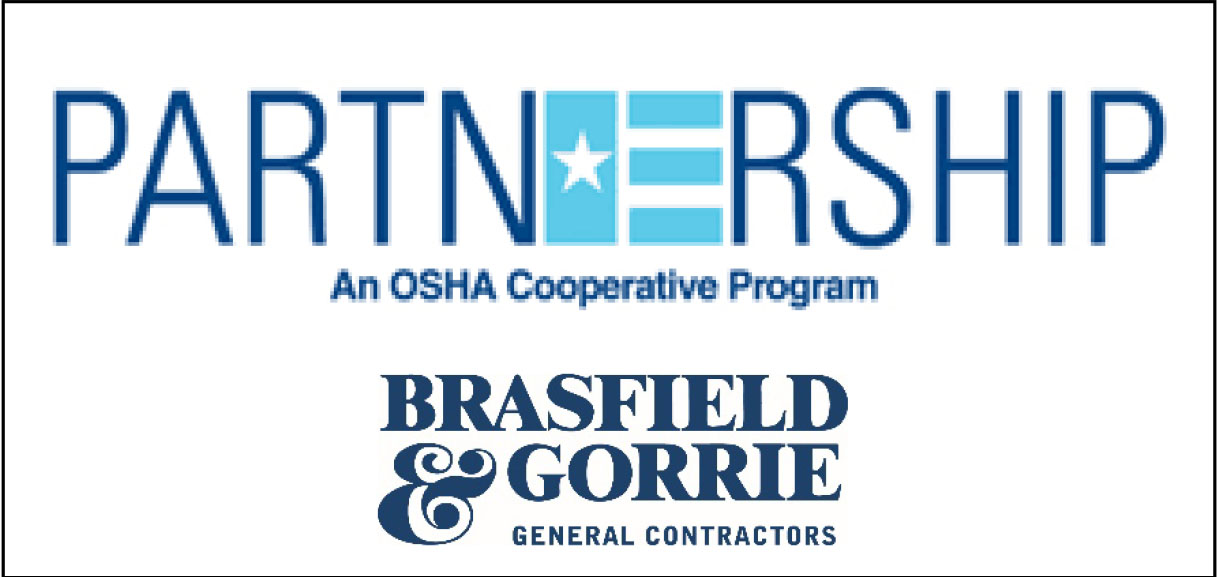
Continental Tire Main Plant
Strategic Partnership
Between
Occupational Safety and Health Administration
Jackson, Mississippi Area Office
And
Mississippi State University, Center for Safety and Health On-site Consultation Program
And
Brasfield & Gorrie, LLC.
-
PURPOSE/SCOPE
This Partnership was developed jointly by the Occupational Safety and Health Administration (OSHA), the Mississippi State University, Center for Safety and Health On-site Consultation Program (MSU-CCE) and Brasfield & Gorrie, LLC (Brasfield & Gorrie). The common objective and goals of the Partnership include the following:
- Reduce injuries and illnesses;
- Increase safety and health training; and
- Increase the number employers with safety and health management systems.
This Partnership is consistent with OSHA's long-range efforts to develop a contractor/government Partnership approach to safety management. It allows for better use of OSHA resources and innovation in safety management. It will also encourage more participation in the safety process from the construction industry.
To facilitate the goal of reducing occupational-related fatalities and serious injuries within the construction industry, OSHA, MSU-CCE and Brasfield & Gorrie will implement a Partnership under the OSHA Strategic Partnership Program (OSPP). This Partnership covers the Continental Tire Main Plant Project in Clinton, Mississippi. The project consists of constructing an approximately 750,000 square foot facility for the new Commercial Vehicle Tire Manufacturing Plant. This construction project will include the following: the main plant building and related site utilities; site infrastructure; paving; hardscape; landscape; a powerhouse building; a guardhouse and fire station building; and a scrap storage building. The scheduled completion for the construction project is June 2019.
By combining their efforts, skills, knowledge and resources, OSHA, MSU-CCE and Brasfield & Gorrie expect to reduce exposure to hazards and thereby decrease the possibility of serious injuries and fatalities at the Continental Tire Main Plant Project.
-
IDENTIFICATION OF PARTNERS
The Partnership participants will include:
- the Occupational Safety and Health Administration; and
- Mississippi State University, Center for Continuing Education
- Brasfield & Gorrie, LLC.
-
GOALS/STRATEGIES/PERFORMANCE MEASURES
The primary objective of this Partnership is to create a working relationship that focuses on preventing work-related fatalities, controlling or eliminating serious workplace hazards, and establishing a foundation for the development of an effective safety and health program. The goals employed to achieve these results will include the following:
GOALS STRATEGIES MEASURES Maintain an OSHA recordable injury frequency at or below the national average for the applicable SIC/NAICS code.
Provide a safe and healthy work environment for construction industry workers employed at this project.
- Review the OSHA 300 Log data of the Partnership participants and their contractors, excluding OSHA.
- Calculate Total Case Incident Rate (TCIR) and Days Away From Work, Restricted, Or Job Transferred (DART)1 rates.
- Compare this data with the baseline rates for the Partnership.
- This goal will be measured by the number of companies participating in the Partnership, which reduce their TCIR and DART rates below the baseline for the Partnership.
- The baseline rate will be based on the 2016 BLS rates for Non-Residential Construction, NAICS 2362, which are 2.4 and 1.3.
Effectively control workplace hazards by increasing the number of construction companies with safety and health management systems (SHMS). Methods to evaluate the participants' performance in this area will include the implementation of comprehensive safety and health management systems and an increase in the number of employers that establish effective safety and health management systems. Compare the number of participants that develop and implement effective SHMS as a result of participating in the Partnership, to the baseline for the Partnership.
The baseline will be established during the initial year of the Partnership.
Increase the number of employees that are provided effective safety and health training, such as the OSHA 10-hour course and relevant Competent Person and user level training. Evaluate employers that provide employees with OSHA 10-hour/ OSHA 30-hour training and appropriate Competent Person and user training and establish baseline. Provide or assist in providing necessary training.
Compare the number of employees provided safety and health training, as a result of participating in the Partnership, to the number of employees provided training during the baseline (initial) year of the Partnership.
1 Days Away from work, Restricted, or job Transferred (DART) rate: This includes cases involving days away from work, restricted work activity, and transfers to another job. It is calculated based on (N / EH) x (200,000) where N is the number of cases involving days away, and/or restricted work activity, and/or job transfer; EH is the total number of hours worked by all employees during the calendar year; and 200,000 is the base number of hours worked for 100 full-time equivalent employees. For example: Employees of an establishment including management, temporary, and leased workers worked 645,089 hours at this worksite. There were 22 injury and illness cases involving days away and/or restricted work activity and/or job transfer from the OSHA 300 Log (total of column H plus column I). The DART rate would be (22 / 645,089) x (200,000) = 6.8 -
OSPP MANAGEMENT AND OPERATION
-
Brasfield & Gorrie:
- Establish a jobsite safety team, consisting of a representative of all primary contractors on site, in order to develop an understanding and awareness that all accidents are preventable and unnecessary, and a comprehensive safety and health management system, which includes:
- Management commitment and employee involvement;
- Hazard analysis;
- Hazard control; and
- Arrangement of training assistance for other stakeholders on site.
