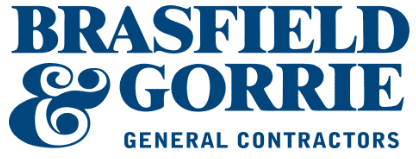
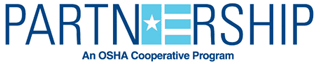
United States Department of Labor
Occupational Safety & Health Administration
Omni Oklahoma City
Strategic Partnership Between
Occupational Safety and Health Administration Oklahoma City Area Office,
And
Brasfield & Gorrie, LLC.
Background
Brasfield & Gorrie, L.L.C., a construction firm with its headquarters in Birmingham, AL and an office in Atlanta, Georgia was selected as the Construction Manager for the OMNI in Oklahoma City, Oklahoma.
The Oklahoma Area Office of the Occupational Safety and Health Administration (OSHA); Brasfield & Gorrie, L.L.C.; Oklahoma Department of Labor (ODOL) – Consultation; participating project subcontractors; and labor organizations recognize the need for a safe and healthy jobsite. The goal of this Partnership agreement is to help ensure that an injury free safety culture is established creating a safe environment for all workers, staff, the public and visitors of the project.
This Partnership is designed to not only address the hazards within the construction industry, but also to promote and recognize jobsites that demonstrate an effective safety and health program.
This document will serve to establish a cooperative effort in ensuring safety and maintaining an open line of communication between OSHA, ODOL – Consultation, Brasfield & Gorrie, L.L.C., participating project subcontractors and labor organizations on this project.
Specifications and assignments within this Partnership document do not relieve the contractors from or lessen their safety & health responsibilities nor change any contractual obligations between Brasfield & Gorrie, L.L.C., or any of the participating project subcontractors. Nor does it lessen any/all affirmative defenses, legal rights or due process afforded contractors with respect to Agency enforcement action.
Project Description
Opening in early 2021, Omni Oklahoma City Hotel will pay homage to the heritage and modern progress of the city. It will take inspiration from the evolving context of a city surrounded by the pastoral landscape of the Oklahoma terrain. The hotel will welcome guests with touches of elegant tradition paired with a sophisticated mix of contemporary and approachable comfort. The hotel, located at 400 S. Robinson, Oklahoma City, OK will feature 605 luxurious guest rooms, inclusive of 26 suites, with dramatic views of the 70-acre Scissortail Park and the downtown skyline. A true outdoor recreation, entertainment and culinary destination, Omni Oklahoma City Hotel will offer seven dining outlets, an expansive pool deck with event space, retail, 78,000 square feet of indoor and outdoor meeting space and a Mokara Spa. The project began in September 2018 with an approximate construction duration of 28 months.
Identification of Partnership Organizations
Brasfield & Gorrie, L.L.C.
Participating Project Subcontractors
OSHA – Oklahoma City OfficeAll subcontractors that work on this project are considered non-signatory participants.
PURPOSE/SCOPE
This Partnership was developed jointly by the Occupational Safety and Health Administration (OSHA), and Brasfield & Gorrie, LLC (Brasfield & Gorrie). The common objective and goals of the Partnership include the following:
- Reduce injuries and illnesses;
- Increase safety and health training; and
- Increase the number of employers with safety and health management systems.
This Partnership is consistent with OSHA's long-range efforts to develop a contractor/government Partnership approach to safety management. It allows for better use of OSHA resources and innovation in safety management. It will also encourage more participation in the safety process from the construction industry.
To facilitate the goal of reducing occupational related fatalities and serious injuries within the construction industry, OSHA and Brasfield & Gorrie will implement a Partnership under the OSHA Strategic Partnership Program (OSPP). This Partnership covers the OMNI Hotel in Oklahoma City, Oklahoma.
By combining their efforts, skills, knowledge and resources, OSHA and Brasfield & Gorrie expect to reduce exposure to hazards and thereby decrease the possibility of serious injuries and fatalities at the OMNI Hotel Oklahoma City.
GOALS/STRATEGIES/PERFORMANCE MEASURES
The primary objective of this Partnership is to create a working relationship that focuses on preventing work-related fatalities, controlling or eliminating serious workplace hazards, and establishing a foundation for the development of an effective safety and health program. The goals employed to achieve these results will include the following:
GOALS STRATEGIES MEASURES Developing a Brasfield & Gorrie, L.L.C./government partnership that will encourage involvement by the owner, construction manager and subcontractors in the improvement of safety and health performance.
Require regular involvement by Brasfield & Gorrie, L.L.C. and participating subcontractors in the oversight of and improvement of S&H performance through completion of the project
Review of site-specific safety plans
Verify by reviewing the number of participating subcontractors that have implemented and/or improved written safety and health management systems. Subcontractors will meet Safety submittal requirements including a written safety program that meets or exceeds Brasfield & Gorrie, L.L.C.'s Health and Safety program.
