Becker Iron and Metal Earns SHARP Recognition through Work with OSHA's On-site Consultation Program
Company: Becker Iron and Metal, Inc.
Location: Venice, Illinois
Employees: 45
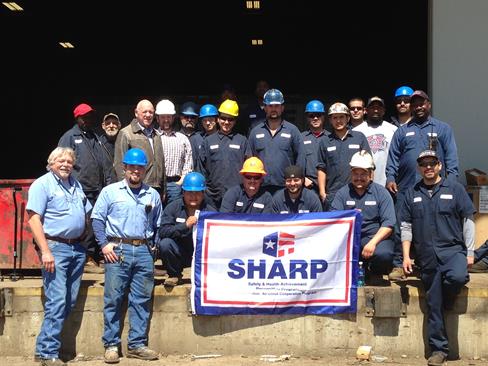
NAICS Code: NAICS 331210 – Metal Recycling
Company Description:
As buyers and processors of ferrous and nonferrous metals, Becker Iron and Metal, Inc., is a family owned, 4th generation company, servicing the scrap metal industry for over 100 years. From humble beginnings using a horse and cart at the turn of the 20th century, the company has come to be recognized as one of the leading scrap metal recyclers in and beyond the Midwest. Becker serves a diverse customer base, ranging from the largest industrial manufacturing plant to the smallest machine shop, from Fortune 500 companies to the individual.
The Situation:
In 2011, the company contacted the Illinois Department of Labor (IDOL), On-site Consultation Program, with the goal of improving their safety programs and using IDOL's safety and health experts to evaluate its policies and procedures without fear of repercussions. "To improve, it was important for us to know exactly where we stood and what we didn't know," said Becker Iron and Metal, Inc., Safety Manager, Lisa Dunn.
OSHA's On-site Consultation Program services are separate from enforcement and do not result in penalties or citations. This program offers free, confidential safety and health advice to small and medium-sized businesses in all states across the country and several territories, with priority given to high-hazard worksites. Consultants from state agencies or universities work with employers to identify workplace hazards, provide advice on compliance with OSHA standards, and assist in establishing injury and illness prevention programs.
The first on-site consultation visit was con-ducted in November 2011. Hazards noted during the consultant's walk-around included insufficient or non-existent safety and health programs for hearing conservation, respiratory protection, and personal protective equipment. Other hazards involved overexposure to metal fumes, damaged electrical cords, unmarked aisles, improper storage of compressed gas cylinders, forklift emitting high levels of carbon monoxide, and improper labeling of hazardous chemicals.
The Solution:
Electrical and improper equipment hazards were abated immediately during on-site consultation visits and/or taken out of service until proper equipment could be put in place. To eliminate amputation and electrical hazards, a new bailer was purchased for the warehouse. A new lockout/tagout program was implemented and subsequent training provided to the employees.
After the consultant conducted personal air monitoring for the workers, new equipment for cutting scrap to reduce exposures to metal fumes was purchased and a comprehensive respiratory protection program was implemented. Additionally, after personal noise monitoring was conducted, a fully compliant hearing conservation program was implemented.
While working with the IDOL consultants, Becker learned about OSHA's Safety and Health Recognition Program (SHARP). This program recognizes small employers who operate an exemplary safety and health management system. Becoming an OSHA-SHARP workplace was used as a goal to drive the overall development of the safety and health management system. Management took the opportunity, using SHARP requirements to identify the milestones needed to improve the overall safety and health management system, and gave the Safety Manager the authority and resources to ensure it was attainable.
Getting buy-in and contributions from everyone that is impacted is an essential element of making significant changes in any organization successful. "We wanted to create a truly collaborative safety culture, explained Dunn, and while the owners always had an open door policy and were very attentive to any worker who brought anything to their attention, there was not a sense of community." Creating an environment where workers felt safe to report concerns proved to be a challenge. Becker endeavored to make reporting near-miss accidents and potential hazards the corner-stone for improving overall safety and health performance. Overcoming employee reluctance to do so was a major hurdle. Employees were afraid that in certain instances reporting near-miss accidents, incidents, or other safety concerns might compromise their welfare or that of their co-workers. Changing this culture of employee fear involved completely eliminating the employee's perception of possible discipline when reporting near-misses, potential accident situations, and any other workplace safety and health concerns.
By involving all levels of the company, the safety program has grown from one of rules and procedures to one of a collaborative safety culture. Becker focused on the goal of becoming a SHARP company by establishing, maintaining, and continually improving the following:
- Near accident reporting (encouraging employees to identify situations, procedures, processes that have the potential for injury and/or illness);
- Incident investigation (educating management to differentiate between accident symptoms and the causes);
- Housekeeping (involving workers to establish specific criteria for each area of the operation);
- Environmental monitoring (establishing employee baseline noise and air quality readings for welding and cutting operations);
- Job Hazard Analysis (evaluating all newly established and/or modified procedures);
- Inspections (developing a comprehensive walk-around safety checklist);
- Management training (having all management personnel attend the OSHA 10-hour and specific safety/health training provided by the Institute of Scrap Recycling Industries);
- Ergonomics (providing adjustable table heights for copper stripping process and educating office employees);
- Enforcement procedures established (implementing strict enforcement of energy control procedures);
- Preventative maintenance (establishing a protocol for routine machinery and equipment servicing and repair);
The Impact:
The hard work paid off. The company implemented a comprehensive safety and health management system, experienced a positive safety culture change, and lowered the injury and illness rates. In 2010, they reported a Total Recordable Case Rate (TRC) of 2.3, and the Days Away, Restricted, and/or Transfer Rate (DART) was also 2.3. In 2011, the TRC was 2.2 and the DART was 2.2. For comparison, the U.S. Bureau of Labor Statistics reported that in 2010 the industry average TRC was 8.0, and the average DART was 3.9; in 2011, these industry averages were 4.5 and 4.2 respectively. Since 2012, Becker's facility has had no recordable injuries. Becker experienced a 20% reduction in Experience Modifier Rate due to program changes, had no workers' compensation claims, and lowered its workers' compensation insurance premiums.
Becker's dedication to protecting workers was further rewarded in 2014 when they were accepted into SHARP. Acceptance of a company into SHARP is an achievement of status that singles out the company among its business peers as a model for worksite safety and health.
"The increase in employee involvement is a big success, said Dunn; I think the level of involvement speaks volumes. Employees are thinking about safety and not just about following rules. Suggestions are given frequently regarding performing processes safer and on other concerns as well. Management has been attentive and active in addressing any concerns and with following up on suggestions."
Sources:
Lisa Dunn, Safety Manager, Becker Iron and Metal Works, Venice, Illinois