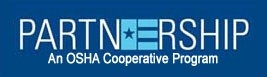
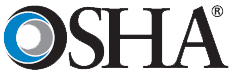
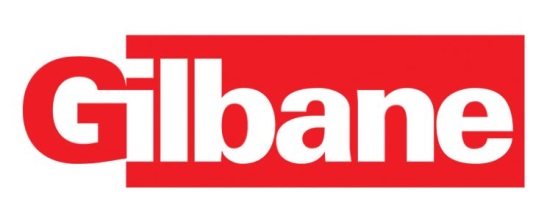
The Georgia Tech Campus Center Project -
OSHA Strategic Partnership
Between
Occupational Safety and Health Administration
Atlanta-West Area Office
and
Georgia Tech Enterprise Innovation Institute –
Safety, Health and Environmental Services Group
and
Gilbane Building Company
PURPOSE/SCOPE
This Partnership was developed jointly by the Occupational Safety and Health Administration (OSHA), the Georgia Tech Enterprise Innovation Institute – Safety, Health and Environmental Services Group (Georgia Tech) and Gilbane Building Company (Gilbane), SERO Division. This Partnership will cover the construction of the Georgia Tech Campus Center Project (Project) located in Atlanta, Georgia. The common objectives and goals of the Partnership will include the following: reduce injuries and illnesses; increase safety and health training; reduce workers’ overexposure to health hazards; and assure employers have appropriate safety and health management systems. This Partnership is consistent with OSHA’s long-range efforts to develop a contractor/ government partnership approach to safety management. It allows for better use of OSHA resources and innovation in safety management. It also encourages more participation in the safety process from the construction community.
The Georgia Tech Campus Center Project is a proposed 216,484 square-foot student center located on Ferst Street on the Georgia Institute of Technology campus. The team’s concept conceives the Campus Center as an experiential path punctuated by a series of walks, plazas, richly articulated buildings, spatial experiences, and opportunities for social, creative, intellectual, and restorative engagement. This Project will include:
- Phase 1: Construction of a 2- story exhibition hall, a pavilion, and a café.
- Phase 2: Demolition of the Stamps addition to the Wenn Student Center, the construction of a new south addition, renovation of the existing Wenn Student Center.
- Phase 3: Construction of major hardscape and site improvements.
IDENTIFICATION OF PARTNERS
The Partnership will include:
- Occupational Safety and Health Administration
- Georgia Tech Enterprise Innovation Institute – Safety, Health and Environmental Services Group On-site Consultation
- Gilbane Building Company
GOALS/STRATEGIES/PERFORMANCE MEASURES
The primary objective of this Partnership is to create a working relationship that focuses on preventing work-related fatalities, controlling or eliminating serious workplace hazards, and establishing a foundation for the development of an effective safety and health program. The goals employed to achieve these results will include the following:
GOALS STRATEGIES MEASURES Reduce the total number of injuries and illness cases by 10 percent, thereby providing a safe and healthy work environment for employees at the Project. - Review the OSHA 300 log data of the Partnership participants. Review injury and illness trends and implement effective corrective action(s).
- Calculate the employer’s Total Case Incident Rate (TCIR) and Days away from work, restricted, or job transferred (DART)1 rates.
- Compare this data with the baseline rates for the Partnership.
- This goal will be measured by the number of companies participating in the Partnership, which reduce their TCIR and DART rates below the baseline for the partnership.
- Baseline will be established by the 2017 BLS Rates for Non-Residential Construction NAICS 2362, which are 2.7 and 1.4.
Effectively control workplace hazards by increasing the number of construction companies with safety and health management systems. - Review the number of employers that receive comprehensive consultation visits.
- Reviewing the number of employers that work with the Partnership to develop and implement comprehensive safety and health management systems.
Measure the number of project employers/subcontractors that develop and implement effective safety and health management systems, as a result of participating in the Partnership, compared to the (baseline) initial year of the Partnership. Increase the number of employees, employers and supervisors who are provided effective safety and health training, such as the OSHA 10-hour course. - Evaluate the employers that establish effective safety and health training programs.