Maintain an OSHA recordable injury frequency at or below the national average for the applicable SIC/NAICS code. Providing a safe and healthy work environment for construction industry workers employed at this project.
a) Review the OSHA 300 Log data of the Partnership participants and their contractors, excluding OSHA.
b) Calculate Total Case Incident Rate (TCIR) and Days Away From Work, Restricted, Or Job Transferred (DART) 1 rates.
c) Compare this data with the baseline rates for the Partnership.
a) This goal will be measured by the number of companies participating in the Partnership, which reduce their TCIR and DART rates below the baseline for the Partnership.
b) The baseline rate will be based on the 2016 BLS rates for Non-Residential Construction, NAICS 2362, which are 2.4 and 1.3.
Effectively control workplace hazards by increasing the number of construction companies with safety and health management systems (SHMS).
Methods to evaluate the participants' performance in this area will include the implementation of comprehensive safety and health management systems and the increase in the number of employers that establish effective safety and health management systems.
Compare the number of participants that develop and implement effective SHMS as a result of participating in the Partnership, to the baseline for the Partnership.
The baseline will be established during the initial year of the Partnership.
Increase the number of employees that are provided effective safety and health training, such as the OSHA 10-hour course and relevant Competent Person and user level training.
Evaluate employers that provide employees with OSHA 10-hour/ OSHA 30-hour training and appropriate Competent Person and user training and establish baseline.
Provide or assist in providing necessary training.
Compare the number of employees provided safety and health training, as a result of participating in the Partnership, to the number of employees provided training during the baseline (initial) year of the Partnership.
1Days Away from work, Restricted, or job Transferred (DART) rate: This includes cases involving days away from work, restricted work activity, and transfers to another job. It is calculated based on (N / EH) x (200,000) where N is the number of cases involving days away, and/or restricted work activity, and/or job transfer; EH is the total number of hours worked by all employees during the calendar year; and 200,000 is the base number of hours worked for 100 full-time equivalent employees. For example: Employees of an establishment including management, temporary, and leased workers worked 645,089 hours at this worksite. There were 22 injury and illness cases involving days away and/or restricted work activity and/or job transfer from the OSHA 300 Log (total of column H plus column I). The DART rate would be (22 / 645,089) x (200,000) = 6.8
- The overall success of the Partnership will be measured as follows:
- The annual and total project aggregate TCIR, DART and DAFW Rates will be compared to the most currently published Bureau of Labor (BLS) National Average rates for construction (NAICS 23), with zero fatalities. The BLS 2016 rates for NAICS 23 are 3.2, 1.9 and 1.4, respectively for TCIR, DART and DAFW will serve as the baseline for the Partnership.
- Project Injury/Illness data will be evaluated for trends in injuries and near misses, from year to year. Partners will seek to establish a Zero incident rate on the Project whereby it is understood that nearly all incidents are linked to human decision-making and therefore preventable when the proper considerations, assessments, controls and decisions are made. Such attitudes and efforts will achieve accident and injury rates well below the latest published BLS national average (2016) for the construction industry, NAICS 23.
- Documented jobsite weekly inspections and observations, with an emphasis on hazard identification and remediation, and tracking the total number of hazards identified and corrected.
- Records of training certifications/training rosters will be maintained. Report the total number of people trained. These may include, but not be limited to, OSHA 10 and 30 hour courses as well as the site orientation and other on-site training.
- Evaluate the effectiveness of the 100% Fall Protection Plan, through the number of plans implemented and/or improved. Additional measurements of effectiveness may include injury/illness records and near misses for falls.
- Safety and Health Programs will be maintained by Brasfield & Gorrie, L.L.C. Reports to be made available quarterly, concerning the general effectiveness of the safety and health programs. Copies will be made available to all members of the Partnership for review.
- Monthly "dashboard" reviews of key performance indicators and applicable metrics. This will be presented, upon request, to the, OSHA Oklahoma Area Office, and ODOL – Consultation.
- The overall success of the Partnership will be measured as follows:
Annual Evaluation
The Partnership will be evaluated quarterly, and will include data used to monitor the success of the Partnership efforts. On a quarterly basis, the Executive Committee comprised of Brasfield & Gorrie, L.L.C.'s Project Director and Safety Manager, appointed Safety Representatives from our Partnership members, a representative from Labor, a representative from ODOL – Consultation, and a representative from OSHA shall meet and discuss the program and make any modifications as required to continually improve the partnership. When an OSHA representative attends these meetings, the meeting will serve as an on-site non-enforcement verification visit by OSHA. A written evaluation will be completed annually and submitted to the Regional OSHA Office.
OSHA STRATEGIC PARTNERSHIP (OSP) BENEFITS/INCENTIVES
Participant benefits from OSHA may include:
- In the event that a company performing work at the site is cited by OSHA, a maximum penalty reduction for good faith will be provided, in accordance with CPL 02-00-159, Field Operations Manual (FOM), dated October 01, 2015. In the event that the FOM is revised, OSHA shall provide such revised FOM provision to Brasfield & Gorrie, L.L.C. and the most current FOM will be utilized.
