Hazardous Waste Operations and Emergency Response (HAZWOPER)
Preparedness
Effective preparation is essential to conducting organized and thorough response operations in an emergency. Preparation before a potential hazardous substance release is critical to ensuring that employers and workers have the proper equipment, know where to go, and know how to stay safe and healthy in the event of an actual emergency. Employers with workers in operations subject to HAZWOPER must prepare and train their workers for hazardous substance emergencies and emergency response and cleanup activities.
OSHA's Role in Emergency Response
During the response to, and recovery from emergencies or disasters, OSHA helps protect the safety and health of response and recovery workers. In addition to enforcement and compliance assistance activities, OSHA can provide technical assistance and support to federal, state, local, tribal, territorial, and insular area agencies under the National Response Framework Worker Safety and Health Support Annex. The Getting Started – OSHA's Role in Emergency Response page provides additional information on this topic.
HAZWOPER Requirements for Distinct Categories of Operations
As discussed in the Background page, the HAZWOPER standard covers five distinct categories of work operations:
- Cleanup operations required by a governmental body involving hazardous substances conducted at uncontrolled hazardous waste sites;
- Corrective actions involving cleanup operations at RCRA-covered sites;
- Operations involving hazardous wastes at TSD facilities;
- Operations that generate hazardous waste but are not TSD facilities; and
- Emergency response operations involving releases of hazardous substances.
This section provides information on how HAZWOPER applies to each of these work operations, including the employer requirements and responsibilities for protecting workers performing tasks at these sites. The section outlines the key provisions of the HAZWOPER standard, including employer requirements, for each type of work operation that HAZWOPER covers, and describes how HAZWOPER requirements relate to employer and worker preparedness.
Workers in cleanup operations remove, contain, incinerate, neutralize, stabilize, process, or handle hazardous substances at uncontrolled hazardous waste sites to make the sites safe for people or the environment. Paragraphs (b)-(o) of HAZWOPER (Standards page) describe the employer requirements for operations where workers are engaged in the cleanup of uncontrolled hazardous waste sites. These include operations under the Comprehensive Environmental Response, Compensation, and Liability Act (CERCLA) of 1980, as amended, such as initial investigations at CERCLA sites before the presence or absence of hazardous substances is determined. Key provisions and employer requirements under paragraphs (b) – (o) of HAZWOPER are summarized below.
Plan
Safety and Health Program [29 CFR 1910.120(b)]
An effective and comprehensive safety and health program is vital to reducing work-related injuries and illnesses and maintaining a safe and healthy work environment. HAZWOPER requires each employer to develop and implement a written safety and health program (29 CFR 1910.120(b)) that identifies, evaluates, and controls safety and health hazards, and provides emergency response procedures for each hazardous waste site. Safety and health programs developed and implemented to meet other federal, state, or local regulations are acceptable in meeting this requirement, if they cover the topics required in (29 CFR 1910.120(b)). Essential elements of the safety and health program include:
- Worksite organizational structure,
- Comprehensive work plan,
- Site-specific health and safety plan (HASP),
- Safety and health training program,
- Medical surveillance program, and
- Standard operating procedures for safety and health
Worksite Organizational Structure [29 CFR 1910.120(b)(2)]
Establish a specific chain of command in the safety and health program and outline the overall responsibilities of supervisors and workers. At a minimum, include:
- A general supervisor with responsibility and authority to direct all hazardous waste site operations,
- A site safety and health supervisor with knowledge, responsibility, and authority to develop and implement the site-specific Health and Safety Plan (HASP) and verify compliance,
- All other personnel needed for hazardous waste site operations and emergency response and their general functions and responsibilities, and
- The lines of authority, responsibility, and communication, such as those involved in cleanup operations at the site and those who respond to emergencies.
Update this organizational structure routinely to reflect any changes in worker/supervisor status. There must be an organizational structure for each worksite.
Comprehensive Work Plan [29 CFR 1910.120(b)(3)]
Develop a comprehensive work plan describing the tasks and objectives of the worksite operations and the logistics and resources required to achieve those tasks and objectives. The plan must:
- Address anticipated cleanup activities as well as normal operating procedures,
- Define work tasks and objectives and identify the methods for accomplishing those tasks and objectives,
- Establish personnel requirements for implementing the plan,
- Provide for the implementation of worker training,
- Provide for the implementation of the required informational programs, and
- Provide for the implementation of the medical surveillance program.