- Mentor subcontractors in safety and health management systems. Subcontractors shall include all multi-tiered subcontractors that arrive for work on the site.
- Where the potential for airborne silica exposure exists, require the use of wet-cutting, or soft-cutting techniques and/or a dust collection system in compliance with Table 1 of 29 CFR Part 1926.1153 and when employee exposure levels require, mandatory use of approved respiratory protection. Where the potential for air borne silica exposure exists, personal air monitoring will be conducted to assess employee exposure levels. Where the potential for other health issues exist (i.e., carbon monoxide, lead, or large-scale use of chemicals in the building interior during floor finishing), Brasfield & Gorrie will coordinate with the subcontractor responsible for creating the hazard and ensure that air monitoring is accomplished to assess employee exposure levels. Brasfield & Gorrie will compile and track sampling results.
- Enforce safety rules and regulations. This role includes holding contractors, subcontractors, and employees accountable for following safety rules and regulations and the ability to remove a contractor's employees and supervisors from the job site, if necessary.
- Ensure that a competent person performs a risk assessment of all fall hazards. The probability and severity of occurrence for each identified hazard will be evaluated to eliminate or reduce the risk through engineering or administrative controls to a level as low as possible. Regarding full hazard risk assessments:
- Critical risks will not be tolerated. A critical risk is defined by work that contains high probability in occurrence and high severity in consequence. No work will be performed until action is taken to reduce the level of risk to as low as reasonably feasible.
- All personnel exposed to a fall greater than 6 feet shall conform to Brasfield & Gorrie's 100 percent tie-off for all employees with fall exposure at heights at six feet or greater (see Site-Specific Safety and Health Plan (SSSP)).
- To the extent feasible, serious ergonomic hazards will be identified and corrected.
- Ensure that ground fault circuit interrupters (GFCI) are used to protect all electrical circuits that are used for work. All contractors will ensure that employees are protected by the use of a GFCI at all times.
- Brasfield & Gorrie's Superintendent and on-site Safety Manager will serve as a point of contact, monitor safety and health at the site and its progress toward achievement of the Partnership goals.
- Brasfield & Gorrie's Superintendent and onsite Safety Manager will ensure that daily Safety Audits are conducted. Brasfield & Gorrie will review subcontractors daily logbooks, note any hazards found, and then review them at the weekly coordination/subcontractor meeting.
- Conduct and document job site safety meetings/toolbox talks with subcontractors and their employees on a weekly basis.
- Brasfield & Gorrie's Superintendent and Project Manager will lead, coordinate and conduct a comprehensive site audit on a weekly basis. Safety Committee and subcontractor representatives will participate in the site safety audit. If non-compliant activity or hazards are discovered, immediate correction is required. Brasfield & Gorrie will document the corrective action taken and share this information with OSHA during the monthly update meetings.
- Audit the Partnership and make recommendations for improvement.
- Share the results of jobsite inspections and information concerning near misses with all workers. Near misses and daily safety audits will be discussed during toolbox talks.
- Ensure that no employees are allowed to work directly below a suspended load except for situations where no other safe alternative may exist. In these rare cases, the following criteria must be met:
- Materials being hoisted shall be rigged to prevent unintentional displacement.
- Hooks with self-closing safety latches or their equivalent shall be used to prevent components from slipping out of the hook.
- A qualified rigger shall rig all loads.
- Appropriate use of tag lines will be utilized to minimize work below suspended loads.
- Require the use of appropriate personal protective equipment. Hard hats are mandatory. Employees on-site shall wear high-visibility reflective clothing. A 100 percent eye protection program will be implemented. Gloves must be worn when hand injuries are likely to occur.
- Ensure that all signs and warnings are posted in English and Spanish, as well as any other languages spoken frequently by workers on-site.
- Implement an effective Heat Illness Prevention Program (Heat Program) to educate workers about the hazards of working outdoors in the heat and steps needed to prevent heat-related illnesses.
- Provide all data to OSHA that is needed for the annual OSHA Strategic Partnership Program (OSPP) report.
- Establish a jobsite safety team, consisting of a representative of all primary contractors on site, in order to develop an understanding and awareness that all accidents are preventable and unnecessary, and a comprehensive safety and health management system, which includes:
-
Subcontractors:
- Appoint a representative to the site Safety Committee who will be responsible for resolving job safety matters and serving as a liaison to Brasfield & Gorrie's Superintendent. Every subcontractor will have a person available to participate in the Safety Committee. Participation in this committee will consist of, but will not be limited to, participation in the Project Team Safety walkthroughs and monthly safety update meetings.
- Participate in the monthly Safety Committee/subcontractor meeting and safety audits. If non-compliant activity or hazards are discovered, immediate correction is required. Abatement methods and verification must be submitted to Brasfield & Gorrie's on-site Safety Manager, who will document the correction taken and share this information during the monthly update meetings.
- Conduct jobsite safety inspections for employees under their supervision. These jobsite safety inspections will be in addition to the general inspections that are to occur daily. If non-compliant activity or hazards are discovered, immediate correction is required. Documentation of abatement methods and verification must be submitted to Brasfield & Gorrie's on-site Safety Manager.
- Share the results of jobsite inspections with all workers by posting them in the project office and notifying all workers of the location of the results.
-
OSHA:
- Participate, to the extent resources permit, in the monthly Partnership Committee/subcontractor meetings, but will not participate in the walk around inspection, except that the verification visits (see Section VIII. OSHA Verification below) may be scheduled as part of the weekly walk around inspection.
- Serve as a resource and liaison for Partnership participants and also assist with safety and health training, as resources permit.
- Give priority to the construction project, as resources permit, when technical assistance is needed.
- Audit the monthly reports/documents and make recommendations for improvements in meeting Partnership goals.
- Conduct inspections in accordance with section VIII of this Partnership.
- Conduct the annual Partnership evaluation report in accordance with section VI of this Partnership.
-
MSU-CCE:
- Give priority consideration to requests for services to small contractors who are engaged in work at the Project.
- Support and perform activities and monitoring related to a heat illness prevention programs.
- Support and perform activities including monitoring, if applicable, related to the silica dust generating activities and potential lead exposure arising from interior demolition activities.
- Support, perform, and monitor activities related to safety focus areas not limited to, falls, confined space, trenching, excavation, and noise generating activities.
