Hazard Identification Training Tool
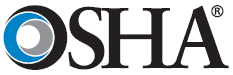
Hazard
Identification
Training Tool
Manufacturing Scenario
You are the head of Amalgamated Polyscientific Enterprises International, a company that manufactures parts for next-generation hovercrafts. Your goal is to ensure that your workers remain safe.
You must find hazards to maintain a safe workplace. There are 4 kinds of tools for finding hazards.
- Collect Info - Read any information you may have (manuals, safety data sheets, OSHA data, etc) to find hazards that have already been identified by others.
- Inspect & Observe - Inspect equipment and areas, and observe processes in action.
- Involve Workers - Talk to your workers and listen to their feedback.
- Investigate Incidents - Whenever an incident occurs, use that as an opportunity to learn about hazards that may have been overlooked.
- Prioritize - Evaluate the hazards you have identified and fix the most hazardous first.
Tools
- Hazard Identification Tools: To find hazards, you can click on equipment, people, and areas in the plant.
- Selecting a piece of equipment gives you access to the hazard identification information and available actions related to the selected equipment.
- Selecting a person gives you access to the "Talk" action for the selected worker.
- You can also inspect an area of your plant. Selecting an area of the plant gives you access to hazard identification information and the Inspect action for the selected area.
- If you have questions, you can access various resources from the "Game Manual".
Choose one of the areas, equipment or workers below to identify hazards:
Equipment
Receiving Area
This is your chance to engage best practices in equipment inspection. Be sure to use all the tools at your disposal to find all of the hazards in the scene. Good Luck!
You found the following hazards:
- Slick surfaces from exposure to rain/snow can cause workers to slip and fall.
- Carbon monoxide due to improper combustion can result in exposures above the PEL.
- When transferring materials from the trailer to facility the workers can stumble/ fall at the trailer/ dock separation.
- Working around an open loading dock has the potential for worker falls.
- When trailer wheels are not chocked, there is potential for inadvertent movement/ dock separation.
- Slick surfaces can cause operators to lose control of equipment/ forklift.
Storage Area
This is your chance to engage best practices in equipment inspection. Be sure to use all the tools at your disposal to find all of the hazards in the scene. Good Luck!
You found the following hazards:
- Charging batteries for the electric forklift can explode due improper venting of the excessive hydrogen gas produced during charging.
- Exits may be blocked due to improper stacking of parts and paints causing workers to be trapped in the area.
- Poisonous chemicals may be spilled during movement or due to faulty/damaged containers.
- Flammable chemicals may be spilled during movement or due to faulty/damaged containers.
- Lubricants may be spilled during movement or due to faulty/damaged containers.
Shearing Area
This is your chance to engage best practices in equipment inspection. Be sure to use all the tools at your disposal to find all of the hazards in the scene. Good Luck!
You found the following hazards:
- Power cords running across the ground and through walkways can become damaged and crushed by pedestrian and equipment traffic.
- Accumulation of dirt, dust and other debris can collect in the work area, increasing the risk of slip & trips.
- Noise from equipment operation may exceed safe operating level standards.
- Accumulation of dirt, dust and other debris can collect in the work area becoming a potential fuel source for a fire.
- Walkways are cluttered with scrap material and debris making workers walk too close to operating equipment.
- Walkways and safe pathways aren't clearly marked or indicated in the area where heavy material is being moved and machined.
- Power cords running across the ground and through walkways can cause trips.
Stamping Area
This is your chance to engage best practices in equipment inspection. Be sure to use all the tools at your disposal to find all of the hazards in the scene. Good Luck!
You found the following hazards:
- Power cords running across the ground and through walkways can become damaged and crushed by pedestrian and equipment traffic.
- Accumulations of dirt, loose material and misc. debris on the ground and in walkways can lead to slips and trips.
- Noise from equipment operation may exceed safe operating level standards.
- Power cords running across the ground and through walkways can cause trips.
- Accumulation of dirt, dust and other debris can collect in the work area becoming a potential fuel source for a fire.
- Doorways to lobbies can become blocked with material and obstruct exits in the event of an emergency.
Finishing Area
This is your chance to engage best practices in equipment inspection. Be sure to use all the tools at your disposal to find all of the hazards in the scene. Good Luck!
