Clearing Product Jams
Company: AF&PA member company
Industry: I-Joist (wood truss) Plant – NAICS Code 321214
Employees: 113 (number at the site)
Task: Clearing Product Jams
Success Brief:
A manufacturer of I-Joists improved access to products on a conveyor by replacing area guarding with point of operation guarding, and installing an access platform along the entire length of a lumber conveying system. This change allowed manual tasks to be performed at waist height rather than above shoulder height and reduced the potential for musculoskeletal injuries of the shoulder, lower back and neck. In addition the risk of pinching and physical contact injuries were reduced.
The Problem:
This conveying system transports 48 foot and 60 foot long runs of grooved, finger-jointed, flange board of various dimensions (2" x 3", 2" x 4", 2" X 6") to an automated assembly area. Here the flange board is joined with oriented strand board (OSB) to produce I-Joists used as structural members in residential and commercial construction. The conveying system experiences occasional product jams which must be manually corrected. Access to the conveying system had been limited by the presence of perimeter guarding (a fence enclosure similar to the yellow expanded metal panel shown in Figure 1) and the absence of a permanent platform to access the bed of the conveying system. Workers typically stood on the factory floor, reached upward to levels at or above shoulder height, and used an overhand grip to lift and reposition these long pieces of lumber when clearing product jams from the conveyor which stood approximately 41/2 feet above the floor. This task exposed the workers to an increased risk of the more common types of physical injuries such as pinching between pieces of product, and contact stress from leaning against the hard edges of the conveyor. In addition there was increased risk of musculoskeletal injuries of the shoulder, lower back and neck due to the extended reaching and twisting in combination with the physical force required to lift product while performing the task.
The Solution:
Access and assumed body postures were improved by:
- Replacing Area (perimeter) guarding with point of operation guarding.
- Installing a platform along the length of the conveyor which allows the worker to perform the task at about waist height.
Both improvements provided the workers with better (safer and more efficient) access to the machinery and product, and eliminated the need to work at or above shoulder height when performing jam clearing tasks, or other maintenance and servicing activities.
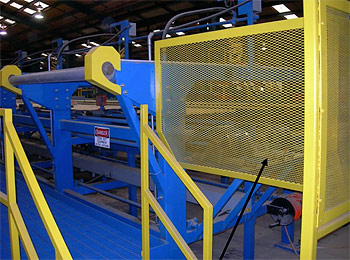
Figure 1: The local area guarding had extended the length of the machine (see arrow pointing to current local area guarding). Platform did not exist. Figure 2: Point of operation guarding put in place, allowing the removal of the perimeter guarding.
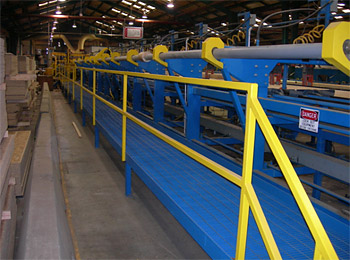
Figure 2: Point of operation guarding put in place, allowing the removal of the perimeter guarding.
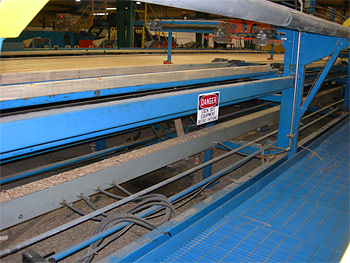
Figure 3: Platform installed to allow worker to stand alongside product at waist height, eliminating at or above shoulder movements.
The Impact:
These changes have significantly reduced the risk of injury, particularly upper body injury, to workers clearing jams and to maintenance personnel performing maintenance work in this area. In addition, this enhanced access has significantly improved the efficiency of maintenance and servicing work performed in this area, and the efficiency of this operation.
Source:
- AF&PA; PPSA (May 2008).