-
-
SAFETY AND HEALTH MANAGEMENT SYSTEM
Brasfield & Gorrie will use its system to collect and analyze injury and illness trends (including near-miss incidents) by all contractors performing work at the site. This data will be used as a tool to ensure continual safety and health improvement at the site. Brasfield & Gorrie will manage this Partnership effectively by implementing a comprehensive jobsite safety and health management system, which will include the following components:
- Brasfield & Gorrie will complete a risk assessment prior to exposing employees (including contractors' employees) to potential safety and health hazards. This will be accomplished by the use of a Crew Work Plan - Risk Assessment (CWP) form (see Appendix 1 for Crew Work Plan).
- Work with OSHA, MSU-CCE and Safety Committee members to provide the resources to conduct initial monitoring for toxins, which are anticipated to be present during construction of this project (silica, etc.). Employee exposures during activities, which may produce these hazards, will be assumed and respiratory protection worn until the results of the initial monitoring studies are received and demonstrate no exposure problems or site-based prior surveys show no hazard exists. Brasfield & Gorrie will endeavor to ensure that no work with these materials will occur, thus preventing any exposure.
- Daily audits will be performed by all contractors on-site. In addition, on a weekly basis, a comprehensive audit of the jobsite will be performed, with the participation of a representative of each contractor currently working on-site. Any hazards found during the audits will be corrected promptly. Items noted on the audit will be annotated on a daily log. When hazards cannot be corrected immediately, they will be tracked until abatement is completed. Employees exposed to these hazardous conditions will be informed of the hazard and effective interim control measures will be implemented. A record will be kept of all hazards found during the weekly audits and the number of hazards corrected as a result of the weekly audits.
- Implement an aggressive Fall Protection Plan to include fall protection in all cases where work is being performed 6 feet or more above lower surfaces.
- Ensure employees receive training as follows:
- Brasfield & Gorrie workers will have received OSHA 10-hour training and possess an OSHA 10-hour card, and all Brasfield & Gorrie supervisors will have received OSHA 30-hour training and possess an OSHA 30-hour card. Brasfield & Gorrie will work with all subcontractors to provide or assist in providing their safety designee with OSHA 10-hour training.
- All employees will receive a site-specific construction safety orientation covering jobsite safety and health issues, procedures relative to the work being performed, as well as the requirements outlined in the Partnership. In addition, employees shall receive training on the content of the Site-Specific Safety Action Plan for operations they will encounter. This may require periodic retraining of employees on the content of the Site-Specific Safety Action Plan as specific parts of the Plan become relevant at new phases of construction. This material will be provided by Brasfield & Gorrie to the subcontractors' designated safety representative for completion (see Appendix 2 for SSSAP).
- Safety and health training, including the OSHA 10- and 30-hour courses, will be provided to all workers in a language they understand. Either effective translators or bi-lingual instructors will be utilized to perform this training.
- Additional hazard-specific training will be conducted on an as-needed basis.
- Subcontractors utilizing other instructors for competent person, OSHA 10/30-hr, and equipment training must provide a valid certification card showing completion of the course. Subcontractors have primary responsibility for providing the safety and health training.
- Subcontractors with written safety and health management systems must submit them to the SNFS, A JOINT VENTURE Team for evaluation. Companies without safety and health management systems may adopt the SNFS, or develop an adequate safety and health management system with the assistance of the Georgia Tech or an accepted outside consultant.
- Ensure the SNFS, A JOINT VENTURE Team and/or the affected subcontractors adequately address health-related issues that occur during the course of the project, with the assistance of OSHA, as its resources permit, and Georgia Tech. All health-related issues will be discussed monthly during the Partnership meetings.
- An effective hearing conservation program, including noise monitoring and engineering controls, where possible, will be implemented by the SNFS safety department.
- An effective environmental monitoring program will be implemented to control airborne hazards, such as silica, and will include personal monitoring, employee training, implementation of engineering controls where possible, and the use of respiratory protection when necessary. Previous site-based data will be considered acceptable.
- Subcontractors will be required to develop an adequate safety and health management system and must submit them to Brasfield & Gorrie for evaluation.
- Ensure Brasfield & Gorrie and/or the affected subcontractors adequately address health-related issues, which occur during the course of the project, with the assistance of OSHA as its resources permit. All health-related issues will be discussed monthly during the Partnership update meetings.
- An effective hearing conservation program, including noise monitoring and implementation of engineering controls, where possible, will be implemented by Brasfield & Gorrie's Safety Department.
- An effective environmental monitoring program will be implemented to control airborne hazards, such as silica, and will include personal monitoring, employee training, implementation of engineering controls where possible, and the use of respiratory protection when necessary. Previous site-based data will be considered acceptable.
- Ensure compliance with the NFPA 70E when working on live electrical equipment, including training and the availability and use of personal protective equipment. A permit system will be implemented whenever work around live electrical systems will be done to ensure the implementation of appropriate protective measures prior to exposure. The permit form includes requirements for pre-task review and lock out/tag out procedures to be followed.
- Ensure all equipment is adequately guarded.
-
ANNUAL EVALUATION
The Partnership will be evaluated on an annual basis through the use of the Strategic Partnership Annual Evaluation Format as specified in Appendix C of OSHA Instruction CSP 03-02-002, OSHA Strategic Partnership Program for Worker Safety and Health.
Brasfield & Gorrie will be responsible for gathering required participant data to evaluate and track the overall results and success of the Partnership. This data will be shared with OSHA. OSHA will be responsible for writing and submitting the annual evaluation.
-
INCENTIVES
Participant incentives from OSHA may include:
- Maximum penalty reductions for good faith and history, to the extent allowed by the OSHA Field Operations Manual (FOM), OSHA Instruction CPL 02-00-160 (August 2, 2016).
- In the event that a citation with penalties is issued, the Area Director has the authority to negotiate the amount of an additional penalty reduction as part of the informal conference settlement agreement, which is consistent with OSHA's current policy regarding this matter.
- Priority consultation service and assistance for small employers working on the construction site from the MSU-CCE.
- An OSHA focused inspection is available where the Partnership participant has an effective safety and health management system fully compliant with 29 CFR 1926.20 and 29 CFR 1926.21 (For additional details refer to the August 22, 1994, memo signed and issued by former Deputy Assistant Secretary for OSHA James Stanley, which was revised in September 20, 1995.)
-
OSHA VERIFICATION
- Verification Enforcement Inspections: OSHA will conduct the initial verification enforcement inspection no sooner than two months, but within three months after Partnership participants formally enter into this agreement. During this period, participants should develop and implement the safety and health management systems required under this Agreement. After this period, OSHA will conduct an annual verification enforcement inspection. Compliance officers that are familiar with the Continental Tire Main Plant Project Strategic Partnership will do verification inspections. Employee rights under the OSH Act will be afforded. If during the verification enforcement inspections OSHA personnel identify serious hazards, the scope of the inspection may be expanded.
