DeCrescente Distributing Company Earns 5th SHARP Renewal
Company: DeCrescente Distributing, Inc.
Location: Mechanicville, New York
NAICS Code: 424810, Beer, wine, and distilled alcoholic beverage merchant wholesalers
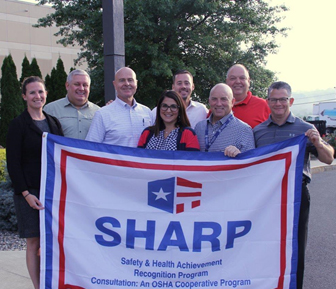
DeCrescente Distributing Company (DDC) is a fourth-generation beverage distributor, family-owned and operated since 1948. Customers include supermarkets, bars, restaurants, convenience stores, and private businesses.
The OSHA On-Site Consultation Program offers no-cost and confidential occupational safety and health services to small- and medium-sized businesses in all 50 states, the District of Columbia, and several U.S. territories, with priority given to high-hazard worksites. On-Site Consultation services are separate from enforcement and do not result in penalties or citations. Consultants from state agencies (such as the New York Department of Labor, Division of Safety and Health (NYS/DOSH) or universities work with employers to identify workplace hazards, provide advice on compliance with OSHA standards, and assist in establishing injury and illness prevention programs.
Experiencing a higher than average injury rate prompted DDC to contact NYS/DOSH for help in improving their safety performance. "We needed to work on changing behavior and creating a safety culture at DeCrescente," said Ray Cordani, DDC Safety and Loss Control Manager.
In 2006, during the first consultation visit walkthrough of DDC's facilities, the consultants identified hazards, such as frayed electrical extension cords, blocked egress doors, machine guarding, and air compressor defects. These hazards were immediately corrected. To prevent recurrence of these hazards, a new inspection process was instituted which required employees to check equipment on a regular basis and to report defects for prompt corrections. Employees were also given the authority to shut down operations, if necessary, to prevent exposure to serious hazards.
Additionally, a safety committee, comprised of employees representing all departments (warehouse, drivers, operations, merchandising, sales, and human resources), was created after the first consultation. This committee meets monthly to discuss safety-related issues and to review all incidents, injuries, and near-miss investigations. In addition to establishing a safety committee, employee training was enhanced to include new employee orientation, on-the-job training, and monthly safety refresher training.
After taking these steps toward improving their safety and health management system, "we started noticing an attitude change in employee behavior," said Cordani. Employees began to realize that they play an integral part in maintaining a safe and healthy workplace. DeCrescente experienced a significant shift in safety behavior by their employees, which led to a "safety culture" never seen before. The success of the program, which continues today, has resulted in a workplace injury rate that is significantly less than the national average for this industry. "Our workers compensation costs have also been greatly reduced," noted Cordani. "We continue to be a role model for companies in our industry."
From 2013 through 2016, DCC's average recordable case (TRC) rate was 3.3, and their average days away from work, job restriction or transfer (DART) rate was 2.9. Their TRC and DART rates for this period were significantly below the Bureau of Labor Statistics industry average TRC and DART for these years. The industry average TRC rate was 6.38, and the industry average DART rate was 4.58. [Note: In 2017, the company's TRC rate was 3.3, and their DART rate was 3.3. However, 2016 is the most recent year these BLS data are available.]
DeCrescente was awarded their first OSHA Safety and Health Achievement Recognition Program (SHARP) certificate in 2006, and they have maintained this recognition throughout the years, with the last renewal in September 2017. SHARP recognizes small business employers who have used OSHA On-Site Consultation Program services and operate exemplary safety and health programs. A business accepted into SHARP by OSHA is identified as a model for worksite safety and health.
Since becoming a SHARP site, the company has enhanced safety and health opportunities for employees and invested in new equipment. Some of these enhancements included creating a medically staffed wellness and fitness center on-site for employees and family members to use, free of charge; installing "Cell Control" systems on all company vehicles; improving driver training; and hosting an "Active Shooter" drill with local law enforcement at their facility.
"Working with the New York State On-Site Consultation Service, the company has discovered that Federal OSHA not only enforces regulations, but also funds programs that help employers to establish and maintain a safe and healthy workplace," said Cordani.
To locate the OSHA On-Site Consultation program nearest you, call 1-800-321-OSHA (6742) or visit www.osha.gov/consultation.
Source: Ray Cordani, Safety and Loss Control Manager