You found the following hazards:
- Cardboard boxes and other flammable material stored near the paint booth can ignite.
- Exits may be blocked due to improper stacking of parts and paints causing workers to be trapped in the area.
- Paint solvents and vapors can come in contact with energized inappropriate electrical wiring.
- Eyes may be splashed by liquid or aerosolized paints during painting and curing operations.
- Area workers can be exposed to airborne solvents during equipment maintenance.
- Hands and arms can come in contact with halogenated solvents during vapor degreasing operations.
- Area workers can be exposed to airborne solvent vapors during paint curing/degreasing operations.
- Paint liquids may be spilled or dripped on the floor during painting or curing operations.
Shipping Area
This is your chance to engage best practices in equipment inspection. Be sure to use all the tools at your disposal to find all of the hazards in the scene. Good Luck!
You found the following hazards:
- Improper fuel storage can result in a release of propane gas.
- Improper engine combustion can result in carbon monoxide exposures above the Permissible Exposure Limit (PEL) set by OSHA.
- Workers who enter the trailer while the fork truck is loading/ unloading can be struck by the fork truck.
- When transferring materials from the trailer to facility the workers can stumble/ fall at the trailer/ dock separation.
- Working around an open loading dock has the potential for worker falls.
- Slick surfaces from exposure to rain/snow can cause workers to slip and fall.
- When trailer wheels are not chocked, there is potential for inadvertent movement/ dock separation.
- Slick surfaces can cause operators to lose control of equipment/ forklift.
- Fork trucks operators operating in dark trailer cabs have limited visibility.
- Road surface defects can cause trailers to be off level with the loading dock leading to fork truck tipping.
Crane
This is your chance to engage best practices in equipment inspection. Be sure to use all the tools at your disposal to find all of the hazards in the scene. Good Luck!
You found the following hazards:
- When operating the crane, contact with plant/ equipment power sources can cause electrocution.
- Leaving the crane energized while not in use can lead to inadvertent contact with controls causing crane movement.
- Crane operation in tight quarters can cause load collision with workers or equipment.
You found the following hazards:
- Make shift or non-OEM attachments can cause failure and dropped loads.
- Loads which are not properly secured or balanced can shift, striking workers.
- Worn crane cables and linkages can fail during operation.
You found the following hazards:
- Improper modification by using spreader bars and makeshift attachments can cause load to fall.
- Loads which exceed the capacity of the crane can cause cable/ linkage failure leading to load drops.
- Using improper rigging such as slings, chains, and straps can cause the load to fall.
- Improper rigging of loads can cause tipping.
- If the crane is not inspected, mechanical malfunction can lead to loads falling.
- Loads which exceed the capacity of the crane can cause crane failure resulting in dropped loads.
Electric Forklift
This is your chance to engage best practices in equipment inspection. Be sure to use all the tools at your disposal to find all of the hazards in the scene. Good Luck!
You found the following hazards:
- Workers lifted/elevated on tines can fall.
You found the following hazards:
- Tine extenders and other attachments can cause load instability resulting in falling objects.
- Makeshift modifications made to the forklift tines and/or mast can create hazardous operating conditions.
- Unstable objects might fall off the forklift tines during operation.
You found the following hazards:
- Improper aftermarket battery replacement can cause equipment counterbalance issues.
- Improper load height, weight and speed can cause instability and cause the forklift to tip over.
- Loads improperly secured to the forklift can shift and fall.
Elevated Conveyor
This is your chance to engage best practices in equipment inspection. Be sure to use all the tools at your disposal to find all of the hazards in the scene. Good Luck!
You found the following hazards:
- Clothing, hair, gloves and extremities can become entangled in moving parts on the elevated conveyor during operation.
- Hands can be pinched between the hoisting mechanism and pieces while placing and removing items.
You found the following hazards:
- Unsecured packages stored at elevated levels can become loose and fall on below workers.
- Items not properly secured to the elevated conveyer during movement of parts may fall.
You found the following hazards:
- Conveyor motor can spark and short if not maintained properly.
Guillotine Shear
This is your chance to engage best practices in equipment inspection. Be sure to use all the tools at your disposal to find all of the hazards in the scene. Good Luck!
