Paper Roll Loading, including insertion of core shaft/spindle and positioning of roll
Company: AF&PA member company
Industry: Generally applicable to NAICS Code 32212 (paper manufacturing), NAICS Code 3222 (paper converting) and NAICS Code 321219 (oriented strandboard manufacturing). A NAICS Code 321219 site was the source of this success story.
Task: Paper Roll Loading, including insertion of core shaft/spindle and positioning of roll
Employees: 213 (number at the site)
Success Brief:
We were able to effectively eliminate manual material handling activities associated with paper and paper roll shaft handling through the appropriate selection and installation of mechanized equipment.
The Problem:
We have introduced several new production processes into our manufacturing lines while converting our mill from producing standard Oriented Strandboard (OSB) product to producing OSB based siding product. Most notable among the process changes was the paper overlay process that is fundamental to the production of this specialized product. The process requires positioning a 3,800 pound roll of paper, installing a 260 pound, 130 inch roll shaft in the roll, and utilizing an overhead hoist to position the roll with inserted shaft into the production process. This task is repeated 24 times per day. The initial process was to position the rolls horizontally onto locally fabricated carts with a forklift. Two people manually inserted the 260 pound shaft, installed the bungs (end pieces) and manually pushed the cart beneath the overhead hoist. The ergonomic challenge was to provide a method for safely performing this task by reducing the required manual lifting, pushing and pulling forces.
The Solution:
We developed a two-fold solution to address the potential hazards posed by this task. First we procured a heavy duty, motorized "cart-caddy" capable of safely moving the assembled paper roll and made slight modifications to the cart. This eliminated the manual task of moving and positioning the paper roll. To eliminate manual shaft handling, we sought to design or procure a device capable of lifting the 260 pound shaft by the end and inserting into the paper roll. Our plant engineer identified an existing machine with an agile, articulating arm designed to handle this type of task. We worked with the manufacturer of this device to custom design a pneumatically actuated clasp with built-in safety devices that safely lifts and positions the shaft.
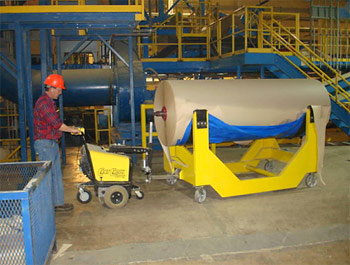
Cart Caddy maneuvering roll assembly
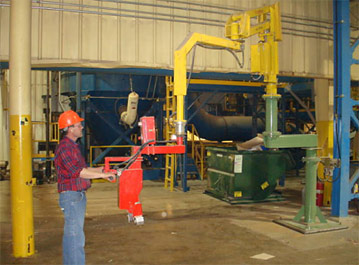
Pneumatic arm (shaft)
The Impact:
We eliminated a manually intensive procedure and created a safe and reliable process that any of our employees can perform repeatedly without risk of acute or chronic injury due to over-exertion from lifting, pushing and pulling tasks. The changes resulted in higher employee morale, reduced levels of biomechanical stress, and improved work flow and demonstrated our commitment to reducing the risk of workplace injuries.
Source:
- AF&PA; PPSA (July 2007)