Ergonomics Case Study: Missouri Slope Lutheran Care Center
Company or Organization: Missouri Slope Lutheran Care Center
Administrator/CEO: Reier Thompson
Safety and Health Manager: Jon Kapp
Industry: Skilled Nursing Facility – NAICS Code: 6231
Task: Resident care
Employees: 450-500
History:
Missouri Slope Lutheran Care Center was established in Bismark, North Dakota in 1967. They have operated as a Skilled Nursing facility since that time, growing to a 258-bed facility, with an additional 64 unit assisted living facility.
In 2016 the company was exploring the possibility of remodeling their campus to modernize facilities and provide individual, private rooms for their residents. Due to the fact that they were at 99% capacity, closing sections of the facility for remodel would displace their residents, so the company decided to purchase land and construct a new facility, with the intent of coming back and remodeling the original campus after the new facility was completed.
Phase 1 of the project is complete and consists of a four story, 192 bed Skilled Nursing facility. The new facility was certified in November 2021 and fully occupied by November 2022.
As the company was providing upgraded services as part of their new location, and had maintained the same number of staff, the new facility incorporated efficiency into its design. The building is designed as an "X" with all essential services located in the hub on each floor (i.e., nursing stations, dining rooms, and activity centers), and resident rooms in the wings.
Phase 2 will include a Basic Care/Assisted Living facility and Phase 3 will be an Independent Living facility.
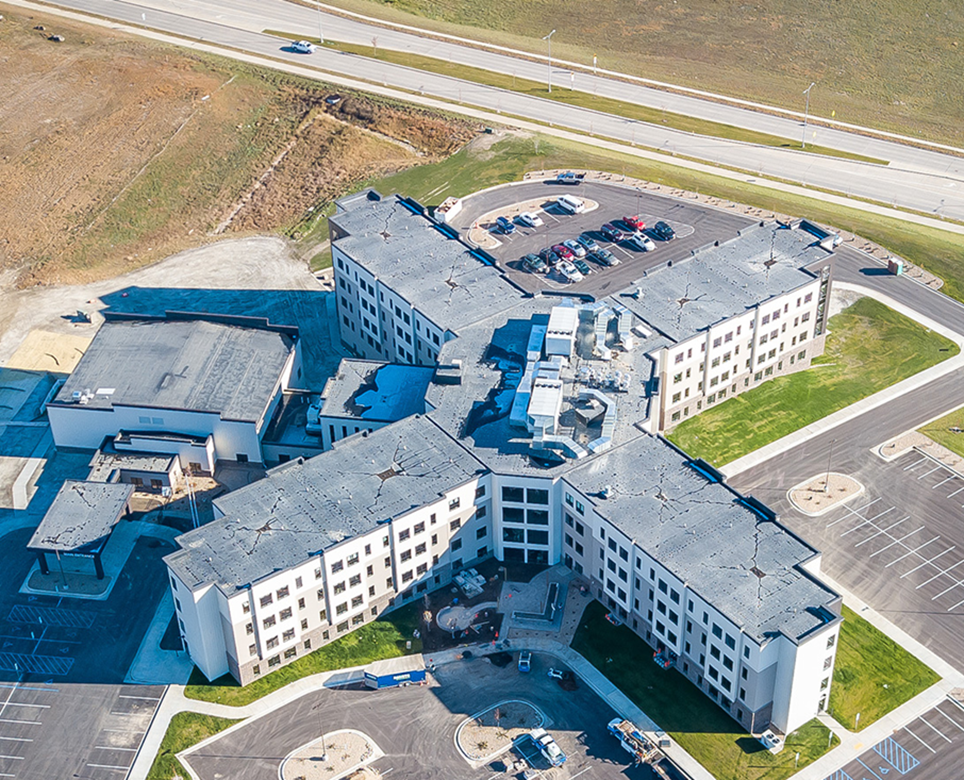
Figure 1 – The New Missouri Slope skilled nursing facility.
The Challenge:
In the mid to late 1990s administrators realized that employees at Missouri Slope had a 1 in 7 chance of suffering a work-related musculoskeletal injury, and their Worker’s Compensation premiums were at an all-time high due to the number of injuries that were occurring. In 1997, premiums paid were over $425,000 with a surcharge of 55.7% due to their experience rating.
The Solution:
In 2007 the company implemented a “No Lift” policy and began requiring employees to use mechanical lifts when lifting/transferring residents. This small change in procedures resulted in modest reduction of employee injuries and worker’s compensation rates. As of 2010 their experience rating has dropped to the point where they were receiving discounts on their annual Worker’s Compensation premiums (See Table 1).
Year: | Experience Rate Discount/Surcharge: |
---|---|
2000 | 33.8% |
2001 | 14.9% |
2002 | 26.3% |
2003 | 21.4% |
2004 | 14.6% |
2005 | 4.6% |
2006 | 0.9% |
2007 | -13.8% |
2008 | -26.0% |
2009 | -34.9% |
2010 | -28.5% |
2011 | -30.0% |
2012 | -10.4% |
2013 | -13.9% |
2014 | -4.0% |
2015 | -3.5% |
2016 | -2.3% |
2017 | -21.8% |
2018 | -25.5% |
2019 | -16.4% |
2020 | 5.4% |
2021 | -2.8% |
2022 | -20.8% |
2023 | -37.6% |
With the construction of a new facility Missouri Slope was able to incorporate efficiency and safety during the design phase. Below is a list of improvements and controls the facility has implemented to prevent employee musculoskeletal disorders (MSDs).
