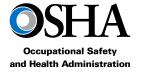
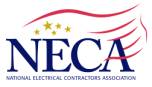

AGREEMENT ESTABLISHING A PARTNERSHIP
BETWEEN
THE OCCUPATIONAL SAFETY AND HEALTH ADMINISTRATION
U.S. DEPARTMENT OF LABOR - OSHA REGION V
COLUMBUS AREA OFFICE
AND
THE NATIONAL ELECTRICAL CONTRACTORS ASSOCIATION (NECA)
CENTRAL OHIO CHAPTER
AND
THE INTERNATIONAL BROTHERHOOD OF ELECTRICAL WORKERS (IBEW)
LOCAL UNIONS 683 & 1105
- Identification of Partners
In an effort to more fully realize the objectives of the Occupational Safety and Health Act of 1970 to provide a safe and healthful work environment for all workers, including those engaged in the electrical construction and maintenance industry, the Central Ohio Chapter of the National Electrical Contractors Association Inc. (NECA) and the International Brotherhood of Electrical Workers Local Unions 683 and 1105 (IBEW), enter into an industry partnership with the United States Department of Labor, Occupational Safety and Health Administration, Region V, Columbus Area Office (OSHA) which has led to this Agreement.
For over 110 years, the NECA/IBEW Labor-Management Partnership has provided its respective members and the entire construction industry with model partnerships designed to meet industry specific issues. These model partnerships are exemplified by our multiple Taft-Hartley Trust Funds and Industry funds. Of these, two NECA/IBEW partnerships deserve special comment.
The first is the National Joint Apprenticeship and Training Committee (NJATC) Through this industry partnership we have seen the development of a network in excess of 280 Local NECA/IBEW JATCs where individuals are given the opportunity to become excellent IBEW Journeyman wireman and IBEW Journeyman Installer Technicians. Many, as exemplified by the apprentices in the Columbus and Newark JATCs are completing the program with an Associate Degree.
The second noteworthy partnership is the Council on Industrial Relations (CIR). The CIR is a panel of electrical industry leaders that is authorized to hear and decide/resolve local issues when formally presented to it. As a result, the CIR provides a means for local Labor and Management representatives to settle disputes without strikes or lockouts. Having this industry partnership to assist local parties in resolving their disputes without the emotional strife is a great service. It is because of this NECA/IBEW Partnership our business model proudly bears the moniker of a "strike-lockout proof industry".
The COHNECA/IBEW 683 & 1105 Partnership is pleased to extend the hand of cooperation and consideration to the Columbus OSHA Area Office to form the COHNECA/IBEW 683 & 1105/ Columbus OSHA Area Office Partnership, not only for the construction industry, but for general industry as well.
- Our organizations enjoyed a high level of cooperation with the development of a national electrical worker safety curriculum being just one of many examples. The NECA IBEW OSHA Partnership builds on this important foundation, and denotes a new era of Labor-Management-Agency cooperation and insight. In the end, meaningful increases in workplace health and safety will benefit the Central Ohio electrical workers and their Employers.
Employers who perform electrical construction and maintenance contracting services within the jurisdictional boundaries of (and are signatory to) the International Brotherhood of Electrical Workers (Local Unions 683 and 1105), and are members in good standing of the Central Ohio Chapter of the National Electrical Contractors Association, Inc. shall be eligible to apply to this Partnership.
Figure 1 Ohio IBEW Jurisdictional Map LU 683 = 13, LU 1105 = 12
- Purpose/Scope
Working as partners and associates, the above parties are committed to achieve measurable, meaningful improvements in electrical worker safety using the following blueprint:
- Encourage the continuous improvement of the safety culture within the electrical trade.
- Actively research, share and implement the top safety and health programs for electrical workers. This includes technology, innovations and best practices that provide measurable improvement in electrical worker safety. These will be shared with the NECA/IBEW Partnership members at the quarterly meetings.
- Continuously develop, build and share improved, effective safety programs specifically for electrical workers.
- Develop and build, with help from the National Joint Apprenticeship and Training Committee (NJATC), improved, effective and meaningful safety training programs specific enough for the electrical trade, yet broad enough to be effective in every facet of diverse industry.
- Constantly recognize and promote electrical worker safety excellence.
