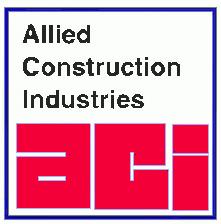
Partnership Agreement between the
Cincinnati and Columbus Area Offices of the
Occupational Safety and Health Administration
and
Allied Construction Industries
-
IDENTIFY PARTNERS AND PARTICIPANTS
The above named groups developed this partnering agreement jointly. The common objective and goal of the agreement is to provide a safe and healthful work environment for employees engaged in construction activities within the twenty counties in the Cincinnati Area Office and the twenty-eight counties in the Columbus Area Office jurisdictions, and to help prevent serious accidents within the industry through increased safety and health training, increased worker involvement and the implementation of enhanced safety and health management system.
By focusing its efforts and utilizing the skills and resources of the Allied Construction Industries (ACI) trade association, their member employers, and with assistance of the Cincinnati and Columbus Area Offices of OSHA, it is believed that this cooperative and voluntary program fosters worker knowledge, increases worker empowerment, and reduces the hazards and serious injuries at jobsites. Past participants continue to achieve injury and illness rates below the national average for the construction industry and it is expected that even lower rates will be achieved through this Partnership because of increased worker involvement.
This initiative represents a voluntary agreement and affords a Partnership alternative to the traditional OSHA enforcement procedures. This Partnership program is consistent with OSHA's long-range efforts to develop a business/labor/government Partnership approach to safety management, allows for better use of OSHA resources, and encourages more participation in the safety process by each stakeholder and their employees. Representatives of the building trade organizations directly involved or affected by this Partnership ("Participant" or "Participating member") have been consulted and encouraged to provide improvements and enhancements to this Partnership. The listing of current Participants is located in Appendix A.
-
PURPOSE AND SCOPE:
ACI is a trade association focused on commercial construction with over 500 member companies employing more than 27,000 employees representing many aspects of the construction industry. Members industries include site construction, concrete, masonry, sheet metal work, carpentry, thermal and moisture protection, doors and windows installation, finishing contractors, specialty contractors, equipment sales and service, furnishings, special construction, conveying systems installation, mechanical, electrical and service companies.
ACI's mission is to provide leadership and opportunities for its members in the Greater Cincinnati construction community, with a focus to provide the means and measures to help its members develop and grow. ACI's principal goal (and a long-standing commitment of the association) is to promote safety awareness, and serve as a safety resource for its members. This safety commitment includes information, education, referrals and training.
ACI and OSHA believe that maintaining a focus on safety saves lives, increases quality of life and maintains jobs. A focus on safety is an objective that OSHA and all ACI members have in common.
In 1998, the ACI Board of Directors realized the importance of safety for their members and agreed to increase the organization's commitment and resources to the safety efforts. A full-time Safety Director was hired and given the long-term goal of developing a safety training institute geared to quality education and training of ACI members and their employees.
OSHA, along with ACI, has a vested interest in the protection of employees and in working with other associations and groups to assist in promoting safety. With limited resources not allowing for inspections at every jobsite and project, this long-standing joint effort by ACI and OSHA has provided an opportunity for them to reach larger populations, thereby keeping safety in the forefront. Continuing this Partnership will increase OSHA's visibility within ACI's membership, and help maintain the spirit of cooperation between the two organizations.
Since the inception of this Partnership in 2000, the Participants have implemented many positive changes in the way they address safety in the construction industry. The Participants' willingness to share new "best practices" with other employers and employees, whether or not they are Participants, has resulted in a consistent safety culture becoming more and more evident on construction projects.
-
SAFETY AND HEALTH MANAGEMENT SYSTEMS
The Safety and Health Management System (SHMS) is a critical part of this OSHA Partnership Agreement in that it is an important aspect of collaboration between the project management team, supervisors, and the workers on site. This Safety and Health Management System will include but not be limited to the following core elements:
-
Management Leadership and Worker Involvement
ACI will ensure each Participating member will implement a Safety and Health Management System patterned after OSHA Safety and Health Program Management Guidelines, within 30 days of the execution of this Partnership Agreement. Such systems will encourage Participating members to commit a high level of worker involvement to assist in monitoring and identifying job site hazards on a continual basis to prevent accidents.
-
Worker Involvement
ACI will ensure each Participant encourages workers to report job site hazards and bring all potential hazards to the attention of the Participant if discovered for immediate response and correction. This will be encouraged in the following ways:
- Each Participating member will hold a Job Site Orientation with each worker prior to work on site. Orientation will include an overview of the employer's participation in the ACI/OSHA Partnership.
- Each Participating member will ensure workers and/or their representatives are involved with daily walkthroughs and weekly documented site inspections.
- Each Participating member will provide a simple system to allow workers to report potential job site hazards to ACI and/or supervisors upon discovery to stop work if necessary.
- Each Participating member will require all workers to attend weekly tool box talks. Participants will also provide the opportunity for workers to lead tool box talks and present safety trainings to fellow workers.
-
Worksite Analysis
ACI will ensure each Participating member will focus on safety at all times and will enforce job site safety compliance to OSHA standards including but not limited to the following ways:
- Each Participating member will conduct daily site inspections and review all subcontractors, workers and site conditions for safe practices.
- Each Participating member will take immediate action to correct any unsafe conditions.
- Each Participating member will monitor all workers, visitors and others entering the work site to ensure safe conditions throughout the worksite.
-
Hazard Prevention and Control
ACI/the Partnership considers Hazard Prevention and Control a process requiring continual efforts of monitoring and identifying job site hazards and taking corrective actions to maintain a safe and healthy job site at all times.
- Each Participating member will ensure that hazard correction procedures are in place.
- Each Participating member will ensure that everyone knows how to use and maintain personal protective equipment.