Resident Room Design:
Every resident now has their own private room. Incorporated into each room is an electric ceiling lift for resident transfer. The ceiling lift allows for assisted transfer of residents to any point in the room, including the bathroom and the shower.
Special waivers were required to design and build bathrooms walls that do not extend to the ceiling. This allows the ceiling lift to travel uninterrupted from the resident’s bedroom directly into the bathroom.
Additionally, the shower curtain rod is split in the middle and hinged on the ends, allowing it to open so the ceiling lift can travel directly into the shower. (See Figures 2-4).

Figure 2 – A ceiling mounted lift in a resident’s room.
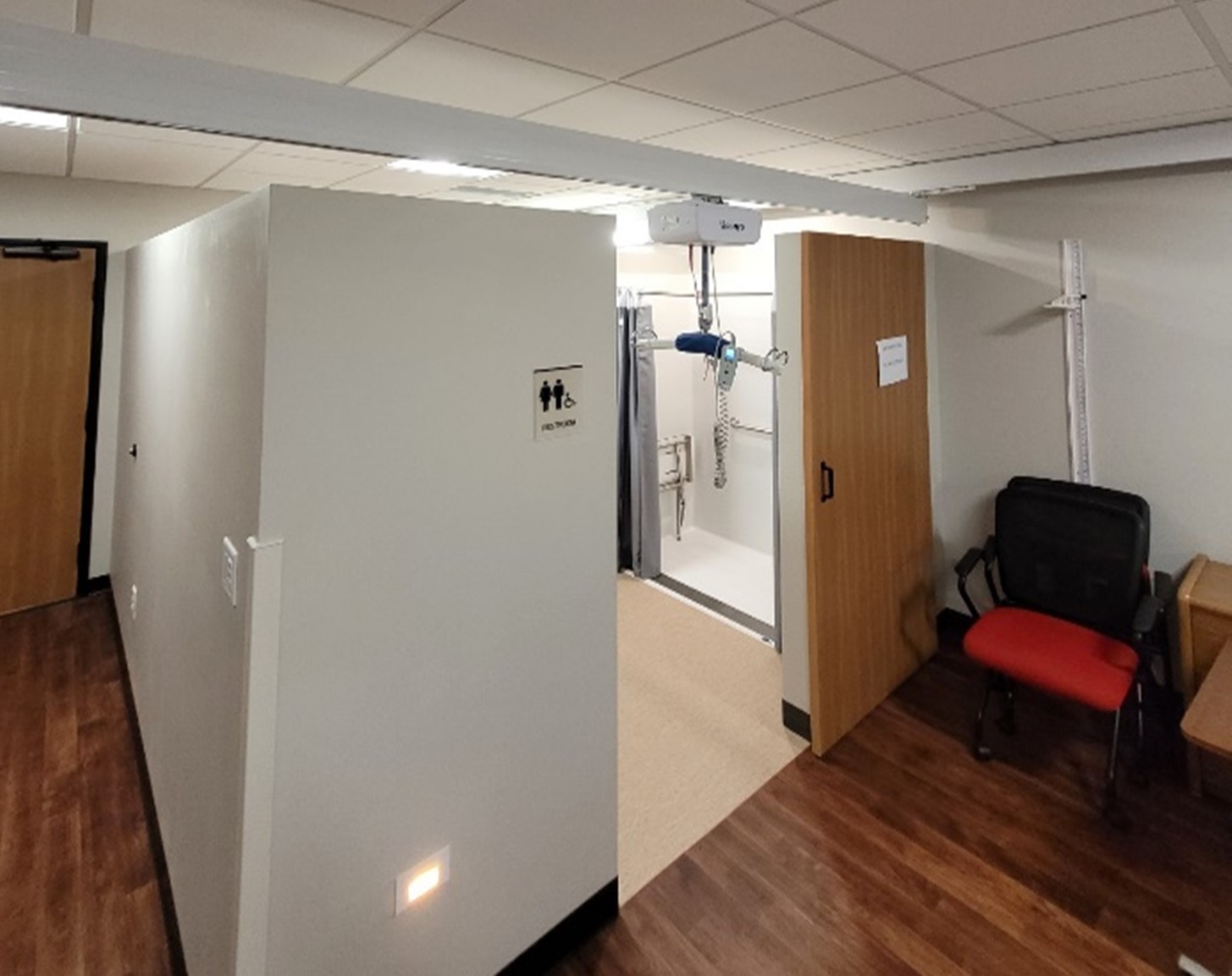
Figure 3 – Bathroom design in the new facility showing the modifications that allow the ceiling mounted lift to move freely throughout the room.