- Evaluate the employers that provide employees with OSHA 10-hour/ OSHA 30-hour training.
- Measure the number of employers with effective safety and health training programs.
- Measure the number of managers, supervisors and employees provided with OSHA 10-hour/ OSHA 30-hour training compared to the (baseline) initial year of the Partnership.
Conduct effective self-inspections, sampling, monitoring, training and consultative activities in areas where employees might be exposed to health hazards such as the following: hazardous noise levels; lead; silica; asbestos; ergonomic stressors; and other health-related hazards.
The overall outcome of this goal should be the reduced overexposure of workers to health hazards, as well as a reduced injury and illness rate.
- Track health hazard-related program improvements, as well as training focused on the prevention of health hazards.
- The Gilbane Team will track the number of self-inspections and site audits, as well as the number of health hazards identified during these activities.
A comparison will be made between the number of health hazards identified during self-inspections and audits conducted during the (baseline) initial year of the Partnership. 1 Days Away from work, Restricted, or job Transferred (DART) rate: This includes cases involving days away from work, restricted work activity, and transfers to another job. It is calculated based on (N / EH) x (200,000) where N is the number of cases involving days away, and/or restricted work activity, and/or job transfer; EH is the total number of hours worked by all employees during the calendar year; and 200,000 is the base number of hours worked for 100 full-time equivalent employees. For example: Employees of an establishment including management, temporary, and leased workers worked 645,089 hours at this worksite. There were 22 injury and illness cases involving days away and/or restricted work activity and/or job transfer from the OSHA 300 Log (total of column H plus column I). The DART rate would be (22 / 645,089) x (200,000) = 6.8MANAGEMENT AND OPERATION
- The Gilbane Team will:
- Establish a jobsite safety walk team, consisting of a representative of all primary trades active on-site, to develop an understanding and awareness that all accidents are preventable. This action will be accomplished by implementing the Gilbane Team’s Safety Vision, a comprehensive safety and health management system, which includes:
- Management commitment and employee involvement;
- Hazard analysis;
- Hazard control; and
- Arrangement of training assistance for other stakeholders on-site.
- Mentor subcontractors in safety and health management systems. Subcontractors shall include all multi-tiered subcontractors that arrive for work on the site.
- Where the potential for airborne silica exposure exists, appropriate engineering controls and respirators will be used in accordance with 29 CFR Part 1926.1153. Table 1 of 29 CFR Part 1926.1153 will be used for reference. When airborne exposure results from an operation not covered by Table 1, project participants and contractors will adhere to the applicable parts of 29 CFR Part 1926.1153.
- Enforce safety rules and regulations. This enforcement authority will include provisions to hold contractors and employees accountable and, if necessary, remove contractors’ employees and supervisors from the job-site, following proper disciplinary procedures.
- Ensure that a competent person performs a risk assessment of all fall hazards. The probability and severity of occurrence for each identified hazard will be evaluated to eliminate or reduce the risk of falls hazards to as low a level as possible through conventional fall protection, engineering or administrative controls.
- Critical risks will not be tolerated. No work will be performed until action is taken to reduce the risk level of fall hazards to as low as reasonably feasible.
- Bricklayers performing overhand bricklaying and related work above lower levels must be adequately protected from falls. No monitor system will be allowed. Additionally, employers/subcontractors must install netting systems for stripping operations.
- Workers on the face of formwork or reinforcing steel must be protected from falling by personal fall arrest systems, with the use of a positioning device, and/or lanyards.
- Each contractor will be required to have at least two (2) competent persons on site at all times by filling out our Competent Person worksheet prior to mobilization.
- Identify and correct serious ergonomic hazards by ensuring that every contractor provides a daily stretch and flex program.
- Ensure that ground fault circuit interrupters (GFCI) are used to protect all electrical circuits that are installed for work. All contractors will ensure that employees are protected by the use of a GFCI at all times.
- All Gilbane staff members serve as points of contact, monitoring safety and health at the site and its progress toward achievement of the Partnership goals.
