More than Just Equipment: Oliver Manufacturing Company, Inc. Is Equipped For Success
Company: Oliver Manufacturing Company, Inc. - Rocky Ford
Location: Rocky Ford, Colorado
Employees: Approximately 47 full-time workers
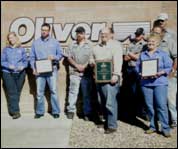
Success Brief:
Since Oliver Manufacturing Company, Inc.'s (Oliver) initial visit with the Colorado On-site Consultation Program in August 2006, the company has successfully consolidated four core operations: metal shop, assembly line, wood shop, and testing into one facility eliminating the need for three separate buildings. Putting into action the recommendations from the Colorado On-site Consultation Program on air monitoring and traffic flow configuration, Oliver completed the move into its new 21st century manufacturing facility in June 2008. Oliver was able to utilize these recommendations during its consolidation to streamline transport and material handling processes which created greater manufacturing efficiencies and improved safety and health in the workplace.
Company Description:
Oliver, a manufacturer of separators, destoners, precision sizers, and other equipment used primarily for agricultural and industrial applications (NAICS 333999), is located in Rocky Ford, Colorado. This third generation family-owned company employs approximately 47 full-time workers and has been a separation solution specialist since 1930. The company's equipment is responsible for separating 95% of the world's coffee beans before roasting. In addition, almost 60% of all seeds are processed by Oliver-manufactured gravity separators before they are planted to produce the world's food.
The Situation:
Jeffrey Fawcett, Chairman of the Safety Committee and Material Control Manager at Oliver, recognized that with no full-time safety and health professionals on staff, the company needed to seek outside assistance in order to improve its safety and health management program. One of Oliver's engineers, a graduate of Colorado State University (CSU), suggested the company seek the assistance of the Colorado On-site Consultation Program to help identify potential workplace hazards and improve their safety and health management program. CSU administers the OSHA On-site Consultation Program in Colorado.
Some employees had concerns about inviting OSHA in as a resource and were skeptical about the benefits of the On-site Consultation Program. After much deliberation by management and employees, the management team at Oliver determined that the services of the Colorado On-site Consultation Program were necessary. The initial Consultation visit was conducted in August 2006.
The Solution:
Oliver was in the planning phase of its operational consolidation and still physically located in its old facility when the Colorado On-site Consultation Program conducted the first visit in August 2006. Oliver received recommendations from the consultant on air monitoring and material handling to ensure that they would not create new hazards after their consolidation into a new building. The company also gained assistance with configuring the traffic flow of their current operations and a strategy for the traffic flow in the new facility. Standing steadfast to the company's mission statement which emphasizes, "Safety is Everyone's Responsibility," management and workers went into action on implementing the consultant's recommendations for traffic flow and material handling in order to improve their safety and health management program. Oliver also turned to their workers compensation carrier who was able to conduct air monitoring to evaluate any potential employee exposure to hexavalent chromium and other welding-related fumes.
Encouraged by the assistance received from the Colorado On-site Consultation Program, Oliver considered applying for the Safety and Health Achievement Recognition Program (SHARP). SHARP recognizes small employers who operate an exemplary safety and health management system. Oliver talked with manufacturing companies participating in SHARP to get a first hand account of the benefits of the Program.
At the time, Oliver did not qualify for SHARP. With their sights set on achieving SHARP, Oliver began making significant changes to improve their safety and health management program. Among the changes between 2005 and 2009, the company acquired a 21st century manufacturing facility and purchased new equipment, successfully merging four separate operations. Working with the Colorado On-site Consultation Program during the planning and implementation phase of their strategic move, Oliver successfully streamlined their transport and material handling processes creating greater manufacturing efficiencies and improved safety and health in their workplace.
The Impact:
As a result of working with the Colorado On-site Consultation Program to improve the company's safety and health management program, Oliver was accepted into the SHARP Program in August 2009. Prior to being accepted into the SHARP Program, Oliver boasted a facility rate of "0" for both Days Away, Restricted and Transferred (DART) and Total Recordable Case Rate (TRC) for 2008. The 2008 national industry average DART and TRC was 3.10 and 6.8, respectively.
While Oliver's 2009 rates did show an increase in their TRC rate from 0 to 2, the sites' DART remains constant at 0, and its DART and TRC rates have been well below the national industry average for the past few years. In 2007, the company's DART and TRC were 0 and 1, compared to national industry average of 2.6 and 5.6, respectively. In 2006, Oliver's DART and TRC were 1 and 2, respectively.
"We have always tried to do over and above what is required for a safe work environment," said Jeffrey Fawcett, Chairman of the Safety Committee and Material Control Manager. Mr. Fawcett went on to say that the [SHARP] achievement has "created a sense of pride in the workplace" for Oliver's employees.
Source:
Mr. Jeffrey Fawcett, Chairman of the Safety Committee and Material Control Manager, Oliver Manufacturing Company, Inc.