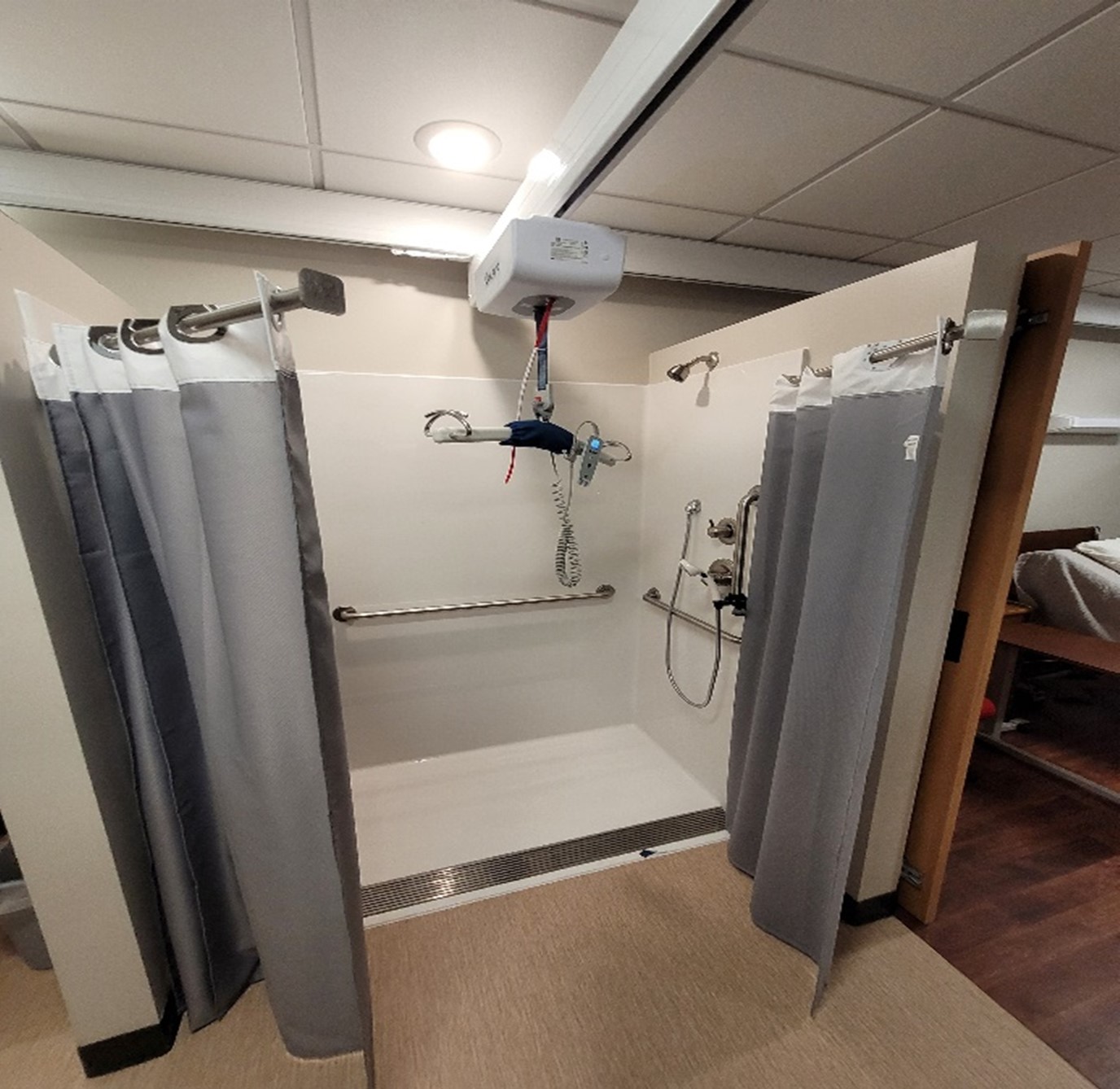
Figure 4 – The shower stall with movable curtain rods that allow the ceiling mounted lift to move freely in and out.
Installation of the ceiling lift, along with the new room design, eliminated the need to lift the residents into a chair, move them to the bathroom, and lift them again with a mobile lift. Additionally, the nurses can attach a scale to the ceiling lifts and weigh residents as needed, again eliminating the need for multiple lifts.
Nursing Department:
Missouri Slope continues to implement the “No Lift” policy they started in 2007. Since then, they have continued to invest in mechanical lifting equipment (e.g., ceiling lifts, mobile full body lifts, and sit to stand lifts) for use in resident transfers. They also require that two employees assist with transfers using a lifting device.
All lifts are battery-powered for the lifting portion and manual for movement. The ceiling lift requires minimal manual effort to move around the resident’s room.
Training for new hires includes a body mechanics class and education on the different types of lifts used in resident care areas. New employees learn proper techniques by performing transfers with each other. This allows them to gain experience before they perform actual transfers as well as helping them understand what the resident experiences while being transferred to, and while using, a lift. Training is performed in a skills lab designed exactly like a resident’s room.
Medical carts are equipped with adjustable laptop platforms so individual nurses can adjust them to their own individual needs.,
To eliminate staff injuries from pushing large garbage cans and laundry carts through the facility, Trash Chutes and Laundry Chutes were installed on each floor. The empty directly into the trash compactor and laundry room, respectively, on the lower level. For garbage that is collected in cans, the trash compactor is equipped with an automatic arm for lifting and dumping large trash cans.
An additional safety mechanism was added in 2023 to the laundry chute. An open door to the laundry chute initiates a buzzer, which notifies the lowest level (sorting room) of items being sent down the chute. An automatic locking feature engages when one door is open to prevent others from being opened at the same time. At the bottom of the laundry chute is a slide panel and door which opens onto a sorting table. This assists in creating a soft landing for those working in the sorting room. (See Figures 5 & 6).
