Pikes Peak Steel Earns 14% Discount on Workers' Compensation Premiums by Improving Safety Performance
Company: Pikes Peak Steel
Location: Colorado Springs, Colorado
NAICS Code: 332312 - Fabricated Structural Metal Manufacturing
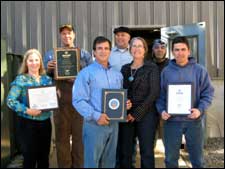
Employees: Approximately 30 full-time workers
Success Brief:
Pikes Peak Steel, a family-owned small business that manufactures structural steel for commercial and residential buildings, worked with the Colorado On-site Consultation Program to strengthen the company's safety and health program. Since the Pikes Peak Steel's initial Consultation visit in October 2005, the company's workers' compensation claims have decreased by $26,000.
Company Description:
Pikes Peak Steel, a steel fabrication company (NAICS 332312) located in Colorado Springs, Colorado, provides steel products to commercial contractors in the western United States and to homebuilders in the Colorado Springs and the surrounding region.
The Situation:
The President and owner of Pikes Peak Steel, Mr. Glen Carter, knew that the company's safety and health program needed improvement to help protect employees' health and safety. He stated that while viewing the Colorado Occupational Health and Safety Consultation Webpage, he discovered that OSHA's On-site Consultation Program offers free and confidential advice to small and medium-sized businesses, with priority given to high-hazard worksites.
In 2005, Mr. Carter decided to take advantage of the On-site Consultation Program and requested a comprehensive consultation visit. He contacted the Colorado On-site Consultation Program to get help with implementing the company's safety and health management program and to educate himself and his workers on the importance of a safe and healthy worksite.
The Solution:
In October 2005, consultants from the Colorado On-site Consultation Program performed a comprehensive consultation survey of the Pikes Peak Steel facility which included a review of the company's safety and health management system. Based on the feedback that he received, Mr. Carter began to correct all identified safety and health hazards and improve elements of the safety and health management program.
For example, Mr. Carter began educating himself and the supervisors on the company's safety and health responsibilities and the impact of safety and health performance on the company's profits and losses. To improve morale, Mr. Carter empowered workers to get involved in the safety and health program decision making process. He asked them to provide input into the types of training they needed to receive in order to do their jobs safely and effectively.
In 2006, Mr. Carter began pursuing the Safety and Health Achievement Recognition Program (SHARP) designation in an effort to acknowledge the hard work of his employees. After successfully completing a hazard identification survey, Pikes Peak Steel showed promise of achieving SHARP status. However, the company's injury and illness rates for the previous three years were higher than the industry average published by the Bureau of Labor Statistics (BLS). As a result, the company entered into the Pre-SHARP program, implemented an action plan, and continued to work to lower their illness and injury rates.
The Impact:
In September 2008, Pikes Peak Steel was recognized under the SHARP Program for their exemplary safety and health management system. According to Mr. Carter, the "employees feel good about what they have accomplished, and it has a positive influence on everything else they do."
When Pikes Peak Steel first began working with the Colorado On-site Consultation Program in 2005, the Total Recordable Case Rate (TRCR) at the company was 20.5 compared to the national average for the industry of 6.7 and the worksite's Days Away, Restricted and Transferred (DART) rate was zero compared to the national average for the industry of 5.0. Pikes Peak Steel paid $31,000 in workers' compensation claims in 2005. By 2008, the company's TRCR dropped to 2.9 and its DART rate was 0, compared to the industry's national average TRCR and DART of 9.9 and 4.4 respectively. Further, Pikes Peak Steel's workers' compensation claims dropped to $5,000 in 2008. To the surprise of Mr. Carter, in 2008 his insurance carrier gave him a 14% discount on his workers' compensation premium due to the company's safe performance record. In 2009, the company's TRCR was 3.3 and its DART rate was 0. Mr. Carter noted, the implementation of a safety and health management program not only saves the company money, but it also protects the employees from experiencing pain and suffering due to injuries. For Mr. Carter, working with the On-site Consultation Program allowed him to cultivate a "workplace that is safe and injury free."
Source:
Mr. Glen Carter, President and Owner, Pikes Peak Steel, Inc.