- Each Participating member will make sure that everyone understands and follows safe work procedures.
-
Safety and Health Training
- Each Participating member will ensure only properly authorized and instructed employees should be allowed to do any job.
- Each Participating member will ensure workers do not do a job that appears to be unsafe.
- Each Participating member will ensure that supervisors are trained to recognize hazards and understand their responsibilities.
-
-
WORKER INVOLVEMENT
The Participants agreed that a positive change is the involvement of workers in pre-planning their tasks around safety at the beginning of the work shift and ensuring there is an outlet for everyone to communicate other hazards that may not have been previously identified. In an effort to further expand this success, the Participants agree these best practices should become the primary focus for renewal of this Partnership Agreement. Workers will be encouraged to report job site hazards and bring all potential hazards to the attention of the participating member(s) and/or supervisors if discovered for immediate response and correction. ACI will ensure worker involvement in the following ways:
- Each Participating member will develop a Safety Committee which will be comprised of a cross-section of company representation including safety personnel, management, middle-management, and trade workers who are employee-elected. Committees will meet on a quarterly basis. At least one representative from the committee, in addition to the main contact, will also attend Partnership and OSHA update meetings.
- Each Participating member will ensure workers and/or their representatives participate in monthly safety meetings as well as report any near miss or unsafe conditions. Each Participating member will collect and report examples of worker safety contributions on a quarterly basis. Examples will include instances where workers have identified and prevented accidents and injuries through pre-planning or identification of hazards. This narrative will be included in quarterly reports submitted to ACI and OSHA.
- Each Participating member will participate in monthly safety audits and provide all subcontractors on site with a copy of the safety audit reports for use in discussion with workers during tool box talks.
- Each Participating member will provide support to all workers and/or their representatives by providing feedback on risks and assisting them in eliminating hazards.
- Each Participating member will increase worker involvement in the recognition of hazards associated with work they perform each day through the use of the "Worker's Identification of Safety Hazards" (WISH) form found in Appendix B.
- Each Participating member will increase worker involvement in communicating recognized hazards through the use of the "Hazard Reporting Procedures" in Appendix B.
-
WORK PRODUCTS
To emphasize the impacts and success of the Partnership, tangible work products will be produced throughout the term of this agreement. Work products will not only provide benefit to the Participating members, but will also prove beneficial to the safety programs of all ACI members and their subcontractors. Example work products may include, but not be limited to:
- Annual ACI/OSHA Safety Day: Each year, in conjunction with OSHA, ACI hosts an annual Safety Day. Safety Day is a full day dedicated to quality industry training, news, and exposure to the latest safety products and technologies. This event is designed not only for safety professionals, but also to emphasize the importance and magnitude of safety to workers. Annually, Safety Day draws average attendances of 350 people. ACI and OSHA will continue to conduct Safety Day on an annual basis.
- Temporary Worker Orientation: As OSHA continues to highlight the importance of temporary worker safety, ACI will ensure the Participating members will work to develop a Temporary Worker Orientation. This orientation will be mandatory for all temporary workers who conduct work for any of the Participating members. Additionally, this orientation may also be shared with other members and community partners of ACI who utilize or place temporary workers. Such a work product is an example of how the Partnership will benefit not only ACI, Participating members and OSHA, but the community and worker safety in its entirety.
- Annual Stand Downs: In the past, Participating members have participated in stand downs, particularly national stand downs announced by OSHA. Participants will continue to conduct and/or host annual stand downs through the term of this agreement. Topics of stand downs may include those emphasized by OSHA, but may also be selected based upon trends that become evident through the Participant's reporting data.
- Data Analysis & Initiative Development: ACI will ensure participants will analyze reporting data and leading indicators for safety trends annually that may warrant additional efforts and focus. If such trends appear, the Participants will develop an appropriate initiative to educate and involve workers in addressing these areas of concern.
- Partnership Mentoring: ACI will assist the Participating members to develop a Peer-to-Peer Mentoring Program for new Participants entering the Partnership, as well as current Participants in need of additional guidance and resources, particularly as indicated by data trends. Mentors may be current Participating members, but may also be companies designated with VPP status. Mentors will be chosen and paired based on factors such as type of work performed and specific areas of need.
-
GOALS / STRATEGIES & PERFORMANCE MEASURES
ACI participants in the Partnership will strive to meet the Goals below by using the associated Strategies. An ACI Safety Representative will collect data quarterly from each Participating member for submission to OSHA.
Should data trends submitted by a Participating member on a quarterly basis indicate increased accidents and injuries or decreasing performance, the Participant may be required to submit monthly reporting for more detailed analysis and evaluation. This information will be utilized to develop Participant-specific solutions to improve performance metrics; failure of commitment or measured improvement may result in exclusion from the Partnership.
GOALS STRATEGIES MEASURES 1. Participants reduce the number of injuries and illnesses to reduce by 10% the Partnership-wide Baseline determined at the renewal date of the Partnership program based on Participants that enroll. 1. a. At the start of every work shift, each Participating work crew will identify and discuss the common hazards associated with the work they will perform that shift.
b. Participants will train workers in use of Worker's Identification of Safety Hazards (WISH) form in Appendix B.
c. Each work crew will document their findings and what methods will be used to eliminate or minimize the identified hazards on the (WISH) form.
d. Participants will provide the necessary engineering controls, administrative controls and personal protective equipment.1. a. ACI will collect and calculate the following injury and illness data on a quarterly basis from each Participant: - Total Recordable Incident Rate (TRIR)
- Days Away/ Restricted or Transfer rate (DART)
b. The quarterly reporting periods will be:- January – March
- April –June
- July – September
- October - December
c. ACI will compare the Participants (TRIR) and (DART) data with their rates since they enrolled in the partnership program.