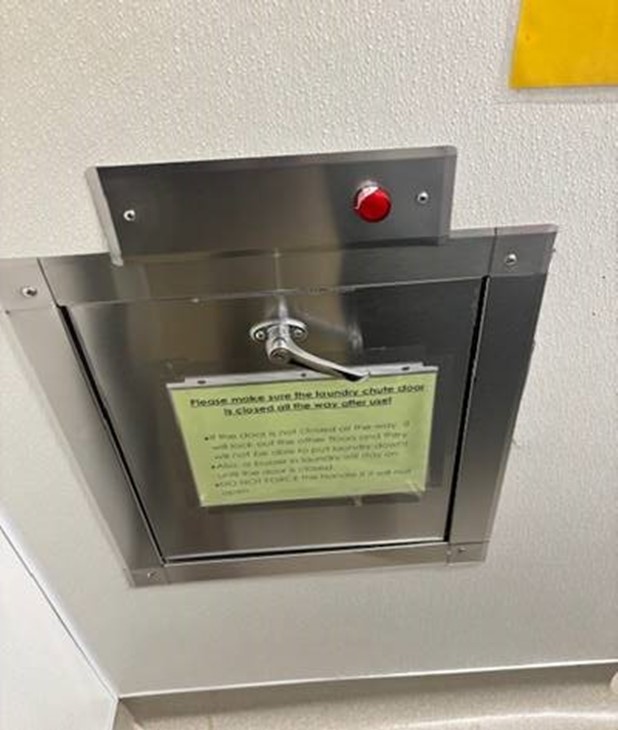
Figure 5 – A laundry chute with auto locking mechanisms.
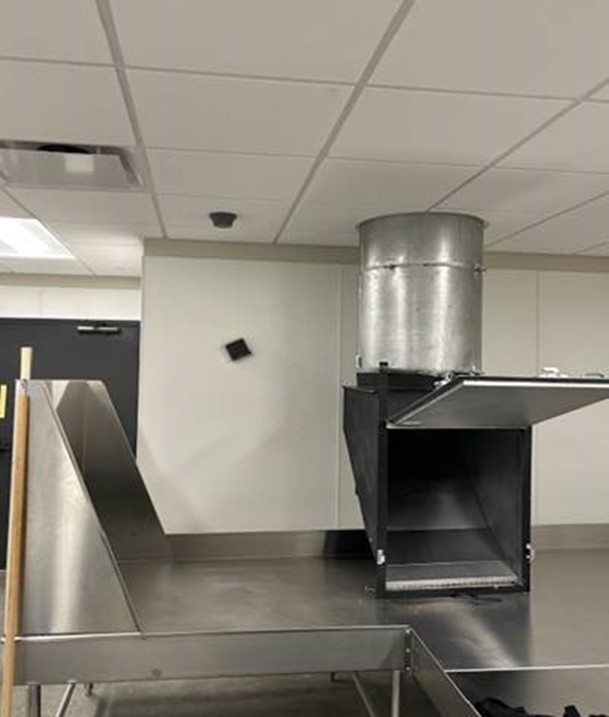
Figure 6 – Laundry chute exit onto the sorting table.
Laundry Department:
To prevent ergonomic related injuries in the Laundry Department Missouri Slope installed taller sorting tables and provided anti-fatigue mates for the employees to stand on.
Additionally, they started using two new types of laundry carts. For wet laundry they use a cart with a spring-loaded bottom. As the laundry is picked out of the cart the bottom rises so the employees do not have to bend over the side. The clean linens carts have cutouts on both sides that allow employees to open the gate and easily reach in and lift items out (See Figures 7 & 8).
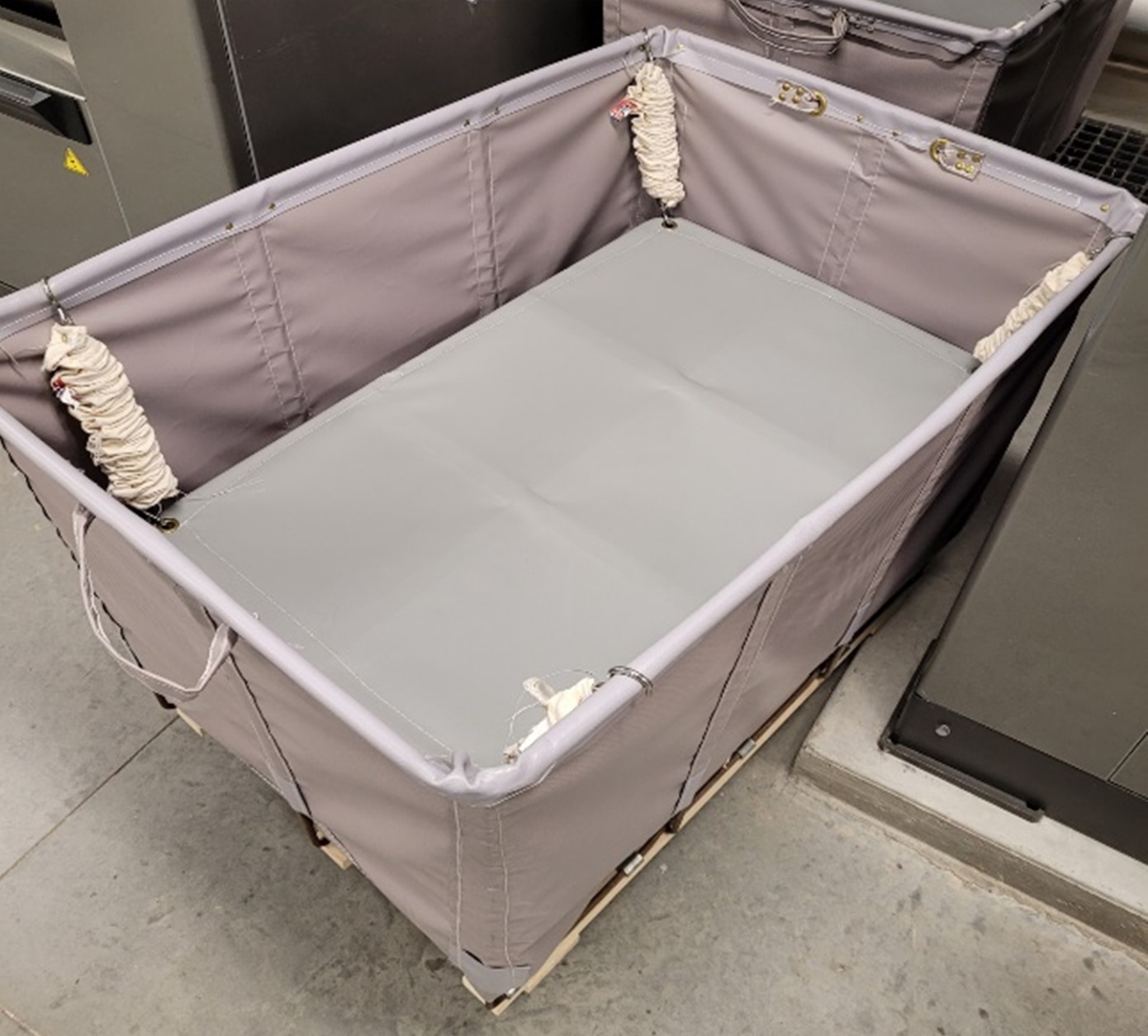
Figure 7 – Laundry cart with a spring-loaded bottom.
