Gate Precast Company of Kissimmee Renews Safety Orientation and Receives SHARP Recognition
Company: Gate Precast Company
Location: Kissimmee, Florida
Employees: 200 Workers
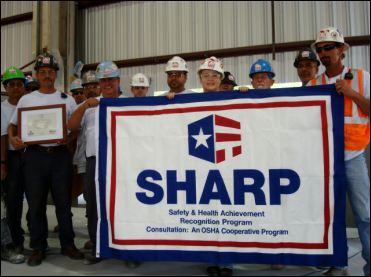
Success Brief:
In 2010, Gate Precast Company, located in Kissimmee, Florida, received a site specific targeting letter1 from the Occupational Safety and Health Administration (OSHA). An elevated incident rate in 2008 had predicated a letter from OSHA recommending the company request the free consultative services offered as part of OSHA's On-site Consultation program. Encouraged by the letter and also by the positive experience their sister plant in Jacksonville had after entering into a relationship with OSHA On-site Consultation in 2008, the management at Kissimmee were resolved to develop and maintain an exemplary safety and health management system. In 2011, one year after contacting OSHA On-site Consultation, the Gate Precast Company Kissimmee Plant, and three other sister plants, had succeeded in achieving recognition in OSHA's Safety and Health Achievement Recognition Program (SHARP).
Company Description:
Gate Precast Company (NAICS 327390, "Other Concrete Production Manufacturing"), headquartered in Jacksonville, FL, is Gate Petroleum's oldest non-petroleum division. The company operates eight manufacturing facilities located in North Carolina, Alabama, Kentucky, Tennessee, two in Florida and two in Texas. Gate Precast Company produces precast/prestressed concrete products for educational, military, institutional/medical, residential/hospitality facilities, parking garages and bridges throughout Florida. In 2001, Gate Precast acquired the plant at Kissimmee, which is situated on 60 acres and has an annual production capacity of over 900,000 square feet of architectural precast. Gate Precast Company's Kissimmee Plant handles design, production and installation of architectural precast projects throughout Florida with a wide range of colors, textures and forms.
The Situation:
In 2010, Gate Precast Company of Kissimmee ("Gate Precast") received a site specific targeting letter from OSHA as a result of the company's elevated Days Away, Restricted, and/or Transfer (DART) rate. DART measures the number of recordable injuries and illnesses per 100 full-time employees that resulted in days away from work, restricted work activity and/or job transfer. This incident rate is one of several tools used to assess the degree to which workers are exposed to hazards in a company or industry. In an industry whose average DART rate was 5.1 in 2008, Gate Precast had reported a rate of 7.8. OSHA's letter recommended the company contact OSHA's On-site Consultation program. This Federally funded program, which offers free and confidential advice to small and medium-sized businesses, is available to businesses in all U.S. states and territories. The University of South Florida (USF) administers the OSHA On-site Consultation in the "Sunshine State" through its program, "SafetyFlorida."
Gate Precast of Kissimmee already was aware of OSHA On-site Consultation. The management of Gate had recently established the goal of receiving SHARP recognition in all eight of its plants. Its Jacksonville plant had in recent years used OSHA's consultation services to address health and safety protection for its workers. In fact, Jacksonville, after initially contacting OSHA On-site Consultation in 2007, had done so well in its efforts to protect workers, that in 2009, the plant achieved recognition in OSHA's SHARP program. SHARP recognizes small employers who operate an exemplary safety and health management system. Acceptance of a company into SHARP is an achievement of status that singles out the company among its business peers as a model for worksite safety and health. Managers at the Kissimmee Plant were resolved to work with OSHA Consultation and aspired to achieve the same level of protection for its workers that the Jacksonville plant had attained.
During their first visit to the Kissimmee Plant, consultants from USF Safety Florida developed a list of potential hazards which needed attention. These included lack of non-potable water in an emergency shower; lack of training for personnel who would use portable fire extinguishers; use of chain slings that were not approved; lack of a process to inspect chain slings used in the plant; and two personnel who were designated as qualified to work on live electrical circuits/systems for testing (up to 480VAC) but who were not provided adequate personal protection equipment for this scope of work. Consultants also determined that the company did not have in place a periodic inspection process for control of hazardous energy (lockout/tagout program), and that workers not yet trained as "authorized personnel" were able to conduct work as "authorized personnel" within the scope of a lockout/tagout program.
The Solution:
The managers at Gate Precast wanted to take their safety and health program to a higher level at the Kissimmee plant. They wanted to greatly improve their knowledge regarding OSHA standards and standards interpretations, strengthen their safety and health programs, policies and procedures and find ways to better communicate this information to their employees and associates. According to Gate Precast Safety Manager, Mike Parker, managers and their employees were eager to work with OSHA Consultation to accomplish this goal. The company started by correcting all of the hazards identified and communicated by OSHA Consultation within the agreed-upon timeframe. Next, the company began to hold daily, instead of weekly, safety meetings. Everyone in the company—plant manager, vice president, steel shop/safety manager, supervisors, foremen/leads, and employees—became involved in the process of hazard recognition, communication and prevention. Morning toolbox talks became more focused, discussing specific situations such as near-misses or incidents from the previous day. Parker says, "These efforts have established a mindset where everyone takes a shared responsibility in safety. Employees are committed to watching each other's back to ensure we all go home in good shape at the end of the day."
The Impact:
The safety efforts are working.. In two years, Gate Precast has seen its Total Recordable Case (TRC) and DART rates each drop from 7.8 to 0.5. Furthermore, workers' compensation claims have dropped by 29 percent.. Parker acknowledges these are nice by-products that boost the company's bottom line, yet the biggest benefit is how employees know they work in a safe location, which helps employee retention and overall morale. "We take care of one another. We're all responsible for safety in this location," said Parker.
According Mike Parker, the company has increased the frequency of safety meetings it holds and also added safety as a metric to company performance measurements (in addition to quality and productivity), thus bringing safety to the forefront of the company. Furthermore, the Kissimmee plant's safety and health budget was increased by 35 percent in 2011, a signal management is a proponent of workplace safety. "We've always wanted to be safe," says Parker, "but what y'all (OSHA On-site Consultation) do, makes it possible. The consultants were very helpful and put safety in such a way that we could understand it ... I'd be willing to stand on a street corner with a sign; that's how strongly I feel about Consultation."
When a safety and health management system succeeds for a company at one of its worksites, it is not uncommon for it to be rolled out company-wide. Gate Precast Company experienced this with its Jacksonville plant when it embraced a more robust safety and health culture after meeting with OSHA On-site Consultation in 2007. By 2009 the plant had earned SHARP recognition. As of July 2011, three of the company's other facilities also have earned SHARP status—Gate's plants in Winchester, Kentucky, Ashland City, TN, and now the plant in Kissimmee, Florida.
Source:
Mike Parker, Safety Manager, Gate Precast Company, Kissimmee, FL
1 The Site Specific Targeting (SST) program is OSHA's main programmed inspection plan for non-construction workplaces that have 40 or more workers. This inspection plan is based on work-related injury and illness data collected from a survey of 80,000 larger establishments in selected high-hazard industries. The plan focuses on several variables such as the number of injury and illness cases and number of days a worker has to stay away from work, or the number of workers who received job transfers or work restrictions due to injury or illness. Establishments on the list are randomly selected for inspection.