d. OSHA log 300 will be used to track the number of work-related injuries and illnesses.2. Participants will promote cooperative relationship between labor and management that increases employee participation in hazard awareness training in topics relevant to their type of work. 2. a. Participants will continue to: - provide a minimum 2-hour safety orientation to newly-hired personnel, including temporary personnel,
- ensure every worker is provided safety training relevant to their tasks,
- provide additional training to ensure awareness of new and existing OSHA regulations, and
- implement a 6-foot fall protection rule.
b. On-site project personnel will assist in conducting training relevant to their expertise.
c. Participants will provide a comprehensive Job Site Safety Orientation for all workers prior to allowing them to work on site.
d. Participants will conduct weekly toolbox safety meetings and encourage workers to lead the talks.
e. Participating members will train their employees how to use the Hazard Reporting Procedures in Appendix B as a means for individuals to report previously unrecognized hazards that could cause injury, illness or death to anyone working on, or in close proximity to the construction project.
f. Participating members will develop a company safety committee that includes workers and meets quarterly.2. a. On a quarterly basis, Participants will track and provide ACI to report to OSHA data collected from:
b. Training logs to track number of employees trained and number of hours spent on training.
c. Minutes of tool box meeting to track and document number of attendees.
d. Completed WISH forms.
e. Completed site audits to track the number of hazards observed and tracked to mitigation.
f. Completed Hazard Reporting forms.3. Increase knowledge and application of the Participating member's worker's abilities to identify and prevent the most common causes of workplace injuries and illnesses in the construction industry, included but not limited to: falls, electrical safety, struck-by, caught in/between, silica, carbon monoxide, heat stress, cranes and noise. 3. a. Provide 10 and 30 hour OSHA training courses (Spanish & English)
b. Conduct weekly toolbox safety meetings that include worker participation.
c. Include worker participation in weekly site audits.
d. Provide additional safety awareness training pertinent to the task as required by OSHA.3. A written record will be maintained for tallying and reporting to ACI the number conducted and/or number of attendees for:
a. Safety audits conducted each week by hourly and salaried project and safety personnel to verify that identified hazards are addressed.
b. Hourly and salaried employee attendance at toolbox meetings.
c. Hourly and salaried employee attendance at all types of safety training.4. Improve communication for sharing safety related information among Participating members and assist in identifying potential near-miss, incident and injury trends. 4. a. Participants will use the Tally Report in Appendix B to track additional leading indicators quarterly.
b. Participating members will attend quarterly Partnership Safety Committee meetings.
c. Participants will document Safety Review meetings, conference calls with ACI, OSHA, OSHA On-Site Consultation and other Participating members.4. ACI will collect data submitted quarterly by Participants to measure leading indicators that identify trends and contribute to lowering Participant's injury and illness rates, such as:
a. Specific types of hazards identified and corrected
b. Number and type of tools and equipment removed from service
c. Pre-planning safety meetings, phone conferences, e-mail exchanges
d. Specific training types5. One hundred percent (100%) of Participating contractors and subcontractors will have site-specific comprehensive written safety and health programs. 5. Written Safety and Health programs will be required for all contractors, subcontractors and tier-subcontractors. 5. Participating members serving as a general or managing contractor will require all of their contractors, subcontractors, and tier-subcontractors have their safety and health programs available for review. -
ANNUAL EVALUATION:
OSHA and ACI shall conduct annual evaluations to identify the strengths and weaknesses of the partnership's strategies and progress in meeting the established goals as specified in Appendix C of CSP 03-02-003 Effective Date: November 06, 2013, OSHA Strategic Partnership Program for Worker Safety and Health directive. The evaluations will be a collaborative effort of ACI and OSHA.
Following implementation of the Partnership agreement, all Participating members shall submit a data form quarterly to ACI so Total Recordable Incident Rate (TRIR) and Days Away Restriction and Transfer (DART) rates can be measured. Such information will be used as an ongoing evaluation tool helping to gauge the effectiveness of the program, and it will be used to compile the annual evaluation to be shared with OSHA.
It is anticipated that OSHA's onsite enforcement verification of the effectiveness of this Partnership agreement may occur during the normal course of compliance investigations and onsite inspections consistent with the criteria specified within the CSP 03-02-003 directive.
-
VERIFICATIONS:
- OSHA will randomly select from the Participating member list at least 10% and no less than three of the Participants for unannounced verifications that include at least one on-site non-enforcement verification, and one off-site verification.
- Participants are encouraged to schedule non-enforcement inspections with OSHA On-Site Consultation throughout the duration of their participation in the Partnering agreement.
- The on-site non-enforcement inspections will follow standard inspection protocols as per OSHA's Field Operations Manual for comprehensive site inspections.
- For programmed inspections on construction worksites, OSHA's "Focused Four" inspection provision is available only where the Participant has effective safety and health programs fully compliant as defined within the CSP 03-02-003 directive.
- Inspections conducted in response to complaints, local emphasis programs, or referrals will qualify as the verifying inspection if, in addition to addressing the complaint/referral item(s), the compliance officer completes a comprehensive site inspection.
- OSHA will recognize and consider ACI safety-training programs when inspecting jobsites of Partnering members.
- Participating members remain subject to OSHA inspections and investigations in accord with established agency procedures.
- Workers or worker representatives will be involved in verifications in a manner similar to their involvement in OSHA inspections. Workers may exercise their rights under the OSH Act without fear of retaliation from their employer.
-
INCENTIVES:
- OSHA's Field Operations Manual details opportunities available during citation/case settlement for all employers who undergo on-site enforcement inspections. These opportunities are also available for Participating members.
- The Participating members' sites will be given priority consideration for compliance assistance and offsite technical assistance.
