Lockout/Tagout eTool
Energy Control Program » Training and Retraining
The employer is required to provide effective training for all employees covered by the lockout/tagout standard and ensure that all employees understand the purpose, function, and restrictions of the energy control program. Authorized employees must possess the knowledge and skills necessary for the safe application, use, and removal of energy controls. This training also must make employees aware that disregarding or violating the energy control program could endanger their own lives or the lives of coworkers.
Employee Training Requirements
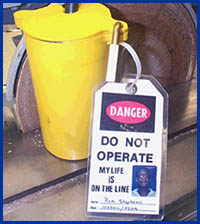
There are three types of employees which must receive training: authorized, affected, and other. The amount and type of training that each employee receives is based upon the relationship of that employee's job to the machine or equipment being locked or tagged out and upon the degree of knowledge relevant to hazardous energy that the employee must possess.
In addition, employers are required to certify that effective training and retraining has been provided to all employees covered by the standard. The certification must contain each employee's name and dates of training.
-
Authorized employee training. The lockout/tagout standard requires that before the machine or equipment is turned off, the authorized employee must be knowledgeable of the following:
-
Recognition of applicable hazardous energy sources.
-
Details about the type and magnitude of the hazardous energy sources present in the work area.
-
The methods and means necessary to isolate and control hazardous energy sources.
-
- Affected and other employee training. Affected employees and all other employees are required to recognize when energy control procedures are being used, understand the purpose of the procedure, and understand the critical importance of not attempting to start up or use equipment that has been locked out or tagged out.
Additional Training Requirements for the Use of Tagout Devices
When the employer uses tagout as opposed to lockout, employees must receive additional training to enhance the safety of the tagout program and to ensure employee protection.
To address the limitations of tags, additional training must be conducted for employees who work with tagout or who work in areas in which tagout is used. This additional training must address the following:
-
Tags are essentially warning devices affixed to energy-isolating devices and do not provide the physical restraint of a lock.
-
Tags must be legible and understandable by all employees.
-
Tags and their means of attachment must be made of materials that will withstand the environmental conditions encountered in the workplace.
-
The presence of tags may create a false sense of security. They are only one part of an overall energy control program.
-
Tags must be securely attached to the energy control devices so that they cannot be detached accidentally during use.
-
When a tag is attached to an isolating means, it is not to be removed except by the person who applied it, and it is never to be bypassed, ignored, or otherwise defeated.
Retraining
Retraining must be provided whenever there is a change in job assignments; a change in machines, equipment, or processes that presents a new hazard; or a change in energy control procedures. Additional retraining must be conducted whenever a periodic inspection reveals, or whenever the employer has reason to believe, that there are deviations from or inadequacies in the employees' knowledge or use of the energy control procedure.
Retraining could be triggered by other events as well. For example, an employee working with an energy control procedure might be injured in the course of his/her duties, or a "near miss" might occur in which no one is injured but a deviation from established energy control procedures occurred. Both of these cases would trigger the need for retraining.
<< Previous Page | Next Topic >> | Topic Contents