- Complaint/Referral Investigations: This Partnership provides for the immediate response to each allegation of a safety or health hazard brought to its attention by any person. Upon a finding that an allegation is valid, the employer shall promptly abate the hazard.
- OSHA agrees that a copy of each non-formal complaint/referral related to the work site and filed with OSHA will be delivered to the Continental Tire Main Plant Project office by a Compliance Safety and Health Officer (CSHO), or forwarded by fax. In accordance with applicable law, the name of the complainant requesting confidentiality will not be revealed. Brasfield & Gorrie agrees to investigate these complaints, regardless of the employer involved and provide OSHA with a written response within 5 working days of receiving the non-formal complaint/referral.
- Accident Investigations: Employers engaged in this Partnership recognize that OSHA fully investigates accidents involving a fatality or serious physical harm. If during the course of the investigation OSHA determines that the incident resulted from violations of OSHA standards, the Partnership may be terminated.
-
WORKER INVOLVEMENT/WORKER AND EMPLOYER RIGHTS
This Partnership does not preclude employees and/or employers from exercising any right provided under the OSH Act (the Act), nor does it abrogate any responsibilities of the Partnership participants to comply with rules and regulations adopted pursuant to the Act.
Brasfield & Gorrie, LLC will ensure employee involvement by establishing an employee Safety Committee that will meet on a monthly basis to share the results of jobsite inspections, information concerning accidents and near misses, suggestions for improvement and recommendations for training for the general workforce. The Partnership members' management and supervisors will also continue to discuss near misses and daily safety audits during toolbox talks.
-
TERM OF PARTNERSHIP
It is understood that this Partnership shall be in effect until completion of construction activities at the Continental Tire Main Plant Project site, but in no case longer than three years from the date the Partnership is signed. If any signatory of this Partnership wishes to terminate their participation prior to the established termination date, a written notice of the intent to withdraw must be provided to all other party(s), which provides a 30-day notice.
If OSHA chooses to withdraw its participation in the Partnership, the entire Partnership is terminated. Any party may also propose modification or amendment of the agreement. Changes may be implemented, if all parties are in agreement that the changes are in the best interest of the Partnership.
-
CONTINENTAL TIRE MAIN PLANT
STRATEGIC PARTNERSHIPPartnership Signing Date: _________________________
- Courtney Bohannon
- Area Director
- Occupational Safety & Health Administration (OSHA)
- Kenny Kossow
- Senior Safety Manager
- Brasfield & Gorrie, LLC
- Davern Jones, CSP
- Program Manager, Sr. Industrial Hygienist
- Mississippi State University,
- Center for Safety and Health
- Andrew Hannah
- Senior Project Manager
- Brasfield & Gorrie, LLC
- Steve Sawyer
- Regional Safety Director
- Brasfield & Gorrie, LLC
- Steve Manown
- Division Manager
- Brasfield & Gorrie, LLC
- Brandon Speegle
- Superintendent
- Brasfield & Gorrie, LLC
- Chad Patterson
- Senior Project Manager
- Brasfield & Gorrie, LLC
Appendix 1
REMIND CREW:
YOU SEE IT, YOU OWN IT, YOU SHARE IT
Every crew member has an obligation to stop work if something is unsafe.
CREW WORK PLAN SIGN IN/SIGN OUT
CREW SIGNATURES: By signing below, crew member acknowledges complete understanding of the assigned task, identified hazards and the appropriate elimination/mitigation actions. By initialing at the end of the day, each crew member acknowledges that they were not injured. All incidents and injuries should be reported immediately to Brasfield & Gorrie Supervisor.
INVOLVED CREW MEMBERS
Name | Initial Out |
1. | |
2. | |
3. | |
4. | |
5. | |
6. | |
7. | |
8. | |
9. | |
10. | |
11. | |
12. | |
13. | |
14. |
ANY CREW MEMBERS (LESS THAN 90 DAYS)
Names:_______________________________________
Assigned Coaches:____________________________
Names:_______________________________________
Assigned Coaches:____________________________
*Hardhat Decal should be in place to identify new employees
CREW LEADER POST WRAP UP
Foreman/Crew Leader:_________________________
Did we meet or exceed our production goals today?
Yes No
If no, what prevented us from reaching our goals?
________________________________________
________________________________________
What did we learn that we can share with the crew tomorrow?
________________________________________
________________________________________
Is the work area clean and free of debris from the days work?
Yes No
Were there any injuries, property damage, or near misses reported today?
Yes No
If yes, notify your Superintendent and the safety department immediately. Who was contacted:
________________________________________
Description of event:____________________
________________________________________
________________________________________
________________________________________
REVIEWERS
Superintendent:_________________________
Safety:_________________________________
MANAGEMENT PARTICIPATION
Name:___________________________________
DAILY CREW
WORK PLAN
Dates:___________________________________
Project Name:____________________________
Client Name:_____________________________
Location:________________________________
Foreman:_________________________________
Weather Forcast:_________________________
PRODUCTION GOALS
What are your production goals for today? |
1. |
2. |
3. |
4. |
5. |
6. |
SERIOUS INJURY PRECURSORS
My Highest Risk Activity Today:_______________
________________________________________
□ Work at Height
□ Utilities Located/Verified
□ Excavation over 4'
□ Rigging/Lifting Operations
□ Demolition
□ Heavy Equipment Movement
(Interaction with foot traffic)
□ Stored Energy/LOTO
□ Traffic Control
□ Overhead Operations (Barricading)
□ Manual Handling
□ Working around/near General Public
Start with and Spend Extra Time on any High Risk Activity Identified.
CREW INVOLVEMENT QUESTIONS
________________________________________
________________________________________
________________________________________
________________________________________
- 1. What changed that will impact our work today? (weather, hazards from other trades, access/egress, location, elevated work, additional material handling, chemicals, new crew members, lighting, public interaction, etc.)
- 2. What did we learn during our last shift that can help us be more productive and safe today?
