Shipyard Employment eTool
PPE Selection >> Surface Preparation
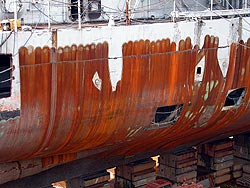
The OSHA Hierarchy of Controls
- Engineering Controls
- Administration Controls
- Personal Protective Equipment (PPE)
Surface preparation requires pre-planning and evaluation of the area for potential hazards before beginning work. Usually, a Shipyard Competent Person (SCP), Certified Industrial Hygienist (CIH), or Certified Marine Chemist (CMC) is needed to help evaluate hazards and select personal protective equipment (PPE). Additional hazards will exist if work is done in enclosed or confined spaces (see confined space).
Surface preparation operations present a significant risk for skin, eye, and respiratory exposure to toxic and corrosive chemicals, as well as risk of burns, cuts, and lacerations. Surface preparation operations often require the use of respiratory protection equipment. Employers must comply with the OSHA respirator standard [29 CFR 1915.154 and 29 CFR 1910.134].
Typical surface preparation operations are as follows:
- Abrasive blasting
- Chemical paint removers
- Flame removal
- Mechanical paint removers (for example grinding, needle gunning, pneumatic chipping)
- Hydro-Blasting
- Solvent Degreasing
Each of these surface preparation operations may present unique hazards. Therefore, a qualified person must select PPE based on the specific operation. Use of appropriate combinations of the following PPE will provide adequate protection:
- Protective clothing and hoods
- Respiratory protection
- Eye and face protection
- Foot protection
- Hand protection (such as gloves)
Review the General Shipyard Worker PPE before proceeding with this section.
PPE is required when performing abrasive blasting and must provide protection from the impact of the rebounding abrasive blast material (for example sand, metal slag) and toxic effects of the abrasive blast material and coatings (such as paint, grease) being removed. Due to possible surges of pressure in the hose line and potential static electricity shocks, fall protection may be necessary. Hearing protection is important in this operation due to the high noise levels usually associated with this operation.
PPE is required when using chemical paint removers (such as methylene chloride, sodium hydroxide/lye) and must provide protection from skin contact, skin absorption, and inhalation. Reactions between the cleaner and the material being removed may produce additional toxic vapors or liquids.
Note: During these operations, it is important to have an emergency eye and body flushing station.
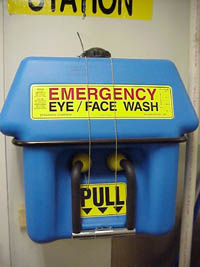
- Fixed or portable eye wash stations/safety showers should meet ANSI Z358.1-1998: Emergency Eye Wash and Shower Equipment.
PPE may be required when the workers are exposed to fumes and smoke created by flame removal of hardened coatings (such as paint).
PPE is required when performing mechanical paint removal (such as by grinding, needle gunning, pneumatic chipping). Due to high noise, flying particles, and dust, hearing and eye protection are required and respiratory protection may be required for all these operations. Due to the sparks produced, by grinding, protective clothing is required. [29 CFR 1915.152(a) and (b)] Anti-vibration devices should be used to reduce the effect of excessive vibration from pneumatic tools.
PPE is required when using hydro-blasting as a surface preparation method and must protect the worker from injury from the hazards of the high-pressure water stream, often from 1000 to 30000 psi. Due to the pressure reaction of turning the stream on and off, fall protection may be necessary. Due to high noise, hearing protection may be required. The PPE should also protect the worker from skin contact with the material being removed, which in many cases can be toxic.
PPE is required when performing solvent degreasing (such as with xylene, mineral spirits, acetone) to provide protection from skin contact, skin absorption, and inhalation. Reactions between the degreaser and the material being removed may produce additional toxic vapors or liquids.
Note: During these operations, it is important to have an emergency eye and body flushing station.
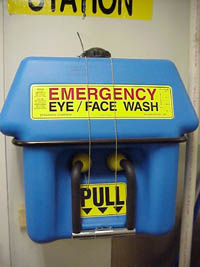
- Fixed or portable eye wash stations/safety showers should meet ANSI Z358.1-1998: Emergency Eye Wash and Shower Equipment.
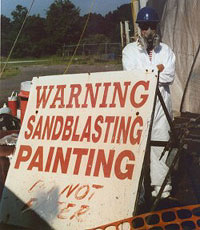
Potential Hazard
- Chemical absorption or burns due to skin exposure to chemical cleaner or residues.
-
Abrasions and amputations from particles generated by grinding, chipping, and blasting operations.
- Hearing loss from excessive noise.
- Burns due to contact with steam or hot water.
- Burns and amputations from contact with high-pressure steam, water, or air streams from high-pressure equipment.
- Struck-by injuries and falls caused by uncontrolled high-pressure hoses.
-
Heat-related illnesses due to a combination of PPE use, heat-producing equipment, work activity, and environmental conditions. See Surface Preparation: Mechanical Removers - Work Environment Temperature Related Hazards.
Requirements and Example Solutions
- PPE (such as a blasting hood and heavy canvas or leather aprons) must be provided to protect the head and body of the blaster from the impact of rebound abrasives. (See Figure 5.) [29 CFR 1915.152(a)]
-
PPE should provide skin protection from water, steam burns and high-temperature water during pressure spraying. (See Figure 6.)