- Ensure that daily safety audits are conducted (since this is a multi-employer worksite and all workers are to work together on safety issues). Upon request, the Gilbane Team will review subcontractors’ daily log books and audits, note any hazards found, and then review them with all Safety Committee members at the weekly coordination/subcontractor meeting.
- Conduct and document weekly job-site safety meetings/toolbox talks.
- Report all safety incidents/concerns immediately
- Provide a high level “Safety Sheet” that documents monthly facts and information needed. This “Safety Sheet,” as well as any corrective actions taken for incidents, will be shared with OSHA and Georgia Tech during quarterly update meetings.
- Provide visual designation of who the Riggers/Signalmen are by using color-coded hardhats, vests, etc. While flying a load that has potential to go overhead of workers, whistles/horn will be blown to provide proper notice.
- Require the use of appropriate personal protective equipment. Gilbane will review the subcontractors’ safety requirements to ensure they are following their own procedures. We will also check to ensure they are following the Site-Specific Safety Procedures, as well as Gilbane’s “Above OSHA” policy. This includes 100 percent PPE at all times (hardhats, vests, eye protection, gloves).
- Ensure that all safety signs and warnings will be posted in English and Spanish.
- Implement a 100 percent Fall Protection Plan for all work performed 6 feet or more above lower surfaces.
- Establish a jobsite safety walk team, consisting of a representative of all primary trades active on-site, to develop an understanding and awareness that all accidents are preventable. This action will be accomplished by implementing the Gilbane Team’s Safety Vision, a comprehensive safety and health management system, which includes:
- Subcontractors will:
- Appoint a representative to the site Safety Committee responsible for resolving job safety matters and serve as a liaison to the Gilbane Team. Every prime trade contractor will have a person available to participate in the Safety Committee. Participation in this committee will consist of, but will not be limited to, participation in the Gilbane Team safety walkthroughs and monthly Safety Committee meetings.
- Conduct jobsite safety inspections for those employees under their control. These jobsite safety inspections will be in addition to the daily general inspections. If non-compliant activity or hazards are discovered, immediate correction is required. Documentation of abatement methods and verification must be submitted to the appropriate Gilbane Team Safety Director.
- Participate in the weekly Safety Committee/subcontractor meetings and safety audits. If non-compliant activity or hazards are discovered, immediate correction is required. Abatement methods and verification must be submitted to the appropriate Gilbane Team Safety Director who will document the correction taken and share this information during the monthly update meetings.
- Share the results of jobsite inspections with all workers by posting them in the Project's on-site management office or on the jobsite bulletin board, to ensure all workers are notified of the results.
- OSHA will:
- Participate, to the extent resources permit, in quarterly meeting with the Partnership's partners, but will not participate in the walk-around inspection, except that the verification visits may be scheduled as part of weekly walk-around inspection.
- Serve as a resource and liaison for Partnership participants and assist with safety and health training, as resources permit.
- Give priority to the construction project when technical assistance is needed.
- Audit the monthly reports/documents and make recommendations for improvements in meeting Partnership goals.
- Conduct inspections in accordance with sections VIII and IX of this Partnership.
- Conduct the annual Partnership evaluation report in accordance with section VII of this Partnership.
- Georgia Tech will:
- Perform quarterly jobsite inspections.
- Give priority consideration to requests for services to small contractors who are engaged in work at the Project.
- The Gilbane Team will:
SAFETY AND HEALTH MANAGEMENT SYSTEM
The Gilbane Team will use their systems to collect and analyze injury and illness trends (including near-miss incidents) by all contractors performing work at the site. This data will be used as a tool to ensure continual safety and health improvement at the site. The management of this Agreement will be accomplished by the Gilbane Team implementing a comprehensive jobsite safety and health management system which includes:
- Using the Gilbane Team - Job Hazard Analysis (JHA) and Safety Task Assessment (STA) forms, the Gilbane Team will complete a risk assessment prior to exposing any employee to potential safety and health hazards.
