EE Technologies, Inc. Works with Nevada's Safety and Consultation Training Section to Improve its Safety and Health Management System and Receives SHARP Recognition
Company: EE Technologies, Inc. - Reno
Location: Reno, Nevada
Employees: 180 employees
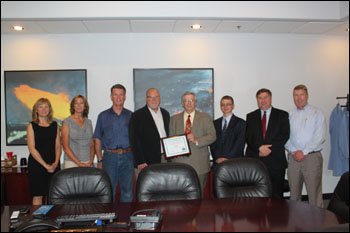
NAICS Code: NAICS 334418 - Printed Circuit Assembly (Electronic Assembly) Manufacturing
Success Brief:
During a Nevada Division of Industrial Relations, Occupational Safety and Health Administration Program inspection, the inspector recommended that EE Technologies, Inc., (EET) consider participating in OSHA's On-site Consultation Program, Safety and Health Achievement Recognition Program (SHARP). Acting on that recommendation, the company made improvements to its safety and health program that were required for SHARP participation.
Company Description:
EE Technologies, Inc., is an electronic component manufacturer that provides a range of integrated services to original equipment manufacturers. The company specializes in full electronic and mechanical box build assembly services as well as circuit board assembly for a wide variety of industries, including automotive, medical, radio frequency/wireless, gaming, military, scientific educational, industrial and digital audio/video markets.
The Situation:
EET uses lead soldering as part of its manufacturing processes. During a programmed inspection as part of a National Emphasis Program on Lead, OSHA representatives told the company that the worksite would be a good candidate for OSHA's SHARP. Safety and Health Achievement Recognition Program recognizes small employers who operate exemplary safety and health management systems. Acceptance into SHARP is an achievement of status that singles out a company among its business peers as a model for worksite safety and health.
The Solution:
Recognizing that safety and health is an integral aspect of providing customer service to its partners, EET took the necessary steps to be eligible for participation in SHARP. Qualifying for the program requires implementing a comprehensive SHMS as well as maintaining injury and illness rates below the national average for the industry. Additionally, EET had to succeed in passing safety and health assessments conducted by Nevada's Safety and Consultation Training Section (SCATS) on a regular basis.
First, EET set the groundwork for the implementation of a safety and health management system by establishing a safety team comprised of supervisors and employees. EET also strengthened its incident investigation program. "We want to know what happened, why, and what actions and protections can be implemented to make a long term difference," said Laura Anderson, EET's Human Resources Supervisor.
Continuous improvement is a value embraced at EET, and it was the case with the company's SHMS. The safety team looked for ways to make the workplace better through regular safety committee meetings, inspections, training, and awareness programs. Feedback from workers, visitors, and state and local agencies were incorporated into EET's SHMS.
"We've already experienced increased communication about our safety program, and now we are talking about safety in a proactive positive way. Employees are proud to work for a company that cares about safety and makes it a priority. Not only has our communication and awareness of safety issues increased, we expect to see reductions in worker compensation insurance premiums and general liability premiums," said Elizabeth Duffrin, Chief Financial Officer.
One of the changes included moving electric drops to be close enough to the workstations to allow single cords to reach. EET trained its employees to be on alert to look for ways to be safer. Extreme care is taken to make sure aisles are clear; appropriate personal protective equipment, such as safety glasses, are worn; and areas around scissor lifts are clear before the equipment is used.
"It is fun to hear employees encouraging other each other when they catch a coworker doing something well and safe," said Rick Pink, Safety Manager. He also added that "[o]ur employees care about each other and demonstrate this concern with their attention to the workplace environment. For them, it is not about rules but about what makes sense. Seeing people take extra time to ensure the areas in front of eye wash machines and fire extinguishers are clear makes me proud."
Sources:
Laura Anderson, EE Technologies, Inc., Human Resources Supervisor
Elizabeth Duffrin, EE Technologies, Inc., Chief Financial Officer
Rick Pink, EE Technologies, Inc., Safety Manager