- Priority will be given to "phone and fax" investigations of all informal complaints in lieu of on-site inspections.
- When hazards cannot be corrected immediately they will be tracked until abatement is completed. Employees exposed to these hazardous conditions will be informed of the hazard and effective interim control measures will be implemented. Proof of tracking and effective interim control measures will be documents and shared with OSHA until final abatement is completed
- This Partnership requires frequent inspections of the worksite by Brasfield & Gorrie, L.L.C., participating subcontractors and other members of the Partnership to identify and correct hazards. It also serves as a model to subcontractors and others by demonstrating how to implement a strong safety and health program on a large multi-employer jobsite. It also encourages a higher level of participation in the safety process by involving everyone on the jobsite. The knowledge gained from this Partnership will be applied to reduce injuries and illnesses at future work sites.
- OSHA Consultation will be available for consultation and job walks upon requests of Brasfield & Gorrie, L.L.C. or participating subcontractors. Brasfield & Gorrie, L.L.C. will participate quarterly and it is required that all subcontractors participate as available quarterly.
OSHA INSPECTIONS/VERIFICATIONS
- OSHA will continue to investigate fatalities and catastrophes should they occur at the jobsite as well as alleged "imminent" danger situations per the FOM. Note: In the event that the FOM is revised, the most current FOM will be utilized.
- OSHA will continue to investigate all complaints and referrals received in accordance with procedures contained in the FOM. Note: In the event that the FOM is revised, the most current FOM will be utilized.
- OSHA will complete at least one focused "monitoring" (on-site enforcement verification visit) inspection each year during the term of the Partnership. These inspections will follow the most current FOM and the "Focused Inspection" protocol {Memorandum from James W. Stanley, "Guidance to Compliance Officers for Focused Inspections in the Construction Industry", dated August 22, 1994 (Revision 2 issued September 20, 1995 and incorporated herein)} addressing hazards related to falls, struck by, caught-in, and electrical hazards. Inspections conducted in response to complaints, Local and/or National Emphasis Programs (LEP/NEP), or referrals will qualify as the monitoring inspection if, in addition to addressing the complaint/LEP/NEP/referral item(s), the compliance officer completes the focused inspection protocol for the worksite.
- On-site non-enforcement verification visits will be performed by OSHA representatives, by their participation in the quarterly Executive Safety Committee meetings (as outlined in Section IV of the Partnership).
- Brasfield & Gorrie, L.L.C. and participating subcontractors will periodically utilize ODOL Consultation's on-site safety and health consultations at the jobsite. Brasfield & Gorrie, L.L.C. will participate quarterly and it is required that all subcontractors participate as available quarterly.
- Brasfield & Gorrie, L.L.C. will permit OSHA access for any inspection to be made pursuant to Section VI paragraphs A, B, and C and will not require an inspection warrant for any such inspection. Brasfield & Gorrie, L.L.C. will be allowed time to have a safety representative accompany OSHA on site.
MANAGEMENT AND OPERATION
Brasfield & Gorrie:
- Establish a jobsite safety team, consisting of a representative of all primary contractors on site, in order to develop an understanding and awareness that all accidents are preventable and unnecessary, and a comprehensive safety and health management system, which includes:
- Management commitment and employee involvement;
- Hazard analysis;
- Hazard control; and
- Arrangement of training assistance for other stakeholders on site.
- Mentor participating subcontractors in safety and health management systems. Subcontractors shall include all multi-tiered subcontractors that arrive for work on the site.
- Where the potential for airborne silica exposure exists, require the use of wet-cutting, or soft-cutting techniques and/or a dust collection system in compliance with Table 1 of 29 CFR Part 1926.1153 and when employee exposure levels require, mandatory use of approved respiratory protection. Where the potential for air borne silica exposure exists, personal air monitoring will be conducted to assess employee exposure levels. Where the potential for other health issues exist (i.e., carbon monoxide, lead, or large-scale use of chemicals in the building interior during floor finishing), Brasfield & Gorrie will coordinate with the subcontractor responsible for creating the hazard and ensure that air monitoring is accomplished to assess employee exposure levels.
- Enforce safety rules and regulations. This role includes holding contractors, subcontractors, and employees accountable for following safety rules and regulations and the ability to remove a contractor's employees and supervisors from the job site, if necessary.
- Ensure that a competent person performs a risk assessment of all fall hazards. The probability and severity of occurrence for each identified hazard will be evaluated to eliminate or reduce the risk through engineering or administrative controls to a level as low as possible. Regarding full hazard risk assessments:
- Critical risks will not be tolerated. A critical risk is defined by work that contains high probability in occurrence, and high severity in consequence. No work will be performed until action is taken to reduce the level of risk to as low as reasonably feasible.