- Ensure, through consequential and honest communication, that enforcement policies and practices are consistent, fair and effective
- Goals, Strategies and Measures
GOALS
- Maintain the participating employers’ injury illness rates below the Bureau Labor Statistics (BLS) data for NAICS 23821, Electrical contractors.
- Increase the number of and use of safety and health programs and best practices among participants.
- All parties will work to promote and encourage new participating firms
STRATEGIES
Strategies to achieve one or all of the above goals:
- Increase the implementation of effective safety and health program through training, self-inspections, and use of NFPA 70e Electrical Safe Work practices.
- Provide quarterly meeting for Partnership participants and stakeholders.
- Use Region V fatality data to focus training efforts of participants in order to encourage the use of on-the- job tool box talks.
- Partnership will be promoted at industry events and functions.
MEASURES
- Comparison of DART injury/illness rate of participating employers’ to the most recently published BLS data.
- Document the quarterly meetings and number of participants in attendance.
- Document the number of employees trained by the electrical training centers in OSHA 10-hour, OSHA 30-hour, and NFPA 70e Electrical Safe Work practices.
- Document the number of meeting to provide safety and health assistance for participating employers.
- Track the number of new employers who apply and become members to this Partnership.
These outcomes will be obtained using the following methods:
- Adopt and require use of an industry standard checklist designed to exceed OSHA requirements when working energized circuits. This policy will be based on the 2012 National Fire Protection Association; (NFPA;;) 70e Standard for Electrical Safety in the Workplace, which can be found in Appendix A of this partnership. Also refer to Annex E of NFPA 70e which provides a typical description of an Electrical Safety Program.
- Mandatory OSHA 10-Hour courses for all field employees and mandatory OSHA 30- Hour courses for all field supervisors. All employees will be subject to regular refresher course through tool box talks or formal classes.
- Site specific safety training for new hires.
- Regular safety program third-party audits.
- Quarterly meetings discussing industry best practices.
All parties will be consulted on a continuing basis for feedback to assess the progression and potential amelioration of these goals.
- Performance Measures
All information will remain confidential as to company name and employee. The only purpose of this data is to assess performance and to target specific training requirements.
- The measurement system will use OSHA recordable fatalities and accidents identified.
- Activity measures shall include:
- The applicable number of employers, supervisors and employees trained.
- Number of job safety analyses conducted.
- Number of worksite audits.
- Increased employee involvement.
- Enhanced communication between management and employees.
- Outcome measures will be gathered on an annual basis and will be comprised of data analyzing the number of hours worked, number of injuries, illnesses, and fatalities during the baseline year.
- All participating firms will keep their OSHA 300 log current and up to date. A copy of the OSHA 300 log will be submitted to the NECA office with the annual recertification and shared with OSHA by June 15th of each year.
- Annual Evaluation
The annual evaluation shall use the Strategic Partnership Annual Evaluation Format measurement system as specified in Appendix C of CSP 03-02-002, OSHA Strategic Partnership Program for Worker Safety and Health Directive.
All data for the annual evaluation shall be submitted to the NECA/IBEW Partnership no later than August 15th of each year. New applications and re-certifications shall be submitted by June 15th to be considered for the upcoming year. Applications turned in past the June 15th deadline will not be considered for the NECA/IBEW/OSHA Partnership.
It will be the responsibility of the NECA/IBEW Partnership to gather participant data to evaluate and track the overall results and success of the NECA/IBEW.OSHA Partnership. Data collected will be given to OSHA as well.
The OSHA liaison will use the collected data to write and submit the annual evaluation to the Columbus OSHA Area Director. The final draft will be made available to the NECA/IBEW Partnership. The annual evaluation will be sent to the National OSHA Office by December 15 for each calendar year of the NECA/IBEW/OSHA Partnership and Agreement.
- NECA/IBEW Partnership Management and Operation
Representative(s) from the NECA/IBEW Partnership will administer this program as outlined herein, and will serve as the primary safety resource, supporting the participating employers and employees. To fulfill this Partnership the NECA/IBEW Partnership will also provide the following services:
- Act as a liaison for NECA/IBEW members with OSHA. Members will be able to call the NECA/IBEW Partnership with questions and the NECA/IBEW Partnership will contact OSHA for responses, if required. The OSHA primary contact will be appointed by the OSHA Area Director and the NECA/IBEW Partnership will be notified in writing.
