Woodworking eTool
Specific Finishing Equipment » Drill Presses
With a drill press, the operator must be protected from the rotating chuck and swarf that is produced by the drill bit. Specially designed shields can be attached to the quill and used to protect this area. A telescoping portion of the shield can retract as the drill bit comes down into the piece-part. On larger gang or radial drills, a more universal-type shield is usually applied.
Definition
A drill press is a wood cutting machine that uses a multiple-cutting-edged rotating tool to remove wood and produce a hole in the stock. Normally, drilling machines are vertically arranged with the tools having variable speeds and feeds. They may also have multiple spindles for gang drilling. The most commonly used drilling machine is a single-spindle, floor-mounted, belt-driven machine for non-production drilling. Belt-driven spindles may require manual belt shifting for spindle speed changes. Feed rates are also adjustable and may be manual or automatic.
Operator Involvement
The drilling machine operator may or may not be a skilled worker. The common drill press is used often by anybody in the shop and injuries can occur because of carelessness. The operator must position the stock, install the drill, operate and observe, and maintain housekeeping. The operator also must change speeds and feeds when required.
Potential Hazards
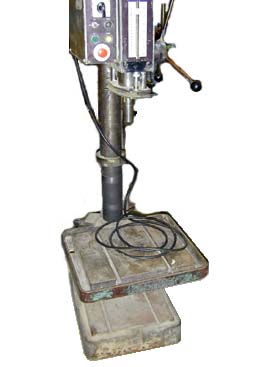
-
One of the most common causes of accidents that occur on a drill press is poor operator judgment. Often the operator will attempt to hand-hold the stock while drilling. When the drill enters the work, it can catch and twist the stock from the operator, which results in an uncontrolled rotating piece of wood. Other point-of-operation hazards include the rotating drill, which is rarely guarded, and hot chip generation.
-
Operating controls often are simple on-off push-buttons with no emergency stop devices.
-
Power transmission components often are exposed.
-
Because the drill press is such a commonly used machine, it often is cluttered with chips and scraps, which create a hazardous work area.
-
This machine is less hazardous than others only because of its simple operation; nevertheless, familiarity with its operation is required.
Possible Solutions
-
Guarding at the point of operation is difficult because of the nature of the drilling process. The drill gradually feeds into the work, it is changed very often, chips must be able to escape, and the stock must be moved around which all reduce the possibility of using guards at the drill. If guards are used, they probably will have to be removed during the actual drilling process. Whenever possible, a hold-down fixture should be used rather than the hands.
-
Automatic machines and high-production machines should use barricades or enclosures to separate the worker from the entire drilling machine.
-
Power transmission components should be enclosed entirely on those machines that have adjustable belt drives. The enclosure should have an interlocked access door to facilitate speed changes.
-
Push button controls should be shrouded and an emergency shut-off switch installed near the machine. A main disconnect is necessary.
-
Good housekeeping and operator training are absolute musts.