Site-specific Health and Safety Plan (HASP) [29 CFR 1910.120(b)(4)]
Develop a site-specific HASP to address the safety and health hazards of the site operations, and include the requirements and procedures for worker protection. At a minimum, cover the elements described under paragraph (b)(4)(ii), including:
- Hazard analysis for each site task
- Employee training
- Personal protective equipment (PPE) to be used by employees based on hazard analysis
- Medical surveillance
- Exposure monitoring
- Site control measures
- Decontamination procedures
- Emergency response plan
- Confined space entry procedures
- Spill containment program
Keep a copy of the HASP on-site and make it always available and easily accessible for workers, contractors, or subcontractors who will be involved with the hazardous waste operation, as well as to OSHA personnel, and to personnel of any other regulatory agency with oversight, such as EPA.
The site safety and health supervisor or another knowledgeable individual must conduct inspections as necessary to determine the effectiveness of the site-specific HASP. Correct any deficiencies in the site-specific HASP promptly and update the copy kept on-site.
Some of the elements required in the HASP are also required as part of the overall safety and health program. The HASP can refer to standard operating procedures already developed as part of the safety and health program to avoid duplication in the HASP.
Site Characterization and Analysis [29 CFR 1910.120(c)]
Before workers enter the site, designate a qualified person to conduct a preliminary evaluation to identify hazards to which workers may be exposed and determine how to protect them using engineering controls, work practices, and PPE. Identify areas immediately dangerous to life and health (IDLH), areas that exceed published exposure levels defined in HAZWOPER 29 CFR 1910.120(a)(3), and areas that indicate exposure above radioactive dose limits.
Soon after workers initially enter the site, the qualified person must use the information gathered from the initial hazard analysis to further evaluate the site to better identify existing hazards and aid in the selection of appropriate controls. This detailed evaluation must include:
- The site's hazards, including the physical or chemical properties of hazardous substances and how workers could be exposed to the hazards,
- Worker health and safety risks associated with exposure to hazardous substances,
- Identification of potential sources, and locations of hazardous substances that may leak or spill
- Location, size, topography, and access to the site,
- What jobs/tasks workers do and how long it will take to accomplish them,
- Qualifications and capabilities of emergency response teams and approximate response times,
- PPE that workers need to conduct their jobs/tasks, and
- All suspected conditions that are immediately dangerous to life or health (IDLH) or that may cause serious harm to employees (e.g., confined space entry)
Site Control [29 CFR 1910.120(d)]
Establish site control procedures and safe practices to ensure worker protection from hazardous substances before cleanup work begins. The site control program must include the following:
- A map of the site that identifies contaminated areas,
- Clearly identified work zones that prevent unauthorized workers from entering contaminated areas and contain the contaminants,
- Written communications and safe work procedures for each work zone,
- Written procedures that address the use of the buddy system,
- Written procedures for warning and alerting workers about emergencies, and
- Identification of the nearest emergency medical responder/assistance
Training [29 CFR 1910.120(e)]
Ensure that workers know about the site hazards and the risk of potential exposure, how to recognize the hazards, what measures are in place to control hazards, and steps the worker can take to prevent or minimize exposures. See the Train section below.
Medical Surveillance [29 CFR 1910.120(f)]
Provide regular medical examinations and consultations for workers potentially overexposed to hazardous substances during work operations. For each worker, keep a record of the medical examination, including the worker's name and the physician's written opinion relating to the worker's ability to perform the required tasks or to wear a respirator. Table 2 outlines when medical examinations are required based on worker category.
Worker Category | When a Medical Exam is Required |
---|---|
|
|
Key points about the medical examination:
- Medical examinations and procedures shall be performed by or under the supervision of a licensed physician,
- Provide the physician with information about the worker's duties, exposure levels, and PPE, and
- Provide the worker with a copy of the physician's written findings.
Engineering Controls, Work Practices, and Personal Protective Equipment [29 CFR 1910.120(g)]
Control hazards according to the hierarchy of controls by first using engineering controls that "engineer" or physically change the work environment to reduce exposures to safe levels. When engineering controls are not sufficient, combine engineering controls with safe work practices, and as a last option, provide PPE to protect workers.
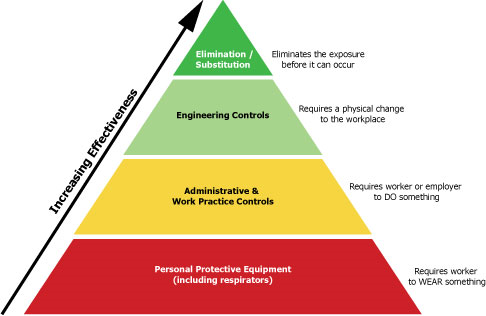
Engineering Controls: Examples include the use of pressurized cabs or control booths on equipment and remotely operated material handling equipment.