-
In concert with The Electrical Trades Center and the Newark JATC Training Center, offer ongoing, quality training on topics of importance for members - specifically the focused areas of fall protection, electrical hazards, trenching, confined spaces etc.
Although providing mandatory fall protection at the 6’ level is not required by the current OSHA construction standards and is not mandated by OSHA as a requirement for participation in any OSHA partnership agreement, the contractors on this partnership are committed to providing a greater level of protection to the employees working at this site and will require protection at the 6’ level and above.
- Provide up-to-date informational materials and brochures to NECA/IBEW Partnership members (from OSHA, OSHA Ohio On-Site Consultation Service, the Bureau of Workers’ Compensation (BWC) and other appropriate organizations).
- Organize and provide to participating employers OSHA’s interpretations of major standards, as well as local inspection perspectives.
- Develop written safety and health policies and programs for participating employers, including emphasis on employer/employee responsibilities.
- Promote construction safety excellence through an annual NECA Safety Recognition Program.
- Administer the NECA/IBEW/OSHA Partnership, including, but not limited to, the initial evaluation of potential participating employer applications to determine whether the firm meets the criteria specified within the Partnership. Information considered by the NECA/IBEW Partnership will include pertinent company information as referenced in Section VII (demonstrated safety and health program, training commitments, OSHA citation history, fatalities, injury/illness experience and similar factors). Any and all information garnered by the NECA/IBEW Partnership will be held with the greatest confidentiality.
- Notify OSHA on a regular and recurring basis with the name(s) of Employers which have met the partnership criteria.
- Conduct periodic audits to determine the impact and effectiveness of the NECA/IBEW/OSHA Partnership.
- A representative(s) from the NECA/IBEW Partnership and a representative(s) from OSHA together will conduct random onsite verification of 10 percent or more of participating employers to ensure that participating employers are fulfilling their commitment to the Partnership. During these onsite evaluations, if an OSHA representative observes serious hazards, these hazards will be addressed in a comprehensive and systematic manner, which may include citations.
- If necessary, terminate employers from the NECA/IBEW/OSHA Partnership if findings indicate unacceptable performance or submission of falsified documentation. (Note: At the discretion of the NECA/IBEW partnership and OSHA, a participating employer may be permitted to correct deficiencies within 30 days of notification and apply to the NECA/IBEW partnership for continued recognition as a partner in good standing before termination would take effect.)
OSHA and the NECA/IBEW Partnership have the discretion to jointly veto Employers from participating for just cause. The OSHA Area Director has the discretion to unilaterally veto Employers from participating in this Partnership for just cause upon providing notification and explanation to the NECA/IBEW Partnership.
- OSHA Benefits: Upon participating Employers' acceptance into this program, OSHA will:
- Conduct quarterly meetings with the NECA/IBEW partnership and participating Employers to provide information on “what’s hot” and to answer general and specific questions.
- OSHA personnel may be available for a variety of onsite/offsite activities such as review of safety and health management systems, and guidance in conducting workplace audits and evaluations.
- OSHA seminars, workshops, and other speaking events.
- Informational material such as safety and health brochures, pamphlets and electronic tools.
- Through the Columbus OSHA Area Director or designated representative meet with participating employers to address their role in the partnership.
- Review the participating Employers’ records and provide limited onsite training as needed during inspections where minor problems (ex: missing mid-rail) are found.
- Participating Employer Verification
To become and take full advantage of participating employer status, the Employer must:
- Submit application and be willing to submit documents to the NECA/IBEW Partnership for review by OSHA (such as the OSHA Log 300 and the company’s safety program).
- Not have had willful or repeat violations in the last three years in Ohio, and nationwide, must not have had serious violations that resulted in a fatally(s) or catastrophe(s).
- Have a written safety and health program that complies with ANSI A-10.38 recommendations or OSHA’s 1989 Voluntary Guidelines. The program must include active employee involvement.
- Ensure that all new field Employees receive site-specific training before beginning work, and receive at least a two-hour safety orientation within the first week of hire. Topics for the orientation must include fall protection, electrical, struck-by, trenching/caught-between and personal protective equipment.
