Cobb Hill/Pro Con Construction Joint Venture, LLC Partnership Reduces Injuries and Illnesses and Increases Workers' Safety and Health
Background:
On June 2006, Cobb Hill Construction and Pro Con Construction partnered with the New Hampshire Department of Environmental Services Consultation Program and OSHA's Region I Concord Area Office to form an OSHA Strategic Partnership (OSP). This OSP was developed as part of the joint venture construction project at the 11 South Main Street and 75 Storr Street location in Concord, New Hampshire. The project involved the construction of a multi-use eight story building including office and retail space, a movie theater, and a five level parking garage.
The main purpose of the OSP was to promote a positive safety and health culture at the project site through the development and implementation of an effective safety and health management system (SHMS). By ensuring that specific elements were included in the SHMS - management commitment, employee involvement, worksite analysis, hazard prevention and control, and safety and health training - injuries, illnesses, and fatalities would be reduced, resulting in lower workers' compensation costs. The project was successfully completed in the fall of 2007.
Success Impact:
Partnership Reduces Injury and Illness Rates
One of the key objectives of the OSP was to reduce injuries and illnesses at the worksite. According to the 2005 Bureau of Labor Statistics (BLS), the national average Total Case Incident Rate (TCIR) for the construction industry was 6.3. Prior to participating in the OSHA Strategic Partnership Program (OSPP), and working on this construction project, Cobb Hill Construction and Pro Con Construction's combined three-year average DART rate was 8.02 (2003-2005). At the completion of the project in 2007, the combined companies' TCIR was 3.73 - 41 percent below the BLS national average. Prior to the OSP, eight of the participating subcontractors had three-year average DART rates of 10.0; however, during the project these same eight subcontractors' average DART rates were 0.0 - a 100% reduction.
Over the 18 months of the project, 19 of the 21 contractors did not experience any recordable injuries or illnesses. Out of 107, 144 hours worked, only two recordable injuries occurred.
Partnership Develops an Effective Safety and Health Management System
One of the main components of the SHMS was to increase safety and health training. One of the requirements of the OSP was that all employees had to complete an onsite safety and health orientation course on specific site requirements and issues - including fall protection, electrical hazards, hazard identification and communication, and site disciplinary actions. Another OSP requirement was that all foremen working at the site had to complete the OSHA 10-hour Construction Safety Course within three months of beginning work at the site. All subcontractors conducted weekly tool box talks as a way to improve their SHMS. The overall result of the safety and health training offered and conducted was that all 250 employees received trained from the inception of the project to the completion of the project.
Other components of the SHMS were to control and prevent worksite hazards through identification and analysis. Independent safety and health consultants and insurance representatives conducted regular onsite inspections during the project. By receiving the previous training on hazard identification and communication, employees were able to abate many hazards before accidents or injuries occurred.
Other successes of the OSP were increased management and employee involvement, and strengthened or enhanced relationships between employers, labor, and government stakeholders.
Partnership Objectives:
The key objectives of this Partnership include reducing safety and health hazards through identification and correction, reducing injury, illness, and fatality rates, increasing the number of contractors with comprehensive SHMS, and encouraging a sustainable working relationship between all involved stakeholders.
- Origin: OSHA Region 1, Concord Area Office
- Partners: Cobb Hill/Pro Con Construction Joint Venture LLC and New Hampshire Department of Environmental Services Consultation Program
- Partnership Signed: June 19, 2006
- Industry: Construction (NAICS Code 23, SIC Code 1542)
- Employees: Approximately 250
- Employers: 21
- Source and Date: ProCon Staffers; Rich Lambert and Brian Knox
Cobb Hill staffer: Jeannie Alberico
Independent safety and health consultants: Jay Fitzpatrick and Kevin Rush
Concord Area Office, OSHA representatives: Rose Ohar and David Berard
OSHA Consultation Services Representative: Steve Beyer
OSHA Region I, OSHA representative: Kevin Clarke
August 2008
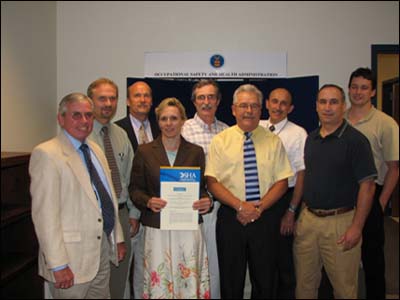
Cobb Hill Construction and Pro Con Construction Joint Venture, LLC OSP Signing (June 2006). Picture (from left to right): Kevin Clarke,
OSHA Region I; Gerry Kingwill, Principle of Cobb Hill;Tom Avelone, President of Cobb Hill; Rose Ohar, Area Director of Concord NH Area Office; Steve Beyer,
Director of NH, OSHA Consultation Program; Richard Lambert, Manager of ProCon Construction; George Kilens, AAD Concord NH OSHA Office; David Berard, CAS Concord,
NH OSHA Office; Steve Rook - AAD Concord NH OSHA Office