You found the following hazards:
- Clothing, hair, gloves and extremities can become entangled in unguarded moving machine parts during operation.
- Noise from operation of machine can exceed safe limits in both duration of exposure and intensity.
- Small metal fines & other debris can be can be ejected from the machine when cutting.
You found the following hazards:
- System safety component failure or bypass can cause accidental start-up before a worker is out of the cutting area.
- Oil drips from machine lubrication can cause slippery areas on the floor around the machine.
- Metal fines and waste stock can collect on floor and cause tripping and slipping hazards
You found the following hazards:
- Exposure to lubricants can cause irritation to the skin, eyes and respiratory system.
Packing Station
This is your chance to engage best practices in equipment inspection. Be sure to use all the tools at your disposal to find all of the hazards in the scene. Good Luck!
You found the following hazards:
- Tossing a football/ baseball in the storage area can cause workers to bump shelving and materials to fall.
- Accessing materials on shelving without proper ladders/ stairs can cause worker falls.
- Workers can be exposed to excessive noise levels while shrinking, taping, banding, etc. operations.
- Packing areas littered with debris (obstructions) can lead to slips, trips, & falls.
You found the following hazards:
- Smoking in undesignated area has potential to cause fire.
- Packing materials in low lit areas can cause eye strain.
- Shelving that is loaded top heavy has greater potential to tip.
You found the following hazards:
- Material placed on shelving that cannot support the capacity can fail.
- Workers can be exposed to dermal and inhalation hazards associated with adhesives (packaging).
Paint Booth
This is your chance to engage best practices in equipment inspection. Be sure to use all the tools at your disposal to find all of the hazards in the scene. Good Luck!
You found the following hazards:
- Workers may be exposed to excessive noise from compressed gas during painting operations.
- Painters can be exposed to airborne solvent vapors during paint application operations.
- Workers improperly using respiratory protection during painting operations can result in an overexposure to solvents.
You found the following hazards:
- Ventilation systems that are ineffective or inoperable during painting operations can result in an overexposure to solvents.
- Cardboard boxes and other flammable material stored in the paint booth can ignite.
You found the following hazards:
- Workers can be exposed to hazardous airborne solvent vapors during paint mixing operations.
- Workers may be exposed to airborne isocyanate vapors during paint application operations.
- Workers may be exposed to airborne solvent vapors during paint spray rig and nozzle cleanout operations causing overexposure to solvents.
Press Brake
This is your chance to engage best practices in equipment inspection. Be sure to use all the tools at your disposal to find all of the hazards in the scene. Good Luck!
You found the following hazards:
- Accidental pressing of foot controls can result in machine cycling before the operator extremities are clear of moving parts.
- Accidental start up of the machine during machine set-up and preparation, making adjustments, etc. can cause the machine to cycle.
- Bypassing pullbacks/pullouts to allow a free-er range of movement during work, can result in the dies compressing before the operator is clear.
- Noise from operation of machine can exceed safe limits in both duration of exposure and intensity.
- Using hands to hold metal pieces in place to close to the press can result in cuts, crushing injuries and amputations.
- Metal debris can be can be ejected from the machine during operation.
You found the following hazards:
- Improperly positioned pullbacks/pullouts guards can result in the dies compressing before the operator is clear of moving parts.
- Clothing, hair, gloves and extremities can become entangled in unguarded moving machine parts.
- Accidental selection of automatic mode setting can cause machine to recycle before the operator is clear of moving parts.
You found the following hazards:
- Flying particles or fragments from cracked or unstable die shoes due to improper height setting can cause injury.
- Accidental descent of the slide during start-up or maintenance can result in cuts, crushing injuries and amputations.
- Exposure to lubricants can cause irritation to the skin, eyes and respiratory system.
- Repeat stroke setting can cause machine to recycle before the operator is clear of moving parts.
Propane Gas Forklift
This is your chance to engage best practices in equipment inspection. Be sure to use all the tools at your disposal to find all of the hazards in the scene. Good Luck!
You found the following hazards:
- Operating at excessive speed can cause collisions with workers, equipment, and machinery.
- Working on inclines and declines can cause collisions (braking).
You found the following hazards:
- Makeshift modifications made to the forklift tines and/or mast can create hazardous operating conditions.