- All personnel exposed to a fall greater than 6 feet shall conform to Brasfield & Gorrie's 100 percent tie-off for all employees with fall exposure at heights at six feet or greater (see Site-Specific Safety and Health Plan (SSSP)).
- To the extent feasible, serious ergonomic hazards will be identified and corrected.
- Ensure that ground fault circuit interrupters (GFCI) are used to protect all electrical circuits that are used for work. All participating contractors will ensure that employees are protected by the use of a GFCI at all times.
- Brasfield & Gorrie's Superintendent and on-site Safety Manager will serve as a point of contact, monitor safety and health at the site and its progress toward achievement of the Partnership goals.
- Brasfield & Gorrie's Superintendent and onsite Safety Manager will ensure that daily Safety Audits are conducted. Brasfield & Gorrie will review participating subcontractors daily log books, note any hazards found, and then review them at the weekly coordination/subcontractor meeting.
- Conduct and document job site safety meetings/toolbox talks on a weekly basis.
- Brasfield & Gorrie's Superintendent and Project Manager will lead, coordinate and conduct a comprehensive site audit on a bi-weekly basis. Safety Committee and subcontractor members will participate in the site safety audit. If non-compliant activity or hazards are discovered, immediate correction is required. Brasfield & Gorrie will document the corrective action taken and share this information with OSHA during the monthly update meetings.
- Audit the Partnership and make recommendations for improvement.
- Share the results of jobsite inspections and information concerning near misses with all workers. Near misses and daily safety audits will be discussed during tool box talks.
- Ensure that no employees are allowed to work directly below a suspended load except for situations where no other safe alternative may exist. In these rare cases, the following criteria must be met:
- Materials being hoisted shall be rigged to prevent unintentional displacement.
- Hooks with self-closing safety latches or their equivalent shall be used to prevent components from slipping out of the hook.
- All loads shall be rigged by a qualified rigger.
- Appropriate use of tag lines will be utilized to minimize work below suspended loads.
- Require the use of appropriate personal protective equipment. Hard hats are mandatory. Employees on site shall wear high-visibility reflective clothing. A 100 percent eye protection program will be implemented. Gloves must be worn when hand injuries are likely to occur.
- Ensure that all signs and warnings will be posted in English and Spanish, as well as any other languages spoken frequently by workers on site.
- Implement an effective Heat Illness Prevention Program (Heat Program) to educate workers about the hazards of working outdoors in the heat and steps needed to prevent heat-related illnesses.
- Provide all data to OSHA that is needed for the annual OSHA Strategic Partnership Program (OSPP) report.
- As a goal, the elimination of work related injuries from inadequate planning and execution by ensuring key job hazards are identified and controlled. Conduct and retain summary documentation of weekly toolbox talks and Crew Work Plans (CWP.)
- Housekeeping initiatives will be introduced to maintain orderly storage of materials and removal of workplace trash and debris:
- Eating, drinking and consumption of food products will only be allowed within designated controlled areas of the project site.
- All trash and waste shall be removed and placed in appropriate provided receptacles.
- Subcontractors will maintain an adequate number of trash containers throughout the floors and areas of construction. All trash will be moved into dumpsters provided at one location on site by Brasfield & Gorrie, L.L.C.
- Project has adopted a continuous clean-up strategy whereby subcontractors are to remove construction debris closely following work activity. Nails and screws are to be bent over or retracted following form stripping operations.
- Access to work areas, ladders, stairs, buck hoist, and storage areas are to remain free and clear of obstructions.
- Methods to control dust will be employed whenever possible (e.g. Wet/dry vacuums, misting, damp wiping, covering / tarping of materials, dust reducing sweeping compounds, etc…)
- Spills and loose materials that pose potential slip hazards are to be cleaned up immediately.
- Tools, equipment, and materials are to be brought and stored only when they are needed and removed from site when no longer required.
- Loose materials are to be contained, stacked, racked and otherwise kept in an orderly condition.
- Fire Extinguishers will be provided by subcontractors for their scope of work.
- Flammable storage cabinets are to be provided by subcontractors for all aerosols, and flammable liquids maintained within the building structure (Most job/tool boxes are not approved for this use).
- Material shall be secured to eliminate the possibility of accidental displacement due to impending inclement weather.
- Employee training and safety meetings:
- All employees working at the project will receive a site-specific safety orientation from Brasfield & Gorrie, L.L.C. covering jobsite safety and health issues and procedures relative to the work being performed. A copy of the Project Safety and Health Work Rules will be provided and signature pages maintained on file.
- Daily pre-task hazard prevention planning will be conducted by all crews. This planning, hazard recognition, and determination of controls will be documented daily Crew Work Plan (CWP) forms. Crew Work Plans will be available in the field for review and periodically audited by the Brasfield & Gorrie, L.L.C. management and project safety staff. CWP records will be filed and maintained in the project trailer.
- Weekly safety meetings will be held by Brasfield & Gorrie, L.L.C. with each participating subcontractor and documentation will be maintained in the Brasfield & Gorrie, L.L.C. project office.
