Woodworking eTool
Specific Finishing Equipment » Routers
Routers often are used for cutting and shaping decorative pieces, making frame and panel doors, and milling moldings. Routers have spindles that spin variously shaped, small-diameter cutting tools at high speeds. The tool is held in a collet chuck and protrudes through a flat, smooth base that slides over the surface of the work. The tool-spindle axis is usually vertical, but it may be tilted. The operator lowers the head for machining, and the head automatically returns to its original position after the cut is made. The spindle is driven by belts and pulleys or by a high-speed motor.
-
Inadvertent contact with the rotating tool or cutter head when handling the stock or removing scrap from the table may cause injuries.
Possible Solutions
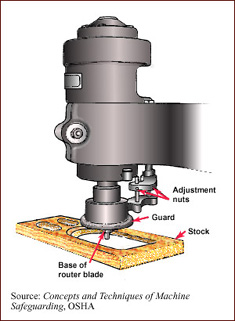
Engineering Controls
-
Enclose the tool with an adjustable tool guard, as shown in Fig. 1 [29 CFR 1910.213(m)(1)].
-
Guard feed rolls [29 CFR 1910.213(b)(7)].
-
Clothing or hair may be caught on a rotating cutter head.
Possible Solutions
Engineering Controls
-
Equip routers with a spindle braking system that gradually engages.
-
Tools can be flung from the cutter head if they are poorly fastened in the tool holder, if the wrong tool is used, or if the tool speed is too high.
Possible Solutions
Work Practices
-
Attach and secure tools to the holder properly.
-
Label cutting tools and holders with the maximum permissible spindle speed.
-
Use tools only as intended.
-
Flying chips - Wood chips or wood dust, and splinters may be thrown by the cutting action.
Possible Solutions
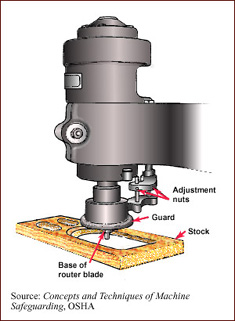
Engineering Controls
-
Enclose the tool with an adjustable tool guard, as shown in Fig. 1 [29 CFR 1910.213(m)(1)].
-
Guard feed rolls [29 CFR 1910.213(b)(7)].
-
Kickback may be caused by poor-quality lumber such as if the stock breaks or incorrect work method, such as feeding the stock into the tool too abruptly or in the wrong direction, or poorly fixing the stock to the template.
Possible Solutions
Work Practices
-
Use quality stock that is unlikely to break.
-
Avoid feeding the stock into the tool too abruptly or in the wrong direction.
-
Always secure the stock to the template.
-
Use tools only as intended.