Retail Store Chain: Lowering of Tractor Trailer Landing Gear
Company: Consultant report of an intervention at a major retail supermarket chain in the Northeast
Industry: Food/Beverage - NAICS 44511003. The retailer has 88 outlets and 12 distribution centers throughout the Northeast that will benefit from this intervention.
Task: Drop hook of tractor trailers 48 and 53 ft.
Employees: 400 drivers
Date: January 2016
Success Brief:
The landing gear must be lowered when separating a large trailer from the tractor that pulls it. This is typically done using a hand crank. This can be a stressful manual operation and has resulted in injury to the drivers. The manual cranking mechanism was replaced with an air operated automated system that requires only toggling an activation switch. The change eliminates injuries to the shoulders and back, from high force repetitive motion as well as from slipping and falling while manually cranking.
The Problem:
Drivers that manually raise and lower tractor trailer landing gears have increased potential for back and shoulder strain and other muscular-skeletal injuries because the operation requires them to repetitively bend and exert considerable force. These motions have led to tendonitis, and muscle strain of the shoulder as well as back injuries in the truck drivers. Typical operation of manually mechanism is shown in Figure 1. Notice the bent position of the body and the extension of the arms that puts stress on the back and shoulders. Typical manual operation requires 50+ revolutions of the crank handle at up to 100 ft.-lbs. of force. The torque required can also lead to slipping on icy surfaces and can cause injuries from falling.
There were approximately 9 injuries per year attributed to the manual cranking of the landing gear prior to the introduction of this intervention.
The Solution:
The company’s Transportation Safety Team (Cross functional team consisting of Operations Management, union drivers and mechanics, Risk Management, Human Resources and Logistics) strategized about methods to reduce injuries from deployment of the landing gear. The Safety manager had experience with an automated type of device from his previous employer and the team decided a test of this device was merited.
Originally, two test units were installed and used for a period of 6 months. Installation training and assistance was provided by the vendor. After installation, an on-site presentation was given to management and a core group of drivers, on proper operating procedures. Installation training was given to OEM installers at each installation location.
The pneumatic automation easily installs to an existing landing gear and uses an air driven motor, powered by the existing air system of the truck, to perform the operation of raising and lowering the landing gear. This eliminates the crank handle and requirement of manual force. The unit weighs only 20 lbs. and can be installed in less than 2 hours. As shown in Figure 2, a forceful two-handed operation requiring considerable effort and balance can now be done with two fingers.
Based on the success of this pilot an additional 100 units were installed and tested over a one year period. Full conversion of the entire fleet (700 trailers) to Air Powered Landing Gear Automation was accomplished in year 3.
The Impact:
The company considered this a successful intervention. Prior to implementation they routinely suffered about 9 injuries per year from the 400 drivers that perform this task. Incorporating this device has reduced that number to 0. Actual costs of injuries vary considerably depending on severity and body part injured. We do not have exact numbers from the company but the National Safety Council estimates that in 2011 the average cost of an injury was about $37,000 in both direct and indirect costs. The cost to outfit 700 trucks was about $1,400,000. Using these assumptions the return on investment (ROI) is less than 5 years.
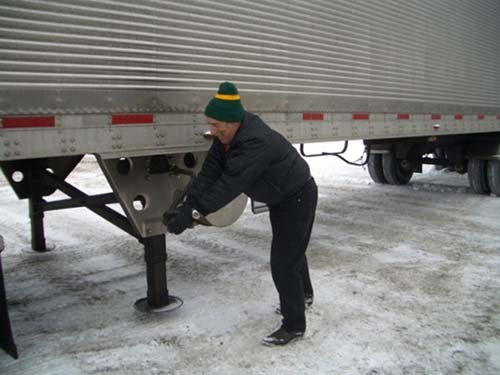
Figure 1 - Manual Cranking to lower the Trailer Landing Gear
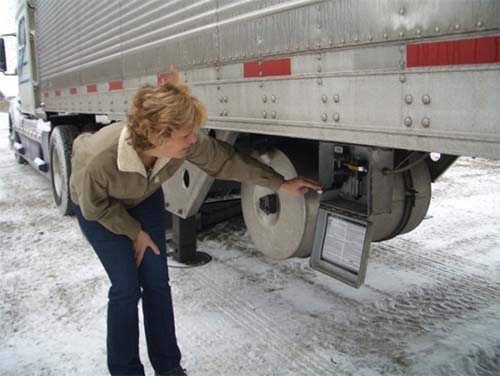
Figure 2 - Air activation allows the landing gear to be raised and lowered with a finger activated lever