- Periodic job-wide safety meetings will be held and various guest speakers including OSHA, Brasfield & Gorrie, L.L.C., Manufacturer Reps, Vendors, and participating subcontractor Supervision and Safety Personnel will be invited to participate. When an OSHA representative attends these meetings, the meeting will serve as an on-site non-enforcement verification visit by OSHA.
- To help keep safety awareness at peak levels, safety commitment banners, warning signs, safety reminder signs will be strategically placed around the job site.
- Additional craft specific hazard recognition education sessions will be conducted on an as-needed basis by the respective participating subcontractors through weekly tool box talks.
- Provide signage identifying the site as an OSHA Partnership Project.
- In addition to OSHA's notification requirements, Brasfield & Gorrie, L.L.C. will notify the local OSHA office of safety or health related events, which are likely to generate public attention and/or news media coverage. This notification will be provided in a timely manner and will include sufficient background and incident information for responding to agency and public inquiries.
- Establish a jobsite safety team, consisting of a representative of all primary contractors on site, in order to develop an understanding and awareness that all accidents are preventable and unnecessary, and a comprehensive safety and health management system, which includes:
- Subcontractors:
- Appoint a representative to the site Safety Committee who will be responsible for resolving job safety matters and serving as a liaison to Brasfield & Gorrie's Superintendent. Every participating subcontractor will have a person available to participate in the Safety Committee. Participation in this committee will consist of, but will not be limited to, participation in the Project Team Safety walkthroughs and monthly safety update meetings.
- Participate in the monthly Safety Committee/subcontractor meeting and safety audits. If non-compliant activity or hazards are discovered, immediate correction is required. Abatement methods and verification must be submitted to Brasfield & Gorrie's on-site Safety Manager, who will document the correction taken and share this information during the monthly update meetings.
- Conduct jobsite safety inspections for employees under their supervision. These jobsite safety inspections will be in addition to the general inspections that are to occur daily. If non-compliant activity or hazards are discovered, immediate correction is required. Documentation of abatement methods and verification must be submitted to Brasfield & Gorrie's on-site Safety Manager.
- Share the results of jobsite inspections with all workers by posting them in the project office and notifying all workers of the location of the results.
- OSHA:
- Participate, to the extent resources permit, in the monthly Partnership Committee/subcontractor meetings, but will not participate in the walk around inspection, except that the verification visits (see Section VIII. OSHA Verification below) may be scheduled as part of the weekly walk around inspection.
- Serve as a resource and liaison for Partnership participants and also assist with safety and health training, as resources permit.
- Give priority to the construction project, as resources permit, when technical assistance is needed.
- Audit the monthly reports/documents and make recommendations for improvements in meeting Partnership goals.
- Conduct inspections in accordance with section VIII of this Partnership.
- Conduct the annual Partnership evaluation report in accordance with section VI of this Partnership.
SAFETY AND HEALTH MANAGEMENT SYSTEM
Brasfield & Gorrie will use its system to collect and analyze injury and illness trends (including near-miss incidents) by all contractors performing work at the site. This data will be used as a tool to ensure continual safety and health improvement at the site. Brasfield & Gorrie will manage this Partnership effectively by implementing a comprehensive jobsite safety and health management system, which will include the following components:
- Brasfield & Gorrie will complete a risk assessment prior to exposing employees (including contractors' employees) to potential safety and health hazards. This will be accomplished by the use of a Crew Work Plan - Risk Assessment (CWP) form (see Appendix 1 for Crew Work Plan).
- Work with OSHA and Safety Committee members to provide the resources to conduct initial monitoring for toxins which are anticipated to be present during construction of this project (silica, etc.). Employee exposures during activities which may produce these hazards will be assumed and respiratory protection worn until the results of the initial monitoring studies are received and demonstrate no exposure problems or site-based prior surveys show no hazard exists. Brasfield & Gorrie will endeavor to ensure that no work with these materials will occur, thus preventing any exposure.
- Daily audits will be performed by all participating contractors on site. In addition, on a weekly basis, a comprehensive audit of the jobsite will be performed, with the participation of a representative of each contractor currently working on site. Any hazards found during the audits will be corrected promptly. Items noted on the audit will be annotated on a daily log. When hazards cannot be corrected immediately, they will be tracked until abatement is completed. Employees exposed to these hazardous conditions will be informed of the hazard and effective interim control measures will be implemented. A record will be kept of all hazards found during the weekly audits and the number of hazards corrected as a result of the weekly audits.
- Implement an aggressive Fall Protection Plan to include fall protection in all cases where work is being performed 6 feet or more above lower surfaces.
- Ensure employees receive training as follows:
- Brasfield & Gorrie workers will have received OSHA 10-hour training and possess an OSHA 10-hour card, and all Brasfield & Gorrie supervisors will have received OSHA 30-hour training and possess an OSHA 30-hour card. Brasfield & Gorrie will work with all participating subcontractors to provide or assist in providing their safety designee with OSHA 10-hour training.