EMERGENCY ACTION PLAN
Evacuation Route/Assembly Area:
________________________________________
Emergency Phone Number:
________________________________________
Location Address:
________________________________________
EMPLOYEE CERTIFICATIONS REQUIRED
(Check all that Apply)
□ Competent Persons (excavation, Confined
Space, Scaffolds, Fall Protection)
□ Crane Operator
□ Forklift Operator
□ Rigging/Signal
□ Powder Actuated Tool User
□ Aerial Lift
□ Scissor Lift
□ Respiratory/Fit Testing
□ Traffic Control Flagger
PERMITS REQUIRED FOR TODAY'S WORK
□ Confined Space
□ Excavation
□ Lockout/Tag out
□ Critical Lift
□ Burn/Hot Work
□ Line Break/Hot Tapping
□ Scaffolding
□ Utility Clearances
□ Lane Closure
Other:__________________________________
JOB/TASK STEP |
POTENTIAL HAZARDS OR ERRORS |
ELIMINATION/CONTROL ACTIONS |
START WITH THE MOST HAZARDOUS WORK FIRST Consider work that is unfamiliar to any crew member as higher risk. Extra time needs to be spent providing CLEAR, |
||
Appendix 2
SITE-SPECIFIC SAFETY ACTION PLAN (SSSAP)
PROJECT: Continental Tire Main Plant
LOCATION: 3000 Continental Parkway, Clinton, MS 39041
PROJECT CONTACTS
Sr. Superintendent:
Superintendent:
Division Manager:
Sr. Project Manager:
Sr. Project Manager:
Job Site Assistant:
Sr. Safety Manager:
Reg. Safety Manger:
Randy Morgan
Brandon Speegle
Steve Manown
Andrew Hannah
Chad Patterson
Karon Leach
Kenny Kossow
Steven Sawyer
205-714-1235 (O)
678-414-9738 (C)
205-714-1640 (O) / 205-238-8023 (C)
205-714-1659 (O) / 205-960-7936 (C)
205-714-1625 (O) / 615-456-0260 (C)
207-294-2812 (C)
205-552-8323 (C)
205-714-1789 (O) / 205-903-4522 (C)
Project Narrative:
The project consists of constructing an approximately 750,000 square feet facility for the New Commercial Vehicle Tire Manufacturing Plant. This work package covers construction of the Main Plant Building, related site utilities, site infrastructure, paving, hardscape, and landscape. In addition to the Main Plant Building, this package includes a Powerhouse Building, a Guardhouse/Fire Station Building, and a Scrap Storage Building.
Scope of Work:
Brasfield & Gorrie's primary work load will consist of general construction. All site employees will be required to complete daily Crew Work Plan meetings and will be supervised by a site foreman. The superintendent and safety manager will have the responsibility of enforcing safety on a daily basis. Brasfield & Gorrie will assist subcontractors with site coordination and planning.
Public Protection:
During non-working hours the jobsite's gates shall be locked. No trespassing signs shall be posted in conspicuous areas on the perimeter of the project to warn the public to stay out of the site. Manned security will be implemented during non-work hours in the evenings and weekends. All visitors will be required to sign-in at the Brasfield & Gorrie office trailer. B & G management will be responsible for making sure all visitors are accompanied on the project and are informed of site personal protective equipment requirements.
Orientation:
Site specific orientation will be held on an as needed basis. All employees who are or will be working on site must attend this training prior to beginning work on the project. This training will encompass site safety, procedures, hazard communication, emergency planning, and basic construction safety. A site-specific orientation sticker will be issued to all employees who attend this training and complete safety acknowledgment form.
Site Logistics:
All haul roads will be built and maintained by site contractor. Laydown area is available to each subcontractor as needed. Work will only take place in the day time unless light towers are installed to provide workers with adequate visibility. Wash out areas will be provided to concrete trucks and pump trucks in areas that will not affect traffic. Brasfield & Gorrie will manage trash dumpsters on the project.
Crane Operations:
Only certified crane operators will be allowed to operate cranes on site. Only qualified riggers/flaggers will be allowed to signal the crane and rig loads to be flown. Hand signals/radios will be used to communicate with the crane operator. Whistles will be used to alert all employees in the area that a pick is being made. All loads must have a non-conductive tag line attached. For mobile cranes, the swing radius of the crane must be barricaded at all times. Outriggers must have appropriate cribbing in place prior to any loads being flown.
If a crane's working radius encompasses active power lines, one of the following must be done:
- De-energize and ground the power lines (Must be done by the appropriate utility company)
- Maintain a minimum 20 feet safe approach distance
- Determine the voltage of the lines and follow safe approach distances Table 4.2 in SHEMS
Personal Protective Equipment:
Hard hats, high visibility vest or shirt, long pants, work boots, and safety glasses shall be worn at all times. This practice will be enforced on a daily basis as per Brasfield & Gorrie's safety policy. Brasfield & Gorrie will monitor subcontractors PPE at all times. Failure to wear mandatory PPE will result in verbal and written warning. If problems persist employees may be suspended or removed from the project.
Fall Protection:
All subcontractors will be required to have fall protection when exposed to a fall of 6' or greater. Brasfield and Gorrie has a zero-tolerance policy on fall protection infractions. Any employee observed violating the fall protection policy will be suspended from the project for a time-period to be determined by the project team. Any further infractions by that employee will result in the employee's permanent removal from the project.
Each subcontractor is required to create a plan or system to address fall protection within their scope of work. These plans or systems are maintained in their company's site-specific safety plans. Each company's site-specific plan is kept at the B & G office trailer.
Guardrails and Floor Opening Protection:
All guardrails, both wire rope and wooden, will be built to comply with Brasfield & Gorrie SHEMS manual. The top railing will be at 42" +/– 3" and able to withstand a downward and outward force of 200 lbs. All railings will include a mid-rail set at 21" +/- 3"and able to withstand a force of 150 lbs. All guardrails that are in locations with work or foot traffic under them shall have toe-boards installed to prevent materials and tools from falling. This toe-board will be maintained until glass or precast concrete is set on the exterior of the building rendering them un-needed. If wire rope is used for guardrails, the wire rope must be at a minimum 3/8" diameter and flagged every 6'. The wire rope must be kept taut so it will be able to withstand a force of 200 lbs. and not sag below 39". Three clips must be installed at attachment points with 3" spacing between them.
All floor holes that are 2'' or greater will be covered with plywood and marked with hi-vis paint. Any holes over 8" will be identified with the words "Hole or Cover" and "Hoyo". In the case of depressions/recesses, the area will be flagged off to warn of the depression or the edge will be painted with hi-vis paint. All covers will be secured to prevent accidental displacement. Hole covers must be made to withstand twice the weight of worker, materials, and tools. No materials can be stored around or on top of hole covers. Covers must be kept well maintained and swept clean.
Roof Access:
Only authorized personal will be allowed on the roof. Fall protection will be required around leading edges beyond warning lines. Roofers will install a warning line 6' back from the edge of the roof. This warning line is only to be used by the roofer. All other subcontractors will be required to install a warning line 15' back from the roof if desired. If work is to take place beyond the warning line, a fall restraint or fall arrest system must be utilized.