- Work with OSHA, Georgia Tech and Safety Committee members to provide the resources to conduct initial monitoring for ALL toxins, carcinogens, or hazardous substances currently emphasized by OSHA and which present inhalation hazards, such as silica, lead, cadmium, and/or isocyanates. Employee exposures will be assumed and respiratory protection worn until the results of the initial monitoring studies are received and demonstrate no exposure problems or prior surveys show no hazard exists. The Gilbane Team will endeavor to ensure that no work with these materials will occur, thus preventing any exposure. The Gilbane Team will request periodic evaluation visits by its insurance company's industrial hygienist and Georgia Tech
- All contractors on-site will perform daily audits. In addition, twice each month, a comprehensive audit of the jobsite will be performed. A representative of the subcontractors will be a safety audit participant in the jobsite areas where their employees may be exposed to hazards. Any hazards found during the audits will be corrected promptly. Items identified during the audits will be annotated on a daily log. When hazards cannot be corrected immediately they will be tracked until abatement is completed. Employees exposed to these hazardous conditions will be informed of the hazard and effective interim control measures will be implemented. A record will be kept of all hazards found during the comprehensive site safety audits and the number of hazards corrected as a result of the weekly audits
- Implement an effective Fall Protection Plan to include fall protection in all cases where work is being performed 6 feet or more above lower surfaces.
- Ensure employees receive training as follows:
- All Gilbane staff members are required to have OSHA 30-hour cards. Supervisory subcontractor personnel should also possess an OSHA 30-hour card.
- All employees will receive a site-specific construction safety orientation covering jobsite safety and health issues, procedures related to the work being performed, as well as the requirements outlined in the Partnership Agreement. In addition, employees shall receive training on the content of the risk assessment for operations they will encounter. This may require periodic retraining of employees on the content of the risk assessment as they become relevant due to entering new phases of construction. This material will be provided by the Gilbane Team to each subcontractor's designated safety representative for completion.
- A safety orientation will be provided to all workers in a language they understand. Subcontractors are required to provide a bilingual instructor who will participate in this training and translate when needed.
- Other hazard-specific training will be conducted on an as-needed basis.
- Each subcontractor with written safety and health management systems must submit them to the Project Construction Team for evaluation. Gilbane requires each subcontractor to provide a dedicated safety person if they exceed 20 employees on-site.
- Ensure the Gilbane Team and/or the affected subcontractors adequately address health-related issues, which arise during the course of the Project, with the assistance of OSHA, as its resources permit, and Georgia Tech. All health-related issues will be discussed monthly during Partnership meetings.
- Gilbane requires all subcontractors to provide an effective hearing protection program, including noise monitoring as necessary.
- An effective environmental monitoring program will be implemented to control airborne hazards, such as silica, and will include personal monitoring, employee training, implementation of engineering controls where possible, and the use of respiratory protection when necessary. Previous site-based data will be considered acceptable.
- Ensure compliance with the NFPA 70E when working on live electrical equipment, including training and the availability and use of personal protective equipment. A permit system will be implemented whenever working in close proximity to or on live electrical systems to ensure the implementation of appropriate protective measures prior to exposure. The permit form includes requirements for pre-task review and lockout/tagout procedures to be followed.
- Ensure all equipment capable of causing amputations is adequately guarded.
- Ensure effective programs are employed, consisting of policies and procedures that comply with OSHA's Process Safety Management (PSM) standards as equipment and processes are brought live and on-line at the Project.
- Ensure effective programs are employed, consisting of policies and procedures that comply with OSHA's Lockout/Tagout standards, as equipment and processes are brought live and on-line at the Project.
WORKER INVOLVEMENT
The site will establish an employee Safety Committee consisting of one member per subcontractor that will participate on periodic weekly and monthly meetings to share the results of jobsite inspections, information concerning accidents and near misses, and suggestions for improvement, as well as recommendations for training the general workforce. Additionally, near misses and daily safety audits will be discussed during Tool Box Talks.
ANNUAL EVALUATION
The Partnership will be evaluated on an annual basis through the use of the Strategic Partnership Annual Evaluation Format as specified in Appendix C of OSHA Instruction CSP 03-02-003, OSHA Strategic Partnership Program for Worker Safety and Health.
