New York On-Site Consultation Helps Reduce Exposures During Permit-Required Confined Space Entry
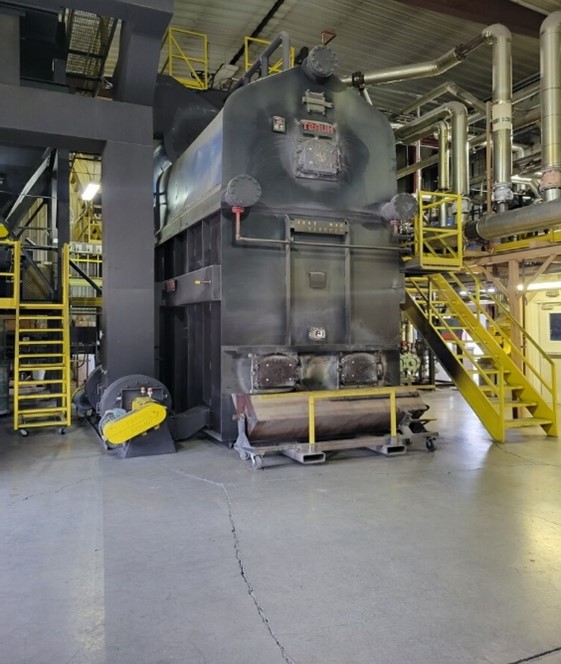
Wagner Hardwoods, LLC is a hardwoods sawmill in Cayuta, New York. It processes logs into dimensional lumber which it ships around the world. Approximately 130 employees work at the facility. The company has worked with the New York State Department of Labor’s On-Site Consultation Program for many years and entered the Safety and Health Achievement Recognition Program (SHARP) in 2009. It continues to be recognized as a SHARP participant. During this time, injury and illness rates have been reduced, identification and correction of hazardous conditions has occurred with the development of a solid safety and health management system, and the company has fostered a strong safety culture throughout the organization. Wagner often provides recommendations and guidance to other area sawmills for improving worker safety and health.
The company has a wood-fired boiler, which is used to provide steam for the facility’s kilns. Twice each year, company employees must perform permit-required confined space entry into the boiler’s combustion chamber for cleaning and inspection. The cleaning involves the manual removal of thick ash and soot deposits from the ceiling and walls of the chamber using shovels and scrapers.
During a January 2018 visit to the site, New York Consultation recommended that exposure monitoring be done on this operation. The exposure monitoring was performed in May 2018. Exposure controls used at the time of the January 2018 On-Site Consultation visit included:
- Permit-required confined space entry plan/procedures;
- A two-day cool down period for the boiler;
- The boiler’s induction fan was used to ventilate the inside the chamber;
- The overhead door to the boiler room was kept open to provide fresh makeup air;
- Carbon monoxide levels and temperature conditions inside the chamber were continuously monitored; and
- Personal protective equipment, which included hard hats, impact-resistant safety glasses, N95 filtering facepiece respirators, disposable coveralls, leather palm work gloves, and safety-toe work boots.
Initial air sampling performed by the On-site Consultation Program identified exposures to total particulate, magnesium oxide, manganese, and a mixture of other metal dusts above the OSHA permissible exposure limits (PELs) and a beryllium exposure above the OSHA Action Level.
Based on the air sampling results, the company:
- Increased the boiler cool-down period from two days to three days,
- Increased the ventilation rate in the boiler by a factor of three,
- Fabricated and used long-handled tools to remove the soot and ash as much as possible from the outside the space prior to entry, and
- Replaced the filtering facepiece respirators with continuous-pressure, full-face, supplied-air respirators.
Follow-up air monitoring, conducted by New York Consultation in October 2018, found that total particulate exposures dropped by approximately 65% with corresponding drops in metal exposures. While respirators were still needed, the full-face, supplied-air respirators provided a greater level of respiratory protection and eye protection than the half masks and safety glasses used previously. The new respirators also provide cooling to the wearers. Use of the long-handled tools helped speed up the cooling process and reduced the likelihood for injury due to hot, falling debris.
The lengthened cooldown period and increased ventilation rate dramatically reduced temperatures inside the space prior to entry, thereby eliminating the heat stress hazard. With those actions, together with the continuous air flow from the supplied-air respirators, employees indicated that they now feel cool or even cold when entering the space. Now, the cleanup can be performed during a single, one-hour entry, without need for break periods. This resulted in a 56% reduction in cleaning time and a corresponding reduction in employee exposure during the permit-required confined space entry.
OSHA On-Site Consultation Program offers no-cost and confidential occupational safety and health services to small and medium-sized businesses in all 50 states, the District of Columbia, and several U.S. territories, with priority given to high-hazard worksites. Consultants from state agencies or universities work with employers to identify workplace hazards and how to fix them, provide advice for compliance with OSHA standards, train and educate workers, and assist in establishing and improving safety and health programs. On-Site Consultation services are separate from OSHA enforcement efforts. To locate the OSHA On-Site Consultation program nearest you, call 1-800-321-OSHA (6742) or visit www.osha.gov/consultation.