-
MANAGEMENT/OPERATION OF THE PARTNERSHIP:
ACI will:
- Administer this Partnership program, including Participating member application evaluations. This evaluation will include demonstrated safety and health programs, training commitments, OSHA citation history, fatalities, injury/illness experience and similar factors. ACI will accept new Participating member applications throughout the year from new member companies.
- Serve as the principal safety resource for ACI Participating members as requested.
- Act as liaison for Participating members with OSHA if requested. Participants may call ACI with questions and ACI will contact OSHA for responses. ACI may attend informal conferences involving Participating members of the Partnership.
- Provide to the Cincinnati OSHA office the names of all Participating members.
- Conduct initial application screening of ACI members wishing to become a Participating member.
- Conduct periodic statistical evaluations to determine the impact and effectiveness of this Partnership agreement with OSHA.
- Conduct onsite audits of its members upon request.
OSHA will:
- Designate an experienced member of the Cincinnati Area Office to serve as a resource and liaison for Partnership Participants.
- Provide an experienced member of the Cincinnati Area Office to assist at ACI training sessions, such as the annual ACI Safety Day and training sessions for new Participants, as resources permit.
- Designate an experienced member of the Cincinnati Area Office to meet quarterly with Partnership Participants and quarterly at the Partnership Safety Committee Meetings.
- Designate an experienced member of the Cincinnati Area Office to meet with ACI members at least quarterly to discuss current jobsite findings, current violation trends and possible options/corrective measures to eliminate hazards.
- Share information on current violations, statistics, and relevant standard interpretations, proposed standards, etc. with ACI members.
-
WORKER/EMPLOYER RIGHTS:
This Partnership does not preclude workers and/or employers from exercising any right provided under the OSH Act (or, for federal workers, 29 CFR 1960), nor does it abrogate any responsibility to comply with the Act.
-
TERMINATION OF AGREEMENT:
This agreement will terminate on ________________, which is (5) five years from the date of the signing. If any signatory of this agreement wishes to terminate their participation prior to the established termination date, written notice of the intent to withdraw must be provided to all other signatories.
If OSHA chooses to withdraw its participation in the Partnership, the entire agreement is terminated. For non-signatory participants of the OSP, OSHA may terminate the Participant's involvement at any time with written notice. Additionally, the Participant may withdraw its participation from the OSP at any time with written notice to OSHA of the intent to withdraw.
-
SIGNATURES:
Signature of intent to participate in this ACI/OSHA Partnership: Based upon a mutual interest to protect construction workers in the Cincinnati Area Office Jurisdiction, the parties below agree to the terms of this ACI/OSHA Partnership Agreement:
Partner Name:
Allied Construction IndustriesContact Person:
Susan BermanAddress:
3 Kovach Drive
Cincinnati, OH 45215Title:
Safety Program ManagerPhone:
(513) 221-8020Fax:
(513) 221-8023
Terry M. Phillips, Executive Director
Allied Construction Industries
Date:
Susan Berman, Safety Manager
Allied Construction Industries
Date:
Ken Montgomery, Area Director - Cincinnati
Occupational Safety & Health Administration
Date:
Appendix A
Current Participating Members 2017
Appendix B
WISH Form, Hazard Reporting Procedures and Sample Tally Report
Participant Logo
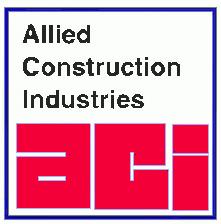
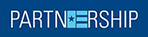
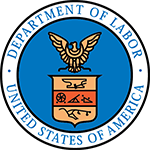
DATE:
At the beginning of each work shift, the Crew Foreman and Crew discuss the task they will perform this shift and do the following:
|
||
Worker Signature @ Start of Shift |
Badge # |
*Initial @ |
End of Day - Reviewed By:
Project Supervisor:
Project Safety:
Release Date: November, 2016
PROJECT NAME:
Y N
▢ ▢ Competent Person Required (excavations, scaffolds, confined spaces, etc.)
Competent Person:____________________
Procedures/Permit Required
Y N
▢ ▢ Job Safety Analysis (JSA)
▢ ▢ Trench/Excavation
▢ ▢ Signs/Barricades
▢ ▢ Line Break/Hot Tapping
▢ ▢ Hazardous Materials
▢ ▢ Roof Access
Y N
▢ ▢ Hot Work
▢ ▢ Lockout/Tagout
▢ ▢ Confined Space
▢ ▢ Scaffolds
▢ ▢ Crane Lift
▢ ▢ Other:_______
Training Qualification and/or Certification Required:
Y N
▢ ▢ Aerial Work Platform
▢ ▢ Scissor Lift
▢ ▢ Rough Terrain Forklift
▢ ▢ Powered Indust. Vehicle
▢ ▢ Skid Steer Loader
▢ ▢ Powder Actuated Tool
Y N
▢ ▢ Traffic Control
▢ ▢ Rigging/Signaling
▢ ▢ Confined Space
▢ ▢ Crane Operator
▢ ▢ Respirator Exam/Fitted
▢ ▢ Other:_______
Special Equipment/Tasks
Y N
▢ ▢ Guard Rails
▢ ▢ Flagging
▢ ▢ Barricades
▢ ▢ Signage
▢ ▢ Confined Space Rescue
Y N
▢ ▢ Traffic Control
▢ ▢ Air Monitir
▢ ▢ Fire Extinguisher
▢ ▢ Permit
▢ ▢ Other:_______
Fall Protection: 6-Foot Rule (Inspect All Equipment Before Use!)
