Northeast Wisconsin Foundry Ergonomics Partnership Promotes Worker Safety and Health During First Year
Background:
On March 11, 2009, the Northeast Wisconsin Foundry Ergonomics Partnership (NEWFEP) II OSHA Strategic Partnership (OSP) was formed to reduce injuries and illnesses by implementing effective safety and health management systems (SHMS); eliminating serious hazards; and developing policies, practices, and processes to decrease the incidence and severity of musculoskeletal disorders (MSDs) for workers in the foundry industry. It is the third OSP formed since 2003 between OSHA and stakeholders from this industry. Seven employers participate which covers close to 5,000 workers. There is also strong Union involvement in the OSP.
Success Impact:
Increased Number of Effective Safety and Health Management Systems Developed and Implemented in the Industry
One key goal of the OSP is that all OSP participants will develop and implement an effective safety and health management system (SHMS). During 2009, this key goal was met with 100 percent of the OSP participants developing and implementing an effective SHMS at their facility. One of the components of an effective SHMS is offering safety training opportunities to workers and managers/supervisors. During this same year, the OSP offered 25 safety training sessions and 5,465 safety training hours to 1,306 workers and managers/supervisors. Workers also received training on signs and symptoms of MSDs and appropriate control measures.
Focus on Worker Involvement Results in Safety Improvements and Best Practices
The OSP participants have worked closely together to share ideas and successes of the many safety improvements made at their facilities. Worker involvement is a critical component to the development of best practices and the overall success of the OSP. Each OSP participant has established the Ergonomics Safety Committee which includes worker representatives who participate in the onsite ergonomics abatement activities and make recommendations for improvements.
In 2009, many safety improvements were made and best practices developed involving the replacement of manual processes with automation which reduced MSD risks for workers. The following images show changes at the facilities involving this new automation:
PERM MOLD POURING
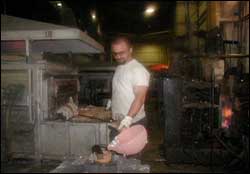
BEFORE
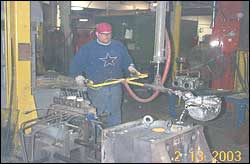
AFTER
- PROBLEM: Workers manually maneuver the ladle to scoop aluminum from the furnace well and pour into a mold.
- SOLUTION: Hydraulic lift arms have been fabricated internally to suspend the ladles, allowing pourers to merely direct the movements of the arm.
- COST: $5000
- COST RECOVERY TIME: Three to six months
- BENEFITS: Eliminated all shoulder and back injuries and burns. Reduced cycle times and fatigue which increased production.
DISA POURER
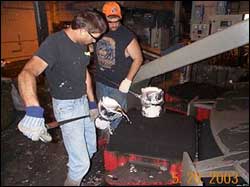
BEFORE
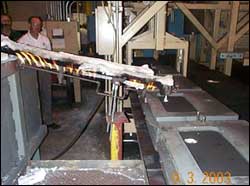
AFTER
- PROBLEM: On the majority of molds on the Hunter 30 x 32 automatic Molding Machine, it took two workers to pour the mold. (Ladle weight – 40 lbs. each with metal)
- SOLUTION: Automatic pouring machine eliminates both workers from hand-pouring.
- COST: $35,000
- COST RECOVERY TIME: Six months
- BENEFITS: Eliminated burns, shoulder and back injuries, and manpower; also increased production.
GRINDER/CHIPPER DIE PRESS OPERATOR
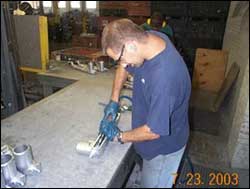
BEFORE
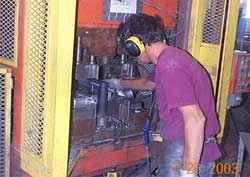
AFTER
- PROBLEM: Small pneumatic hand grinders were used to finish parts, exerting strain on the wrists and arms.
- SOLUTION: A trim die is now used to trim parts.
- COST: $40,000
- COST RECOVERY TIME: Six to twelve months
- BENEFITS: Reduced cycle time, eliminated ergonomic stressors including vibration, poor posture, and force.
