Woodfold Manufacturing, Inc., Graduates from Oregon OSHA SHARP
Company: Woodfold Manufacturing, Incorporated
Location: Forest Grove, Oregon
Employees: 47
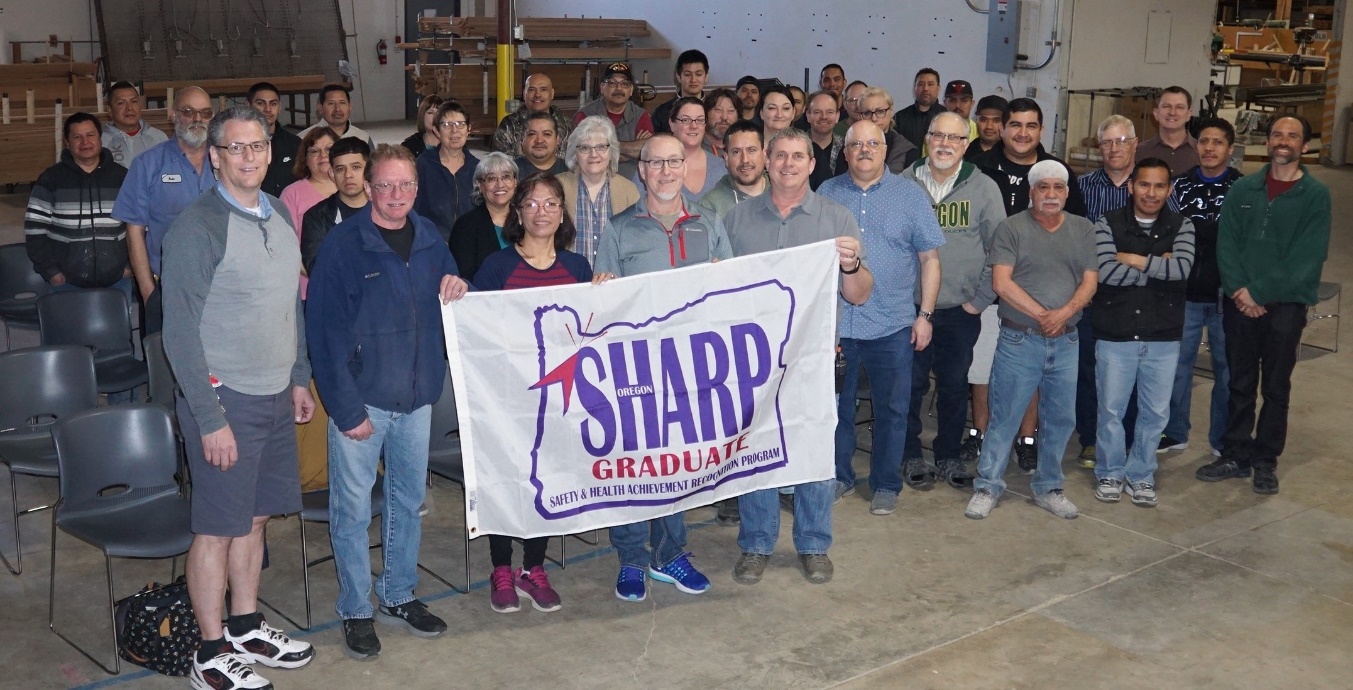
Woodfold Team with Oregon SHARP Flag
For Kevin Emerick, workplace safety is no mere box to be checked on a To-Do List. It is about people. It is about family. It is about sending members of your work family home safe after each and every workday.
“With the median tenure at our company at almost 25 years, we are family, and the last thing you want to see is someone in your family get hurt or worse,” said Emerick, risk manager for Woodfold Mfg., Inc., a Forest Grove, Oregon-based company that makes custom-crafted accordion doors, roll-up doors, and hardwood shutters. Woodfold was established in 1957. Since then, the company has grown into one of the nation’s leading suppliers for residential and commercial installations. Although times have changed, some things at Woodfold have not. At least, not the values that really make a difference to their customers and employees.
Since 1991, Woodfold has used Oregon Occupational Safety and Health (Oregon OSH), Consultation Services, to bolster its commitment to continuous improvement, which reflects its sense of itself as a family. More recently, though, the company – owned 100 percent by employees – decided to take its commitment to the next level by signing up for Oregon OSH’s Safety and Health Achievement Recognition Program (SHARP).
The company became aware of the federal Occupational Safety and Health Administration (OSHA), On-Site Consultation Program, in 1991. This program offers no-cost and confidential occupational safety and health services to small and medium-sized businesses in all 50 states, the District of Columbia, and several U.S. territories, with priority given to high-hazard worksites. On-Site Consultation services are separate from enforcement and do not result in penalties or citations. Consultants from state agencies, such as the Oregon OSH or universities, work with employers to identify workplace hazards, provide advice for compliance with OSHA standards, and assist in establishing and improving safety and health programs. The OSHA Safety and Health Achievement Recognition Program (SHARP) recognizes small business employers who have used OSHA On-Site Consultation Program services and operate exemplary safety and health programs. Acceptance of a worksite into SHARP from OSHA is an achievement of status that singles the company out among its business peers as a model for worksite safety and health.
