Altus Air Force Base Utilizes Employee Involvement and Management Commitment to Contribute to a Successful Air Force National Partnership
Background:
The Secretary of Defense previously tasked the Department of Defense (DoD) with reducing the number of occupational injuries and illnesses at all 400 DoD installations nationwide. DoD selected OSHA's Voluntary Protection Programs (VPP) safety and health management system (SHMS) model to help them accomplish this task over other international SHMS models because of other federal agencies' success with the model. So far, 22 DoD facilities have been recognized by OSHA as VPP Star participants, and by the end of September 2009, DoD plans to have an additional 15 participants approved in the program.
Attaining an excellent safety and health management system takes hard work and dedication and may seem a little overwhelming at first. The United States Air Force (USAF) recognized that OSHA had valuable expertise in workplace safety and health, and could offer useful tools, such as VPP and OSHA Challenge, to help them achieve DoD's goal. OSHA Challenge provides a three-stage process to establishing an effective SHMS. Participants are guided through this process by volunteer Administrators and Coordinators.
First, in the spring of 2006, USAF approached OSHA to discuss forming a partnership to assist them with promoting safety and health at their installations. They recognized that OSHA had valuable expertise in occupational safety and health and could offer useful tools and resources. In late August of 2007, USAF and OSHA formed a national OSHA Strategic Partnership (OSP) with the main purpose being to provide an infrastructure for managing installations that are working towards attaining VPP recognition in the future. USAF also is utilizing OSHA Challenge to help them develop an effective SHMS and volunteered to serve as a Challenge Administrator. Lessons learned shared by VPP participants will benefit employee safety and health at all DoD installations.
Success Impact:
Implementing Effective Safety and Health Management Systems and Promoting Occupational Safety and Health Leads to Many Positive Results
Eighteen installations are covered under the USAF and OSHA national OSP - one of these being the Altus Air Force Base (Altus) in southwestern Oklahoma. With an average of over 300 days of weather favorable to flying each year, Altus is an ideal location for young airmen and airwomen to sharpen their skills. Since it was founded in 1943, the base has evolved to become the premier air mobility training location in USAF.
However, several years ago in 2005, Altus was listed as one of DoD's top 10 hazardous worksites which was consistently reflected in reported high injury and illness rates. In August 2006, the base began developing their safety and health management system which included implementing safety and health policies and practices. Almost immediately, Altus began to see a decrease in incident rates and a dramatic reduction in lost work days. Before starting the VPP process, Altus recorded 720 lost work days. Two years later in 2008, 42 lost work days were recorded - this represents a 94 percent reduction over a two-year period. Below are a couple of examples of how this was accomplished:
- Altus employees suggested implementing a new work practice and researched a design of special rack and charging station minimizing manual handling of oxygen cylinders weighing 133 pounds each. Rather than manually moving dozens of cylinders from multiple levels on existing racks, they adopted a National Aeronautics and Space Administration (NASA) designed charging station allowing for the use of a forklift to transport the cylinders, significantly reducing employee exposure to sprains and strains.
- Employees coordinated with base engineering to design a specialized work platform to maintain jet engines attached to C-17s in the hanger bays. The outcome was astonishing. Not only did the new platform reduce exposure to ergo related injuries, fall hazards, and damage to the aircraft caused by traditional work platforms, it aslo allowed up to seven mechanics to work on the platform at one time (as opposed to one mechanic in the past). This new design has led to a 50 percent reduction time needed to maintain the engines and was so successful that other platforms will be fabricated at other USAF bases around the country. USAF also shared this design with the Royal Australian Air Force who has plans to build a similar unit for maintaining their own aircrafts.
"Base management and employees will attest that their preparation for VPP _ particularly increasing employee involvement and using the OSHA Challenge tool - had the greatest impact to date. I attribute this success to employees and management working together to make their work tasks safer….and as it turns out - a lot more efficient."
—Lieutenant Colonel Wade Weisman
United States Air Force
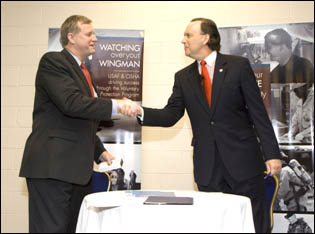
Edwin G. Foulke, Jr., former Assistant Secretary of Labor, OSHA (left) and William C. Anderson, Assistant Secretary of the Air Force, Installations,Environment and Logistics (right), shake hands after the signing of the national USAF OSP agreement on August 27, 2007.
Partnership Objectives:
Key objectives of the national OSP are to: reduce civilian and military workforce injuries and illnesses at each participating Air Force installation by at least three percent per year, expand USAF participation in VPP, increase awareness of the value of effective safety and health management systems, and provide mechanisms for promoting contractor safety and health.
Origin: Washington, D.C.
Partners: The Department of Defense, Department of the Air Force (Air Force)
Partnership Signed: August 2007
Industry Code Description (NAICS Code): Air Force-National Security (928110)
Employees: 20,000+
Employer: 1
Source/Date: Lieutenant Colonel Wade Weisman, United States Air Force Pentagon; Jim Boom and Danielle Gibbs, OSHA National Office/July 2009