Y N
▢ ▢ Full-Body Harness
▢ ▢ Retractable
▢ ▢ Lanyard
▢ ▢ Positioning Device
▢ ▢ Rope Grab
Y N
▢ ▢ Cross-over Strap
▢ ▢ Concrete Anchor
▢ ▢ Decking Plate Anchor
▢ ▢ Other:_______
Personal Protective Equipment (PPE):
Y N Head/Face
▢ ▢ Hazard Hat/Safety Glasses
▢ ▢ Ear Plugs/Ear Muffs
▢ ▢ Face Shield
▢ ▢ Dust Mask (disposable)
Y N
▢ ▢ Goggles
▢ ▢ Welding Hood
▢ ▢ Respirator
▢ ▢ Other:_______
Y N Hands
▢ ▢ Jersey/Cotton
▢ ▢ Chemical Resistant
▢ ▢ Mechanics
▢ ▢ Anti-Vibratory
Y N
▢ ▢ Leather
▢ ▢ Welding/TIG
▢ ▢ Rubber or Latex
▢ ▢ Other:_______
Y N Clothing
▢ ▢ FR Welding Jacket/Pants
▢ ▢ Other;
Y N
▢ ▢ Chemical Resistant
Y N Foot
▢ ▢ Hard Side Boots
▢ ▢ Over Boots
Y N
▢ ▢ Safety Toe Boot
▢ ▢ Other:_______
At the end of the work shift, Crew Forman asks Crew questions below. *Crew must initial next to their name after review complete.
Y N
▢ ▢ 1. Was anyone on this crew injured today? (if Yes, explain)
▢ ▢ 2. Did a near-miss or unplanned incident occur today? (if Yes, explain)
▢ ▢ 3. If yes was checked in 1 or 2, was it reported to Project Safety?
▢ ▢ 4. Did any problems make it difficult to perform your work today?
1. List Steps Required To Perform This Task |
2. Itentify What Hazards Exsist or May Occur With This Task |
3. List Safe Solutions To Complete This Task |
Participant Logo
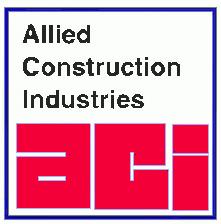
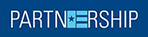
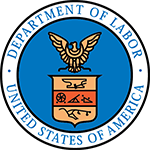
COMPLETE THIS FORM ONLY IF NO INJURY HAS OCCURED
If an injury has occured please complete an Incident Analysis Report or OSHA 301.
PURPOSE
The Hazard Reporting Procedures were established to provide a means for individuals to report perviously unrecognized hazards that could cause injury, illness or death to anyone working on, or in close proximity, to the project.
This procedure does not prohibit workers from exercising their right to refuse unsafe work, as defined by the Occupational Safety and Health Act. In addition, workers should report a hazard without fear of retaliation or reprimand.
The following actions must be taken:
Person Reporting:
- When possible, resolve the hazard first, then inform your immediate Supervisor of the hazard and the corrective action taken.
- If intervention by a Supervisor is necessary, report the hazard either verbally or on this form. For hazards requiring immediate attention, immediate VERBAL notification comes first!
- If the hazard does not require immediate attention, complete Section A below and forward the original to your immediate Supervisor.
Supervisor:
- Review the hazard reported, and in consideration of the circumstances, respond to the workers' concerns as soon as possible, (but not later than 24 hours after receipt of report.) Response may be any of the following:
- resolution of the concern;
- a timetable for the resolution of the concern;
- explaination that steps have been taken towards the resolution (i.e. maintenance scheduled); or
- schedule a time to further discuss the concern.
- Complete section B within (5) work days, unless additional time is approved by the designated Company Safety Representative.
- After corrective action is complete, inform the person who reported the hazard what actions were taken.
- Send original to the designated Company Safety Representative and a copy to the person who reported the hazard.
SECTION A(PERSON REPORTING) | Are You: (Please Circle) (Company Name) Employee/ Contractor Employee/ Project Visitor | |
:( ) - | Name: (Please Print) | |
Project Name: | Date: | |
Hazard Description (Please Be Detailed): | ||
Have Accidents Been Caused By This Hazard? (Please Circle) Yes No Don't Know | ||
If yes, give details: | ||
Corrective Action Recommended/Taken: | ||
SECTION B(SUPERVISOR) | Name: (Please Print) | |
:( ) - | Date/Time Report Received: / / AM PM | |
Signature: | Date Complete: |
RECOMMENDATIONS to prevent further occurances of this type of hazard (please complete). There may be more than one response.
