Removal of Heavy Generator from Response Trailer
Company: OSHA – Directorate of Technical Support and Emergency Management, Salt Lake Technical Center
Industry: 921110
Task: Removing Heavy Generator from response trailer for storage
Employees: There were about 10 employees potentially affected by this intervention
Success Brief:
A heavy generator had to be removed from a response trailer. Development of a roll off device allowed a single employee to safely remove the generator while minimizing lifting in awkward postures.
The Problem:
OSHA has a response trailer designed for assistance after disasters such as hurricanes or fires. Reliable power is sometimes unavailable at incident sites so a large Honda generator (about 200 pounds) is transported as part of the response trailer's contents. To prevent theft, the generator is housed in a metal security locker located on the tongue of the trailer. The generator must be removed from the locker for maintenance and storage between responses. Removal required several employees to work in very awkward postures such as extreme reaches and deep torso bending. There was a concern that someone would sustain a back injury during this process. Additionally, the generator was not appropriately maintained because it was so difficult to get in and out of the locker.
The Solution:
A height adjustable cart was purchased for about $140. Four sections of used, light duty 10" roller conveyor was purchased for around $20. Two sections of roller conveyor were cut to size and bolted into the security locker. Two other sections of conveyor were bolted to the top of the adjustable height cart. The roller conveyor extended beyond the platform of the cart by about 8" to facilitate match up with the conveyor in the locker during transfer.
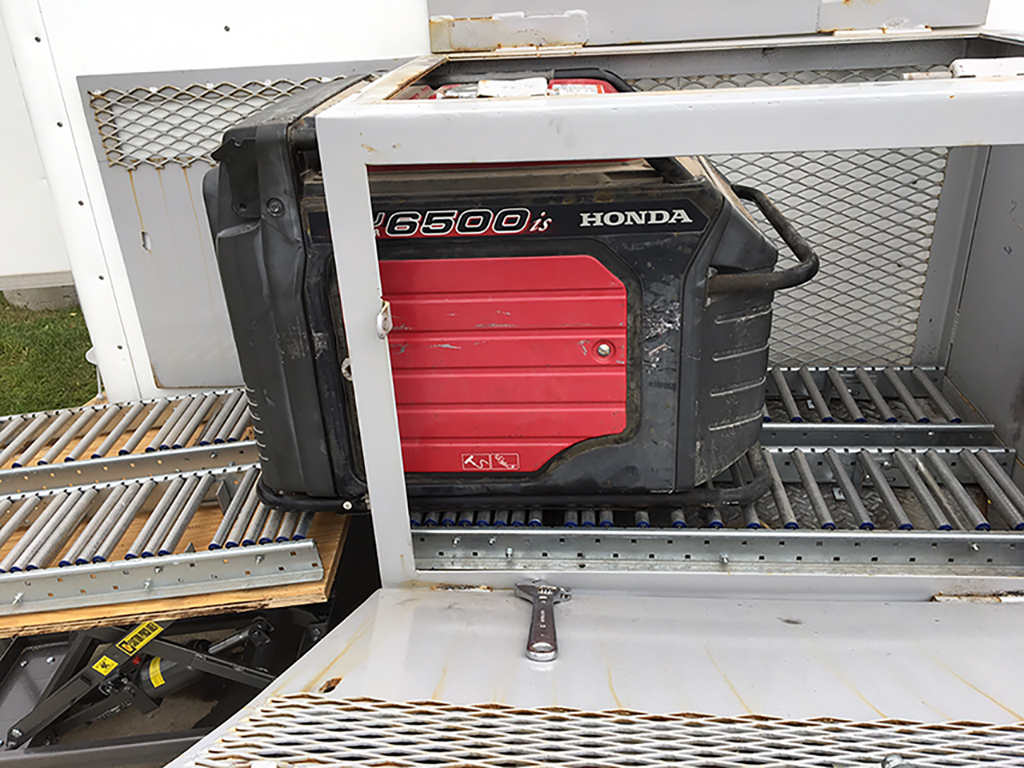
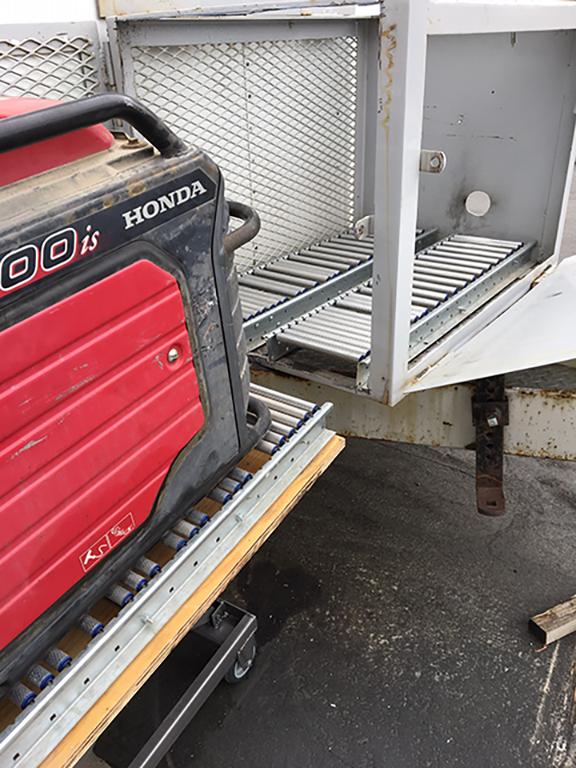
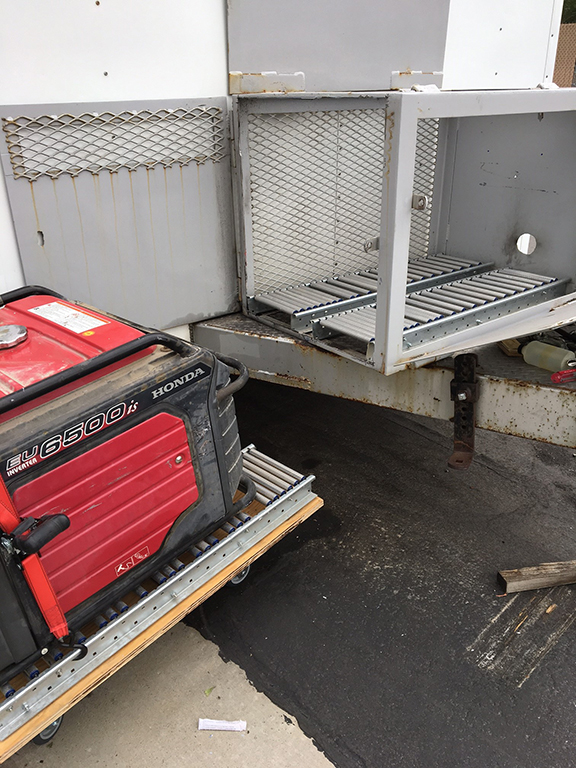
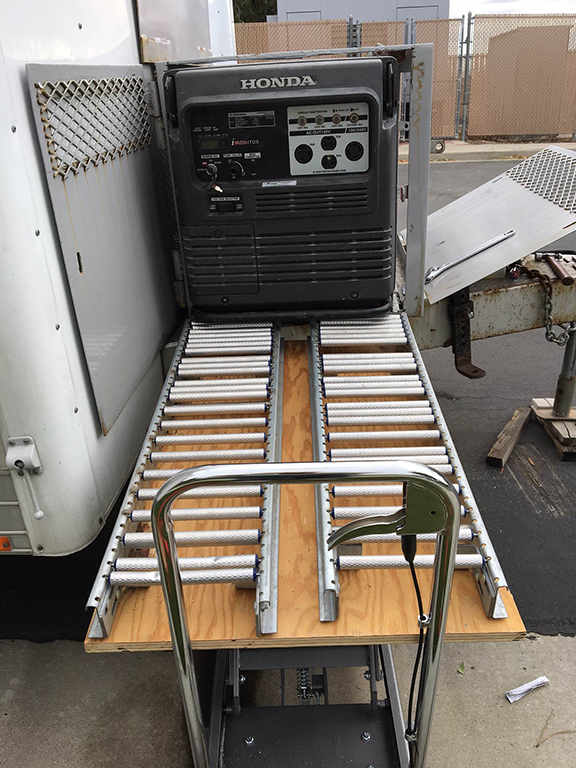
The Impact:
The generator now can be transferred from the security locker to a cart for transport by a single employee. With the generator out of the locker, it is easy to perform routine maintenance such as oil changes, battery charging, and monthly start up procedures. While SLTC currently had no injuries from this task, the potential for injury existed whenever the generator was transferred. In addition, due to challenges in removing the generator from the locker, maintenance of the generator was not adequate. This poor maintenance led to ongoing operational issues that cost SLTC money and readiness capability. An investment of a few hundred dollars negated the possibility of an injury of several thousand dollars and improved maintenance feasibility.