Long Trail Brewing Company sets craft-brewing industry's workplace safety benchmark
Company: Long Trail Brewing Company
Location: Bridgewater Corners, Vermont
Employees: 117 full-time workers at two locations, Long Trail (81) and Otter Creek (36)
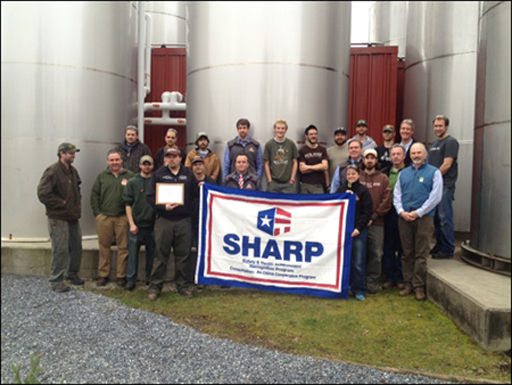
Industry: NAICS 312120, Breweries
Success Brief:
In 2010, the Long Trail Brewing Company (Long Trail) earned recognition in the Occupational Safety and Health Administration (OSHA) Safety and Health Achievement Recognition Program (SHARP). This made Long Trail the first brewery in the state of Vermont to receive this award, which recognizes small business employers who operate an exemplary injury and illness prevention program, and only the third brewery in the country to achieve this status. Acceptance of a worksite into SHARP is an achievement that singles out a worksite among its business peers as a model for worksite safety and health. In 2012, Otter Creek Brewing Company (Otter Creek), a wholly owned subsidiary of Long Trail, followed their parent company's example and raised the SHARP flag at their Middlebury, Vermont brewery. At the time of writing, Long Trail and Otter Creek are two of the three breweries in the United States actively participating in SHARP.
Long Trail and Otter Creek were able to achieve SHARP recognition by working with OSHA's On-site Consultation Program through Project WorkSAFE. The OSHA On-site Consultation Program offers free and confidential services to small and medium-sized businesses and is available to employers in all U.S. states and several territories. Consultants from state agencies or universities work with employers to identify workplace hazards, advise on compliance with OSHA standards, and assist in establishing injury and illness prevention programs. Project WorkSAFE is a division of the Vermont Department of Labor, Vermont Occupational Safety and Health Administration (VOSHA).
Prior to working with Project WorkSAFE, Long Trail and Otter Creek did not have an injury and illness prevention program in place to protect their workers. Safety procedures were placed in piecemeal fashion for its highly manual processes. As the business expanded, the senior management realized that the lack of an injury and illness prevention program would hinder its future growth and place employees at risk. In less than 4 years working with Project WorkSAFE, Long Trail successfully implemented injury and illness prevention programs at both breweries which both were eventually recognized as SHARP participants, and in doing so also transformed the companies' attitudes toward safety.
Company Description:
Founded in 1989, The Long Trail Brewing Company has strong roots in the state of Vermont and currently produces the number one selling craft beer in the state. In 2012, Long Trail produced approximately 130,000 barrels of four different brands of beer at its two locations, Bridgewater Corners and Middlebury, which are distributed and sold in 15 states in the northeastern United States. The company takes pride on its award-winning beers, constant innovation, industry-leading environmental initiatives, and maintaining a healthy and happy workforce.
The Situation:
Breweries are considered a high-hazardous industry as it is inherently fraught with multitudes of hazards. With the use of extremely hot liquids, pressurized tanks, caustic chemicals, fast moving machinery, frequently wet floors and fork-lifts weaving in and out of the production floor (just to name a few common risks), making beer can have safety risks which can be very dangerous if not controlled.
When a new management team took over Long Trail in 2005, they found that workplace safety programs in place were insufficient. Prior to the new management's arrival, expansion and growth had been top priorities, while safety was less of a focus. As a result, employees were not able to identify what was right or wrong with regard to workplace safety. Decisions were often made on the fly and as a result, product quality, employee safety and plant efficiencies were all at risk.
The need for a comprehensive injury and illness prevention program was clearly identified following an enforcement inspection visit from VOSHA. Management viewed the visit as an opportunity to reverse the direction for safety and follow a new path. This path included contacting Project WorkSAFE.
Project WorkSAFE's initial visit discovered over one hundred items that needed to be fixed. Ultimately, Project WorkSAFE would review both plants in detail, working from the outside of the buildings to the inside. They looked at flow patterns of trucks, workers, and guests visiting each facility. They discovered several areas and patterns that were unsafe and needed immediate correction. Once they moved into the buildings, they looked at all utilities that served the needs of each plant. On the surface, they appeared to be in decent shape; however, closer inspection revealed a lack of preventative maintenance. The same applied for the equipment that was being run. Much of the machinery had one or more safety issues that needed to be fixed immediately.
The Solution:
The company decided that if it was going to correct all of the safety issues within the plants, they would have to make an effort to develop a world-class injury and illness prevention program; one that would serve as a model for the industry. All of the safety procedures needed to run a safe facility directly linked every department in one or more areas, and Standard Operating Procedures were developed for each department. A safety manager was hired, along with 2 additional full-time employees to cover safety at both breweries. Also, a safety team was established where employee representatives from every department meet weekly.
As a result of this effort, new policies were implemented which required multiple mechanical redundancies and fail-safes. Maintenance tracking software was used to ensure that their equipment would remain intact and safe. Safety issues would be tracked from shift to shift, by computer. Also, a new storage facility was constructed which helped alleviate congestion on the production floor. In all, Long Trail spent millions of dollars in improvements and upgrades to their two breweries.
The Impact:
According to Paul Murphy, Safety Manager for Long Trail and Otter Creek Breweries, "Implementing the injury and illness prevention program was like starting a separate company within the company. Its implementation had to be seamless and woven into the company's fabric." Mr. Murphy emphasized, "Unless there was buy-in from everyone in the company, it would not have been successful. Although there was a fair amount of reluctance at first, the company's entire culture and attitude towards workplace safety dramatically changed. Safety awareness now permeates every department in the company, right down to the sales force, who are required to sign a contract that prohibits talking on the phone while driving. As a result, most employees are reporting a much keener awareness of their safety outside the workplace as well." Murphy added, "And the impact can be felt on the bottom line as the capital investment in safety resulted in a more productive, more efficient, and healthier workforce."