Trenching and Utility Lines:
Brasfield & Gorrie and all subcontractors involved in trenching activities will be required to complete an excavation inspection for all excavations or trenches that are 4' or deeper. These reports will be completed daily, after rain storms, and after an event where conditions may change the characteristics of the trench. These are to be completed by a competent person and submitted to Brasfield & Gorrie. Trenches of significant depth or trenches that are obstructed from view shall be flagged to prevent accidental injury. Trenches 4' or greater in depth will have a means of access and egress (ladder, ramp, stair, etc.). All trenches shall be guarded or sloped when at a depth of 5' or greater. In compliance with SHEMS, Brasfield & Gorrie will assume all soils are type C until a soils engineer proves otherwise. Acceptable sloping for trenches or excavations 5' in depth or greater is 1.5:1. Any excavations or trenches 20' or greater in depth must have shoring/shielding system designed by a registered professional engineer.
All utilities will be located by a third party prior to any excavation or trenching activities. If utilities are present in the proposed excavation, soft digging methods must be utilized. Once utilities have been uncovered, they must be brace and protected from damage.
Safety Meetings and Training:
All subcontractors are required to attend the weekly project safety meeting. Brasfield & Gorrie will provide site specific orientation to all new employees on site. Orientation and hazard awareness training will be administered on an as needed basis. PM/Superintendent safety walks will be held biweekly and a supervisory member of each subcontractor is expected to attend. All deficiencies identified will be sent to the responsible subcontractors via emails. Subcontractors are required to respond to these deficiencies in writing within 48 hours. Failure to abate deficiencies or respond in writing could delay payment.