- Ensure that within a year all field employees attend an OSHA 10-Hour training course. Field employees must receive refresher training in the 10-Hour Course every three years.
- Ensure that within a year all field supervisors attend an OSHA 30-Hour training course. Field supervisors must receive refresher training in the 30-Hour course every three years.
- Note: A supervisor is defined as someone who directs/controls work.
- Have a Days Away Restricted and Transfer (DART) rate for work in Ohio at least 25 percent below the BLS national average for the company’s North American Industry Classification Code (NAICS).
- The company will submit individual DART rates for the past three years, and will be evaluated on a three-year average.
- If a company fulfills all other requirements, but does not have a qualifying DART, it may appeal for inclusion in the Partnership. OSHA and the NECA/IBEW Partnership will review these appeals on a case by case basis, and may allow the company to participate if the improvement can be shown.
- Show evidence that both employees and supervisors are held accountable for safety.
- Allow OSHA access to sites for inspection if the Employer has the authority to allow an inspection of the site. OSHA will follow the guidelines for inspections as outlined in the Field Operations Manual (FOM).
- Recognize that OSHA implements Local Emphasis Programs (LEP) and National Emphasis Programs (NEP) to better manage specified hazards. These specific programs will involve inspections. The NECA/IBEW
- Partnership will be informed by OSHA of all LEPs and NEPs, and through the Partnership, this information will be shared with all participating Employers.
- Participate in a site audit by an outside, independent source approved by the NECA/IBEW Partnership. The audit must include an action plan to prevent future hazards, as well as methods to abate current hazards. These audits will be made available to OSHA upon request.
- Agree that all work on energized circuits will be performed under a standard policy as referenced in Appendix A to be developed and built in accordance with the current National Fire Protection Association publication 70e. This policy will cover hazard/risk evaluation, and procedures including protective barriers and shields, communication, insulated tools and equipment, and personal protective equipment.
- Be a member in good standing of the National Electrical Contractors Association.
- Employer/Employee Rights
This Partnership Agreement does not preclude employees and/or employers from exercising any right provided under the OSH Act (or federal employees, 29 CFR 1960), nor does it abrogate any responsibility to comply with rules and regulations adopted pursuant to the Act.
Routine Employee involvement in the day to day implementation of worksite safety and health programs is expected to be assured, including Employee participation in Employer self-audits, site inspections, job hazard analysis, safety and health program reviews and near miss investigations.
- Termination of this Partnership
Any party may withdraw from this Partnership Agreement by providing written notification to the other parties. Termination will be effective 30 days after receipt of said notification. Furthermore, an individual participating Employer may withdraw from this Agreement by providing written notification to the NECA/IBEW partnership and OSHA. Termination shall be effective 30 days after receipt of notification.
If OSHA chooses to withdraw its participation in the partnership, the entire Agreement is terminated. Either party may also propose modification or amendment of the Agreement.
An individual participating Employer's violation of this Partnership Agreement shall not be grounds for OSHA to terminate this Partnership or the Partnership Agreement.
The NECA/IBEW partnership and OSHA may terminate an individual Employer from the partnership if the Employer fails to meet the qualifications or otherwise violates the terms and conditions of this Partnership.
Any party may propose modification or amendment to this Partnership subject to concurrence by the every other party to the Partnership.
Unless modified or superseded, this Partnership Agreement will terminate three years after the signing date. Agreed this 3rd day of December, 2012.
Deborah Zubaty
Area Director
U.S. Department of Labor OSHA
Columbus Area Office
Mario Ciardelli
Business Manager, Financial Secretary
Local Union 683, IBEW
Columbus, Ohio
Brian Damant
Chapter Manager
Central Ohio Chapter, NECA, Inc.
Columbus, Ohio
William Hamilton
Business Manager, Financial Secretary
Local Union 1105, IBEW
Newark, Ohio
Appendix A - Energized Checklist
TO BE REVIEWED BY FORMAN PRIOR TO START OF WORK
VALID FOR NAMED WIREMAN AND DAY ISSUED ONLY
Date:_________________________ START TIME:_________________________ A.M. P.M.