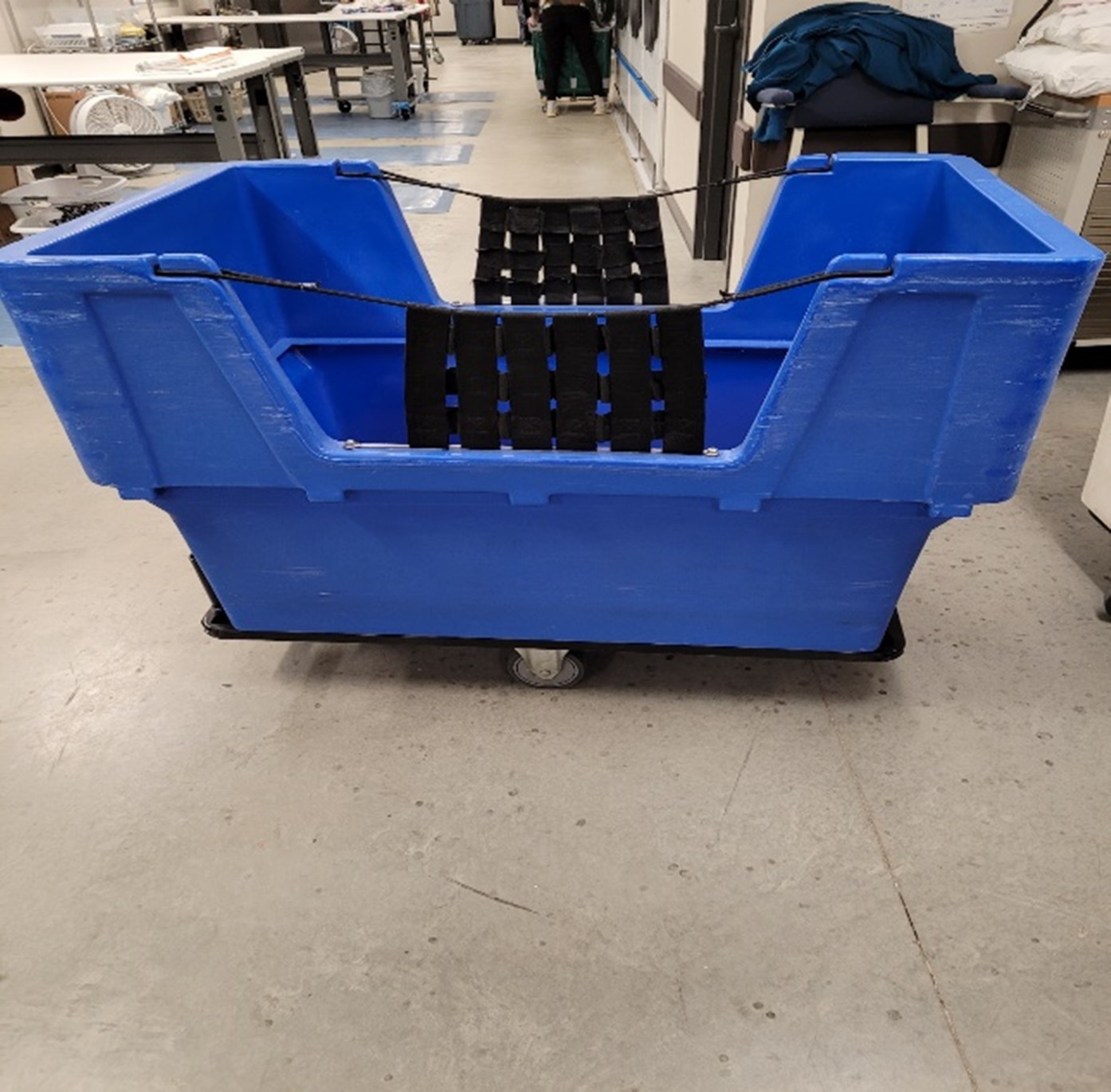
Figure 8 – Clean linen cart with cut away sides for easy access.