Emergency Action Plan:
Emergency Action Plan (EAP) will be posted in common areas around the project site (Brasfield & Gorrie trailer, job boards, break areas, etc.). The plan will be included in each employee's orientation. The EAP will be reviewed periodically during site wide safety meetings and scheduling meetings. This plan is subject to change, as the site progresses, all employees will be notified and retrained if any changes are made. Please see the site specific EAP on the following pages.
CONTINENTAL EMERGENCY ACTION PLAN
Key Personnel and Contract Info
- Randy Morgan (Sr. Supt.) 205-714-1235 (O)
- Andrew Hannah (Sr. PM) 205-960-7936 (C)
- Chad Patterson (Sr. PM) 615-456-0260 (C)
- Kenny Kossow (Safety) 205-552-8323 (C)
ALTERNATES:
- Brandon Speegle (Supt.) 678-414-9738 (C)
EMERGENCY NUMBERS:
- Clinton MS Fire Department 911 or 601-925-1001
- Bolton Police Department 911 or 601-866-7233
- Merit Health Central Hospital 911 or 601-376-1000
SHELTER IN PLACE
LIGHTNING
- Monitor weather via WeatherBug, Weather Underground, etc. – Kenny Kossow (Alt: Brandon Speegle)
- If lightning is within 10 miles, halt all outdoor activity and notify employees to seek shelter (text/radio) – Kenny Kossow (Alt: Brandon Speegle)
- Sound All Clear (Text/Radio) once lightning is more than 10 miles away – Kenny Kossow (Alt: Brandon Speegle)
SEVERE WEATHER
- Monitor weather via sources above – Kenny Kossow (Alt: Brandon Speegle)
- All personnel notified of severe weather and told to proceed to shelters via text – Kenny Kossow (Alt: Brandon Speegle)
