T.O. Haas Tire & Auto Reduces Injuries and Achieves SHARP at 14 Locations
Company: T.O. Haas Tire & Auto
Location: , Nebraska
Employees: 175 company-wide
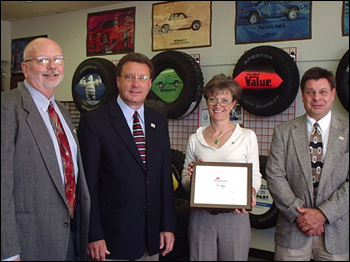
Industry: NAICS 441320, Automotive Tire Dealers
Company Description:
T.O. Haas Tire & Auto ("T.O. Haas") first opened their doors as a retailer of tires and automotive services in Lincoln, Nebraska in 1947. The company now has a chain of 26 stores throughout Nebraska, Kansas, and Iowa. With 175 employees, the company provides tire sales, installations, and repairs on: cars, light- and medium-size trucks, and agricultural equipment, as well as offering preventive maintenance services. The services are either performed at the location of the store or on-site with the use of a tire service trucks.
The Situation:
In 2006, an employee at one T.O. Haas worksite was fatally injured in a tire mounting accident. The employee had been attempting to repair an irrigation tire, which is a type of tire used on a variety of agricultural irrigation systems. During the inflation process the wheel and tire assembly failed, resulting in the tire and rim exploding. Although company policy had called for that type of tire/wheel combination to be inflated inside a cage that is designed to protect workers, company safety procedures were not followed, and the safety cage was not used. The tragic accident made it clear to company owner, Randy Haas, that they needed a more focused and comprehensive safety policy. Haas determined what was needed was to completely revamp their injury and illness prevention program for all 26 T.O. Haas locations.
To seek assistance in establishing a comprehensive injury and illness prevention program Hass contacted OSHA's On-site Consultation Program for assistance. The On-site Consultation Program offers free and confidential advice to small and medium-sized businesses in all states across the country and in several territories with priority given to high-hazard worksites. On-site Consultation services are separate from enforcement and do not result in penalties or citations. Consultants from state agencies or universities work with employers to identify workplace hazards, provide advice on compliance with OSHA standards, and assist in establishing injury and illness prevention program.
The Solution:
While working with the various T.O. Haas establishments, consultants representing OSHA's On-site Consultation Program identified a variety of hazards that were common among many of the T.O. Haas worksites. These included electrical hazards (outlets showing reverse polarity, fluorescent light fixtures not protected from damage, ground pins missing from cords, unused openings in disconnect boxes, ungrounded electrical fans, no ground fault circuit interruptions (GFCI's) installed, flexible cords used as permanent wiring, etc.), instances of personal protective equipment (PPE) being stored improperly, compressed air not reduced to 30 psi, and several instances where oxygen and gas cylinders were not secured or were stored together. Other hazards that were identified at some sites included unlabeled containers, material safety data sheets (MSDS) not on site, no eye wash stations, containers labeled with the wrong contents, and unmarked exits. In one instance, consultants also identified a problem with the site's lockout/tag-out procedures.
While establishing a strong working relationship with the OSHA On-site Consultation Programs in Nebraska, Kansas, and Iowa, the company determined that it would also hire a safety consultant. An aggressive plan was put in place to address the hazards identified by On-site Consultation Consultants, and to improve safety and health training, hazard awareness, and the implementation of the company's new injury and illness prevention program. The company established safety committees and began a process of monthly safety meetings that included training and review of the companies' safety policies and procedures. Seven years later, with significant improvements in place, the Monthly Safety Meeting process remains the foundation of its program. According to Randy Haas, "Safety policies are now an integral part of company culture and structure. Safety awareness is everyone's business."
It was after the completion of a few visits from the Kansas On-site Consultation Program that the company learned about OSHA's Safety and Health Achievement Recognition Program (SHARP). SHARP recognizes small employers who operate an exemplary safety and health management system at their worksite. The company then set the ambitious goal to attain SHARP certification at all 26 store locations. T.O. Haas earned their first SHARP award in June of 2008. As of November 2013 the company has 14 stores with SHARP recognition, and several others are on track to qualify for the award.
The Impact:
The T.O. Haas safety initiative has allowed the company to save thousands of dollars per year in workers' compensation insurance premiums, and recordable injury accidents have improved from a high of 21 in 2005 to just 2 through November of 2011. The company has also noticed a dramatic decline in the number of first aid only type injuries. Even though the trend of reducing injuries has been significant, it has not been without the need for continual improvements. The T.O. Haas locations that have not yet received SHARP status are working hard to improve their operation, so they too are eligible for the same distinction and recognition as the other locations.
The company has earned many awards in its 64 years of service, including the Better Business Bureau Integrity Award and Consumer Preference Awards. The founder of T.O. Hass was even inducted into the Tire Industry Hall of Fame. However, according to Randy Haas, the company "considers its SHARP achievements to be at the top of the list."
Although working with OSHA's On-site Consultation Program and achieving and maintaining SHARP status has contributed to the company's bottom line, the management of T.O. Haas recognizes their greatest mission is to do all they can to ensure that workers go home to their families safe and healthy every day.