- Tine extenders and other attachments can cause load instability resulting in falling objects.
- Unstable objects might fall off the forklift tines during operation.
You found the following hazards:
- Improper engine combustion can result in carbon monoxide exposures above the Permissible Exposure Limit (PEL) set by OSHA.
- Loads improperly secured to the forklift can shift and fall.
- Workers lifted/elevated on tines can fall.
- Based on load height, load weight and speed, the forklift can be unstable and tip over.
Punch Press
This is your chance to engage best practices in equipment inspection. Be sure to use all the tools at your disposal to find all of the hazards in the scene. Good Luck!
You found the following hazards:
- Accidental start up of the machine during machine set-up and preparation, making adjustments, etc. can cause the machine to cycle.
- Unplanned start up and movement of the machine can injure workers.
- Noise from air ejectors can exceed safe limits in both duration of exposure and intensity.
- Handling non-deburred plates without proper precautions or safety equipment can expose workers to sharp edges.
You found the following hazards:
- Flying particles or fragments from cracked or unstable die shoes due to improper die location can cause injury.
- Flying particles or fragments from cracked or unstable die shoes due to improper height setting can cause injury.
- Accidental selection of automatic mode setting can cause machine to recycle before the operator is clear of moving parts.
- Repeat stroke setting can cause machine to recycle without operator knowledge, before the operator is clear of moving parts.
You found the following hazards:
- Clothing, hair, gloves and extremities can become entangled in unguarded moving machine parts.
- Interlocking guard failure can cause accidental start-up of the machine before the worker is clear of moving machine parts.
- Self-adjusting guard failure/obstruction can cause accidental start-up before a worker is clear of moving machine parts.
- Flying particles or fragments caused by waste movement jammed in machine during automatic feed mode can cause injury.
- Using hands to hold metal pieces in place between the die shoes or bolster plates can cause cut and amputations.
- Exposure to lubricants can cause irritation to the skin, eyes and respiratory system.
- Bypassing two-hand controls to use one hand to assist in placing or clearing metal from the press.
Roller
This is your chance to engage best practices in equipment inspection. Be sure to use all the tools at your disposal to find all of the hazards in the scene. Good Luck!
You found the following hazards:
- Clothing, hair, gloves and extremities can become entangled in unguarded moving machine parts.
- Accidental start up of the machine during machine set-up and preparation, making adjustments, etc. can cause the machine to cycle.
You found the following hazards:
- Self-adjusting guard failure/obstruction can cause accidental start-up before a worker is clear of moving machine parts.
- Exposure to lubricants can cause irritation to the skin, eyes and respiratory system.
You found the following hazards:
- Unplanned start up and movement of the machine can strike, or entrap workers.
- Interlocking guard failure can cause accidental start-up of the machine before the worker is clear of moving machine parts.
- Faulty electrical wiring or damage to power cables can expose workers to electricity.
Roller Conveyor
This is your chance to engage best practices in equipment inspection. Be sure to use all the tools at your disposal to find all of the hazards in the scene. Good Luck!
You found the following hazards:
- Clothing, hair, gloves and extremities can become entangled in unguarded pulleys and rollers during operations.
- Faulty electrical wiring or damage to power cables can expose workers to electricity.
You found the following hazards:
- Oil drips from conveyor lubrication can cause slippery areas on the floor around the motor.
You found the following hazards:
- Exposure to lubricants can cause irritation to the skin, eyes and respiratory system.
Shelving
This is your chance to engage best practices in equipment inspection. Be sure to use all the tools at your disposal to find all of the hazards in the scene. Good Luck!
You found the following hazards:
- Accessing materials on shelving without proper ladders/ stairs can cause worker falls.
You found the following hazards:
- Material placed on shelving that cannot support the capacity may fail.
- Incompatibility of chemicals/paints improperly stored can result in a chemical fire.
You found the following hazards:
- Shelving that is loaded top heavy has greater potential to tip.
Stamping Press
This is your chance to engage best practices in equipment inspection. Be sure to use all the tools at your disposal to find all of the hazards in the scene. Good Luck!
You found the following hazards:
- Clothing, hair, gloves and extremities can become entangled in unguarded moving parts during operation.
- Noise from air ejectors can exceed safe limits in both duration of exposure and intensity.