The Gilbane Team will be responsible for gathering required participant (employer/subcontractor) data to evaluate and track the overall results and success of the Partnership. This data will be shared with OSHA. OSHA will be responsible for writing and submitting the annual evaluation.
INCENTIVES
Participant benefits from OSHA may include:
- Maximum penalty reductions for good faith and history, to the extent allowed by the OSHA Field Operations Manual (FOM), OSHA Instruction CPL 02-00-160 (August 2, 2016).
- In the event that a citation with penalties is issued, the Area Director has the authority to negotiate the amount of an additional penalty reduction as part of the informal conference settlement agreement.
- Priority consultation service and assistance for small employers working on the construction site from the Georgia Tech Consultation program.
- An OSHA focused inspection is available where the Partnership participant has an effective safety and health management system fully-compliant with 29 CFR Part 1926.20 and 29 CFR Part 1926.21. (For additional details, refer to the 1994 memo signed by then Deputy Assistant Secretary for OSHA James Stanley.)
OSHA VERIFICATION
- Verification Enforcement Inspections: OSHA will conduct the initial verification enforcement inspection no sooner than three months, but within four months after Partnership participants formally enter into this Agreement. During this period participants should develop and implement the safety and health management systems required under this Agreement. After this period, OSHA will conduct the verification enforcement inspections annually thereafter. Verification enforcement inspections will be conducted as a focused inspection, per the appropriate OSHA guidelines. Compliance Safety and Health Officers (CSHOs) who are familiar with the Project will do verification enforcement inspections. Employee rights under the Occupational Safety and Health Act (OSH Act) will be afforded. During the verification enforcement inspections, if OSHA personnel identify serious hazards that site management refuses to correct, the scope of the inspection may be expanded.
- Complaint/Referral Investigations: This Partnership provides for the immediate response to each allegation of a safety or health hazard brought to its attention by any person. Upon a finding that an allegation is valid, the employer shall promptly abate the hazard.
- OSHA agrees that a copy of each non-formal complaint/referral related to the work site and filed with OSHA will be forwarded by fax, or by CSHO, to the Gilbane Team's - Project Management office on-site. In accordance with applicable law, the name of the complainant requesting confidentiality will not be revealed. The Gilbane Team agrees to investigate these complaints, regardless of the employer involved, and provide OSHA with a written response within 5 working days of receiving the non-formal complaint/referral.
- Accident Investigations: Employers engaged in this Partnership recognize that OSHA fully investigates accidents involving a fatality or serious physical harm. If during the course of the investigation OSHA determines that the incident resulted from violations of the OSHA standards, the employer will not be afforded Partnership incentives.
WORKER AND EMPLOYER RIGHTS
This Partnership does not preclude employees and/or employers from exercising any right provided under the OSH Act, nor abrogates any responsibility to comply with rules and regulations adopted pursuant to the OSH Act.
TERM OF PARTNERSHIP
It is understood that this Agreement shall be in effect until completion of construction activities at the Project, but in no case longer than three years. Should any "signatory" stakeholder choose to withdraw prior to Project's completion, a written notice shall be given stating the reason(s) and providing 30 days' notice to the other party(s).
If OSHA chooses to withdraw its participation in the Partnership, the entire Partnership is terminated. Any party may also propose modification or amendment of the Agreement. Changes may be implemented, if all parties agree that they are in the best interest of the Partnership.
THE GEORGIA TECH CAMPUS CENTER PROJECT SIGNATURE PAGE
Partnership Signing Date:
- Keith Hass
- Area Director
- Occupational Safety & Health Administration (OSHA)
- Brian Steed
- Vice President
- Gilbane Building Company
- Drew Gaskins
- Safety Director
- Gilbane Building Company
- Christopher Torchia
- Senior Project Executive
- Gilbane Building Company
- Sean Rice, Sr.
- General Superintendent
- Gilbane Building Company
- Christian Lee
- Project Manager
- Gilbane Building Company