- All employees will receive a site-specific construction safety orientation covering jobsite safety and health issues, procedures relative to the work being performed, as well as the requirements outlined in the Partnership. In addition, employees shall receive training on the content of the Site-Specific Safety Action Plan for operations they will encounter. This may require periodic retraining of employees on the content of the Site-Specific Safety Action Plan as specific parts of the Plan become relevant at new phases of construction. This material will be provided by Brasfield & Gorrie to the subcontractors' designated safety representative for completion (see Appendix 2 for SSSAP).
- Safety and health training, including the OSHA 10- and 30-hour courses, will be provided to all workers in a language they understand. Either effective translators or bi-lingual instructors will be utilized to perform this training.
- Additional hazard-specific training will be conducted on an as-needed basis.
- Participating subcontractors utilizing other instructors for competent person, OSHA 10/30-hr, and equipment training must provide a valid certification card showing completion of the course. Subcontractors have primary responsibility for providing the safety and health training.
- Participating subcontractors will be required to develop an adequate safety and health management system and must submit them to Brasfield & Gorrie for evaluation.
- Ensure health-related issues which occur during the course of the project are adequately addressed by Brasfield & Gorrie and/or the affected subcontractors, with the assistance of OSHA as its resources permit. All health-related issues will be discussed monthly during the Partnership update meetings.
- An effective hearing conservation program, including noise monitoring and implementation of engineering controls, where possible, will be implemented by Brasfield & Gorrie's Safety Department.
- An effective environmental monitoring program will be implemented to control airborne hazards, such as silica, and will include personal monitoring, employee training, implementation of engineering controls where possible, and the use of respiratory protection when necessary. Previous site-based data will be considered acceptable.
- Ensure compliance with the NFPA 70E when working on live electrical equipment, including training and the availability and use of personal protective equipment. A permit system will be implemented whenever work around live electrical systems will be done to ensure the implementation of appropriate protective measures prior to exposure. The permit form includes requirements for pre-task review and lock out/tag out procedures to be followed.
- Ensure all equipment is adequately guarded.
WORKER INVOLVEMENT/WORKER AND EMPLOYER RIGHTS
This Partnership does not preclude employees and/or employers from exercising any right provided under the OSH Act (the Act), nor does it abrogate any responsibilities of the Partnership participants to comply with rules and regulations adopted pursuant to the Act.
Brasfield & Gorrie, LLC, will ensure employee involvement by establishing an employee Safety Committee that will meet on a monthly basis to share the results of jobsite inspections, information concerning accidents and near misses, suggestions for improvement and recommendations for training for the general workforce. The Partnership members' management and supervisors will also continue to discuss near misses and daily safety audits during toolbox talks.
TERM OF PARTNERSHIP
It is understood that this Partnership shall be in effect until completion of construction activities at the OMNI Hotel Oklahoma City project site, but in no case longer than three-years from the date the Partnership is signed. If any signatory of this Partnership wishes to terminate their participation prior to the established termination date, a written notice of the intent to withdraw must be provided to all other party(s), which provides a 30-day notice.
If OSHA chooses to withdraw its participation in the Partnership, the entire Partnership is terminated. Any party may also propose modification or amendment of the agreement. Changes may be implemented, if all parties are in agreement that the changes are in the best interest of the Partnership.
OMNI Hotel Oklahoma City STRATEGIC PARTNERSHIP
United States Department of Labor
Occupational Safety & Health
AdministrationBased upon a mutual interest to protect construction workers in Oklahoma, the Parties below agree to the above terms of the Brasfield & Gorrie, L.L.C., OSHA Partnering Agreement for The Omni Hotel Oklahoma City Project.
Signed this ______ day of ________ 2019.
Carmen M. Martinez
Acting Area Director
Occupational Safety & Health Administration
Oklahoma City Area Office
Leslie Osborn
Labor Commissioner
Oklahoma Department of Labority Area Office
Doug Coffey
General Superintendent
Bradfield & Gorrie L.L.C
Ethan Gebhart
Superintendent
Brasfield & Gorrie L.L.C
Brent Cash
Senior Project Manager
Brasfield & Gorrie L.L.C
Richard Jewell
Safety Manager
Brasfield & Gorrie L.L.C
Josh White
Regional Safety Director
Brasfield & Gorrie L.L.C
Erick Holt
Safety Manager
Brasfield & Gorrie L.L.C
Appendix 1
REMIND CREW:
YOU SEE IT, YOU OWN IT, YOU SHARE IT
Every crew member has an obligation to stop work if something is unsafe.CREW WORK PLAN SIGN IN/SIGN OUT
CREW SIGNATURES: By signing below, each crew member acknowledges complete understanding of the assigned tasks, identified hazards and the appropriate elimination/mitigation actions. By initialing at the end of the day, each crew member acknowledges that they were not injured. All incidents and injuries should be reported immediately to Brasfield & Gorrie Supervision.