Administrative controls and Safe Work Practices: Examples include removing all non-essential workers from potential exposure while opening drums, wetting down work areas to prevent dusty conditions, and placing workers upwind of potential hazards.
PPE: If workers are required to use PPE (which includes respirators) during hazardous waste operations, ensure that the written program includes:
- Equipment selection procedures to protect workers against site-specific hazards,
- Proper equipment maintenance and storage procedures,
- Proof that workers understand the equipment's limitations,
- Proper equipment decontamination and disposal procedures,
- Procedures for training workers in using, wearing, and inspecting PPE,
- The importance of fit testing respirators for effective worker protection, emphasizing other PPE (e.g., goggles, safety glasses, hearing protection) should not interfere with the respirator fit and the PPE must not interfere with work assignments. Only respirators and hearing protection devices can be fit tested.
In an emergency response operation addressing unknown or IDLH atmospheres, use of a self-contained breathing apparatus (SCBA) is critical. See Appendix B of the HAZWOPER standard for SCBA requirements.
Non-mandatory Appendix B to HAZWOPER provides guidelines for selecting PPE and further discusses the levels of protection.
Monitoring [29 CFR 1910.120(h)]
Exposure monitoring quantifies the concentration of air contaminants in areas with potential worker exposure to hazardous substances. Personal sampling (or monitoring) measures individual worker exposures by sampling the air in their breathing zones. Area monitoring measures air contaminants in specific locations to estimate exposures affecting groups of workers. Monitoring is required during initial site entry and cleanup. Employers must establish a monitoring program applicable to conditions at the site. The program should briefly describe the monitoring objectives, the type of monitoring equipment that will be used, and how often monitoring will occur. The program must also specify the concentrations of airborne contaminants that will trigger reevaluation of the effectiveness of the site's engineering controls, safe work practices, and PPE. Table 3 summarizes HAZWOPER requirements relating to type and frequency of air monitoring.
When to Monitor | How to Monitor |
---|---|
At initial site entry (i.e., at uncontrolled hazardous waste sites), including when:
|
|
Periodically after cleanup phase of a hazardous waste operation begins, including when:
|
Informational Programs [29 CFR 1910.120(i)]
Ensure that workers and contractors know about the chemical, physical, and toxicological properties of the hazardous substances to which potential exposure may occur, before they begin work at the site. Provide information about the nature, level, and degree of exposure from performing hazardous waste cleanup operations. Typically, initial and refresher HAZWOPER training addresses this requirement. HAZWOPER does not cover workers who are working outside of the cleanup operations and have no reasonable possibility of exposure to safety or health hazards (e.g., clerical staff working on the periphery of the site).
Handling Drums and Containers [29 CFR 1910.120(j)]
If drums or containers on the site (i.e., buried or above ground) need to be moved, inspect them for leaks or signs that they may fail. Consider unlabeled containers as containing hazardous materials, until chemical sampling verifies that their contents are not hazardous. Always use explosion-resistant equipment to handle containers in flammable atmospheres.
Controlling leaks and spills. Train workers on procedures to contain leaks or spills and appropriate containment equipment. Provide salvage containers and absorbents at the site. Assess exposure risks prior to moving containers that show signs of weakness, bulging, or swelling, or containers that contain radioactive waste.
Opening hazardous waste containers. Use caution when opening containers with pressurized contents; open them from a remote location or use appropriate shielding. Workers not involved in opening such containers must keep a safe distance, or be protected by a suitable shield. Allow only specially trained workers to open laboratory waste packs.
Shock-sensitive waste. Consider unidentified laboratory waste or any laboratory waste pack with crystallized material on the outside as shock-sensitive. When handling shock-sensitive waste, first evacuate all non-essential workers from the area. Use an employee alarm system to signal the start and completion of explosive waste handling activities. Use handling equipment that has explosion-resistant shields or barriers. Handlers must keep continuous communication with the site's safety and health supervisor.
Decontamination Procedures [29 CFR 1910.120(k)]
Develop, implement, and communicate to workers decontamination procedures before they enter a hazardous waste site. Workers potentially exposed to hazardous substances must know how to decontaminate themselves and decontaminate or properly dispose of contaminated equipment, including PPE. Establish decontamination areas that will minimize the exposure of uncontaminated workers or equipment. Decontaminate, clean, maintain, or replace PPE to retain its effectiveness. Do not permit workers to launder contaminated clothing at home. Inform external laundry establishments of the hazardous nature of the laundry and the potentially harmful effects of the hazardous substances involved.