- Verify all employees accounted for in Shelters – Kenny Kossow (Alt: Brandon Speegle)
- Give the All Clear Alert (Text/Radio) – Kenny Kossow (Alt: Brandon Speegle)
MEDICAL EMERGENCIES AND 1st RESPONDERS
- Notify 1st Responders (Who, What, Where) - Kenny Kossow (Alt: Brandon Speegle)
- Retrieve First Ait Kit/AED - Kenny Kossow
- Perform First Aid/CPR (if needed) - Kenny Kossow
- Entrances manned to flag and guide Emergency Vehicles into site - Kenny Kossow
BUILDING/SITE EVACUATIONS
FIRE
- All personnel notified of fire and told to evacuate to nearest Assembly Area via Text/Radio - Kenny Kossow (Alt: Brandon Speegle)
- Attempt to extinguish fire (if incipient) - Kenny Kossow
- If fire can't be contained, notify Emergency Responders - Kenny Kossow (Alt: Brandon Speegle)
- Entrances manned to flag and guide Emergency Vehicles into site - Kenny Kossow (Alt: Brandon Speegle)
- 1st Responders guided to staging areas/scene - Kenny Kossow (Alt: Brandon Speegle)
- Verify all employees accounted for at Assembly Areas - Kenny Kossow (Alt: Brandon Speegle)
GAS LEAK
- All personnel notified of gas leak and told to evacuate to nearest Assembly Area via Text/Radio - Kenny Kossow (Alt: Brandon Speegle)Kenny Kossow (Alt: Brandon Speegle)
- Notify Emergency Responders - Robert Gambill (Alt: Walton Stone)
- Entrances manned to flag and guide Emergency Vehicles into site - Kenny Kossow (Alt: Brandon Speegle)
- Verify all employees accounted for at Assembly Areas - Kenny Kossow (Alt: Brandon Speegle)
- All Clear (Text/Radio) - Kenny Kossow (Alt: Brandon Speegle)
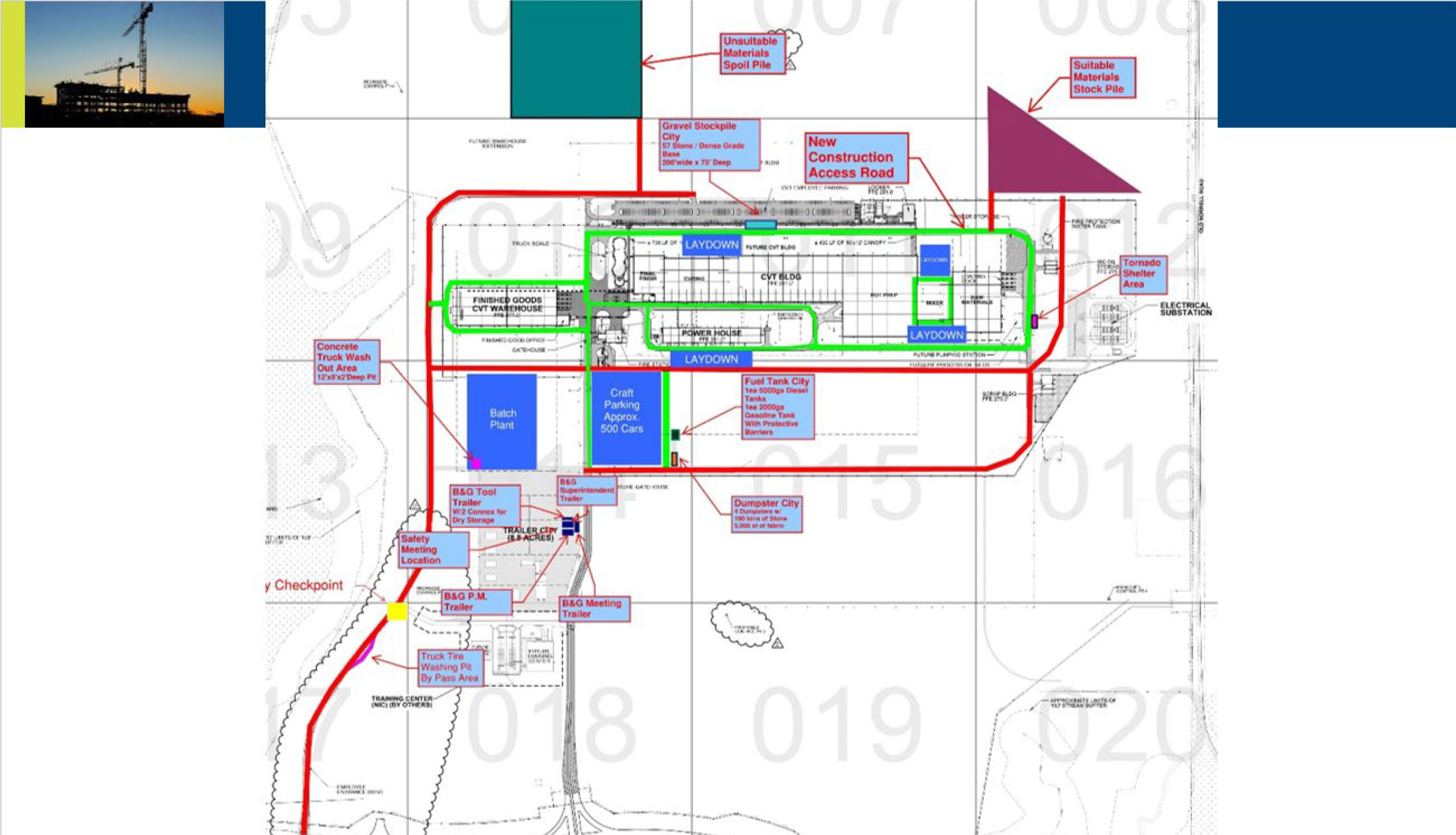
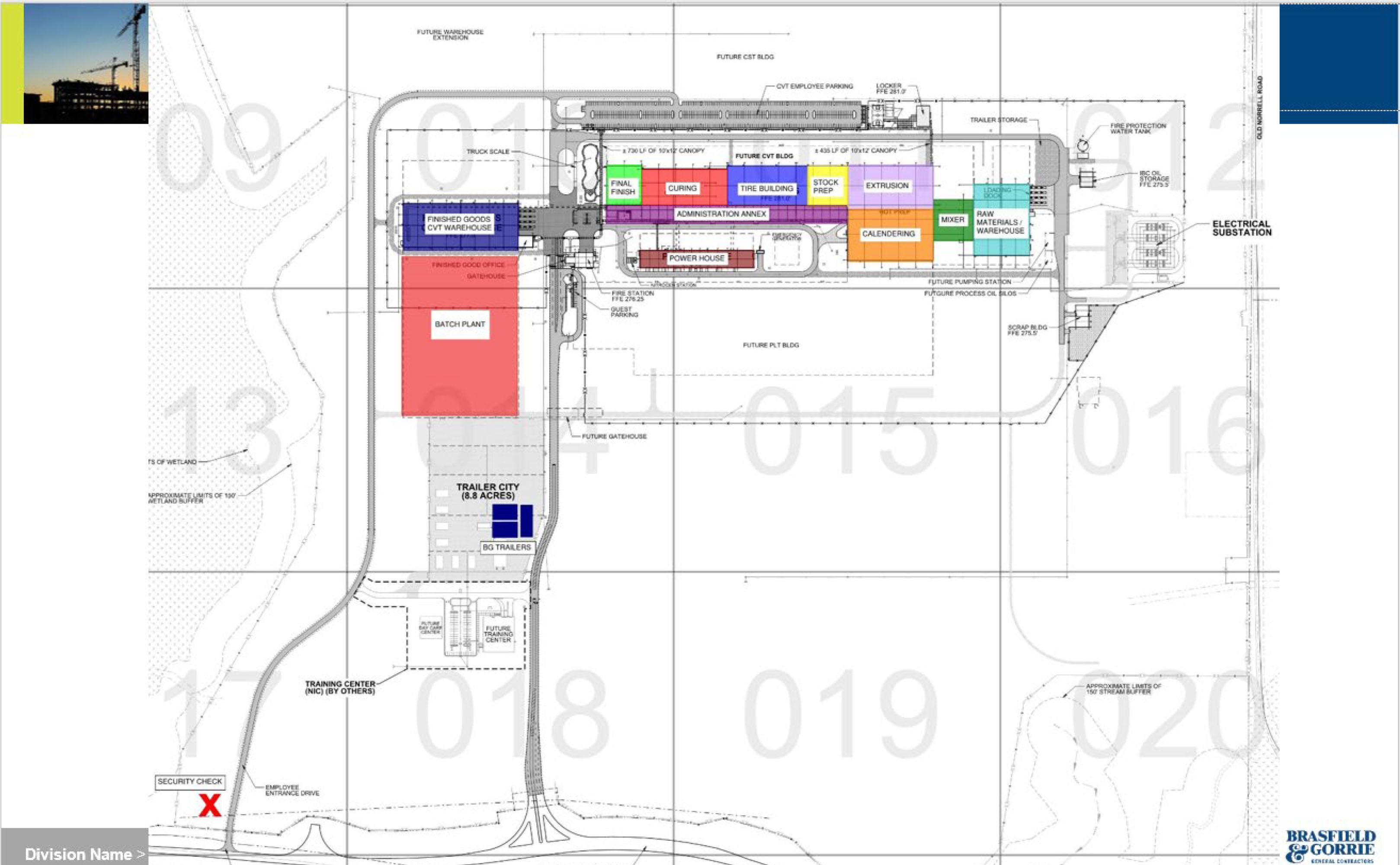
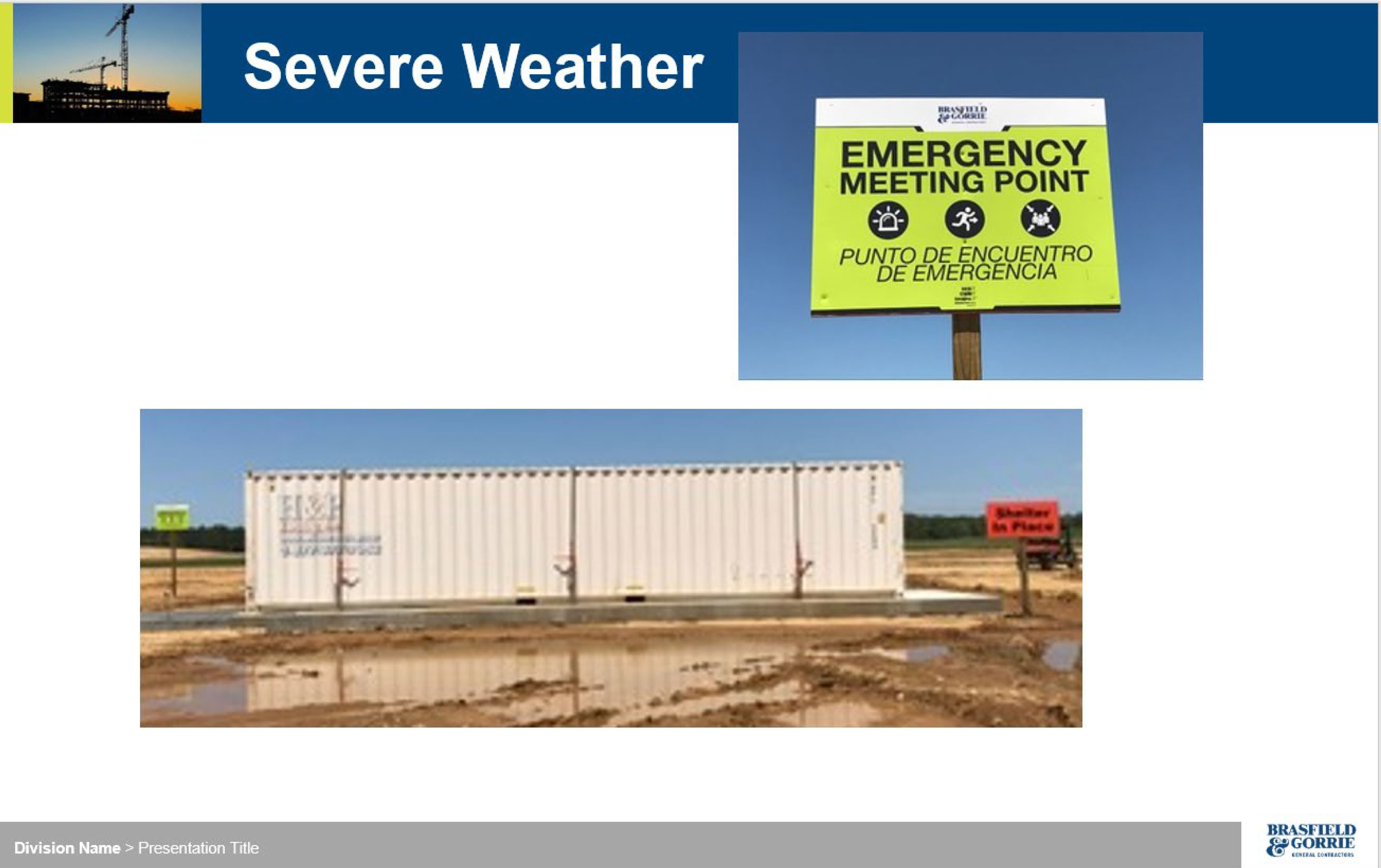
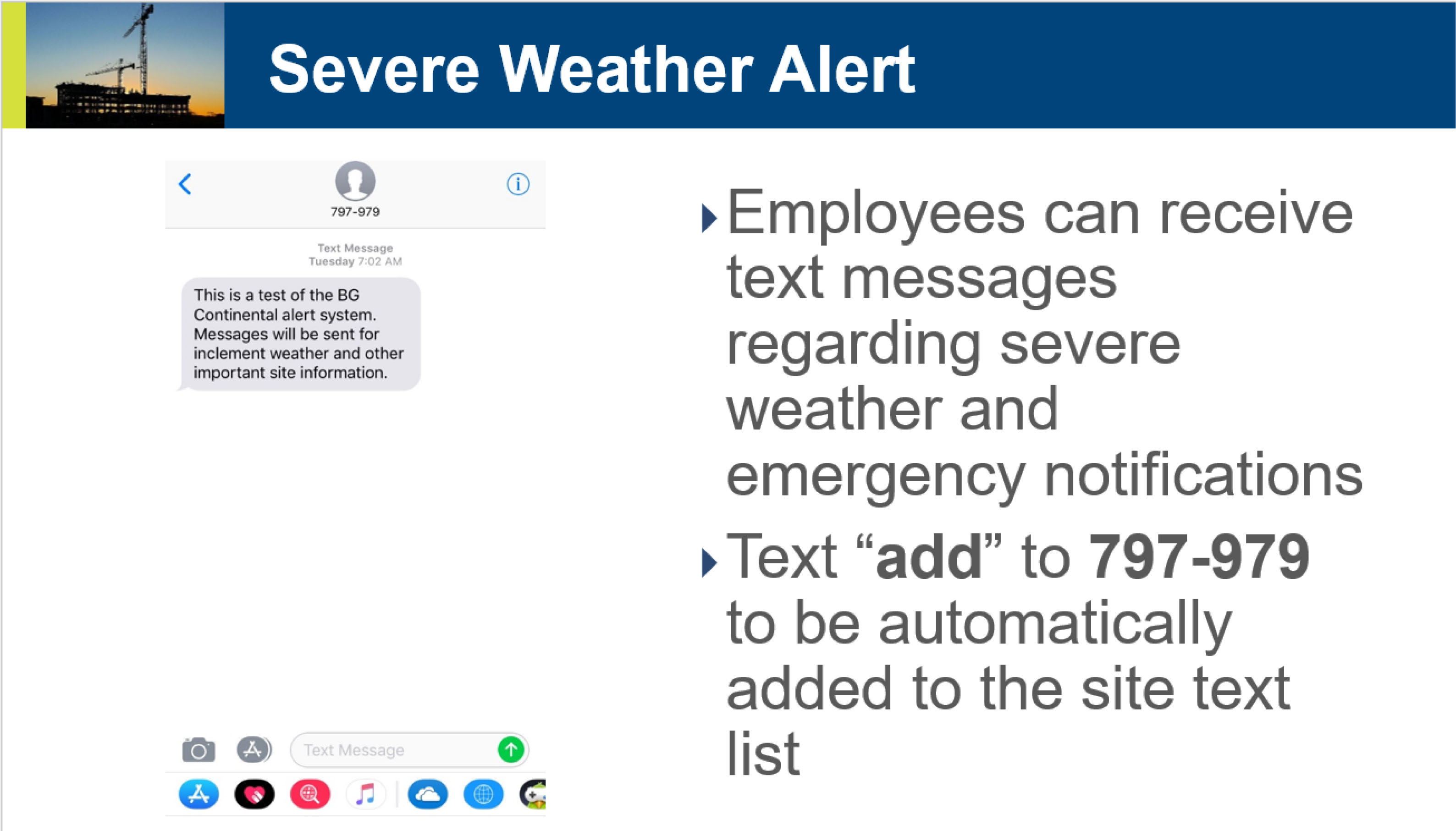