Plastic Strap Spool Assembly
Company: AF&PA member company
Industry: Converting Plant - NAICS Code 322299
Task: Plastic Strap Spool Assembly
Employees: 100 (number at the site)
Success Brief:
A converting facility built and installed strapper spool stands to facilitate assembly of plastic strap spools at waist level reducing potential for back strains.
The Problem:
Plastic strapping spools used on strapping machines are sandwiched between a front and back plates that act as a guide when feeding the strapping material into the machine. When the spool is empty the unit is removed from the machine, the top plate and empty spool are removed, and a new spool is set in place. The top plate is replaced on the spool and the assembly reinstalled on the machine. Prior to this intervention, employees had to bend over or squat to work at floor level. The bottom plate had to be held in place to prevent it from turning while a tool was used to remove the top plate. Risk factors included bending/squatting and use of hand force to hold the bottom plate.
The Solution:
Strapper roll stands were built and installed so the strap spools could be assembled at about waist height. The raised rib on the stand keeps the bottom plate from turning while the tool is used to remove the top side-panel.
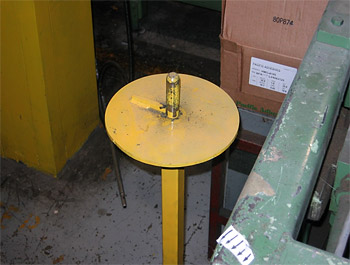
Figure 1: Strapper roll stand
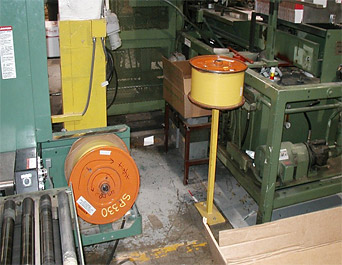
Figure 2: Spool assembly installed on machine
The Impact
The benefit of the strapper roll stands is twofold:
- Employees don't have to bend over or squat to assemble the strap spools, thereby reducing the force placed on the low back and knees.
- Hand force does not need to be exerted to hold the bottom plate in place while the top plate is removed.
Source:
- AF&PA; PPSA (May 2008).