When a hazardous waste cleanup operation will take six months or longer to complete, provide workers with showers and change rooms that meet the requirements of OSHA's General Environmental Controls standard (29 CFR 1910.141, Subpart J; see also 29 CFR 1910.120(n)(7)). Workers must not remove their protective clothing or equipment from change rooms unless specifically authorized. In construction, 29 CFR 1926.65(k)(8) states that when decontamination procedures require a need for regular showers and change rooms outside of the contaminated area, they shall be provided and meet the requirements of 29 CFR 1910.141; 29 CFR 1926.65(k)(8) does not include the six-month time requirement.
Emergency response by employees at uncontrolled hazardous waste sites [29 CFR 1910.120(l)]
Develop a site-specific emergency response plan (ERP) as a separate section of the site HASP. The ERP must include:
- A description of anticipated emergencies at the site (pre-planning),
- The roles and authority of emergency personnel,
- Communication procedures used during emergencies,
- Procedures for reporting emergencies to local, state, and federal government agencies,
- Emergency zones, safe distances, and evacuation areas at the site,
- Security and control measures for emergencies,
- Site evacuation procedures and routes,
- Emergency response equipment available at the site,
- Procedures for medical treatment and first aid,
- Emergency decontamination procedures,
- Training required for workers who will respond to emergencies at the site,
- Criteria for evaluating the plan,
- Site topography, layout and prevailing weather conditions, and
- Procedures for reporting incidents to local, state, and federal government agencies.
Ensure that workers at the site know what to do during an emergency. If the ERP involves the use of a fire department during the response, ensure the fire department has the capabilities that are required to respond to the emergency (see 29 CFR 1910.120 Appendix C). It is also important to ensure that all response requirements and potential emergency situations are communicated and understood. If the fire department cannot provide appropriate services, find a responder that can. Coordinate the worksite ERP with state and local emergency response plans. Changes in work processes, equipment, and personnel require periodic review and rehearsal to ensure plan effectiveness.
Illumination [29 CFR 1910.120(m)]
Workers must have enough light to conduct their work safely. Table 4 provides the minimum illumination intensities in foot-candles for typical areas at hazardous waste operations.
Foot-candles* | Work Area |
---|---|
5 | General work areas |
3 | Excavation and waste areas, access ways, active storage areas, loading platforms, refueling, and field maintenance areas |
5 | Indoors: Warehouses, corridors, hallways, and exitways |
5 | Tunnels, shafts, and general underground work areas (Exception: minimum of 10 foot-candles is required at tunnel and shaft heading during drilling, mucking, and scaling. Mine Safety and Health Administration approved cap lights shall be acceptable for use in the tunnel heading.) |
10 | General Shops: such as mechanical and electrical equipment rooms, active storerooms, barracks or living quarters, locker or dressing rooms, dining areas, and indoor toilets and workrooms. |
30 | First-aid stations, infirmaries, and offices |
*The common measurement for Illumination is foot-candles. One foot-candle is the illumination produced by one candle at a distance of one foot. The most practical way to measure illumination is with a light meter. |
Sanitation at temporary workplaces [29 CFR 1910.120(n)]
Provide temporary worksites with a supply of drinking water that is stored in tightly closed and clearly labeled containers and equipped with a tap. Provide disposable cups and a receptacle for cup disposal. Clearly mark all water outlets that are unsafe for drinking, washing, or cooking. Also, equip temporary worksites with toilet and hand washing facilities. Sites that do not have sanitary sewers must have chemical, recirculating, combustion, or flush toilets. Provide locks on toilet doors controllable from the inside. Provide shower facilities and changing rooms at the site, if workers conduct cleanup work for at least six months and are potentially exposed to hazardous substances. Showers and change rooms must meet the sanitation requirements of 29 CFR 1910.141(d)(3) and 29 CFR 1910.141(e), General Environmental Controls, and must be located in areas with exposures below permissible exposure limits and published exposure levels. Workers must shower at the end of their work shifts or before they leave the site.
New Technology Programs [29 CFR 1910.120(o)]
Evaluate equipment with new technologies aimed at improving the protection of workers on worksites. Such equipment may include new foams, absorbents, adsorbents, and neutralizers used to decrease exposures. Evaluation is necessary to determine the effectiveness of worker protection before implementing new technologies on-site. Review manufacturer and supplier information as part of the evaluation.
