R-V Industries makes continuous improvement part of their safety and health culture
Company: R-V Industries, Inc.
Location: Honey Brook, Pennsylvania
Employees: 215
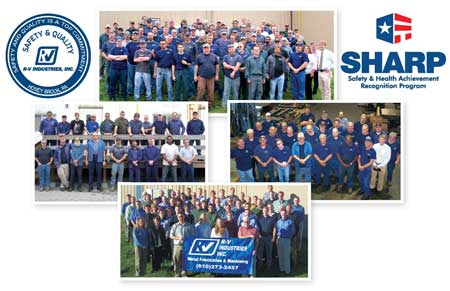
Success Brief:
In 2006, R-V Industries, Inc. began working with the On-site Consultation Program in Pennsylvania to improve its safety and health management program. Since 2006, R-V Industries has seen a significant decrease in injuries and illnesses, and has not experienced any recordable/lost-time injuries in over 650 days.
Company Description:
R-V Industries, Inc. (R-V) is an industrial process equipment manufacturer located in Honey Brook, Pennsylvania (NAICS 332313, Plate Work Manufacturing). Founded in 1974, R-V is dedicated to providing complete engineering and manufacturing services, including turnkey metal fabrication and machining operations for a variety of industries including biotech and pharmaceutical research, chemical, food and beverage, fossil power generation, nuclear power generation and waste disposal, oil and gas, and paper manufacturing.
The Situation:
As outlined in their corporate mission statement, R-V strives to improve the quality of life for each individual they employ. Safety (defined as freedom from danger, risk, or injury) is one of the company's core values. Part of that commitment to safety includes the belief that all workers have the right to work in a safe environment, and if changes need to be made to ensure the safety and health of employees at their plant, those changes are made.
R-V has worked intermittently with Indiana University of Pennsylvania's (IUP) On-site Consultation Program since 1996. In 2005, Robert Miller, R-V's Environmental Health and Safety (EHS) Director, requested the IUP On-site Consultation Program assist the site in the continued improvement of their safety and health programs.
The Solution:
R-V was interested in having IUP serve as an independent observer to ensure employees were safe. In January 2006, an IUP consultant conducted a visit to help R-V review their safety and health programs and provide assistance with specific hazards. In addition, IUP spent time answering questions of managers and employees. During 2006, IUP visited R-V's plant multiple times, working with them on improving their programs. Based on IUP's feedback, R-V improved their written safety and health program and focused on increasing employee involvement in the program's implementation. In addition to improving their written safety and health program, IUP recommended changes to specific areas, including proper use of personal protective equipment, and provided advice on engineering controls to eliminate hazards at their source.
Although some employees were initially leery of changes, R-V worked with IUP to initiate a cultural shift, implementing an effective safety and health program. With the support of R-V's Executive Management Team, Middle Managers, Team Leaders, and the employees began to appreciate the benefits of effective safety and health programs.
The Impact:
Although the On-site Consultation Program's Safety and Health Achievement Recognition Program (SHARP) was not an initial goal of R-V when it contacted IUP, by 2007, R-V decided to pursue SHARP and was awarded SHARP status on August 8, 2007. As part of this process, R-V communicated to their employees a vision for success which included a greater commitment to safety and health.
Part of these changes over the last several years has included significant investment in capital improvements specifically designed to make the work environment safer for workers. R-V also believes that when identifying and purchasing new equipment, that part of the process includes a risk assessment of the item in question, not simply going for the cheapest tools or machinery. One example was when R-V recently purchased a plasma burner, they specifically factored into the expense of the item appropriate engineering controls which would better protect both their employees and the environment. R-V also invested in fume extraction equipment to protect welders years in advance of the mandatory OSHA engineering controls compliance date to protect workers from hexavalent chromium fumes.
Another proactive change R-V initiated was conducting interactive biweekly Tool Box Meetings. These 15-30 minute presentations are made by a shop team leader who discusses a safety topic in a small group of 5 or 6 people. The team leaders have the latitude to add to the Tool Box Meeting's agenda and are encouraged to discuss issues and other safety topics relevant to the specific area and department in which they work. Any questions by the employees that the team leaders are unable to answer are written down and passed along to the EHS Director to address. Many times those questions lead to an expansion of the safety topics presented in the Tool Box Meetings.
Inspired by IUP's recommendations, R-V also initiated a process of continuous improvement to protect the safety and health of their employees throughout their company. In 2008, R-V began requiring the reporting of all incidents, and all near misses, no matter the severity. This process helped highlight many hazards of which R-V was previously unaware. In 2010, R-V began requiring a physical assessment with a licensed physical therapist before anyone is hired, with particular attention paid to ergonomic training and identifying whether the physical demands and work environment would be harmful to potential employees.
R-V's implementation of their improved safety and health programs has led to improved performance. As of February 2011, the facility has gone 685,000 hours without a lost-time incident and has managed to reduce its Days Away, Restricted/Transferred (DART) Rate to 0.53. The lessons learned and improvements have carried over to all the facilities owned by R-V. In 2002, R-V, corporate-wide, had 41 OSHA recordable injuries and 132 reported injuries. In 2010, only 8 reported injuries occurred among all three of their facilities.
Through their commitment to safety and health, R-V became self-insured. This change was motivated by both financial considerations and by R-V's belief that everyone in the company would benefit by taking ownership of their safety and health.
For R-V Industries, working with the On-site Consultation Program at IUP has made this company more aware of the importance of injury and illness prevention programs, given it another set of eyes to look over processes, and has enhanced R-V's corporate philosophy of continuous improvement. According to Mr. Miller: "Our work force is our greatest asset, and we have some of the finest craftsmen in the industry. It is our responsibility to keep them safe by having freedom from danger, risk, or injury in the workplace. Maintaining a safe and healthy work environment is not just an idea, it is a top priority. No function or process at R-V Industries is so critical as to require or justify a compromise of safety and health."
Source:
Mr. Robert Miller, EHS Director, R-V Industries, Inc.
Ms. Marlene Haws, Vice President of Finance, R-V Industries, Inc. (March 2011)