INVOLVED CREW MEMBERS
Name Initial Out 1. 2. 3. 4. 5. 6. 7. 8. 9. 10. 11. 12. 13. 14. ANY CREW MEMBERS (LESS THAN 90 DAYS)
Names: ____________________________
Assigned Coaches: ___________________Names: ____________________________
Assigned Coaches: ___________________*Hardhat Decal should be in place to identify new employees
CREW LEADER POST WRAP UP
Foreman/Crew Leader: _________________
Did we meet or exceed our production goals today? Yes No
If no, what prevented us from reaching our goals? ______________________________________________
What did we learn that we can share with the crew tomorrow?
_____________________________________________
_____________________________________________Is the work area clean and free of debris from the day's work? Yes No
Were there any injuries, property damage, or near misses reported today? Yes No
If yes, notify your Superintendent and the safety department immediately. Who was contacted:
_____________________________________________Description of event: ____________________________
_____________________________________________
_____________________________________________
_____________________________________________REVIEWERS
Superintendent: ________________________________
Safety: _______________________________________
MANAGEMENT PARTICIPATION
Name: _______________________________________
DAILY CREW
WORK PLANDates: ____________________________________
Project Name: ______________________________
Client Name: _______________________________
Location: __________________________________
Foreman: __________________________________
Weather Forecast: ___________________________
PRODUCTION GOALS
What are our production goals for today? 1.
2.
3.
4.
5.
6.
SERIOUS INJURY PRECURSORS
My Highest Risk Activity Today: _______________
________________________________________☐ Work at Height
☐ Utilities Located/Verified
☐ Excavation over 4'
☐ Rigging/Lifting Operations
☐ Demolition
☐ Heavy Equipment Movement (Interaction with foot traffic)
☐ Stored Energy/LOTO
☐ Traffic Control
☐ Overhead Operations (Barricading)
☐ Manual Handling
☐ Working around/near General Public*Start with and Spend Extra Time on any High Risk Activity Identified
CREW INVOLVEMENT QUESTIONS
1. What has changed that will impact our work today? (weather, hazards from other trades, access/egress, location, elevated work, additional material handling, chemicals, new crew members, lighting, public interaction, etc.)
_______________________________________
_______________________________________What did we learn during our last shift that can help us be more productive and safe today?
_______________________________________
_______________________________________EMERGENCY ACTION PLAN
Evacuation Route/Assembly Area:
_______________________________________
Emergency Phone Number:
_______________________________________
Location Address:
_______________________________________EMPLOYEE CERTIFICATIONS REQUIRED
(Check all that Apply)☐ Competent Persons (Excavation, Confined Space, Scaffolds, Fall Protection)
☐ Crane Operator
☐ Forklift Operator
☐ Rigging/Signal
☐ Powder Actuated Tool User
☐ Aerial Lift
☐ Scissor Lift
☐ Respiratory/Fit Testing
☐ Traffic Control FlaggerPERMITS REQUIRED FOR TODAY'S WORK
☐ Confined Space
☐ Excavation
☐ Lockout/Tag out
☐ Critical Lift
☐ Burn/Hot Work
☐ Line Break/Hot Tapping
☐ Scaffolding
☐ Utility Clearances
☐ Lane Closure
Other: ______________________________________JOB/TASK STEP
How are we going to do the work?POTENTIAL HAZARDS OR ERRORS
How can injury occur? What could go wrong?ELIMINATION/CONTROL ACTIONS
What are we going to do about it?
(Include tools, equipment, material, PPE)START WITH THE MOST HAZARDOUS WORK FIRST Consider work that is unfamiliar to any crew member as higher risk. Extra time needs to be spent providing CLEAR, CONCISE INSTRUCTIONS for any work that may be new to any crew member.
OMNI OKC - SAFETY ACTION PLAN
The Safety Action Plan will be reviewed by the project team on a quarterly basis for new ideas and any improvements needed to cultivate a stronger safety culture will be identified.
Schedule A - Scope
Address:
400 S Robinson Ave
Oklahoma City, OK 73109Project Manager:
Matt Mitchell, Alec BrauningSuperintendent(s):
Doug Coffey, Ethan GebhartProject Manager:
Austin Luttrell, Wyatt KellerSenior Project Manager:
Brent BashForeman:
Casey GebhartSenior Safety Manager:
Erick HoltOn-Site Safety Manager:
Richard JewellProject Scope:
OMNI OKC will be a 600,000+ sqft, 17 floor hotel stretching block to block. The hotel will feature a 3-story podium full of lobby space, restaurants, ballrooms, meeting rooms ,and outdoor amenities - proceeded by a room tower stretching floors 4-17. The structure will be cast-in-place concrete and feature 150+ below grade parking spaces.Estimated crew size: 20-25 B&G
Project Duration: September 2018 - January 2021
Deliveries: SW 4th Street & Broadway Avenue
Safety Personnel Duration: October 2018 - January 2021
High Risk Operations/Major Project Challenges:
- Wind & weather
- 4+ projects landlock site
- General public exposure
- Multiple lane/road closures for access/deliveries
- 3 tower cranes
- 2 personnel buck hoists
- Concrete truss tables at levels 4-17
Project Initiatives
- As-Built/Dig Permits: Full size site-drawing to be posted with overlay of all known utilities. All subcontractors will be asked to perform and discuss Dig Permit with B&G before excavating. Subcontractors and B&G to mark installed/existing utilities physicall on-site (utility markers, survey whiskers, etc.)
