CamGlass Continues SHARP Recognition For Tenth Year!
Company: Cameron Glass, Inc.
Location: Broken Arrow, Oklahoma
Employees: Approximately 115 full-time workers
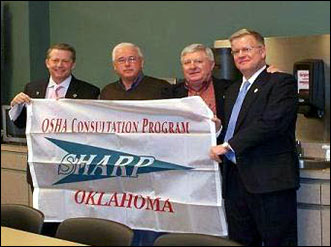
Success Brief:
Cameron Glass, Inc. (CamGlass) began operations in 1978 as a small business that manufactures fabricated glass products. The company began working with the Oklahoma On-site Consultation Program in 2000 and achieved Safety and Health Achievement Recognition Program (SHARP) certification in February 2002. As a result of continuous improvement, the site was reapproved to SHARP in November 2003, January 2004, March 2006, June 2008, and February 2011. Since CamGlass had its initial consultation visit in 2000, the site has reduced its injuries and illness rate by 82%. In addition, by maintaining SHARP, CamGlass has increased employee involvement in the development of organizational objectives and goals which has led to a closer working relationship between management and plant employees at the site.
Company Description:
CamGlass, a prototyping and fabrication company of glass products for automotive, agricultural and construction equipment (NAICS 327215), located in Broken Arrow, Oklahoma has approximately 115 employees. CamGlass serves the construction, agricultural, and forestry industries. The glass is used in the cabs of road graders, back hoes, dozers, skid steers, farm and logging equipment.
The Situation:
In the late 1990’s CamGlass was experiencing frequent workplace accidents which resulted in increased workers compensation insurance costs. CamGlass knew the company’s safety and health program needed improvement to help protect employees’ health and safety.
The Solution:
CamGlass contacted OSHA and talked with an OSHA safety compliance officer about the company’s interest in improving its safety and health program. After several discussions, the compliance officer recommended the company contact the OSHA Onsite Consultation Program in Oklahoma. As a result, in 2000 CamGlass contacted the Oklahoma Labor Department’s On-site Consultation Program and scheduled a meeting with a consultant to discuss the company’s safety program and interest in improving employee health and safety at the facility.
During the on-site consultation visit walkthrough, the consultants identified multiple high hazards that needed correction. The following hazards were noted: several machines needed additional guarding, pinch points on machinery needed to be eliminated, slip and water hazards, broken electrical outlets, loose electrical connection, and excessive noise levels which required hearing protection.
Based on the feedback, the Oklahoma consultation team worked with CamGlass to correct all identified safety and health hazards and to improve elements of the safety and health management programs. As a result of the visit, the consultants also recommended CamGlass increase employee involvement in the safety and health culture in the organization by providing training awareness programs. In April 2002, the Executive Management of CamGlass implemented a comprehensive safety and health program. Mr. Skotarek, Cameron’s Safety Manager, stated that the company desired to initiate an exemplary safety and health program that offered immediate and long-term prevention of job-related injuries. In addition, according to Mr. Skotarek, the implementation of the safety and health program was part of the company’s preparation to qualify for recognition in the Safety and Health Achievement Recognition Program (SHARP). Mr. Skotarek stated, "The goal was to create and maintain the best possible safety and health worksite environment for all employees."
In February, 2002, CamGlass had greatly improved safety and health awareness and was approved for SHARP certification.
Since the site’s initial approval into SHARP, CamGlass’ management and employees developed strategies to prioritize a systematic reduction of incidents. For example, the site holds "Tool Box" meeting with employees to communicate and review incidents for awareness training. Management and employees also conduct individual workplace hazard assessments. In addition, root cause investigations of accidents are conducted with corrective and preventive actions and recommendations are communicated to management, supervisors, and employees.
CamGlass achieved SHARP recertification in November 2003, January 2004, March 2006, and June 2008. In February 2011, CamGlass celebrated ten years of SHARP achievement when it received re-certification for SHARP participation from the Oklahoma On-site Consultation Program.
The Impact:
According to Mr. Skotarek, the site’s strategic integration of SHARP’s criteria including management’s commitment to implementing an exemplary safety system and empowering employees to actively shape the safety program has been the key to reducing workplace injuries and illness at the site. Furthermore, Mr. Skotarek added that the reduction in injuries and illnesses at the site has significantly reduced the lost claim losses (both short and long term).
Since 2007, CamGlass has seen a reduction in its experience modifier rate (EMR). By the end of 2010, the site had an EMR of .87, a decline from the 2008 EMR of 1.15. In addition, over the last three years, the company’s workers compensation insurance premium was reduced by 26% and in the last ten years by 38%. According to Mr. Skotarek, "It takes a significant commitment at all levels in an organization to pursue and achieve SHARP certification, but the Program works and the benefits to workplace safety and health are certainly worth it. I would highly recommend the Oklahoma On-site Consultation Program to other employers interested in improving workplace safety and health."
Source:
Mr. Alex Skotarek, Quality and Safety Manager, Cameron Glass, Inc.