Lockout/Tagout eTool
Group Lockout-Tagout » Group Lockout-Tagout Procedures
Whenever servicing and/or maintenance is performed by a group of employees, the employer must develop and implement an energy control procedure that provides authorized and affected employees with the same level of protection as a personal lockout or tagout device. The requirements for group lockout or tagout are set out in section 29 CFR 1910.147(f)(3).
Servicing and maintenance operations performed by a group of employees are often more complex than servicing or maintenance performed by an individual. As a result, group lockout or tagout operations typically require more coordination and communication than personal lockout or tagout operations. Greater coordination between employees is particularly important when more than one craft or department must be involved to complete the task.
Under the standard's group lockout/tagout requirements, a single authorized employee must assume the overall responsibility for the control of hazardous energy for all members of the group while the servicing or maintenance work is in progress.
The authorized employee with the overall responsibility must implement the energy control procedures, communicate the purpose of the operation to the servicing and maintenance employees, coordinate the operation, and ensure that all procedural steps have been properly completed. In such operations, it is critical that each authorized employee involved in the group lockout/tagout activity be familiar with the type and magnitude of energy that may be present during the servicing and maintenance work.
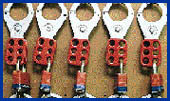
In addition, each employee must affix his/her personal lockout or tagout device to the group lockout device, group lockbox, or comparable mechanism, before engaging in the servicing and maintenance operation. This enables the authorized employee to have control over his/her own protection, and verify that the equipment has been properly deenergized. Additionally, the lockout or tagout device will inform other persons that the employee is working on the equipment, and as long as the device remains attached, the authorized person in charge of the group lockout or tagout knows that the work has not been completed and that it is not safe to reenergize the equipment.
The servicing employee will continue to be protected by his/her lockout or tagout device until it is removed. The authorized employee in charge of the group lockout or tagout must not remove the group lockout or tagout device until each employee in the group has removed his/her personal device, indicating that he/she is no longer exposed to the hazards from the servicing operation.
When the activities involving group lockout or tagout extend into another workshift, or there is a change of authorized employees, the provisions for shift or personnel changes must also be followed.
Next Page >> | Topic Contents