- Subcontractor JSAs: All subcontractors to perform daily JSAs, B&G to perform Daily Crew Work Plan.
- Falling Object Protection: Debris netting to be used on floors 4-17. Pearl weave fencing to be installed on all guardrails. Sidewalks around site will be closed eliminating need for overhead protection of public.
- Safety Incentives: B&G to implement positive reinforcement/caught-in-the-act recognition during PM/Supt. Safety Walks. Further Safety Milestones to be discussed/celebrated.
Main Areas of Focus/Concern (Updated Quarterly)
- B&G Supervision with Weekend Work: All weekend work shall be arranged through B&G Supervision, and no work to be performed without a B&G Supervisor on-site. Possible night-shift once pre-cast begins.
- First Aid/CPR/AED Certified Employees: 3+ B&G Supervision currently have First Aid/CPR/AED certification. B&G Safety to provide further training at jobsite.
- Public Protection Abatements: Project will have 3 sidewalk closures, a full lane closure on Broadway Ave, and a lane closure on S Shields Blvd t oserve as site access from jobsite trailers. B&G will use yoddocks and fencing with wind screen on the fencing. Debris netting will be used on floors 4-17, jumping every 3 floors. B&G will work diligently to ensure protection to surrounding projects and public.
- Crane Operations: 3 tower cranes with hook heights ranging from 220'-270' will be erected starting Nov. 26th. Tower cranes bases will have enclosure of at least 12' to prevent public access. Crane 2 will swing over convention center project to the south, B&G will coordinate with neighboring contractor. The project will have 2 buck hoists on S Broadway side of project.
- Underground Utilities: 4 utility tie-ins on south edge of site. North edge of site has water line that will be abandoned end of September 2018. High pressure gas main to be relocated by the city by 09/20/2018. Electrical duct bank on south edge of project is marked. *refer to As-Build/Dig Permits section*
- Fall Protection Exposures: Pier piles to have rails around them until poured during foundation work. Safe-T straps to be installed along building edge to prevent secondary falls during leading edge work. Perimeter guardrails, and interior guardrails (shafts, chases, openings, etc.) with pearl-weave netting to be used. *refer to Falling Object Protection section*
- Confined Spaces: Sanitary manhole and water vault have potential to be confined space, although not anticipated at this time.
- Lockout/Tag-out Procedures: Subcontractors to follow LOTO procedures in accordance with, or proceeding B&G requirements. Prism Electric to have meeting before the start of temporary power, as well as the transfer from temporary to permanent to discuss proper LOTO. Testing and troubleshooting is considered hot work and proper procedures to be followed.
- Cleanup/Housekeeping: B&G will mandate trash carts for each subcontractor to practice proactive housekeeping. A trash chute will be installed at the podium, with the potential to extend to the tower.
- Excavations: 12 ft excavation to be protected with temporary shoring during foundation work for underground parking deck/building. Elevator pits of 10' and 7' to be protected by tangent piles. Tower crane 3 foundation may require excavation beyond 5' that will need to be discussed.
- Employee Training Needs: CPR, OSHA 10 Hour, OSHA 30 Hour to be provided. Other training needs will be met as they present themselves. B&G Project Team to be in contact with B&G Safety Department to schedule training.
Subcontractor Safety Management Plan
- Safety Milestones:
- Transitioning from underground work to structure start
- Full building under temporary power
- Full building under permanent power
- Erection/dismantle of tower cranes
- Interior finishes beginning
- Sub Safe Start Meetings: All subcontractors to participate in a Sub Safe Startup Meeting with B&G Project Team. Erick Holt and Richard Jewell to provide safety support during these meetings.
- Supt/PM Walks: Supt./PM Safety Walks to be performed bi-weekly. B&G to request participation from subcontractors, and issue report to subcontractors following walk. Written response to be required if deficiencies are noted during report.
Conditions of Safety Success
Safety success on this project will not be measured by failure rates but rather by the proactive approach that the project teams takes towards eliminating hazards.
- Maintaining consistent attitude of proactiveness to job housekeeping and cleanliness.
- Fully executing on the wind plan.
- Job-specific training and demonstrations (i.e. EAP drill)
- Robus Safety Week 2019 participation at Omni OKC.
- Richard Jewell and B&G Project Team to engage and develop relationships with loca lsafety committee/OKC OSHA.
Appendix 2
/>