Environmental Services:
To reduce strains from repetitive motions while cleaning (i.e., mopping floors) Missouri Slope purchased stand behind and riding equipment for cleaning larger areas (e.g., hallways, dining rooms, the atrium, and the chapel). These pieces of equipment not only reduce repetitive motions and manual pushing/pulling but reduce the amount of time needed to complete the cleaning.
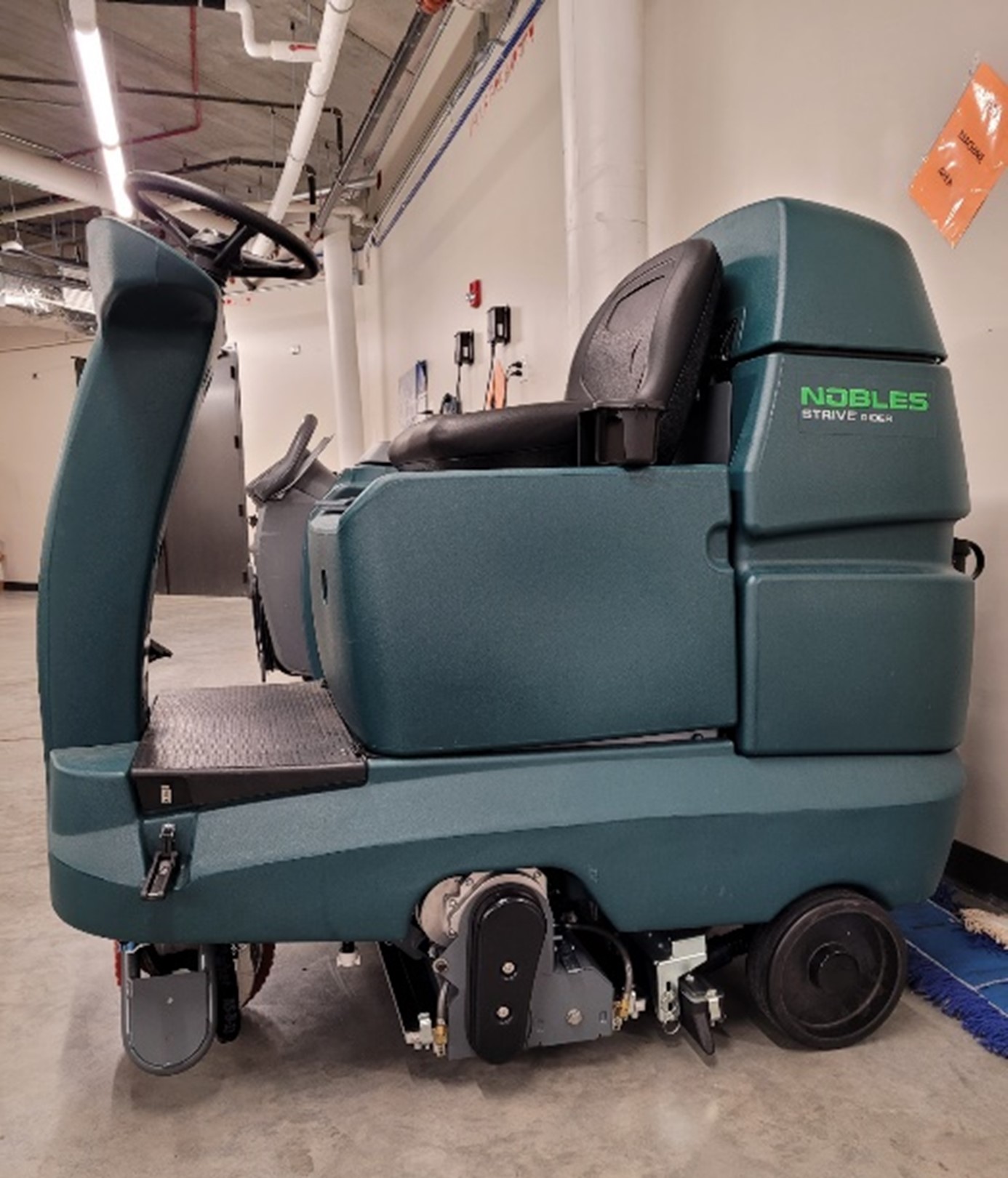
Figure 9 – Riding floor cleaner.
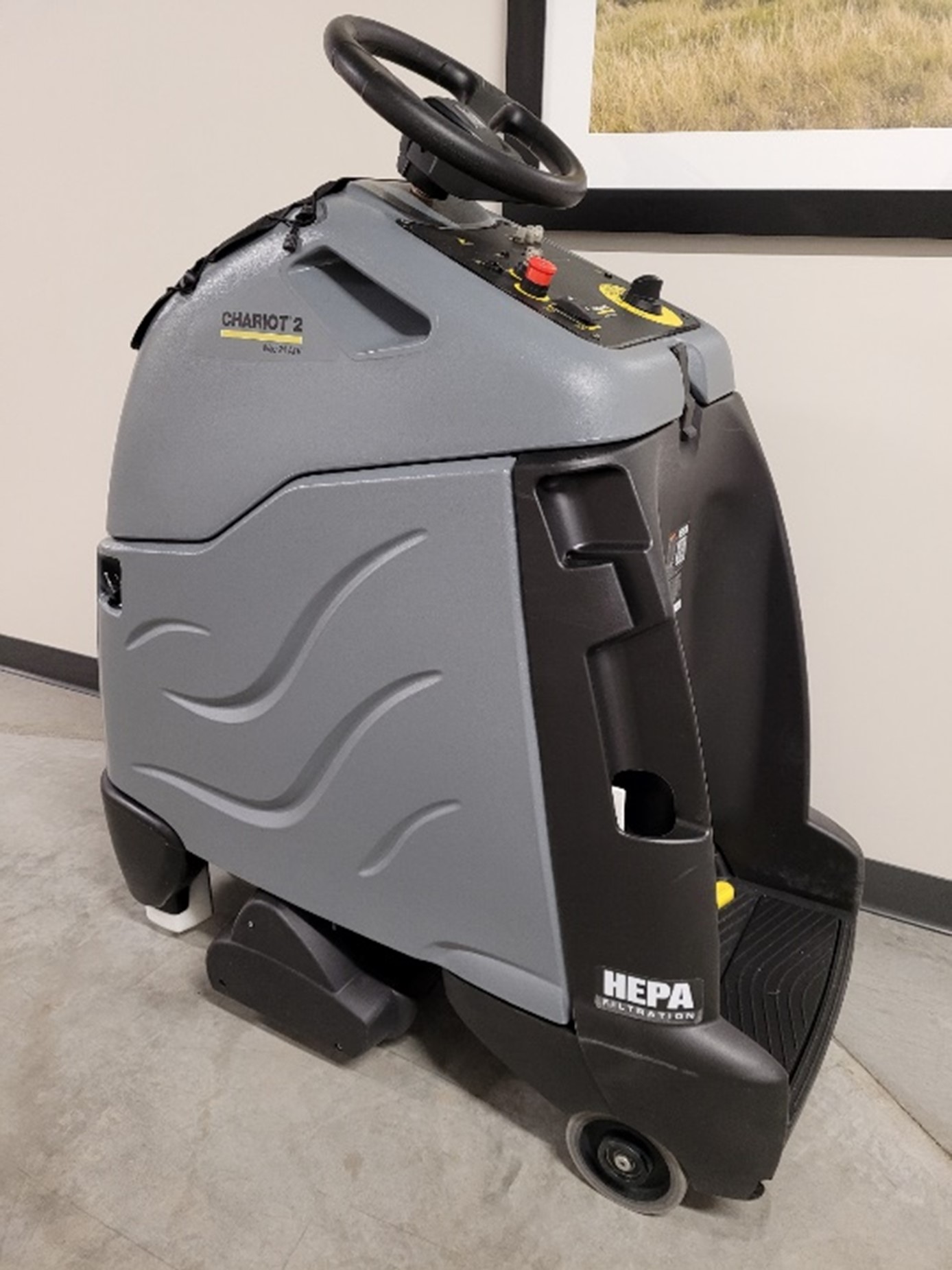
Figure 10 – Stand behind floor cleaner.
Kitchen:
To assist the kitchen staff Missouri Slope installed pot fillers that allow staff to fill cooking pots with water directly on the stove eliminating the need to fill large, heavy stock pots and carry them to the stoves to fill the cooking pots (See Figure 11).
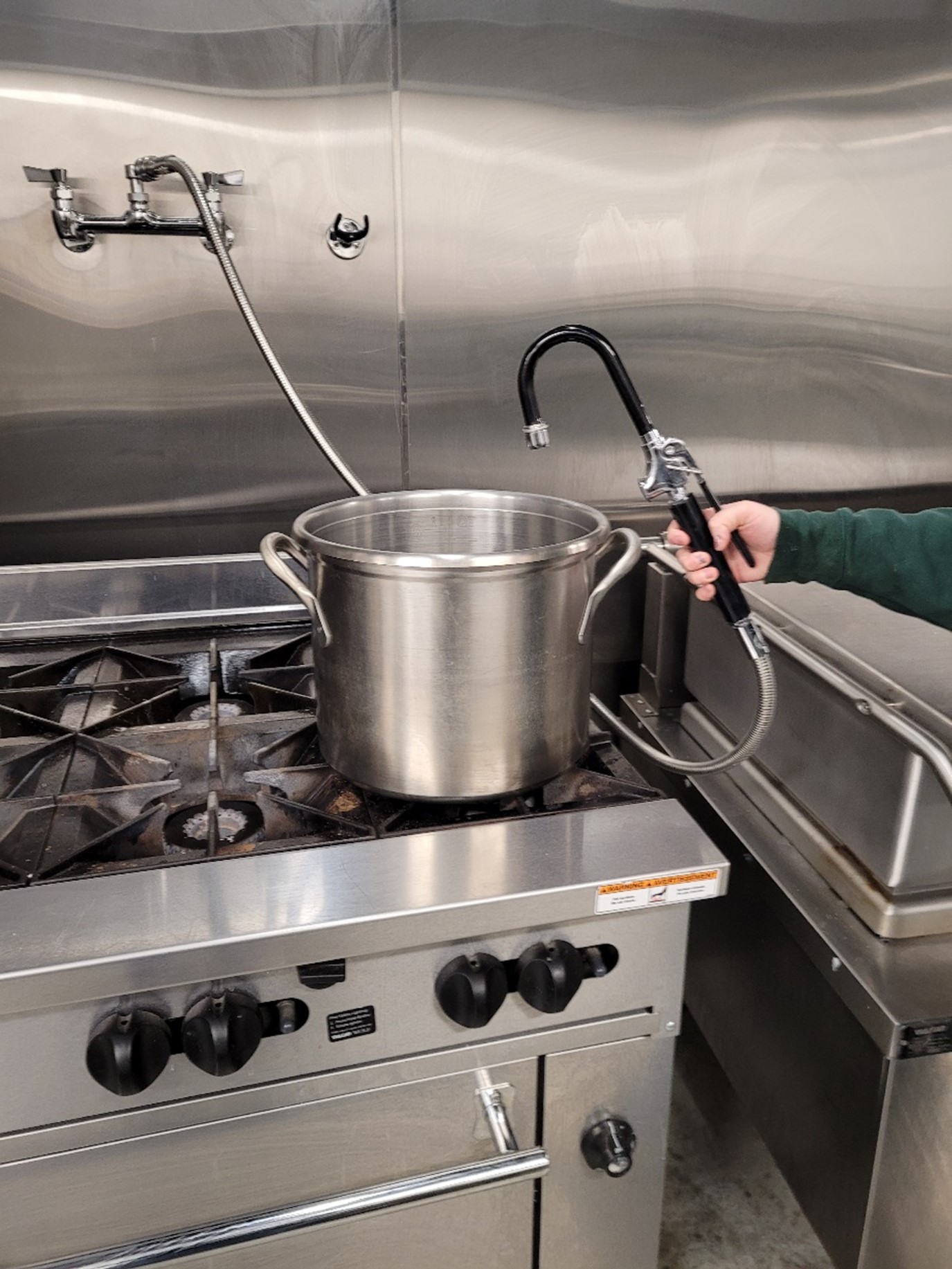
Figure 11 – Pot filler in the kitchen.
Office Workstations:
Administrative office staff have the option to use ergonomic equipment which is available upon request. Available options include:
- Sit-to-stand desks
- Anti-fatigue mats
- Adjustable office chairs
- Adjustable computer stand for the desktop
- Adjustable computer monitor stands
Staff involvement:
One of the most important aspects of Missouri Slope’s ergonomics program has been allowing the employees to participate and provide suggestions and feedback. This has given the employees a stake in the program and helped make safety a part of the culture from the bottom to the top.
Facility management is committed to providing employees with the tools, resources, and the processes needed to bring their ideas to fruition. To that end Missouri Slope has established a safety committee that meets monthly and provides a forum for employees to share feedback and ideas (e.g., instillation of the laundry chutes and the doorbell was an employee idea). The committee reviews injuries, near misses, and suggestions for improvements. They then develop a plan for implementation of corrections and ideas. As an example of their commitment, management has placed their trust in the committee and employees to get the job done. Missouri Slope has also established a safety council made up of executive leadership that meets quarterly with the Safety and Health Manager to review the results of the Safety Committee meetings. The council will assist in approving any new initiatives and discussion/resolution of higher-level topics.
Every month Missouri Slope holds a director’s meeting where safety is a regular agenda item. Each Director is required to report out on safety concerns, outcomes, near misses, and good catches. This helps build into the Safety Committee by giving them the resources and direction they need to implement improvements in each department.
Missouri Slope has also taken a proactive approach to safety by performing a Job Hazard Analyses (JHA) for non-routine tasks and new equipment and providing “Good Catch Reports” for employees to report hazards and safety concerns before they become problems.
Missouri Slope has also applied for and utilized Ergonomic Initiative Grants through North Dakota Workforce Safety Insurance (NDWSI). The program allows facilities to purchase ergonomic equipment (e.g., sit to stand lifts, sit to stand desk, full body lifts, posture correctors, anti-fatigue matts, and ergonomic chairs) approved by NDWSI and submit the invoice for full reimbursement from the grant program.
They also continue to develop and enhance their body mechanics program, along with a stretch and flex program, for all employees in a continued effort to reduce injuries.
Impact:
Currently, Missouri Slope has an experience rating/discount of -13% with total premium of $79,829 (See Table 1). The success of the program has allowed the company to invest dollars into more safety programs and equipment.
Implementation, and continued improvement, of the facility’s ergonomic program, along with employee engagement, has reduced and almost eliminated employee musculoskeletal injuries related to resident lifts/transfers, Average injury rates for 2021 – 2023 are 64% below the national average for Skilled Nursing facilities (2022 BLS Rates) (See Table 2). Additionally, integrating the ceiling lifts into resident’s rooms has reduced resident injuries during a lift/transfer to zero, thus resulting in not only a reduction in employee injuries, but improvement of resident safety and overall efficiency.
Year | Total Case Incident Rate (TCIR) | Days Away/Restricted Duty (DART) |
---|---|---|
2021 | 7.1 | 4.2 |
2022 | 3.1 | 1.5 |
2023 | 4.0 | 3.4 |
3-year Average | 4.7 | 3.0 |
Bureau of Labor Statistics (BLS) national Skilled Nursing Facilities (SKF) Rates | 13.1 | 10.8 |
% below National AVG | -70% | -69% |
To encourage continued employee involvement, Missouri Slope has implemented awards/prizes for their employees as incentives for reporting near miss/good catch reports and in completing monthly safety walkthrough assessments. The team at Missouri Slope seeks to improve upon its culture of safety each year with input from all levels of the organization.
As part of their ongoing commitment to employee and resident safety Missouri Slope continues to evaluate and purchase ergonomically appropriate equipment and improve their training and best practices in all departments.
Implementing a change in the resident transfer policy also prompted the company to apply for membership in OSHA’s Voluntary Protection Program (VPP). They have now been a VPP Star site for 15 years and are the only VPP Skilled Nursing facility in the region. With a simple change to the company’s policy, Missouri Slope embarked on a multi-year process that culminated in a facility wide ergonomics program, continues to evolve and improve each year, and has resulted in few to no work-related injuries and zero resident injuries from resident lifts/transfers.