Ade-Wifco Steel Products, Inc. Fixes 242 Hazards and Cuts Recordables in Half
Company: Ade-Wifco Steel Products, Inc.
Location: Hutchinson, Kansas
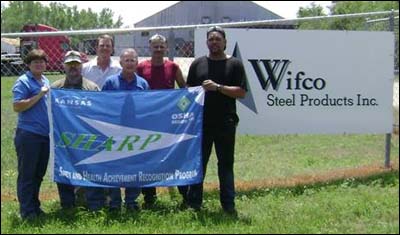
In January 2005, when Fred Ade Jr. bought a steel manufacturing company that serves the oil field market in Hutchinson, Kansas, he knew he needed to make some major occupational safety and health changes. He called on the Kansas Department of Labor (KDOL) for a free, confidential on-site consultation to help him address the highest risks of injuries for his employees. Deborah Grow, a safety consultant and Safety and Health Achievement Recognition Program (SHARP) Coordinator with the Division of Industrial Safety and Health of KDOL, remembers her first visit well. She said, "The facility was so dark and disorganized, it was an accident waiting to happen."
Mr. Ade initially wanted a full-service consultation from KDOL to identify all hazards and evaluate all aspects of the company's safety and health management system; however because of the potential amputation hazards associated with the apparent lack of adequate machine guarding, he requested a limited service that focused on serious machine guarding hazards. On their first visit, KDOL identified a total of 52 hazards.
With the assistance of KDOL, Ade-Wifco developed a machine guarding action plan that also emphasized employee safety training. To assist the company, the KDOL safety consultant provided the company with a number of Occupational Safety and Health Administration (OSHA) compliance presentations and several "tool box topics." Rhonda Barnhart, Ade-Wifco's Safety Coordinator said, "Deborah Grow made it easier for us."
One of the first things Ade-Wifco did was establish an employee - supervisor safety team: the "Safety Ambassador Program." Additionally, KDOL provided training for the safety team on: hazard identification, conducting self inspections, machine guarding, and how to develop and use a job safety hazard analysis program to create safe working conditions. KDOL's training also included topics from the OSHA 10-hour General Industry course which explains OSHA policies and procedures, as well as the fundamental OSHA standards for general industry.
There were a number of creative actions taken by Ade-Wifco. First, Joshua Barden, an intern, was hired from the Manufacturing Technology Program at Hutchinson Community College to work on three major projects: identifying and correcting slip, trip, and fall hazards; inspecting machine safety guards; and properly placing and marking fire extinguishers throughout the facility. Second, Ade-Wifco Steel Products, Inc. instituted a policy to provide a Spanish interpreter for all company safety training. Third, Ade-Wifco took the innovative step of documenting every safety improvement opportunity. As items on this list were corrected, they were closed out; however, the documentation is maintained for reference. They have addressed and closed 280 safety improvement opportunities.
In January 2007, Mr. Ade requested a full-service safety and health consultation from the KDOL Division of Industrial Safety and Health. The company established a two-year work plan to implement the changes and suggestions recommended by the team of consultants from KDOL. However, they found that they were able to accomplish the task in 15 months and were eligible for OSHA's highest safety and health recognition program that focuses on small businesses: the Safety and Health Achievement Recognition Program (SHARP). SHARP recognizes small businesses that have a proven effective safety and health management system by exempting them from OSHA's routine programmed inspections. Companies are awarded a SHARP flag that flies proudly to indicate the exceptionally safe and healthful working environment.
Ade-Wifco Steel Products, Inc. is a tremendous safety success story. In 2008, they became the 94th SHARP company in Kansas. A SHARP company earns far more than recognition; there are benefits and rewards for the company as well as the employees. The Total Recordable Case (TRC) rate has been cut nearly in half, reduced from 20.9 in 2006 to 10.8 in 2007. (TRC is the employer's incidence rate of recordable injuries and illnesses during the calendar year.) As of November 2008, there have been only three recordable injuries this year. Ade-Wifco's Days Away, Restricted or Transferred (DART) rate plummeted from 11.9 in 2006 to 4.0 in 2007. (The DART rate is the employer's injury and illness incidence of recordable cases involving days away from work and days of restricted work activity or job transfer.)
From May 2005 through December 2007, Ade-Wifco Steel Products, Inc. corrected 242 hazards. In a two-year period, the company totally changed its culture through employee involvement, dedication and a strong commitment to safety, thereby significantly increasing the likelihood that every employee returns home safely every night to their families.
There have been financial rewards for Ade-Wifco Steel Products, Inc. The amount a company pays for workers' compensation insurance is a variable rate determined each year by the insurance carrier based on that company's past three years of safety and health data compared to the industry's average. Today, Ade-Wifco enjoys an experience modifier of 0.93 which is indicative of their strong, impressive safety and health record; this translates into a 7% reduction for their workers' compensation insurance than the average company in the same industry would pay. In 2007, the company paid $31,325 in workers' compensation claims; as of November 2008, there were no claims paid.
An employee summed up the changes made at Ade-Wifco with - "I've worked here for years, under the old ownership and the new. The difference in safety and health around here is like night and day."