- PPE (such as impermeable chemical resistant clothing) must be provided to protect the skin from corrosive and toxic chemicals that may be spilled, sprayed, or splashed during their use. (See Figure 7.) [29 CFR 1915.152(a)]
- Attached hoods should be used when there is head or neck exposure.
- When respirators are used, hoods should be tightened over the respirator to prevent interference with the face seal and allow proper removal of gear.
- Heat stress program should be used.
-
Leather garments provide such protection provided that they are free of flammable or combustible materials such as oil, grease, and solvents.
For more detailed information, review Hand and Body Protection.
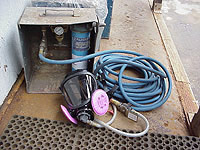
Potential Hazards
Respirators protect the lungs and upper respiratory track from dust, mists, fumes, and vapors that are associated with the cleaners and residues. Worker illness may result from:
- Inhalation exposure to toxic or corrosive chemicals.
-
Exposure to oxygen-deficient atmospheres.
-
Exposure to dust (such as silica, lead, and chromate).
Requirements and Example Solutions
OSHA requirements [29 CFR 1915.32, 33, 34, 35 and 36] for the following operations do not apply to Shipbreaking:
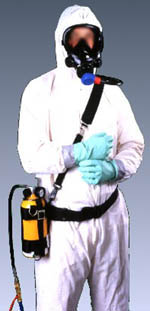
- Abrasive Blasting
- Chemical Paint Removers
- Flame Removal
- Mechanical Paint Removers (for example Grinding, Needle Gunning, Pneumatic Chipping)
- Hydro-Blasting
- Solvent Degreasing
However, a Hazard Assessment is required by 29 CFR 1915.152 to protect workers from the hazards associated with these operations.
For more detailed information, review Respiratory Protection.
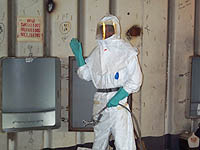
Potential Hazards
- Chemical absorption or burns due to skin exposure to chemical cleaner or residues.
- Eye and face injury from particles generated by grinding, chipping and blasting operations.
- Worker face and eye exposure to corrosive or toxic chemicals that may splash or be sprayed.
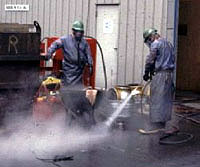
Requirements and Example Solutions
- Full-face respirators should be used when toxic chemicals, that can be absorbed through the skin, are used.
- Face shields and chemical goggles are necessary to protect the eyes and face from corrosive materials.
- A defogging solution should be wiped on the face shield before use and whenever necessary to provide adequate vision when steam cleaning or hydro-blasting.
For more detailed information, review Eye and Face Protection.
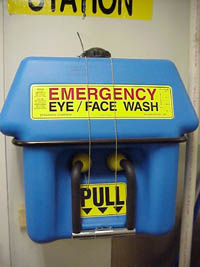
- Fixed or portable eye wash stations/safety showers should meet ANSI Z358.1-1998: Emergency Eye Wash and Shower Equipment.
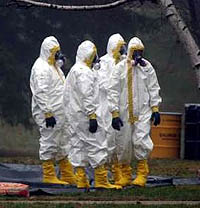
Potential Hazards
- Chemical absorption or burns due to skin exposure to chemical cleaner or residues.
- Foot injuries from blasting operations.
- Lacerations or amputations due to exposure to high-pressure water and steam.
- Slips and falls due to slippery surface.
- Foot related illnesses due to wading in water.
- Burns due to contact with steam or hot water.
- Crushing hazards from falling objects.
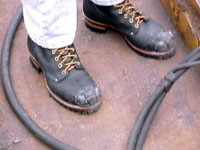
Requirements and Example Solutions
- Boots (for example chemical resistant or waterproof) should provide skin protection from:
- Corrosive and toxic chemicals that may be spilled, sprayed or splashed during their use.
- Trauma during high-pressure spraying.
- Steam burns and high-temperature water.
- Prolonged exposure to water and similar non-hazardous liquids.
- Boots should be worn with the legs of the protective clothing over them to prevent liquids from entering the boots.
- Slip-resistant soled boots should be worn when working on slippery surfaces.
- If flammable solvents are involved in the operation, non-static discharge producing shoes/boots and shoe covers should be used.
For more detailed information, review Foot Protection.
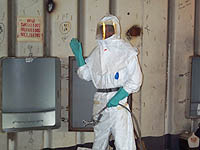
Potential Hazards
- Chemical absorption or burns due to skin exposure to chemical cleaner or residues.
- Burns due to contact with steam or hot water.
- Hand injuries from grinding, chipping, and blasting operations.
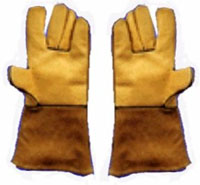
Requirements and Example Solutions
OSHA requirements [29 CFR 1915.32, 33, 34, 35 and 36] for the following operations do not apply to Shipbreaking:
- Abrasive Blasting
- Chemical Paint Removers
- Flame Removal
- Mechanical Paint Removers (for example Grinding, Needle Gunning, Pneumatic Chipping)
- Hydro-Blasting
- Solvent Degreasing
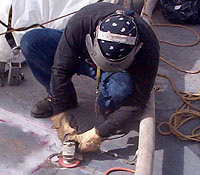
However, a Hazard Assessment is required by 29 CFR 1915.152 to protect workers from the hazards associated with these operations.
For more detailed information, review Hand and Body Protection.