Oregon Occupational Safety and Health, Consultation Services, has a 5-year program that identifies the strengths and weaknesses of employers’ safety and health management systems and empowers companies to become self-sufficient in managing on-the-job safety and health. Woodfold began the Oregon OSHA SHARP journey in early 2014, and it graduated from this program in 2019. Along the way, the company worked with Oregon OSH consultants to improve everything from machine guards and ergonomics to control of hazardous energy.
In taking on the challenge of SHARP, the company was taking a long-term view of the health and safety of its 47 workers. “I was looking for help in developing a safety management system that would give us a sustainable safety system that would continue on with or without me,” Emerick said.
Today, Woodfold stands as a proud Oregon SHARP graduate. The company did not just implement safety and health improvements. It also further burnished its reputation in the labor market as an employer who does the right thing. “Certainly,” Emerick continued, “anything we can do to position ourselves as an employer of choice is beneficial.”
Continuous improvement
Woodfold’s safety and health achievements as a SHARP company pile up like cordwood. That is not to say the process was easy.
Several pieces of custom equipment are used to enable the company to fashion custom-made products. This equipment posed machine-guarding challenges, but SHARP is all about removing obstacles and eliminating hazards. One of the most significant machine-guarding improvements was a cage the company built around the infeed and outfeed of a machine that has a moving bed that extends out from both sides. “Through on-site training from the SHARP consultants, we were able to come up with several machine-guarding improvements without compromising the functionality of the equipment,” Emerick said.
Woodfold tackled repetitive stress challenges, too. The material-handling demands of the company’s doors – which range in weight from 50 to 100 pounds – posed hurdles to helping employees avoid bodily wear and tear. Employees used to manually lift the doors up to inspection racks to slide them onto a track. Not anymore. “Now we have an in-ground lift that the employee stands on with the door, which raises the door to the necessary height to slide onto the rack,” Emerick said. The company did not stop there. “Downstream from this process, doors are placed into a box and lifted onto our packaging table,” Emerick said. “After much brainstorming, we came up with a pneumatic device that lays the boxed door onto the table – eliminating all lifting.”
Then, there were the company’s written lockout/tagout procedures. More than 200 of these procedures were updated. “We went through and audited every single machine and upgraded our instructions to include photos of the lockout points,” Emerick said.
All through the Oregon SHARP process, Woodfold did something else that is crucial to building a robust safety and health management system: It increased employee involvement. That included having employees drive the training program choices made by the company. “Additionally,” Emerick said, “our Safety Improvement Team [the company’s safety committee] has put in systems to annually review all of our data and establish goals and objectives for the next year.”
By the end of the company’s 5-year journey, Oregon OSHA’s consultants – Jeff Jackson, senior health consultant, and Michael Gordon, safety consultant – summed up the company’s status this way: “Woodfold is a model SHARP company.”
Caring for your family
To participate in SHARP, a company must have injury and illness rates below the national average. During the SHARP process, Woodfold put up model numbers. From 2014 through 2017, Woodfold's total recordable case (TRC) rate averaged 4.58, and their days away, restricted, and transferred (DART) rate averaged 1.08. During this period for NAICS code 321911, the Bureau of Labor Statistics reported that the industry average TRC rate was 4.68, and the industry average DART rate was 2.55.
According to Oregon OSHA’s report, these rates demonstrate effective controls of hazards because the company’s TRC and DART rates were below the national average for their industry. What’s more, the company’s Experience Modification Rate (EMR) is on a positive trajectory. This number – used by insurance companies to measure past injury costs and future risks – can have a sizable impact on a business’s workers compensation premiums. Woodfold recently learned that its EMR is 0.76, down 21 percent from 0.97 the previous year.
While Emerick certainly understands why the low workplace injury and illness numbers are important, he also knows what matters most: treating employees like family. “The toll an injury takes on the employee, their family, and friends is more important than just the financial cost,” he said. “A phrase we use often at Woodfold is ‘Everyone is someone’s son or daughter, and it’s our responsibility to look out for them as if they were our own son or daughter.’”
On-Site Consultation and SHARP are voluntary programs. To locate the OSHA On-Site Consultation Program nearest you, call 1-800-321-OSHA (6742) or visit www.osha.gov/consultation.
Source: Kevin Emerick, Risk Manager, Woodfold Mfg., Incorporated
Aaron Corvin, Public Information Officer, Oregon OSHA