The Horsley Company Makes Safety Improvements with Recommendations from Utah Consultation
Company: The Horsley Company
Location: Salt Lake City, Utah
Employees: 42 Workers
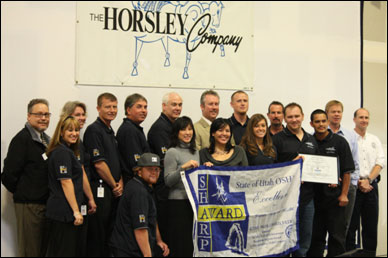
Success Brief:
The Horsley Company (Horsley) of Salt Lake City, Utah is a manufacturing, installation and automation company specializing in conveyor projects. The company has been providing solutions for material handling problems for over 70 years. Although Horsley's injury and illness rates had been below the national average for their industry, they wanted to do better. They contacted Utah Labor Commission OSHA Consultation Services, which administers OSHA's On-site Consultation Program in Utah, and worked with the program's safety consultants to improve workplace safety at the company's manufacturing facility. After implementing the recommended improvements, the company achieved lower recordable injury and illness rates and, in the process, realized lower Workers' Compensation premiums and claims. In September 2009, Utah OSHA formally recognized the company for having an exemplary safety and health management system by accepting Horsley into the agency's Safety and Health Achievement Recognition Program (SHARP).
Company Description:
Founded in 1928 as a small material handling company, Horsley developed many methods, processes and equipment necessary to improve operations at local food cannery facilities. Other companies soon recognized the expertise that Horsley was developing and started to enlist this expertise in solving their material handling needs. Horsley's capabilities in these areas evolved and grew over time. Today, Horsley (NAICS 333922, "Conveyor and Conveying Equipment Manufacturing") designs, manufactures and installs conveyor systems used at airports, and other industries requiring automated conveyor solutions. However, Horsley's primary business focus is integrating sophisticated in-line explosive detection processes into its baggage handling systems, which it supplies to the Transportation Security Administration (TSA) for use at airports. The company also develops and installs conveyor systems used at automated food processing plants, water treatment plants, and in other industries that need to move items from "Point A" to "Point B."
The Situation:
Historically, Horsley's recorded injury and illness rates have been below the national average for its industry. In 2008, Horsley's Total Recordable Case (TRC) rate was 1, and a Days Away, Restricted, and/or Transfer (DART) rate of 2.55. By comparison, the average TRC for its industry was 7.4 and the DART was 3.9. TRC represents the total non-fatal injuries and illnesses per 100 full-time employees for a given period of time. The DART rate measures the number of recordable injuries and illnesses per 100 full-time employees that resulted in days away from work, restricted work activity, and/or job transfer. OSHA uses injury and illness data collected by the Bureau of Labor Statistics to determine the degree to which workers may be exposed to hazards in specific industries and companies.
Although their incidence rates indicated that Horsley's health and safety record were significantly better than the industry average, the company was eager to make improvements. According to Michael O'Connor, General Manager and Vice President for Horsley, the company "places the safety of its employees above all other company goals. The team at Horsley understands that the investment in safety is an investment in its employees, which, in turn, is an investment in the company's future."
The Solution:
Horsley heard about OSHA's On-site Consultation Program from its parent company, G&T Conveyor Company. They learned that OSHA's On-site Consultation Program offers free and confidential advice to small and medium-sized businesses in all states across the country, with priority given to high-hazard worksites. OSHA's On-site Consultation Program conducts over 30,000 visits per year covering over one million workers in response to requests from small employers looking to create or improve their safety and health management systems. In Utah, the office that administers the OSHA On-site Consultation Program is the Utah Labor Commission OSHA Consultation Services (OSHA Consultation). Horsley contacted OSHA Consultation and arranged for its consultants to conduct an initial site visit, which occurred in May 2009.
During the site visit, OSHA Consultation identified several potential hazards: missing chemical labels on containers, a scissor lift without a top rail, unstable storage of a generator on a storage rack, a drill press that was not properly secured to the floor, extension cords being used as permanent wiring, a fire extinguisher not identified with proper signage, and an electrical outlet with an unsecured cover plate. As a result of the site visit, hazards were immediately corrected and appropriate personal protective equipment (PPE) was assigned whenever the hazard called for specific PPE.
After the walk-through, OSHA consultants held productive discussions with Horsley management and workers, and reviewed in detail the company's safety manual and procedures to ensure that all processes and programs applied directly to operations at Horsley. Also, workers were subsequently trained on hazard detection and the proper procedures for dealing with discovered hazards and how to avoid them in the future.
Prior to contacting OSHA Consultation, Horsley already had many processes properly in place. However, OSHA Consultation identified some processes that would improve workplace safety. As with any change, the recommended process changes were met with some uncertainty, but when the recommendations were implemented, the benefits of change became obvious.
The Impact:
After their visit from OSHA Consultation, workers at Horsley became even more aware of the importance of safety, and that each worker has a role and responsibility to ensure safety in the workplace. According to Michael O'Connor, employees are now asking themselves, "Is this the safest way to perform this task?" He added, "We want our employees to carry this mindset with them when they go home and work around the home. We have heard from our employees that they now are wearing PPE when they work around the house. That says the program is a success in the community as well."
Since the OSHA Consultation site visit and follow-up discussions, Horsley has continued to effectively implement processes and procedures that promote workplace safety. In the fall of 2009, Utah OSHA formally recognized the company for having an exemplary safety and health management system by accepting Horsley into the agency's Safety and Health Achievement Recognition Program (SHARP). Evidence of an exemplary safety and health program were reflected in 2010, when annual records for Horsley indicated that the company's TRC and DART rates each dropped to zero. Improvements involving workplace safety often have financial rewards. The company experienced a significant reduction in both Workers Compensation Premiums and claims since 2008.
According to Michael O'Connor, "The SHARP award tells business partners that you are committed to success in your business and you will go the extra mile to be the best. The biggest advantage working with the On-site Consultation Program is that employees are involved and committed to safety. It has given them something to be proud of and to strive for every day. A strong emphasis on safety conveys the message that the company cares about its employees. You can't put a dollar value on something as important as that."
Source:
Tenille Whitten, Manager of Administrative Services, The Horsley Company, Salt Lake City, Utah