Risk Control Options |
Corrective Action Required |
By Whom |
By When |
1. Elimination (i.e. remove) | |||
2. Substitution (i.e. alternate) | |||
3. Engineering (i.e. controls/guards) | |||
4. Administration (i.e. standard operating procedures, training) | |||
5. Personal Protective Equipment (PPE) (i.e. safety glasses, hard hats, gloves) |
November 30, 2016
SAMPLE ACI/OSHA Quarterly Report Data
Training Type | # Sessions | # EEs Trained | # EE Hours | # Sup/Mgrs Trnd | # Sup/Mgr Hours |
Fall Protection | 15 | 13 | 585 | 5 | 225 |
PIT | 4 | 61 | 122 | 1 | 4 |
RT | 4 | 61 | 122 | 1 | 4 |
Skid Steer | 4 | 61 | 122 | 1 | 4 |
Aerial | 4 | 61 | 122 | 1 | 4 |
Confined Space | 2 | 5 | 40 | 2 | 16 |
FA/CPR | 2 | 0 | 0 | 13 | 52 |
Respirators | 1 | 1 | 2 | 0 | 0 |
Rigging | 10 | 104 | 1040 | 1 | 10 |
Signaling | 10 | 104 | 1040 | 1 | 10 |
HazWOper | 1 | 0 | 0 | 2 | 16 |
Toolbox Talks | 0 | 0 | 0 | 0 | 0 |
Trenching/Excav | 0 | 3 | 0 | 0 | 0 |
DFSP | 0 | 0 | 0 | 0 | 0 |
Accident Invest. | 0 | 8 | 0 | 2 | 0 |
NH Orientations | 2 | 2 | 12 | 1 | 6 |
Proj. Orientations | 3 | 13 | 13 | 1 | 3 |
Supt. Meetings | 0 | 0 | 0 | 0 | 0 |
Safety Council | 3 | 0 | 0 | 1 | 3 |
Insurance | 1 | 0 | 0 | 3 | 6 |
BWC | 0 | 0 | 0 | 0 | 0 |
Safety Day (Planning) | 4 | 0 | 0 | 1 | 8 |
TSSD | 3 | 0 | 0 | 2 | 12 |
ACI Sfty Comm Meeting | 4 | 0 | 0 | 1 | 8 |
ACI/OSHA Partn Mtg | 2 | 0 | 0 | 1 | 4 |
Challenge Mtg | 1 | 0 | 0 | 1 | 2 |
D&M Sfty Comm | 1 | 2 | 4 | 9 | 18 |
OSHA Update | 0 | 0 | 0 | 1 | 0 |
OSHA 10 | 10 | 104 | 10400 | 1 | 150 |
8 HR Refresher | 0 | 0 | 0 | 0 | 0 |
BI/MP Refresher | 0 | 0 | 0 | 0 | 0 |
Misc. Training - Lead | 0 | 5 | 0 | 2 | 0 |
Misc. Training - Asbestos | 0 | 5 | 0 | 2 | 0 |
Misc. Training - Incident Rep. | 3 | 3 | 9 | 1 | 12 |
Misc. Trng - Concrete Placem | 0 | 0 | 0 | 3 | 0 |
Misc. Trng - FP Symposium | 1 | 0 | 0 | 3 | 24 |
Biohazard Training | 10 | 104 | 520 | 1 | 5 |
AGC Safety Committee | 1 | 0 | 0 | 1 | 4 |
Misc Mtg - Dept Head | 3 | 0 | 0 | 13 | 39 |
Misc Mtg - TPA | 2 | 0 | 0 | 1 | 3 |
Misc Mtg - Supplier | 2 | 0 | 0 | 1 | 2 |
Misc Mtg - Crane Pre-Erect | 1 | 0 | 0 | 5 | 5 |
Misc Mtg - Planning- | 0 | 0 | 0 | 0 | 0 |
Misc Mtg - Planning- | 0 | 0 | 0 | 0 | 0 |
Safety Pre-Qual | 15 | 0 | 0 | 1 | 7.5 |
Create/Rev Policy/Prog | 1 | 0 | 0 | 1 | 2 |
Review Policy | 2 | 0 | 0 | 1 | 2 |
Create JHA - Proj. Specific | 0 | 0 | 0 | 0 | 0 |
Create SSSP | 1 | 0 | 0 | 1 | 8 |
Totals | 133 | 720 | 14153 | 90 | 678.5 |
SAMPLE ACI/OSHA Quarterly Report Data
Projects |
# Inspections |
# Hazards Identified |
# Hazards Abated |
#EE's |
#Superv |
# Toolbox Talks |
# DFSP Talks |
# Incident Investigations |
# WISH Complete |
# Tools/Equip Rem.Frm Svc. |
OSHA or OSHA OnSite |
# Positive Comments |
Project A | 0 | 0 | 0 | 0 | 0 | 0 | 0 | 0 | 0 | 0 | 0 | 0 |
Project B | 0 | 0 | 0 | 0 | 0 | 0 | 0 | 0 | 0 | 0 | 0 | 0 |
Project C | 0 | 0 | 0 | 0 | 0 | 0 | 0 | 0 | 0 | 0 | 0 | 0 |
Project D | 0 | 0 | 0 | 0 | 0 | 0 | 0 | 0 | 0 | 0 | 0 | 0 |
Project E | 0 | 0 | 0 | 0 | 0 | 0 | 0 | 0 | 0 | 0 | 0 | 0 |
