Steel Company Implements Operator Inspection Program to Improve Cutting Torch Safety
State: Texas
Company: Chaparral Steel
State: Texas
Company: Chaparral Steel, Texas
Industry: Steel Recycling/Steel Manufacturing - SIC Code: 3212
Employees: 1,010 employees
Success Brief:
After Chaparral Steel started an operator inspection program that included using an inexpensive plastic spray bottle containing a solution of soap and water to spray on cutting torches and the associated piping to find leaks, the company experienced a 90 percent reduction in leaks.
The Problem:
Cutting torches are used in many facets of the steel industry. Leaks in the torches and the associated hoses and connections can lead to explosions and cause serious injury, usually to workers' hands. While such leaks may develop in any part of a torch system, they generally occur at the joints and connections.
In 2004, a Chaparral Steel employee's hands were severely injured when using a cutting torch. The incident involved a worker who was cutting scrap steel. After he had finished cutting a piece of scrap with a cutting torch, he used his left hand to push it into the scrap bucket. As he reached past the lighted torch (about 4" - 6" away), oxygen that had collected in his glove ignited and blew the glove off his hand. (See Figure 1.) He received first- and second-degree burns on his hand and fingers.
The incident investigation revealed that the oxygen hose had a leak either where the hose ferrule had been crimped or a few inches downstream. The major root cause findings were that oxygen had been leaking from the hose and that the worker did not inspect the torch for leaks before using it. The incident investigation also revealed that the hose ferrule had been crimped with the wrong die. After the accident, Chaparral identified an inexpensive and effective solution for identifying these leaks.
The Solution:
According to Bobbie Angelo, Mill Operations General Manager at Chaparral, leaks occur in torches with repeated use in industrial environments. Eliminating all circumstances that could damage torch lines and devices is difficult. Chaparral has instituted an operator inspection process for workers to verify that all torch components are in proper working order. Before an operator uses a torch, he inspects it including the hoses, connections and valves allowing the worker time not only to find conditions that could lead to an accident but also to think about safety. Bobbie noted that "Over time this thought process becomes a habit and supports an attitude of safety that helps to eliminate risks of an accident. Habit and job safety are very closely related. We know that individual habits influence safety performance. The operator inspection process is just one form of a safe work habit that reflects positively in employees' overall safety attitude and makes for a safer work environment."
The operator inspection process includes spraying the hose and all torch fittings, connectors, weld piping and gauge end fittings with a solution of soap and water pumped out of a plastic spray bottle costing less than $2.00. Chaparral keeps a spray bottle clearly marked "Soap and Water" at every torch station. When the soap and water solution is sprayed on a torch and hits a leak, it bubbles. If the hose is under pressure, the test results are immediate. (See Figure 2.) Chaparral uses only soap and water testing solutions that are approved for use by equipment manufacturers because incompatible solutions can lead to corrosion of the cylinder valve and cutting hose. Leaky hoses and fittings are not always repairable and may need to be replaced when a leak is detected. A competent person—one who has been trained in torch cutting operation and equipment repair—can determine if a hose is repairable.
The Impact:
Chaparral Steel wanted to find a way to identify the leaks that caused serious injury to workers who used cutting torches. So the Company began an operator inspection program that involved the use of an inexpensive spray bottle containing a soap and water solution.
When the safety team conducted weekly and daily safety audits in 2003, they found leaking torches everywhere. After the operator inspection program began in 2004, they found 90-percent fewer leaking torches, regulators and hard gas piping. Prevention and/or reduction to that exposure were Chaparral's goals.
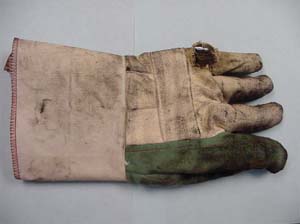
Figure 1. Glove damaged by leaking torch
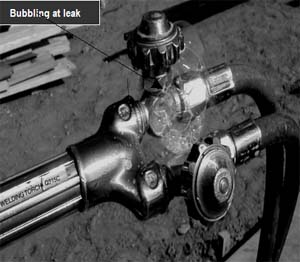
Figure 2. Bubbling at leak
Sources:
- Ron Herring, Safety Manager for Chaparral Steel (August 2005)
- Developed through the OSHA and The Steel Group Alliance.