- Using hands to hold metal pieces in place too close to the press can result in cuts and crushing injuries.
- Repetitive movements during operation without sufficient breaks for stretching can lead to worker fatigue and injury.
You found the following hazards:
- Cracked or unstable die shoes due to improper die location may cause flying particles or fragments.
- Cracked or unstable die shoes due to improper height setting may cause flying particles or fragments.
- Oil drips from machine lubrication can cause slippery areas on the floor around the machine.
- Metal fines and waste stock can collect on floor and cause tripping and slip hazards.
- Handling non-deburred metal pieces without proper precautions or safety equipment can result in cuts.
You found the following hazards:
- Accidental start up of the machine during machine set-up and preparation, making adjustments, etc. can cause the machine to cycle.
- Accidental selection of automatic mode setting can cause machine to recycle before the operator is clear of moving parts.
- Repeat stroke setting can cause machine to recycle without operator knowledge, before the operator is clear of moving parts.
- Exposure to lubricants can cause irritation to the skin, eyes and respiratory system.
Vapor Degreaser
This is your chance to engage best practices in equipment inspection. Be sure to use all the tools at your disposal to find all of the hazards in the scene. Good Luck!
You found the following hazards:
- Degreaser solvents are heavy and awkward to handle while refilling the degreaser.
- Degreaser solvents may be spilled during refilling operations resulting in a fire.
You found the following hazards:
- Improper use of respiratory protection during vapor degreasing operations resulting in an overexposure to halogenated solvents.
You found the following hazards:
- Operators can be exposed to airborne solvent vapors during degreaser operations.
Crane Operator
This is your chance to engage best practices in equipment inspection. Be sure to use all the tools at your disposal to find all of the hazards in the scene. Good Luck!
From talking to the worker the following hazards have been identified:
- Quickly entering and exiting the crane cab can create slips, trips, & falls.
- Operating in areas where visibility is limited can lead to collisions and falling objects.
- Workers in close proximity to moving parts on the elevated conveyor can be hit by parts in motion.
Degreaser Operator
This is your chance to engage best practices in equipment inspection. Be sure to use all the tools at your disposal to find all of the hazards in the scene. Good Luck!
From talking to the worker the following hazards have been identified:
- Eyes may be splashed by solvents during vapor degreasing operations.
- Hands and arms can come in contact with halogenated solvents during vapor degreasing operations.
- Degreaser solvents may be spilled on floor during vapor degreasing operations.
Electric Forklift Operator
This is your chance to engage best practices in equipment inspection. Be sure to use all the tools at your disposal to find all of the hazards in the scene. Good Luck!
From talking to the worker the following hazards have been identified:
- Lack of seat belts/restraint use can cause the operator to be tossed from the forklift during operation.
- Operation without attention to surroundings or workers can lead to accidental contacts.
- Operating at excessive speed can cause collisions with workers, equipment, and machinery.
- Operating in a small space with limited walkway protection, pedestrians can be struck by forklift in operation.
Guillotine Shear Operator
This is your chance to engage best practices in equipment inspection. Be sure to use all the tools at your disposal to find all of the hazards in the scene. Good Luck!
From talking to the worker the following hazards have been identified:
- Accidental start up of the machine during machine set-up and preparation, clearing jams, or making adjustments can cause the machine to cycle.
- Placing and removing items from the machine can cause excess strain on backs, necks, and wrists of workers.
- Poorly position controls can cause excess strain on backs, necks, wrists and other areas of workers.
- Sharp edges on cut pieces can cause lacerations.
- Large pieces of metal can become unstable during cutting, shift position and strike workers.
- Large pieces of metal can become unstable during cutting and fall on legs & feet.
- Faulty electrical wiring or damage to power cables can expose workers to electricity.
Loading Dock Clerk
This is your chance to engage best practices in equipment inspection. Be sure to use all the tools at your disposal to find all of the hazards in the scene. Good Luck!
From talking to the worker the following hazards have been identified:
- Crane operation in close/ tight quarters could cause load collision with workers or plant equipment.
- Materials improperly placed on shelving may fall (i.e. round containers/ packaging on flat shelving).
- Packages stored at elevated levels can become loose and fall on below workers.
