effort to counteract torque forces. Sustained use of these tools puts stress on the back, hands, arms, and shoulders.
-
Tools such as jack hammers or large saws that transmit vibration may cause hand-arm vibration syndrome (HAVS). Early signs of HAVS are feelings of numbness or tingling in the fingers, hands, or arms, or numbness and whiteness in the tips of fingers when exposed to cold.
-
When using tools employees may assume awkward postures including bending, stooping or extended reaching. Awkward postures maintained for long periods of time may cause fatigue, discomfort and pain, especially when heavy tools are used.
-
Improper orientation of tool handles may cause awkward position of the hand, wrist, or arm and increase force requirements of the task.
-
Repeatedly using a single finger to activate triggers on power tools may cause overuse of tendons and muscles leading to irritation, swelling, pain and eventually immobility.
Possible Solutions
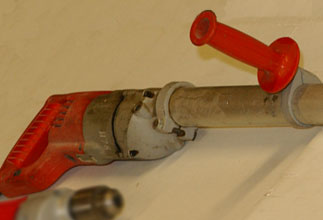
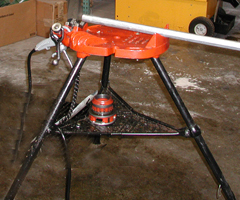
-
Use tools with a proper handle orientation that allows neutral wrist position. Generally, use tools with a pistol grip for vertical surfaces and an in-line grip for horizontal surfaces.
-
Use torque bars (Figure 6) on tools such as drills or pipe threaders to minimize the exertion required to control the tool.
-
Use trigger-levers on power tools. These have a longer trigger to accommodate three fingers, rather than those with single finger trigger action.
-
Maintain equipment and tools in proper working order. Unbalanced rotating parts or poorly sharpened cutting tools may create excessive vibration and increase force requirements when in use.
-
Support the weight of heavy tools (Figure 7) by using overhead or under-tool supports.
-
Avoid older power tools that were not designed with ergonomics in mind and may vibrate excessively. Consider reduced-vibration tools when making new tool selection.
-
Wear proper anti-vibration gloves when using power tools and use only as much finger force as necessary to provide proper control of the tool.
-
Learn proper tool usage and safety practices. Employees should allow the tool or machine to do the work and should arrange the work so that they can stand upright and use the tool with the elbows close to the body.
-
Keep hands warm and dry.
-
Use platform ladders, regular ladders or lifts to reach higher work areas so that arms may be kept closer to the body. The arms may then safely support tools when in the power zone.
-
Wear kneepads when kneeling is required.
-
To reduce crouching and kneeling, sit on a stool while working on lower areas.
-
Minimize the time of continuous use when operating a vibrating tool. Appropriate operating times will vary depend on the magnitude of vibration, however limiting sessions to 10 to 15 minute of continuous use with no more than 2 hours of total operating time per day is generally recognized as a prudent work/rest schedule. Other means of dampening or reducing vibration should still be observed even during shortened sessions.
-
Criteria for a Recommended Standard: Occupational Exposure to Hand-Arm Vibration. US Department of Health and Human Services (DHHS), National Institute for Occupational Safety and Health (NIOSH) Publication No. 89-106, (1989, September).
-
-
Keep cutting surfaces of tools sharp and lubricated.
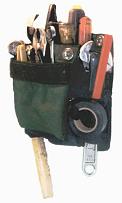
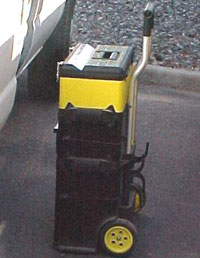
Potential Hazards
-
Loaded tool belts may weigh over 50 pounds (Figure 8), causing an increased load and contact stress on the lower back and hips.
-
Suspenders used to hold the tool belt may cause shoulder contact stress and discomfort.
-
Wearing a tool belt for an extended period of time may cause fatigue, discomfort and pain.
Possible Solutions
-
Use mobile tool box or bucket-style tool bag (Figure 9) instead of a tool belt.
-
Use padded belts and suspenders to evenly distribute the weight between the shoulders and the waist, thus reducing contact stress.
-
Arrange tools in bags so that their weight is distributed evenly.
-
When possible, reduce the weight of the tool belt by reducing the number of tools carried to those necessary for the task.
-
Use a backpack-style tool bag to distribute the weight of tools over the body and improve posture if tools must be carried for extended distances.
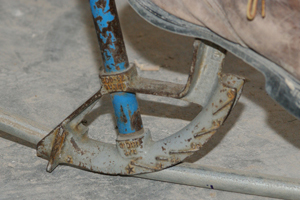
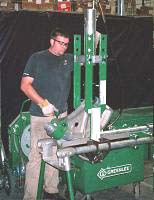
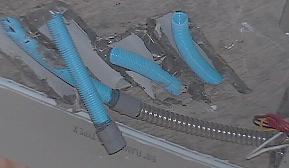
Potential Hazards
-
Manual conduit bending (Figure 10) may require exertion of significant forces and awkward postures which may lead to overexertion of the back and shoulders.
-
Bending over to cut conduit may result in overexertion to the back and shoulders.
Possible Solutions
-
Use mechanical conduit benders (Figure 11), especially on conduit with a diameter larger than 1 1/2 inches.
-
Where conditions are not optimal and power equipment may not be available, prefabricate as much conduit as possible to minimize on-site bending.
-
Where manual benders are required, use longer handles thus increasing leverage and minimizes the amount of force required to bend conduit.
-
Place conduit in a vice or fixture to maintain stability when cutting. Support conduit on a table or sawhorse.
-
Wear gloves when manually bending conduit to reduce contact stress and avoid cuts. Ensure that conduit ends are properly reamed and good handles are maintained on manual conduit benders.
-
Where code allows, use lightweight, flexible conduit (Figure 12) which does not require bending.
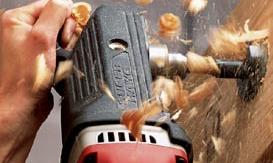
Potential Hazards
-
Hole saws and drill bits may get stuck while spinning resulting in strong kickback and increasing the potential of severe injuries to the wrists, elbows and shoulders.
-
Drills must be used frequently on floors, floor joists or rafters forcing employees to bend or reach for a work piece.
-
Supporting heavy drills for extended periods of time may cause fatigue, discomfort and pain.
-
Regular exposure to vibration when using hand-held power tools may cause hand-arm vibration syndrome (HAVS).
Possible Solutions
-
Use an angle drill for large holes. This provides a longer lever arm to control torque forces (Figure 13).
-
Use a torque bar to help absorb the shock of a stuck bit.
-
Use drilling tools with a built-in kickback clutch.
-
Do not force the bit. Apply even pressure and let the drill do the work.
-
Use bit extensions to help minimize reaching.
-
Use platform ladders, regular ladders (Figure 14) or lifts to reach higher work areas so that arms may be kept closer to the body. The arms may then safely support tools when in the power zone.
-
Ask builders to use materials that do not require drilling, such as engineered wood products with knockouts.
-
Ask builders to use spacers while laying fresh concrete to minimize drilling after concrete has cured.
-
Ensure that tool bits are sharp before using. Replace or sharpen bits frequently.
-
Use a stool to improve access and minimize reaching.
-
Wear kneepads when frequent or prolonged kneeling is required.