ALMACO Achieves SHARP Recognition and Improves Bottom Line after Implementing Protective Measures Identified by Iowa Consultation Team
Company: ALMACO
Location: Nevada, Iowa
Employees: 180 Workers
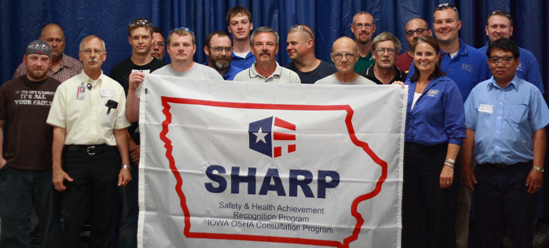
Success Brief:
Prior to working with the Iowa Bureau of Consultation and Education (Iowa Consultation), ALMACO's injury and illness rate was over 3 times the national average for companies in their industry. By 2010, approximately 10 years after initiating a relationship with Iowa Consultation, ALMACO had lowered its incident rate to less than half the industry average.
By correcting hazards identified by Iowa Consultation, and by developing and implementing a safety management program, ALMACO was able to significantly improve protection for its employees, lower their workers' compensation insurance rates, improve their bottom line, expand their business, and enhance the company's culture. ALMACO was approved by OSHA for participation in the On-site Consultation Program's Safety and Health Achievement Recognition Program (SHARP) in July 2010. SHARP recognizes employers who operate exemplary safety and health management systems.
Company Description:
ALMACO is a family-run enterprise located in Nevada, Iowa. The company manufactures agricultural research equipment used in the development of improved hybrids and varieties throughout the world. Specifically, the company produces planting, harvesting, and data collection equipment designed for performing seed research functions. ALMACO (SIC 3523, NAICS 333111) was founded in 1888, and is the oldest business in Story County, Iowa.
The Situation:
In 2001, ALMACO's injury and illness rate was almost 30, as compared to the industry's 2001 average injury and illness rate of 9.6, according to information from the Bureau of Labor Statistics. The management of ALMACO realized that something had to be done. That year, the company received a targeted direct mail flyer from Iowa Consultation regarding the free on-site consultation services available to small businesses, like ALMACO, which operate in high hazard industries. After some internal discussions, the company decided to contact Iowa Consultation to see if they could help the company lower its injury and illness rates. ALMACO's Vice President of Manufacturing, John Sturtevant made the call to ask Iowa Consultation to conduct a comprehensive visit of the plant.
The Solution:
After their initial visit in 2003 from Iowa Consultation, ALMACO worked with the Iowa consultants to address numerous hazards. ALMACO started with correcting the serious hazards identified by Iowa Consultation, such as fall hazards, unprotected machinery, and electrical hazards. The company reduced fall hazards by purchasing better equipment and installing railings; increased the mandatory use of personal protective equipment; and initiated efforts to improve the enforcement of all of their safety policies. ALMACO also made design modifications to their products to allow for safer assembly, reduced the amount of grinding they do by hand by purchasing automated equipment, and nearly eliminated utility knives by finding safer tools or changing processes. In addition, ALMACO addressed ergonomic issues and reduced sprains and strains by purchasing lifting equipment and improved safety and housekeeping by adopting a "5S" philosophy, which focuses on having visual order, organization, cleanliness and standardization.
ALMACO has continued to work with Iowa Consultation. For example, ALMACO has improved their emergency lighting, energy control program, and ergonomics with the help and input from Iowa Consultation. ALMACO also has increased employee involvement in many aspects of the company's safety program, including participation on the Injury Prevention Team, bi-weekly safety training and attending daily stretching exercises. By 2009, the company decided it would pursue SHARP recognition. According to Mark Smith, ALMACO Director of Manufacturing, "[w]e pursued SHARP status so that we could benchmark the best companies in terms of safety management and to hold ourselves to the high standards that SHARP recognition requires."
The Impact:
By 2006, after working with Iowa Consultation, ALMACO's injury and illness rate had dropped below the national average. In 2006, its Total Recordable Case (TRC) rate was 6.46 and its Days Away, Restricted, and/or Transferred (DART) rate was 4.1. In comparison, according to 2006 data from the Bureau of Labor Statistics (BLS), TRC and DART rates for the industry averaged 9.3 and 4.8 respectively. By 2010, the worksite's rates dropped further to 3.38 and 0.56 respectively. What makes these improvements even more impressive is that they occurred at a time when the company was increasing their workforce by 157%. According to Iowa Consultation, ALMACO's efforts to develop and implement effective training and safety and health management programs were crucial to this success.
In addition to the positive impact these improvements have made in the lives of ALMACO workers, the company also has experienced financial benefits that have resulted in increased revenues and profits. Since 2005, ALMACO has experienced a 37% reduction in its workers compensation insurance modification rate, and a 79% reduction in its employee turnover rate. In 2010, workers compensation premiums dropped from approximately $262,000 in 2009 to $218,000. According to Mark Smith, these improvements were made possible because the company dedicated themselves to identifying and correcting hazards in their workplace with guidance from Iowa Consultation. In July 2010, OSHA approved ALMACO for participation in SHARP.
According to Mr. Smith, "the company has effectively transformed itself to be safety-oriented and has realized financial rewards in the process." However, as emphasized by Christian Clem, President of Operations at ALMACO, "It's not about dollars and cents; it's about people's lives. It's about showing up for work in the morning and going home at the end of the day in the exact same status, and that's not just lip service for us - we take it to heart, and we're really serious about it." Recognizing the positive impact OSHA Consultation has had on his company, Clem challenges the employees at ALMACO to "maintain our SHARP status for the rest of our careers, and for the next generation."
Source:
Mark Smith, Director of Manufacturing, ALMACO