Through SHARP, Ideal Jacobs Stands-out as an Ideal Company in the Printing Industry
Company: Ideal Jacobs
Location: Maplewood, New Jersey
Employees: Employs 25 workers
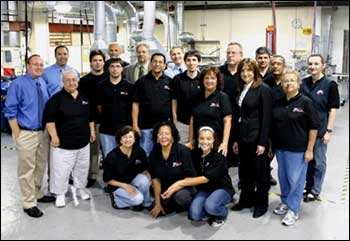
Success Brief:
In 2002, Ideal Jacobs began working with the New Jersey On-site Consultation Program to improve its regulatory compliance efforts and create a more efficient safety and health management program. Utilizing the recommendations provided by the consultant, Ideal Jacobs developed a comprehensive Job Hazard Analysis (JHA) and implemented a lockout/tag-out program. The implementation of these two solution-oriented features contributed to the company's safety and health success by creating a safer and more efficient work site.
Company Description:
Ideal Jacobs (NAICS 323117), a commercial printing company specializing in custom die-cut labels and graphic overlays, including polycarbonate labels, fabric over foam gaskets, injected molded panels, wire assemblies, and machined parts. Begun as a family business in 1921 and headquartered in Maplewood, New Jersey, the company has grown into a multi-national corporation with locations in the United States, China, Mexico, The Netherlands, and Thailand. Ideal Jacobs serves Fortune 500 clients in the telecommunications and consumer electronics industries.
The Situation:
According to Andrew Jacobs, President of Ideal Jacobs, the safety culture is rooted, communicated, and strongly supported throughout the company starting at the top with his leadership. With a desire to operate as safely as possible, Mr. Jacobs realized that the company needed help with its regulatory compliance efforts. In 2001, a colleague suggested that Mr. Jacobs contact the OSHA On-site Consultation Program to find out how the Program could help the company identify the strengths and weaknesses of its safety and health management program.
Ideal Jacobs wanted the On-site Consultation Program's assistance with the detection of potential hazards at its worksite. In February 2002, Ideal Jacobs contacted the New Jersey On-site Consultation Program and requested a free and confidential consultation survey of its facility. Not knowing what results to expect from the consultation visit, Mr. Jacobs let the consultant know up front that he was open to all suggestions that would make Ideal Jacobs a safer workplace. Mr. Jacobs believed that working with OSHA would give Ideal Jacobs the competitive advantage it needed to thrive in the marketplace and allow the company to improve its safety and health management program.
The Solution:
A consultant from the New Jersey On-site Consultation Program conducted an initial consultation survey of the Ideal Jacobs facility in Maplewood, NJ in May 2002. The consultant began the visit with an explanation of the Program's services and informed the employer of its rights and responsibilities. The consultant, along with Mr. Jacobs, Vincent Santoro, Vice President of Global Manufacturing for Ideal Jacobs, and a worker, conducted a walk through of the plant and discussed what the company was doing right and what things the company could do better. Based on observations and a review of all the company's documents related to its safety and health procedures, the consultant provided Ideal Jacobs with a written report. The report included an itemized list of all the hazards identified during the visit, the classification of each hazard, a correction due date for each serious hazard, and recommended methods to eliminate or control each hazard. In addition, the consultant provided workers with training in emergency preparation, personal protective equipment, hazard communication, machine safeguarding, and electrical standards. The consultant also shared with the company research materials and examples of "best practices" of what other companies were doing.
In response to the recommendations that the consultant provided, Ideal Jacobs instituted several solution-oriented features that improved the company's safety and health management program. These activities included the implementation of a noise abatement program and a lockout/tag out program. The company also received assistance with the development of a comprehensive JHA. JHA, a technique that identifies hazards associated with job tasks, allows employers to take steps to eliminate uncontrolled hazards or reduce hazards to an acceptable risk level. Further, Ideal Jacobs used the consultant's report to address hazards such as the improper use of extension cords, failure to secure small machinery to the bench top, and inadequate signage.
The consultant also shared information with Ideal Jacobs about OSHA's Safety and Health Achievement Recognition Program (SHARP) during the consultation visit. SHARP recognizes small employers that operate exceptional safety and health management programs. Based on this knowledge, Ideal Jacobs made achieving SHARP status its focus and continued working with New Jersey On-site Consultation Program to address the company's regulatory hazards. In 2004, Ideal Jacobs attained SHARP status.
The Impact:
When Ideal Jacobs began working with New Jersey On-site Consultation in 2002, its Days Away, Restrictions, and Transfers (DART) and Total Recordable Case (TRC) rates were zero compared to industry averages at that time of 1.3 and 3.0. In 2004, Ideal Jacobs' DART rate was 1.1 and the TRC rate was 3.85, compared to the national average of 1.5 and 4.1 respectively. With injury and illness rates below the national average, the company was able to realize its goal of achieving SHARP status. The company continually works with the New Jersey On-site Consultation Program to improve the safety and health of its workers. As of August 2010, the company sustains DART and TRC rates of zero. According to Mr. Jacobs, maintaining SHARP status recognizes the efforts of Ideal Jacobs' workers and demonstrates that OSHA and small businesses can successfully collaborate.
Since its first On-site Consultation visit, Ideal Jacobs has become an active ambassador for the On-site Consultation Program. For example, on September 30, 2008, Mr. Santoro participated in OSHA's Small Business Forum "Business of Small Business" entitled "Challenges Small Businesses Face in Complying with OSHA Regulations." In his presentation, "Journey towards Safety," Mr. Santoro highlighted the ways in which OSHA's On-site Consultation Program has helped Ideal Jacobs address issues related to the production of noise, crush zones and nip points, chemical use and storage, ultraviolet light, and sharp objects. Please visit OSHA's Small Business Forums to view additional information.
According to Mr. Santoro, "Committing time and resources to worker safety, health, and overall well-being has resulted in Ideal Jacobs' having satisfied, healthy, highly productive employees that spend less time away from work." Mr. Santoro concluded, "Working with On-site Consultation enabled Ideal Jacobs to provide worker safety and health protections which allows the company to successfully compete in the marketplace since regulatory compliance translates into profitability."
Source:
Vincent Santoro, Vice President of Global Manufacturing, Ideal Jacobs Corporation