Project F | 0 | 0 | 0 | 0 | 0 | 0 | 0 | 0 | 0 | 0 | 0 | 0 |
Project G | 0 | 0 | 0 | 0 | 0 | 0 | 0 | 0 | 0 | 0 | 0 | 0 |
Project H | 0 | 0 | 0 | 0 | 0 | 0 | 0 | 0 | 0 | 0 | 0 | 0 |
Project I | 0 | 0 | 0 | 0 | 0 | 0 | 0 | 0 | 0 | 0 | 0 | 0 |
Project J | 0 | 0 | 0 | 0 | 0 | 0 | 0 | 0 | 0 | 0 | 0 | 0 |
Project K | 0 | 0 | 0 | 0 | 0 | 0 | 0 | 0 | 0 | 0 | 0 | 0 |
Project L | 0 | 0 | 0 | 0 | 0 | 0 | 0 | 0 | 0 | 0 | 0 | 0 |
Project M | 0 | 0 | 0 | 0 | 0 | 0 | 0 | 0 | 0 | 0 | 0 | 0 |
Project N | 0 | 0 | 0 | 0 | 0 | 0 | 0 | 0 | 0 | 0 | 0 | 0 |
Project O | 0 | 0 | 0 | 0 | 0 | 0 | 0 | 0 | 0 | 0 | 0 | 0 |
Minus # Positive notes on weekly reports |
0 | 0 | ||||||||||
Totals | 0 | 0 | 0 | 0 | 0 | 0 | 0 | 0 | 0 | 0 | 0 | 0 |
Total Hrs. EE Training | 0 | 0 | ||||||||||
Total Hrs. Superv Training | 0 | 0 | ||||||||||
Total Training |
0 | 0 |
Quarterly Report Period:
Hazard Types by Project
Projects |
18 Elev. Change
|
Access
|
Barricade
|
Compressed Gas
|
Crane Training
|
Electrical
|
Equipment Training
|
Equip. Unattended
|
Equip. Manual
|
Equip Spotter
|
Eye Protection
|
Eyewash
|
Face Protection
|
Fall Protection
|
Fire Extinguisher
|
Flammable
|
Floor Opening
|
Gas Monitor
|
Generator
|
Guardrail
|
Hand/Glove
|
HazCom
|
Housekeeping
|
Impalement
|
Ladder
|
Nails In Lumber
|
Posting
|
PPE
|
Project Orientation
|
Respriatory Prog
|
Scaffold
|
Seat Belt
|
Sharp Edge
|
Signage
|
Silica Hazard
|
Sling
|
Slip/Trip
|
Struck By
|
Tag Line
|
Tool Handle Mis
|
Trench/Excavation
|
Trench Form
|
Wire Rope Rigging
|
WISH
|
|
Drill Removed
|
Extension Chord
|
Fire Ext. RFS
|
Fuel Cont. RFS
|
Generator RFS
|
Grinder RFS
|
Harness RFS
|
Ladder RFS
|
Lanyard RFS
|
Positioning Dev. RFS
|
Respirator RFS
|
Saw RFS
|
SRL RFS
|
Sling RFS
|
Wire Rope Rigging
|
Total By Project
|
---|---|---|---|---|---|---|---|---|---|---|---|---|---|---|---|---|---|---|---|---|---|---|---|---|---|---|---|---|---|---|---|---|---|---|---|---|---|---|---|---|---|---|---|---|---|---|---|---|---|---|---|---|---|---|---|---|---|---|---|---|---|
Project A | 0 | 0 | 0 | 0 | 0 | 0 | 0 | 0 | 0 | 0 | 0 | 0 | 0 | 0 | 0 | 0 | 0 | 0 | 0 | 0 | 0 | 0 | 0 | 0 | 0 | 0 | 0 | 0 | 0 | 0 | 0 | 0 | 0 | 0 | 0 | 0 | 0 | 0 | 0 | 0 | 0 | 0 | 0 | 0 | 0 | 0 | 0 | 0 | 0 | 0 | 0 | 0 | 0 | 0 | 0 | 0 | 0 | 0 | 0 | 0 | 0 |
Project B | 0 | 0 | 0 | 0 | 0 | 0 | 0 | 0 | 0 | 0 | 0 | 0 | 0 | 0 | 0 | 0 | 0 | 0 | 0 | 0 | 0 | 0 | 0 | 0 | 0 | 0 | 0 | 0 | 0 | 0 | 0 | 0 | 0 | 0 | 0 | 0 | 0 | 0 | 0 | 0 | 0 | 0 | 0 | 0 | 0 | 0 | 0 | 0 | 0 | 0 | 0 | 0 | 0 | 0 | 0 | 0 | 0 | 0 | 0 | 0 | 0 |
Project C | 0 | 0 | 0 | 0 | 0 | 0 | 0 | 0 | 0 | 0 | 0 | 0 | 0 | 0 | 0 | 0 | 0 | 0 | 0 | 0 | 0 | 0 | 0 | 0 | 0 | 0 | 0 | 0 | 0 | 0 | 0 | 0 | 0 | 0 | 0 | 0 | 0 | 0 | 0 | 0 | 0 | 0 | 0 | 0 | 0 | 0 | 0 | 0 | 0 | 0 | 0 | 0 | 0 | 0 | 0 | 0 | 0 | 0 | 0 | 0 | 0 |
Project D | 0 | 0 | 0 | 0 | 0 | 0 | 0 | 0 | 0 | 0 | 0 | 0 | 0 | 0 | 0 | 0 | 0 | 0 | 0 | 0 | 0 | 0 | 0 | 0 | 0 | 0 | 0 | 0 | 0 | 0 | 0 | 0 | 0 | 0 | 0 | 0 | 0 | 0 | 0 | 0 | 0 | 0 | 0 | 0 | 0 | 0 | 0 | 0 | 0 | 0 | 0 | 0 | 0 | 0 | 0 | 0 | 0 | 0 | 0 | 0 | 0 |
