Anthony Forest Products Saves Over 75% on Workers' Compensation Insurance Premium
Company: Anthony Forest Products Company
Location: Atlanta, Texas
Employees: 275 Workers Company-wide
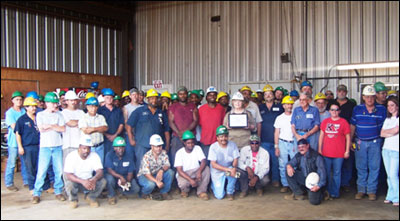
Success Brief:
Since Anthony Forest Products began working with the Texas Occupational Safety and Health Consultation Program (OSHCON) in 1991, the company has improved its safety and health management program and lowered its Workers' Compensation insurance premium by almost 75% company-wide.
Company Description:
Anthony Forest Products Company, a family-run enterprise founded in 1916, specializes in integrated forest products. The company, headquartered in El Dorado, Arkansas, operates southern pine lumber producing sawmills in Urbana, Arkansas and Atlanta, Texas (NAICS 321113); wood chip mills in Plain Dealing, Louisiana and Troup, Texas (NAICS 113310); and engineered wood laminating plants in El Dorado, Arkansas and Washington, Georgia (NAICS 321213). The company also operates a joint venture I-Joist plant, Anthony-Eacom, Inc., in Sault Ste. Marie, Ontario, Canada.
The Situation:
In 1990, Anthony Forest Products' workers' compensation insurance premium was approaching $1 million. In an effort to reduce workplace injuries and lower the company's workers' compensation premium, Lynda Anthony, Vice President of Human Resources, Safety and Environment Division, instituted a company-wide safety and health management program.
Ms. Anthony stated that after a period of success, "the company hit a brick wall and safety was at a standstill." She knew that the only way to transform the safety and health culture of the company was to get help from an outside source. In 1991, while attending a safety-training course at the National Safety Council, Ms. Anthony learned that the OSHA On-site Consultation Program works with small business employers to identify safety and health hazards and lower workplace injuries, illnesses, and fatalities. With this information in mind, she contacted OSHCON to request a site visit at the company's southern pine lumber producing mill in Atlanta, Texas.
The Solution:
In June 1991, an OSHCON consultant conducted a walk through of the Anthony Forest Products sawmill in Atlanta, Texas. The consultant clarified OSHA regulatory requirements, identified potential hazards, provided correction assistance, and aided the company in the development of written safety and health policies. The company's machine guarding protocols, lockout/tag out procedures, and personal protective equipment requirements were also reviewed. While working with the consultant to identify the adequacies and deficiencies of its safety and health policies, the company recognized a need for improved management/worker communications. To keep workers informed of safety and health activities and conditions, bimonthly meetings between workers and supervisors were established.
After completing a walk through of the facility, the consultant held a closing conference with the company manager to review established correction due dates for identified hazards and recommendations for improving the safety and health management system. During the closing conference, the consultant also told the company about OSHA's Safety and Health Achievement Recognition Program (SHARP). SHARP is designed to support small employers that implement and continuously improve effective safety and health management systems at their worksite.
Once Anthony Forest Products implemented all of the consultant's recommendations at the Atlanta, Texas sawmill, it instituted a new, company-wide safety and health management program. The company then set a goal to attain SHARP certification at each of its six facilities. In 1998, the Atlanta, Texas sawmill became the first worksite in the company to achieve SHARP status. Shortly after receiving the certification, the company began pursing SHARP recognition for its five other facilities. The wood chip mill in Troup, Texas achieved SHARP in 1999. Two years later, the mill in Plain Dealing, Louisiana became the third SHARP certified facility. In 2002, the wood laminating plant in El Dorado, Arkansas achieved SHARP status. The Urbana, Arkansas lumber sawmill achieved SHARP status in 2004; and the laminating plant in Washington, Georgia achieved status SHARP in 2007.
The Impact:
In 2000, the Total Recordable Case Rate (TRCR) at the Atlanta, Texas sawmill was 4.0 compared to the national average of the industry of 10.7 and the site's Days Away, Restricted and Transferred (DART) rate was 2.0 compared to the national average for the industry of 3.3. In 2008, after achieving the SHARP designation at all six of its facilities, the site's TRCR was 2.1 compared to the national average for the industry of 4.7 and its DART was zero compared to the national average of the industry of 2.2.
As a result of working with the On-site Consultation Program, the company as a whole has saved hundreds of thousands of dollars per year in workers' compensation insurance premiums. In 1989, prior to working with the Texas OSHCON Program, the company's Workers' Compensation Experience Modifier Rate (EMR) was over 1.0 and the workers' compensation annual insurance premium was approaching $1 million. In 2010, with six SHARP facilities, the company's EMR is 0.56 and the workers' compensation insurance premium is currently $125,000. The company's workers' compensation premium has decreased more than 75% since it began working with the Texas OSHCON Program in 1991. The investment in worker safety and health has had a large impact on the company's bottom line, but the real bottom line is that workers are less likely to suffer a workplace injury.
Achieving SHARP certifications at all of its facilities has significantly affected the company's safety and health culture. According to Ms. Anthony, the shift in the safety and health culture and attitude at the company's facilities has improved worker moral, enhanced productivity, and improved the quality of the company's products. In addition, the company's personnel turnover rate has significantly decreased.
Anthony Forest Products believes that the safety and health management program that it developed with the On-site Consultation Program has provided the company with a competitive business advantage. According to Ms. Anthony, the company views worker safety and health as the key indicator of its organizational excellence and believes that its SHARP certified facilities will remain competitive within the integrated forest products industry. Ms. Anthony also stated that the company's SHARP certifications are indicative of its commitment to its workers, customers, peers, and the surrounding communities where the facilities are located.
Source:
Ms. Lynda Anthony, Vice President of Human Resources, Safety and Environment Division, Anthony Forest Products Company