#252 - Koch Industries (#252)
- Date Signed:
- January 14, 2003; renewed March 06, 2006
- Date Concluded:
- March 06, 2009
- Contact Information:
- Directorate of Cooperative and State Programs, (202) 693-2213
Partnership Overview
In the fall of 2001, Koch Industries, Inc. approached the Occupational Safety and Health Administration (OSHA) about expanding its relationship through a Partnership Agreement between certain Koch companies and OSHA. As a result, a Partnership Agreement was signed in January 2003 and subsequently renewed in March 2006. This Partnership facilitated the relationship by communicating the commitment to develop strong environmental, health and safety (EHS) management systems and to strive toward workplace safety and health excellence. Koch's partnership sites allowed OSHA to reach out to a diverse industry spectrum and to impact safety and health in a meaningful way. The lessons learned from the partnership site participation will be used to further impact health and safety globally at all Koch company sites.
Participating Facilities:
The following facilities were participating in the Partnership when it concluded:
- Ammonia Plant, Beatrice, Nebraska
- Ammonia Plant, Dodge City, Nebraska
- Ammonia Plant, Enid, Oklahoma
- Aviation Hangar, Wichita, Kansas
- C. Reiss Coal Company, Green Bay, Wisconsin
- Koch Carbon BX Coal Terminal, Chicago, Illinois
- Koch Minerals Office Complex, Wichita, Kansas
- Petroleum Coke Pad, Corpus Christi, Texas
The following facilities participated in the Partnership but were not actively participating when the agreement concluded.
- Asphalt Plant, Billings, Montana
- Asphalt Plant, Boise, Idaho
- Asphalt Plant, Catoosa, Oklahoma
- Asphalt Plant, Dodge City, Kansas
- Asphalt Plant, Garden City, Georgia
- Asphalt Plant, Gloucester City, New Jersey
- Asphalt Plant, Reading, Pennsylvania
- Asphalt Plant, Saginaw, Texas
- Fractionator, Hutchinson, Kansas
- Fractionator, Medford, Oklahoma
- Fractionator, Mont Belvieu, Texas
- Isomerization Unit, Conway, Kansas
Partnership Goals:
- Prevent and reduce employee injuries and illnesses
- Develop baseline data
- Use EHS Management System to develop management practices for various health and safety hazards
- Review injury and illness information, identify causal factors, and implement fixes
- Expand awareness of the value of EHS management systems
- Identify opportunities for management and staff to participate in site EHS management system implementation
- Highlight successes to emphasize value of safety and health
- Recognize sites that improve their EHS management systems or develop innovative approaches
- Enhance ergonomic program management
- Integrate ergonomic principles into existing EHS management system programs
- Establish systems that identify ergonomic risk factors, evaluate and control ergonomic risk, and share best practices in ergonomic program management
- Improve communication and knowledge sharing between OSHA and Koch
- Enhance local relations between OSHA and Koch
- Share best practices and lessons learned
- Identify at least two case studies that advance the knowledge of the practical implementation and impact of EHS management systems
- Attend and network at conferences
- Increase Voluntary Protection Programs (VPP) participation
- Identify potential VPP sites
- Seek mentors for facilitation of VPP application
- Use tools such as OSHA Challenge to track sites' progresses to VPP participation
- Increase participation in SGE program
- Enhance contractor safety
- Share and encourage use of information about best practices in EHS management systems (i.e., OSHA e-tools or small business publications) with Koch company contractors
- Develop site training for contractors as appropriate
Partnership Results:
The Partnership concluded on a successful note. First, the Partnership made strides towards its main goal, the prevention and reduction of employee injuries and illnesses as the participating facilities continued to outperform their respective industry average injury and illness rates. At the end of 2008, of the 8 facilities, 6 had Total Recordable Cases of injuries and illnesses (TCIR) rate and 7 had Days Away, Job Restriction or Transfer (DART) rates below their respective industry averages. On the average, the three year (2006-2008) overall TCIR and DART rates of the facilities were 41% and 51% below their industry averages.