Maintenance
This is your chance to engage best practices in equipment inspection. Be sure to use all the tools at your disposal to find all of the hazards in the scene. Good Luck!
From talking to the worker the following hazards have been identified:
- Paint solvents and vapors can come in contact with energized inappropriate electrical wiring.
- Area workers can be exposed to airborne solvents during equipment maintenance.
- Paint liquids may be spilled or dripped on the floor during painting or curing operations.
- Slick surfaces from exposure to rain/snow can cause workers to slip and fall.
- Power cords running across the ground and through walkways can become damaged and crushed by pedestrian and equipment traffic.
- Walkways are cluttered with scrap material and debris making workers walk too close to operating equipment.
- Walkways and safe pathways aren't clearly marked or indicated in the area where heavy material is being moved and machined.
- Power cords running across the ground and through walkways can cause trips.
- Power cords running across the ground and through walkways can cause trips.
- Faulty electrical wiring or damage to power cables can expose workers to electricity.
- Accidental motion during maintenance activities such as cleaning and lubricating machine parts can cause injury to workers.
- Hands and arms can come in contact with solvents and isocyanates during maintenance and cleaning.
- Accidental motion during maintenance activities such as cleaning and lubricating machine parts can cause injury to workers.
- Faulty electrical wiring or damage to power cables can expose workers to electricity.
- Unplanned start up and movement during maintenance and repairs can cause workers to become injured.
- Accidental descent of the slide during start-up or maintenance can result in cuts, crushing injuries and amputations.
- Accidental motion during maintenance activities such as cleaning and lubricating machine parts can cause injury to workers.
- Faulty electrical wiring or damage to power cables can expose workers to electricity.
- Unplanned start up and movement during maintenance and repairs can cause workers to become entangled.
- Accidental motion during maintenance activities such as cleaning and lubricating machine parts can cause injury to workers.
- Unplanned start up and movement during maintenance and repairs can injure workers.
- Accidental motion during maintenance activities such as cleaning machine parts and lubricating of machine parts.
- Unplanned start up and movement during maintenance and repairs can cause workers to become injured.
- Accidental descent of the slide during start-up or maintenance can result in cuts and crushing injuries.
- Workers can become trapped in the vapor degreaser during pit cleaning and maintenance operations.
- Eyes may be splashed by solvents during degreaser cleanout and maintenance operations.
- Hands and arms can come in contact with halogenated solvents during vapor degreaser cleanout and maintenance.
- Workers can be exposed to airborne solvent vapors during degreaser cleanout and maintenance operations.
Packer
This is your chance to engage best practices in equipment inspection. Be sure to use all the tools at your disposal to find all of the hazards in the scene. Good Luck!
From talking to the worker the following hazards have been identified:
- When handing materials with bare hands, hands can be cut and punctured.
- Packed materials can fall off working surfaces and injure toes.
- Over tensioning banding on packaging can lead to strapping failure causing bands to hit workers.
- Workers who work for extended periods by themselves have a greater chance of being injured and unable to communicate.
Painter
This is your chance to engage best practices in equipment inspection. Be sure to use all the tools at your disposal to find all of the hazards in the scene. Good Luck!
From talking to the worker the following hazards have been identified:
- Worker muscles and joints can be adversely affected while placing and removing items from the elevated conveyor.
- Eyes may be splashed by liquid or aerosolized paints during paint mixing operations.
- Hands and arms can come in contact with solvents and isocyanates during painting operations.
- Hands and arms can come in contact with solvents during paint mixing operations.
- Eyes may be splashed by liquid or aerosolized paints during cleaning and maintenance operations.
- Material on/near, as well as flammable solvent vapors can ignite due to faulty electrical wiring causing fires.
- Paint solvents and vapors can come in contact with energized improper lighting.
- Large pieces of metal can become unstable during operation and shift position, striking workers.
- Flying particles or fragments from cracked or unstable die shoes due to improper die location.
- Metal plates can become unstable during operation and fall on legs & feet.
Press Brake Operator
This is your chance to engage best practices in equipment inspection. Be sure to use all the tools at your disposal to find all of the hazards in the scene. Good Luck!
From talking to the worker the following hazards have been identified:
- Dies can fall during setting causing cuts, crushing injuries or amputations.