When making these kinds of ergonomics improvements, the OSP participants draw upon each other's expertise and learn from each other's mistakes. As new ergonomics initiatives are implemented, the OSP participants share both their successes and failures with the Ergonomics Safety Committee. As a result, safety decisions are determined without much investment being necessary. When the OSP participants need additional technical assistance and guidance, they can draw upon the technical resources of the Wisconsin Safety and Health Consultation Program and OSHA.
OSP Reduces Injury and Illness Rates from Baseline - Days Away, Restricted, and Transferred (DART) Rate and Days Away from Work Injury and Illness (DAFWII) Rate
One of the key goals of the OSP is to evaluate the effectiveness of the ergonomic program by calculating the DART and DAFWII incidence rates for each facility and comparing these rates to the previous year. A uniform reporting system was used to collect data by the OSP participants. These rates were determined for injuries and illnesses relating to MSDs (ergonomic-related injuries), as well as all other injures and illnesses experienced. The OSP's DAFWII rate for ergonomic-related injuries decreased 24 percent from the baseline and the DART rate decreased 48 percent which is quite impressive. The table below presents the OSP's ergonomic-related and non-ergonomic-related injury and illness rates compared to the baseline:
Year One | DAFWII Rate | DART Rate | ||
---|---|---|---|---|
OSP Baseline Rates (2008)* | Non-ergo | 14.4 | Non-ergo | 3.3 |
Ergo | 3.8 | Ergo | 2.3 | |
OSP 2009 Rates | Non-Ergo | 11.8 | Non-ergo | 3.2 |
Ergo | 2.9 | Ergo | 1.2 | |
Percentage Difference b/t Baseline and 2009 Rates | Non-ergo | -18% | Non-ergo | -3% |
Ergo | -24% | Ergo | -48% |
*Note: The established baseline represents rates from the last year (2008) of the previous FEP OSP.
Benefits of the OSP
In most cases, the increased automation has increased productivity which often offsets the cost of the process improvement. Worker morale has improved because the automation has eliminated many of the more difficult aspects of their jobs, such as heaving lifting, pushing, and pulling. The OSP participants anticipate that worker retention rates at the foundries will continue to improve over time. Other benefits reported in the OSP's first annual evaluation included: increased safety and health awareness; and improved relationships with unions/workers; management; and OSHA. The planned end date for this OSP is March 12, 2012.
Increasing OSP Outreach and Awareness
The OSP has developed a website to share ergonomics information among the OSP participants and other stakeholders interested in ergonomic improvements. As this website continues to develop, descriptions of the OSP, along with a database of case studies of ergonomic interventions, will be available. The website is up and ready to visit at http: //www.newfep.com/. The OSP is currently in the process of developing a PowerPoint presentation on the OSP and its current safety ergonomic initiatives which will be posted on the new website.
Partnership Objectives:
Key objectives of the OSP are to: reduce the incidence and severity of MSDs at participating facilities; implement ergonomic improvement, and communicate best practices in the foundry ergonomic arena.
- Origin: OSHA Region V, Appleton Area Office
- Partners: Neenah Foundry Company; ThyssenKrupp Waupaca, Inc.; Brillion Iron Works, Inc.; Roloff Manufacturing Corporation; Manitowoc Grey Iron Foundry, Inc.; Wisconsin Aluminum Foundry, Co.; Mercury Marine Division of Brunswick Corporation; and the Wisconsin Consultation Program (WisCon), Wisconsin State Laboratory of Hygiene
- Participating Labor Unions: GMP Local 121B (Neenah Foundry); GMP Local 301 (Manitowoc Grey Iron Foundry); United Steelworkers, Local 125; Glass, Molders, Pottery, Plastics & Allied Workers, Local 301; International Association of Machinist & Aero Space Workers, Local 516 (Wisconsin Aluminum Foundry); GMP, Local 271 (Roloff Manufacturing Corporation); USW, Local 70475 (Brillion Iron Works); and International Association of Machinists and Aerospace Workers, Local 17 (Mercury Marine).
- Partnership Signed: March 11, 2009
- Industry (NAICS Code): Iron Foundries (331511)
- Employees: 4,870
- Employers: 7
- Source (Date): Kelly Bubolz, Compliance Assistance Specialist, Appleton Area Office; James Dillard, OSPP Coordinator, Chicago Regional Office; Danielle Gibbs, OSHA National Office (September 2010)