Other notable events and achievements of the Koch Industries National Partnership include:
- Publication of the Field Ergonomic Guide
- OSHA/Koch collaboration addresses partnership goal of reducing ergonomic-based injuries which comprise a majority of the injuries partnership-wide
- Partnership-wide distribution launched along with training
- Contractor Safety Training
- Developed by a team of OSHA and Koch Representatives
- VPP Activity
- Koch Carbon facility in Corpus Christi, Texas achieved VPP Star Status
- Koch Aviation in Wichita, Kansas achieved VPP Star Status
- C. Reiss Coal Company achieved VPP Star Status in April 2007 after achieving VPP Merit Status in 2005
- Three facilities are actively pursuing VPP
- Mentored another corporate aviation service which ultimately received VPP Star recognition
Publication of Field Ergonomic Guide
A review of the injury and illness trends shows that the majority of injuries and illnesses were associated with ergonomics and walking/working surfaces. To address this, one of the partnership's objectives in achieving the partnership goal of reducing ergonomic injuries was to publish and implement a field ergonomic guide. The ergonomic task force, formed by the partnership management team in late 2004, met this goal by developing and publishing the guide. Training was provided to the plants safety teams who then began using the guide to help identify ergonomic risk factors.
The ergonomic field guide was shared and implemented at all partnership sites through the use of training sessions. The publication of the guide shows the goal of improved communication and knowledge sharing between OSHA and Koch being met.
To address specific ergonomic hazards, several facilities in the partnership have taken proactive steps. For example, one facility decided to do the following: mandate that all supervisors receive training in ergonomic hazards recognition; require the use of pre-job hazard analyses using a decision matrix to recognize hazards; and purchased specific items to assist employees. Another site had all of its employees receive ergonomic training, added an ergonomic section to each step of its Job Safety Analyses, included contractors in ergonomic awareness trainings which included the ergonomic field guide, and made several modifications to equipment to reduce vibrations.
Contractor Safety
One partnership objective focused on enhancing contractor safety. To address this, This involved providing training to both partnership and non-partnership site representatives in best practices in contractor safety. The committee successfully conducted a training session in March 2005 that involved subject matter experts in contractor safety from OSHA, Koch, and Monsanto. Training was conducted using Video Teleconferencing technology at Koch's Washington D.C. and Wichita offices. The event was well received by all attendees. This effort demonstrates a spirit of cooperation not only between Koch and between OSHA but between other industry safety leaders as well.
Eventually, several partnership sites established teams to specifically focus on making improvements in their contractor programs at their sites. The contractor safety training session shows improved communication and knowledge sharing between OSHA and Koch as well as the increased awareness of the value of EHS management systems, both of which are two of the partnership's goals. At this time, a list of active contractors is vetted and approved based on a grading system that includes performance criteria such as EMR, incident rates, lost time rates and environmental performance. Also, several sites are currently working with consultants to incorporate into their qualifying services a matrix of prescribed training, developed internally by Koch Industries, for which training records are required. Revision of the site hazard reporting and tracking procedure will be accompanied by a parallel review of contractor hazard tracking and abatement verification.
VPP Activity
VPP participation remained a major objective of the Partnership. Three partnership sites achieved VPP recognition and by the conclusion of the Partnership, several sites were actively working toward VPP participation. Addressing the goal, the partnership achieved the following:
- Koch Carbon's Petroleum Coke facility in Corpus Christi, Texas achieved VPP STAR status.
- C. Reiss coal terminal in Green Bay, WI submitted their application and had their on-site assessment
- Koch Nitrogen's facility in Enid, OK conducted their first "VPP gap assessment" and started working with a Region VI OSHA compliance assistance specialist
According to Koch Industries, this Partnership "has set the bar for other Koch affiliates to pursue VPP... Overall the Safety and Health awareness within [the sites] in the Partnership has increased which will lead to an increased number of applications into VPP from selected sites in 2009."
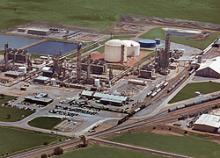
Koch Nitrogen Company operates this facility in Enid, Okla., which produces free ammonia, UAN and urea.
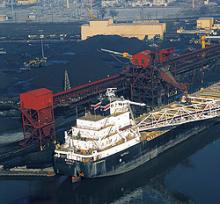
At its bulk-loading terminals, Koch Carbon can load and unload ocean vessels, barges, rail cars and trucks and can also blend, dry, screen or crush material for customers. This facility, located near Chicago on the Calumet River, has more than 1 million tons of storage capacity and handles 4.5 million tons of cargo each year, including various grades of coal and petroleum coke, as well as gypsum, salt, fertilizer and other dry bulk materials.