- Poorly positioned controls can cause excess strain on backs, necks, wrists and other areas of workers.
- Repetitive movements during operation without sufficient breaks for stretching can lead to worker fatigue and injury.
- Placing and removing items from the machine can cause excess strain on backs, necks, wrists and other areas of workers.
- Sharp edges on metal pieces can cause lacerations.
- Large pieces of metal can become unstable during operation and shift position, striking workers.
- Flying particles or fragments caused by a machine overload situation when more than one work piece is fed at a time can cause injury.
- Debris can be can be ejected from the machine during operation striking workers.
- Large pieces of metal can become unstable during rolling and shift position, striking workers.
- Debris can be can be ejected from the machine during operation striking workers.
Propane Forklift Operator
This is your chance to engage best practices in equipment inspection. Be sure to use all the tools at your disposal to find all of the hazards in the scene. Good Luck!
From talking to the worker the following hazards have been identified:
- Lack of seat belts/restraint use can cause the operator to be tossed from the forklift during operation.
- Operation without attention to surroundings or workers can lead to accidental contacts.
- Operating at excessive speed can cause collisions with workers, equipment, and machinery.
- Operating in a small space with limited walkway protection, pedestrians can be struck by forklift in operation.
Punch Press Operator
This is your chance to engage best practices in equipment inspection. Be sure to use all the tools at your disposal to find all of the hazards in the scene. Good Luck!
From talking to the worker the following hazards have been identified:
- Metal plates can become unstable during operation and fall on legs & feet.
- Poorly positioned controls can cause excess strain on backs, necks, wrists and other areas of workers.
- Repetitive movements during operation without sufficient breaks for stretching can lead to worker fatigue and injury.
- Placing and removing items from the machine can cause excess strain on backs, necks, wrists and other areas of workers.
Roller Operator
This is your chance to engage best practices in equipment inspection. Be sure to use all the tools at your disposal to find all of the hazards in the scene. Good Luck!
From talking to the worker the following hazards have been identified:
- Large pieces of metal can become unstable during operation and fall on legs & feet.
- Sharp edges on cut pieces of metal can cause lacerations during loading of metal pieces into the roller.
- Poorly positioned controls can cause excess strain on backs, necks, wrists and other areas of workers.
- Placing and removing items from the machine can cause excess strain on backs, necks, and wrists of workers.
Shipper
This is your chance to engage best practices in equipment inspection. Be sure to use all the tools at your disposal to find all of the hazards in the scene. Good Luck!
From talking to the worker the following hazards have been identified:
- Lifting heavy objects can lead to back strain.
- Workers who carry too many packages are at greater risk of muscle fatigue and injury.
- Twisting while carrying and object can cause lower back strain.
Stamp Press Operator
This is your chance to engage best practices in equipment inspection. Be sure to use all the tools at your disposal to find all of the hazards in the scene. Good Luck!
From talking to the worker the following hazards have been identified:
- Accidental pressing of foot controls can result in machine cycling before the operator extremities are clear of moving parts.
- Metal plates can become unstable during operation and fall on legs & feet.
- Poorly positioned controls can cause excess strain on backs, necks, wrists and other areas of workers.
- Placing and removing items from the machine can cause excess strain on backs, necks, wrists and other areas of workers.
- Faulty electrical wiring or damage to power cables can expose workers to electricity.
Stamping Laborer
This is your chance to engage best practices in equipment inspection. Be sure to use all the tools at your disposal to find all of the hazards in the scene. Good Luck!
From talking to the worker the following hazards have been identified:
- Placing and removing items from the conveyor can cause excess strain on backs, necks, wrists and other areas of workers.
- Lifting materials without bending the knees can cause back strain.
- Oil drips from machine lubrication can cause slippery areas on the floor around the machine.
- Metal fines and waste stock can collect on floor and cause tripping and slip hazards.
- Items falling off conveyors during transport can strike workers.
- Large pieces of metal can become unstable during operation and shift position, striking workers.
- Feeding more than one work piece at a time and cause particles or fragments to fly out and strike workers.
- Flying particles or fragments caused by waste movement jammed in machine can cause cuts and lacerations.
- Metal debris can be can be ejected from the machine during operation striking workers.