Edstrom Industries, Inc. Reduces Injury and Illness Rates and Earns Its Fifth SHARP Renewal
Company: Edstrom Industries, Inc..
Location: Waterford, Wisconsin
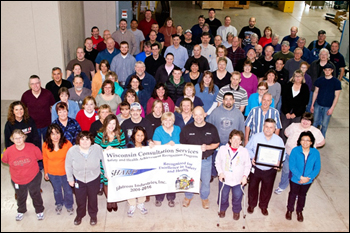
NAICS Code: NAICS 339999, Manufacturing
Company Description:
Edstrom Industries, Inc., is a family-owned company that designs and manufactures automated animal drinking water systems; water purification, access control, light control, and environmental monitoring products; and vivarium management software.
The Situation:
Because of his passion for safety and concern for the well-being of his employees, the company's founder, Bill Edstrom, Sr., reached out to the University of Wisconsin-Madison (UW-Madison), Wisconsin State Laboratory of Hygiene, in December 1986 to request help improving workplace safety and health policies and procedures at his business. UW-Madison administers the U.S. Occupational Safety and Health Administration (OSHA), On-site Consultation Program in Wisconsin, known as WisCon. OSHA's On-site Consultation Program offers free, confidential advice to small and medium-sized businesses in all states across the country, with priority given to high-hazard worksites. On-site Consultation services are separate from enforcement and do not result in penalties or citations. This voluntary program's primary goal is to identify workplace hazards, provide advice on complying with OSHA standards, and assist in establishing injury and illness prevention programs.
The first on-site consultation visit was conducted in 1987, and the consultant identified an improperly guarded brake press during a walkthrough of the Fabrication Department and foam-packaging operation. Since that first visit, Edstrom has worked closely with WisCon and invited OSHA Consultation back several times to conduct additional on-site visits and to advise on changes with potential impacts on worker safety. Consultants have identified and helped Edstrom abate acid mist, air quality, hexavalent chromium, diisocyanate exposure, surface lead dust, ultrasonic noise, animal handling sensitization, machine guarding, electrical, and other hazards.
The Solution:
A new brake press was purchased to replace the one with defective guards, and the company went a step further. Based on hazards and areas for improvement identified during OSHA on-site consultation visits, Edstrom established a working relationship with Rockford Systems, LLC, a company with over 42 years of experience in industrial machine safeguarding, to evaluate the equipment on its manufacturing floor, ensure that equipment is properly guarded, and put appropriate signage in place. After 18 months, Edstrom had updated the entire facility using the recommendations on machine guarding and signage. Special focus was placed on updating Lockout/TagOut, and a program was implemented to label equipment with proper Lockout/Tagout procedures. These labels are accompanied by corresponding pictures.
Housekeeping procedures play a key role in ensuring that employees have a safety and healthful workplace. Recently, to address a concern about the levels of surface lead exposure in the Electronics Department, a consultant from WisCon collected several samples and sent them to the Wisconsin Occupational Health Laboratory (WOHL) for testing. "We were surprised to learn that a few of the samples yielded high levels of surface lead," said Tom Clark, Vice President of Operations. "Through OSHA's education, we have now heightened our surface cleaning schedule to be a daily event, and we replaced all of the old solder mats with new mats."
Several safety and health processes have been implemented, improved, or both. Now, all Safety Committee members obtain OSHA 10-Hour Certifications. Annual safety training is conducted for all employees. Safety Hazard Forms are available throughout the plant for employees to use in reporting any safety concerns directly to the Safety Committee. A more formalized accident investigation process includes worker involvement with any corrective actions being taken. Stretching programs help reduce repetitive motion issues. In addition, each year, four volunteers from the production floor are solicited to participate on the Safety Committee.
To keep its employees aware of the importance of safety and health in the workplace, Edstrom conducts regular "Tool Box Talks." The production supervisors hold stand-up meetings with their team to review Safety Committee Meeting Minutes, reinforce training, and explain workplace safety and health policy and procedure changes. These meetings involve an open discussion format to promote give and take, and everyone is encouraged to provide input on any and all safety concerns.
The Impact:
On November 12, 2004, Edstrom's dedication to protecting workers was rewarded. They became the second company in the state of Wisconsin to be accepted into OSHA's Safety and Health Achievement Recognition Program (SHARP). Acceptance into SHARP is an attainment of status that singles out the company among its business peers as a model for worksite safety and health. The company has continually maintained this standing, earning their fifth SHARP recertification in 2013.
Edstrom's injury and illness rates dropped from nine in 2011, to six in 2012, and to two in 2013. Days Away, Restricted, and/or Transfer rates went from 0.46 in 2011 to zero in 2012 and remained at zero in 2013. According to the U.S. Bureau of Labor Statistics, the national average DART rates in this industry were 2.5 in 2011 and 1.4 in 2012, the most recent years these data are available.
"These accomplishments would not have been possible without the commitment of the Edstrom management team as well as the passion and dedication our employees have to making Edstrom a safe place to work," said Clark. "Through training, communication, and employee involvement, our employees are able to recognize and report hazards at their onset so that immediate corrective action can be taken. We've seen a direct correlation between our effective safety program and the resources we receive from the OSHA On-site Consultation Program which has resulted in an engaged safety culture."
Source:
Tom Clark, Vice President, Operations, Edstrom Industries, Inc.