Harris Rebar Earns SHARP Award
Company: Harris Rebar
Location: Albuquerque, New Mexico
NAICS Code: 332312, Fabricated Structural Metal Manufacturing
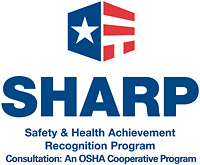
Harris Rebar fabricates and sells custom bent reinforcing steel to comply with plans and specifications provided by construction contractors. "The company's number one core value is 'we work safe,'" said Scott Murin Branch Manager. "Working with the Boise State University, Occupational Safety & Health Consultation Program (OSHCon), On-Site Consultation Services, offered us a way to improve the safety in our work environment and demonstrate to customers and employees alike the seriousness of our commitment to staying safe on a daily basis."
Harris Rebar first discovered the On-Site Consultation Program from Occupational Safety and Health Administration (OSHA) publications and advertising for the program. The OSHA On-Site Consultation Program offers no-cost and confidential occupational safety and health services to small and medium-sized businesses in all 50 states, the District of Columbia, and several U.S. territories, with priority given to high-hazard worksites. On-Site Consultation services are separate from enforcement and do not result in penalties or citations. Consultants from local agencies or colleges, such as Boise State University, work with employers to identify workplace hazards, provide advice for compliance with OSHA standards, and assist in establishing and improving safety and health programs.
On August 26, 2009, during the first visit, the OSHCon consultant identified a number of hazards, such as the need for installing more machine guarding and putting a fall protection system in place where trailers are unloaded.
The company corrected all of these hazards, but they did not stop there. "We first started by eliminating the hazards through replacing and repairing existing machine guarding," said Murin. "We also added machine guarding where needed. Next, we focused on training to educate our team members on what to look for and proper machine-guarding methods. We then moved into making daily inspections of the guarding a central part of our daily routine." The fall protection from trailers followed a similar path, starting with the elimination of the fall hazard by adding removable handrails and later upgrading to a net system. "This equipment installation and/or upgrade was followed with the education of our teammates on how to identify the hazards and eliminate or report them as needed," Murin explained.
"We thought we were operating safely prior to the first consultation visit; however, being in the OSHA Safety and Health Achievement Recognition Program (SHARP) has provided big changes to our business practices," continued Murin. "We continually review our policies, procedures, and training to improve all aspects of our programs, based on the most current knowledge of best practices. We inspect all machinery daily to ensure it is meeting the manufacturer's recommendations for safe operation. We work tirelessly to improve our safety culture. Our teammates have become more involved in spreading our safety message and taking ownership of safety on our site. This work is accomplished through our joint health and safety committee, near miss reporting, and open door policy to raise any concerns of possible safety issues. We now perform investigations at the near miss and first aid levels instead of waiting for an accident to happen. Safety stand-downs occur with our entire shop staff at the time a serious near miss occurs, so everyone can benefit from the knowledge immediately. In general, everything is done in a much more in-depth way than previously. Our safety culture has taken on a life of its own and continues to improve daily."
In the beginning, the biggest challenge was changing our safety culture. Many teammates had been doing a task the same way for many years and did not understand why things had to change. Another issue was loss of production. When the new policies and procedures were first implemented and enforced, it slowed everything down. This situation slowly changed and improved as the new policies and procedures became part of the normal daily activities. This improved safety environment, coupled with increases in productivity, was also the turning point in our safety culture. Our teammates now are part of it and believe in it. We also have implemented a company-wide computer monitoring system that looks for trends and leading indicators of areas that may become safety hazards as well as breaking out all of our pertinent safety statistics.
Harris Rebar's efforts were rewarded. On November 13, 2012, the company was accepted into the OSHA Safety and Health Achievement Recognition Program (SHARP). With renewals in 2014 and 2018, Harris Rebar has maintained its position as an OSHA SHARP participant. This program recognizes small business employers who have used OSHA's On-Site Consultation Program services and operate an exemplary safety and health programs. Acceptance into SHARP from OSHA is an achievement of status that singles Harris Rebar out among its business peers as a model for worksite safety and health.
"SHARP helped us build the strong, ongoing safety culture we have," said Murin. "Our teammates witnessed and took part in the consultation visits, then helped change our workplace for the better. SHARP participation helped each teammate take ownership of our safety."
To earn the OSHA SHARP designation, companies must have injury and illness rates below the national average. "Our biggest success has been not inuring any of our teammates," continued Murin. "Everyone watches out for each other, and we hold each other accountable. Of course, our days away, restricted, and/or transfer (DART) rate has significantly decreased, and our EMR is currently at 0.53, but our teammates are our most valuable asset. Not injuring them is our biggest success. Each night we are able to send every teammate home to their family and have done this successfully for 2,000 nights as of August 27, 2018."
In addition, the company's total recordable case (TRC) rate was maintained at zero from 2016 through 2018. Harris Rebar's DART rate was also maintained at zero from 2016 through 2018. For this period, NAICS code 332312, the Bureau of Labor Statistics reported that the industry average TRC rate was 4.5, and the average DART rate was 2.4. [NOTE: 2017 is the most recent year national averages are available.]
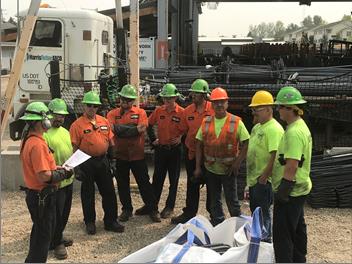
On-Site Consultation and SHARP are voluntary programs. To locate the OSHA On-Site Consultation Program nearest you, call 1-800-321-OSHA (6742) or visit www.osha.gov/consultation.
Source: Scott Murin, Branch Manager.