PROJECT ________________________________________________________________________________________________________________
BUILDING LOCATION _______________________________________________________________________________________________________
PANEL LOCATION __________________________________________________________________________________________________________
DESCRIPTION OF WORK TO BE PERFORMED _____________________________________________________________________________________
SPECIFIC REASON EQUIPMENT CIRCUIT CANNOT BE DE-ENERGIZED: _________________________________________________________________
_________________________________________________________________________________________________________________________
_________________________________________________________________________________________________________________________
MAXIMUM VOLTAGE PRESENT ________________________________________________________________________________________________
MAXIMUM VOLTAGE PRESENT ________________________________________________________________________________________________
PERSONAL PROTECTIVE EQUIPMENT (PPE) WORN/USED:
HARD HAT | ______ | *INSULATED GLOVES | ______ |
FACE SHIELD | ______ | *INSULATED SLEEVES | ______ |
FLASH RESISTANT JACKET | ______ | *INSULATED BLANKET | ______ |
INSULATED MATS | ______ |
ADDITIONAL PPE REQUIRED ________________________________________________________________________________________________
WIREMAN SIGNATURE _____________________________________________________________________________________________________
WORK AUTHORIZED BY _______________________________________ TITLE ___________________________________
REQUIRED SECOND WIREMAN ASSISTING SIGNATURE ___________________________________________________________________________
**On all energized circuits or equipment carrying four hundred forty (440) volts or over, as a safety measure, two (2) or more journeyman must work together.**
OWNER/CUSTOMER REPRESENTATIVE________________________________________________________________________________________
TIME WORK COMPLETED _______________________________________________ A.M. P.M.
*REVIEW BACK SIDE OF CHECKLIST FOR INFORMATION ON RUBBER GOODS
Rubber goods are classed, color coded, rated and tested at voltages as follows:
CLASS |
COLOR |
MAXIMUM USE VOLTAGE PHASE-TO-PHASE AC |
MAXIMUM USE VOLTAGE PHASE-TO-PHASE DC |
---|---|---|---|
00 |
BEIGE |
500 V |
700 V |
0 |
RED |
1000 V |
1,500 V |
1 |
WHITE |
7,500 V |
11,250 V |
2 |
YELLOW |
17,000 V |
25,500 V |
3 |
GREEN |
26,500 V |
39,750 V |
4 |
ORANGE |
36,000 V |
54,000 V |
Rubber goods are required to be labeled as follows:
- Manufacturer's name.
- Type I for non-ozone-resistant equipment or Type II for ozone-resistant equipment.
- Size (Gloves only).
- Voltage class (0, 1, 2, 3, and 4).
- Color coding according to voltage class.
Each Foreman should ensure that rubber protective equipment under his or her control and care is maintained, inspected, used and tested as per the equipment manufacturer's instructions and as per the appropriate American Society for Testing and Materials (ASTM) standards that are available for review in the Safety Coordinator's office:
11.2 RUBBER GOODS TESTING GUIDELINES
The Site Superintendent should ensure that Foreman and employees inspect all rubber protection products before each use in accordance with the manufacturer's inspection guidelines and the ASTM standard:
- ASTM F 1236 Standard Guide for Visual Inspection of Electrical Protective Rubber Products.
The Safety Coordinator should maintain a master list of all Company rubber protection equipment and set up a testing schedule so that there will be an adequate amount and types of rubber protection equipment and devices on site while tested rubber goods are off site undergoing manufacturer's retesting.
- Manufacturer's Periodic Electrical Testing Instructions
PRODUCT
MAXIMUM TEST INTERVAL, MONTHS
ASTM
NOTES
GLOVES
6
F496
Tested. Unused gloves may be place into service within 12 months of the previous tests without retesting. SLEEVES
12
F496
Tested. Unused gloves may be place into service within 12 months of the previous tests without retesting. BLANKET
12
F479
Tested. Unused gloves may be place into service within 12 months of the previous tests without retesting. MATS
-
D178
Only needs to be tested b Manufacturer, when new. COVERS
-
F478
Retested when in-service in section indicates a need. LINE HOSES
-
F478
Retested when in-service in section indicates a need. - Typical Rubber Goods Defects That Employees Should Look For: The following are typical types of rubber goods damage or imperfections that employees should look for while inspecting each item prior to being used: