Troy Industrial Solutions Stays SHARP and Celebrates 5 Years of Zero Deficiencies
Company: Troy Industrial Solutions (formerly known as Troy Belting and Supply Company)
Location: Watervliet, New York
Employees: 70
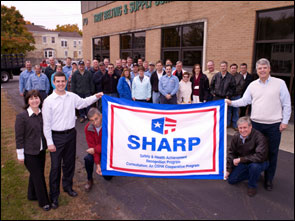
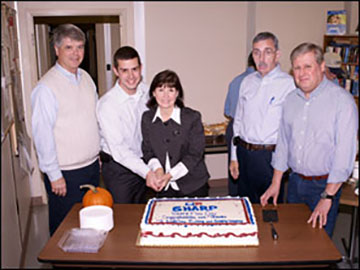
NAICS Code: 811310 - Commercial and Industrial Machinery and Equipment Repair and Maintenance
Success Brief:
Over the last 5 years, there have been no lost time incidents at Troy Industrial Solutions' facilities or job sites, and no safety and health hazards found during OSHA's On-Site Consultation Program Safety and Health Recognition Program (SHARP) renewal visits.
SHARP recognizes small business employers who operate an exemplary injury and illness prevention program. Acceptance of a worksite into SHARP from OSHA is an achievement of status that singles out a worksite among their business peers as a model for worksite safety and health. Upon receiving SHARP recognition, OSHA exempts your worksite from OSHA programmed inspections during the period that your SHARP certification is valid.
These safety and health successes have earned Troy recognition as a SHARP participant, an honor held since in 1999. Over Troy's time in SHARP, the company has consistently met OSHA's high safety and health standards.
Company Description:
Troy Industrial Solutions employs 70 workers at its Watervliet, New York, facility and celebrated its 150th anniversary in October 2012. Established in 1862 as the J. Leroy Pine Company and renamed Troy Belting and Supply in 1886, the company originally supplied belting products to the mills and factories in the Northeastern United States. In the ensuing years, they expanded their business to provide service and repair for a variety of electromechanical machinery used in the mining, aggregate, cement, chemical, food and beverage, paper and pulp, power generation, and water and waste management industries. This machinery ranges from conveyer belts and related equipment to electric motors, pumps, blowers, and gear reducers.
The Situation:
Deficiencies in safety documentation and processes were increasingly impacting Troy's ability to address administrative, operational, and management requirements. Ripple effects included delays in replying to requests from insurance carriers for details on the safety program and from customers. "Our top priority is to make sure everyone goes home at the end of the day safe and free from injuries. Making safety a high priority in daily work activities at all levels of the company enabled us to address deficiencies in our workplace, avoid injuries, save money, and be more competitive," said Troy General Manager, David Barcomb. "We needed to improve our safety program and strengthen our company-wide safety culture."
The Solution:
Based on a customer's recommendation, Troy contacted the New York State Department of Labor (NYS DOL) and requested assistance from OSHA's On-site Consultation Program, administered by the NYS DOL, Division of Safety and Health (DOSH). The OSHA On-site Consultation Program offers free and confidential safety and health advice to small and medium-sized businesses. In this program, which is available in all U.S. states and several territories, consultants from state agencies or universities work with employers to identify workplace hazards, provide advice on compliance with OSHA standards, and assist in establishing injury and illness prevention programs.
The initial consultation visit took place in 1997. During this visit, the consultant worked with Troy to educate them on the benefits of consultation, identified several hazards, and suggested methods for abating or eliminating them. As expected, proper documentation and recordkeeping of training records, safety committee meeting notes, Material Safety Data Sheets, and incident investigation reports were concerns. In the shop operations, however, proper guarding of equipment, job hazard analysis, and expertise in identifying workplace hazards were key areas to address.
The Impact:
Hazards identified during the initial On-site Consultation visit were corrected, but that's not all that Troy did. Troy used information provided by the consultant to re-design their safety and health programs and to prevent identified hazards from reoccurring. Today, Troy has a proactive approach to its comprehensive injury and illness prevention program, implementing several elements to reach this point. Having the management team's full support and participation made for a good beginning. Committing full-time resources and establishing a safety committee, comprised of staff from all levels of the company, were important steps. Holding regular safety meetings helped to get employees to participate. Updating company safety manuals, giving new employees a safety orientation, and ensuring everyone attended regular safety training also played a role. The combination of the efforts implemented by Troy demonstrated management's commitment; helped get everyone to take an active role; improved worker morale, retention, and attendance; and saved money that could be reinvested in the business. "Troy has become a preferred contractor to work on-site for customers based on a superior safety record," said Jason W. Smith, President, Troy Industrial Solutions.
After working with NYS DOL, the company first earned recognition as a SHARP site in December 1999 and was awarded its most recent re-approval on February 15, 2013. "I would be remiss if I didn't mention the work of Bruce Flagler," Barcomb continued. Appointed Safety Coordinator in 2008, Flagler was instrumental in taking the Troy Safety Program to a new level of competency. Shortly after his appointment, he was diagnosed with amyotrophic lateral sclerosis (ALS). He continued to work diligently up until his death in 2010. "Bruce was an advocate for the safety of his fellow employees, a 39-year veteran of Troy, and a proud Vietnam Veteran," Barcomb recalls. "We continue to work hard on our safety program in his honor and to pay tribute to Bruce's relentless compassion for the safety of his fellow workers. His presence is greatly missed."
To celebrate their 2009 On-site Consultation Program SHARP recertification, a cake cutting was in order. Shown from left to right are Dave Barcomb, General Manager; Jason W. Smith, President; Karen E. Smith, Chairperson, Bruce Flagler, Safety Coordinator; and Geoffrey Holodook, NYS DOL Senior Safety and Health Consultant.
As a result, Troy's Workers' Compensation Insurance rates declined from $69,780 in 2010, to $63,958 in 2011, and to $51,934 in 2012, returning $17,846 that could be put to better use making further improvements to the safety and health programs.
"Some benefits of having everyone working in a safe environment are not hard to measure," said Jason Smith. "Yes, our workers are very proud of our safety record, and they appreciate the commitment our company has made to safety. General liability and workers compensation insurance premiums are favorable. And let's not forget the value it brings to our customers who enjoy dealing with a company with a solid safety record. But how do you measure the best benefit of all - seeing the people who walked in the door in the morning go home to their families after their shifts, tired but safe?"
Source:
David R. Barcomb, General Manager, Troy Industrial Solutions
Jason W. Smith, President, Troy Industrial Solutions