Project E | 0 | 0 | 0 | 0 | 0 | 0 | 0 | 0 | 0 | 0 | 0 | 0 | 0 | 0 | 0 | 0 | 0 | 0 | 0 | 0 | 0 | 0 | 0 | 0 | 0 | 0 | 0 | 0 | 0 | 0 | 0 | 0 | 0 | 0 | 0 | 0 | 0 | 0 | 0 | 0 | 0 | 0 | 0 | 0 | 0 | 0 | 0 | 0 | 0 | 0 | 0 | 0 | 0 | 0 | 0 | 0 | 0 | 0 | 0 | 0 | 0 |
Project F | 0 | 0 | 0 | 0 | 0 | 0 | 0 | 0 | 0 | 0 | 0 | 0 | 0 | 0 | 0 | 0 | 0 | 0 | 0 | 0 | 0 | 0 | 0 | 0 | 0 | 0 | 0 | 0 | 0 | 0 | 0 | 0 | 0 | 0 | 0 | 0 | 0 | 0 | 0 | 0 | 0 | 0 | 0 | 0 | 0 | 0 | 0 | 0 | 0 | 0 | 0 | 0 | 0 | 0 | 0 | 0 | 0 | 0 | 0 | 0 | 0 |
Project G | 0 | 0 | 0 | 0 | 0 | 0 | 0 | 0 | 0 | 0 | 0 | 0 | 0 | 0 | 0 | 0 | 0 | 0 | 0 | 0 | 0 | 0 | 0 | 0 | 0 | 0 | 0 | 0 | 0 | 0 | 0 | 0 | 0 | 0 | 0 | 0 | 0 | 0 | 0 | 0 | 0 | 0 | 0 | 0 | 0 | 0 | 0 | 0 | 0 | 0 | 0 | 0 | 0 | 0 | 0 | 0 | 0 | 0 | 0 | 0 | 0 |
Project H | 0 | 0 | 0 | 0 | 0 | 0 | 0 | 0 | 0 | 0 | 0 | 0 | 0 | 0 | 0 | 0 | 0 | 0 | 0 | 0 | 0 | 0 | 0 | 0 | 0 | 0 | 0 | 0 | 0 | 0 | 0 | 0 | 0 | 0 | 0 | 0 | 0 | 0 | 0 | 0 | 0 | 0 | 0 | 0 | 0 | 0 | 0 | 0 | 0 | 0 | 0 | 0 | 0 | 0 | 0 | 0 | 0 | 0 | 0 | 0 | 0 |
Project I | 0 | 0 | 0 | 0 | 0 | 0 | 0 | 0 | 0 | 0 | 0 | 0 | 0 | 0 | 0 | 0 | 0 | 0 | 0 | 0 | 0 | 0 | 0 | 0 | 0 | 0 | 0 | 0 | 0 | 0 | 0 | 0 | 0 | 0 | 0 | 0 | 0 | 0 | 0 | 0 | 0 | 0 | 0 | 0 | 0 | 0 | 0 | 0 | 0 | 0 | 0 | 0 | 0 | 0 | 0 | 0 | 0 | 0 | 0 | 0 | 0 |
Project J | 0 | 0 | 0 | 0 | 0 | 0 | 0 | 0 | 0 | 0 | 0 | 0 | 0 | 0 | 0 | 0 | 0 | 0 | 0 | 0 | 0 | 0 | 0 | 0 | 0 | 0 | 0 | 0 | 0 | 0 | 0 | 0 | 0 | 0 | 0 | 0 | 0 | 0 | 0 | 0 | 0 | 0 | 0 | 0 | 0 | 0 | 0 | 0 | 0 | 0 | 0 | 0 | 0 | 0 | 0 | 0 | 0 | 0 | 0 | 0 | 0 |
Project K | 0 | 0 | 0 | 0 | 0 | 0 | 0 | 0 | 0 | 0 | 0 | 0 | 0 | 0 | 0 | 0 | 0 | 0 | 0 | 0 | 0 | 0 | 0 | 0 | 0 | 0 | 0 | 0 | 0 | 0 | 0 | 0 | 0 | 0 | 0 | 0 | 0 | 0 | 0 | 0 | 0 | 0 | 0 | 0 | 0 | 0 | 0 | 0 | 0 | 0 | 0 | 0 | 0 | 0 | 0 | 0 | 0 | 0 | 0 | 0 | 0 |
Project L | 0 | 0 | 0 | 0 | 0 | 0 | 0 | 0 | 0 | 0 | 0 | 0 | 0 | 0 | 0 | 0 | 0 | 0 | 0 | 0 | 0 | 0 | 0 | 0 | 0 | 0 | 0 | 0 | 0 | 0 | 0 | 0 | 0 | 0 | 0 | 0 | 0 | 0 | 0 | 0 | 0 | 0 | 0 | 0 | 0 | 0 | 0 | 0 | 0 | 0 | 0 | 0 | 0 | 0 | 0 | 0 | 0 | 0 | 0 | 0 | 0 |
Project M | 0 | 0 | 0 | 0 | 0 | 0 | 0 | 0 | 0 | 0 | 0 | 0 | 0 | 0 | 0 | 0 | 0 | 0 | 0 | 0 | 0 | 0 | 0 | 0 | 0 | 0 | 0 | 0 | 0 | 0 | 0 | 0 | 0 | 0 | 0 | 0 | 0 | 0 | 0 | 0 | 0 | 0 | 0 | 0 | 0 | 0 | 0 | 0 | 0 | 0 | 0 | 0 | 0 | 0 | 0 | 0 | 0 | 0 | 0 | 0 | 0 |
Project N | 0 | 0 | 0 | 0 | 0 | 0 | 0 | 0 | 0 | 0 | 0 | 0 | 0 | 0 | 0 | 0 | 0 | 0 | 0 | 0 | 0 | 0 | 0 | 0 | 0 | 0 | 0 | 0 | 0 | 0 | 0 | 0 | 0 | 0 | 0 | 0 | 0 | 0 | 0 | 0 | 0 | 0 | 0 | 0 | 0 | 0 | 0 | 0 | 0 | 0 | 0 | 0 | 0 | 0 | 0 | 0 | 0 | 0 | 0 | 0 | 0 |
Project O | 0 | 0 | 0 | 0 | 0 | 0 | 0 | 0 | 0 | 0 | 0 | 0 | 0 | 0 | 0 | 0 | 0 | 0 | 0 | 0 | 0 | 0 | 0 | 0 | 0 | 0 | 0 | 0 | 0 | 0 | 0 | 0 | 0 | 0 | 0 | 0 | 0 | 0 | 0 | 0 | 0 | 0 | 0 | 0 | 0 | 0 | 0 | 0 | 0 | 0 | 0 | 0 | 0 | 0 | 0 | 0 | 0 | 0 | 0 | 0 | 0 |
Totals |
0 | 0 | 0 | 0 | 0 | 0 | 0 | 0 | 0 | 0 | 0 | 0 | 0 | 0 | 0 | 0 | 0 | 0 | 0 | 0 | 0 | 0 | 0 | 0 | 0 | 0 | 0 | 0 | 0 | 0 | 0 | 0 | 0 | 0 | 0 | 0 | 0 | 0 | 0 | 0 | 0 | 0 | 0 | 0 | 0 | 0 | 0 | 0 | 0 | 0 | 0 | 0 | 0 | 0 | 0 | 0 | 0 | 0 | 0 | 0 | 0 |