Solutions for Electrical Contractors eTool
Prefabrication » Assembly Tasks
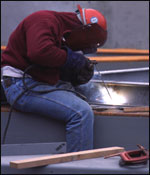
Prefabrication assembly may improve efficiency and allow companies to have greater control over the workplace. However, it may also expose employees to a number of ergonomics-related risk factors including forceful exertion, highly repetitive motions, awkward postures and contact stress.
Potential Hazards
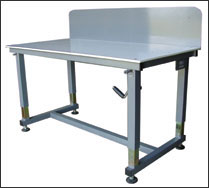
-
Employees may work around a table or other flat work surface, either in a sitting or standing position. Improper placement of materials can require repetitive reaching or torso twisting and bending.
-
Inappropriate height of the work surface may force employees to bend forward at the waist or the neck if it is too low, or continually lift and support the weight of their arms if it is too high.
-
Sharp edges on work tables (Figure 1) may create contact stress to soft tissues of the forearm, hand and wrist.
Possible Solutions
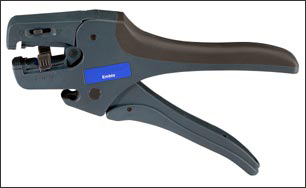
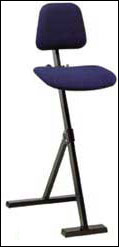
-
Pad tools and work surfaces where they come in contact with body parts.
-
Use hand tools and work surfaces with rounded edges (Figure 2).
-
Provide adjustable workstations so that employees may properly adjust the height and tilt of work surface.
-
Provide lighted, adjustable magnifying glasses to increase visibility while assembling smaller parts such as screws and wire couplings.
-
Provide sit/stand stools (Figure 3) so that employees may rest while remaining in an upright position. It provides periods of change in posture, a chance to rest while working, and increases the range of movement.
Potential Hazards
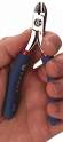
-
Tools with short handles can press into the palm of the hand (Figure 4).
-
Tools that require highly repetitive exertion such as crimpers or side cutters may stress the muscles and tendons of the hands and forearms.
-
Employees who use tools that require significant repetitive force, such as using side cutters to cut large-gauge wire, may stretch and fray tendons and fatigue muscles.
-
Improper size tools when in use require more force to complete a task increasing the risk of overexertion injury.
-
Tools that require repeated opening such as pliers or cutters, create contact stress on the fingers increasing the risk of soft tissue injury.
-
The assembly line process forces users to perform the same motion over and over. Twisting wire with regular pliers or using a manual screwdriver may be appropriate for on-site jobs with many differing tasks. However, in prefabrication jobs this greatly increases the chance of repetitive-motion injuries such as tendonitis or epicondylitis.
Possible Solutions
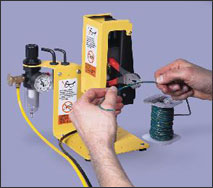
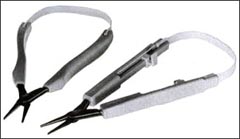
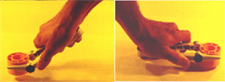
-
Use mechanical assists (Figure 5) or self-opening tools (Figure 6) for tools such as snips and crimpers that require repeated opening and closing.
-
Ensure that tool handles extend across the entire palm of the hand.
-
Use pistol-grip and padded handles to protect the entire palm of the hand.
-
Use hand tools and work surfaces with rounded edges.
-
Provide tools that are appropriately sized for the employee.
-
Use a properly designed tool to promote neutral posture of the wrist and hand (Figure 7). Generally, an inline tool is best on horizontal surfaces at about waist height, and a pistol grip is preferable for vertical surfaces at about waist height. Bent-handled tools can be designed to accommodate differing work positions and angles.
-
Use powered tools for tasks that require exertion of significant force.
-
Increase scope of tasks so that employees have a greater variety of things to do and are not doing the same thing for an extended period (or length) of time. This provides rest for affected muscles.
-
Take regular breaks to stretch and move around.
-
Use broad range of pneumatic tools when working in an assembly setting for crimping, stripping, and cutting wires. These tools can help to reduce the risk of injury and increase productivity.
-
Use a balancer for tools weighing 5 pounds or more or when heavy tools are used for an extended period of time.
-
Sharpen cutting tools frequently.
-
Keep tools lubricated and well maintained.
Potential Hazards
-
Working at an assembly process exposes employees to static postures maintained for long periods of time. This may involve prolonged standing to perform tasks which are difficult to handle from a seated position.
-
Standing on hard floor surfaces may cause discomfort, fatigue, swelling in the lower extremities and increase the risk of low back pain.
-
Standing in one spot may reduce muscle activity, which is needed to pump blood throughout the lower extremities. Muscles may become deprived of nutrients and fatigued leading to stiffness as well as swelling and varicose veins.
-
Employees may need to use one hand to hold work pieces during assembly. This forces employees to use their fingers to grasp for extended periods.
Possible Solutions
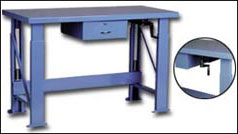
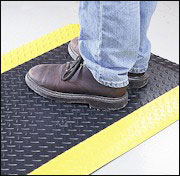
-
Provide adjustable-height workstations (Figure 8) so that employees may change their work height to maintain neutral body postures.
-
Use adjustable clamps or fixtures to hold parts during assembly.
-
Provide sit/stand stools (Figure 3) that allow employees to rest while remaining in an upright position. It provides periods of change in posture, increases the range of movement, and provides a chance to rest while working.
-
Alternate posture between sitting and standing when performing work tasks, if possible.
-
Increase scope of tasks so that employees have a greater variety of things to do and are not doing the same thing for extended periods of time. This provides rest for affected muscles.
-
Provide anti-fatigue mats (Figure 9) and shoe inserts to reduce stress on the lower extremities and lower back caused by prolonged standing on hard floor surfaces.
-
Take regular breaks to stretch and move around.