Equip
Employers of emergency response and recovery workers are responsible for ensuring that their workers have and properly use personal protective equipment (PPE) when necessary. PPE can include respiratory protection, protective clothing, and protective barriers used to protect workers from exposure to chemical (including oil), biological, radiological and nuclear (CBRN) materials and other hazards. The selection of PPE is based on anticipated hazards and PPE selection may need to be modified as a result of monitoring and assessing actual working conditions. In planning for worker PPE needs, employers should consider the full range of a particular hazard a worker may experience (e.g., respirator cartridges suitable for both chemical and particulate exposures even if workers may only need protection from particulates most of the time).
Different types and levels of PPE may be used depending on the specific hazard or hazards present. PPE also may be needed to protect workers from other hazards, such as electric shock hazards or hazards associated with exposures to hazardous substances that may be encountered during emergency response and recovery operations.
The following are some of the important steps employers with emergency response and recovery workers, who may be affected by hazardous substances, need to take with respect to PPE:
- Conduct a hazard assessment to determine what safety and health hazards workers may encounter;
- Follow the hierarchy of controls—including elimination/substitution and engineering, work practice, and administrative controls—before relying on PPE to protect workers;
- Determine what PPE workers need;
- Provide the proper PPE to workers;
- Train workers in the proper use of PPE, including how to put it on and take it off correctly, and how to clean, maintain and dispose of it after or between uses;
- Ensure that PPE is used properly and whenever necessary;
- Provide medical exams and/or fit testing, as required by OSHA standards, prior to using certain types of PPE (e.g., respirators); and
- Regularly review and update the PPE program as hazards change.
It is crucial that employers plan in advance of an emergency for the PPE needs of their workers. During and immediately after an emergency, there may be limited supplies of PPE available for purchase, so it is important to have the necessary PPE on hand in advance. In an emergency situation, employers may have little or no time to train or fit workers (e.g., perform fit testing for respirators) for certain types of equipment, so it can be critical to have those tasks complete before an emergency occurs.
The HAZWOPER standard further requires the employer to develop a written PPE program for all workers involved in cleanup operations. This program is required under the overall safety and health program, and the HASP must include appropriate PPE specifications for workers in each of the anticipated site tasks and operations. The PPE program must include an explanation of equipment selection and use, maintenance and storage, decontamination and disposal, training and proper fit, donning and doffing procedures, inspection, in-use monitoring, program evaluation, and equipment limitations. Refer to OSHA standards for PPE General Requirements (29 CFR 1910.132/29 CFR 1926.95), Eye and Face Protection (29 CFR 1910.133/29 CFR 1926.102), Respiratory Protection (29 CFR 1910.134/29 CFR 1926.103), Head Protection (29 CFR 1910.135/29 CFR 1926.100), Foot Protection (29 CFR 1910.136/29 CFR 1926.96), Hand Protection (29 CFR 1910.138), and Occupational Noise Exposure (29 CFR 1910.95/29 CFR 1926.101) for more information on developing a PPE program.
In cleanup operations addressing unknown or IDLH atmospheres, use of a self-contained breathing apparatus (SCBA) is critical. See Appendix B of the HAZWOPER standard for SCBA requirements.
Non-mandatory Appendix B to HAZWOPER provides guidelines for selecting PPE and further discusses the levels of protection.
OSHA's Getting Started – PPE for Emergencies page provides information on PPE selection and use during emergency response and recovery operations.
OSHA and the National Institute for Occupational Safety and Health (NIOSH) have developed guidance on Chemical, Biological, Radiological, Nuclear (CBRN) PPE selection. The guidance includes PPE recommendations for CBRN-related emergency responders.
Train
A training program is required under the safety and health program and as part of the site-specific HASP (See 29 CFR 1910.120(b)(1)(ii)(C)). Provide training to all workers performing operations on the site, such as equipment operators, general site workers, and supervisors or managers potentially exposed to hazardous substances. Workers whose jobs/tasks put them at higher risk of exposure need more training than those who perform lower-risk jobs/tasks. Train workers to the highest level of responsibility you may assign them.
A 40-hour course is for workers who are exposed to hazardous materials above OSHA Permissible Exposure Levels (PELs) for which respiratory protection is required. A 24-hour course is for workers who have a temporary or short work task at a HAZWOPER site; no potential for exposure to hazardous substances or materials above the PEL exists; and no respiratory protection is required. An 8-hour HAZWOPER annual refresher is required for both the 40-hour and 24-hour HAZWOPER training designations. In addition, at least one person per work group must have the 8-hour supervisor training. Table 5 below provides a summary of the OSHA-required HAZWOPER training requirements for cleanup operation workers.
CLEANUP OPERATIONS | ||
---|---|---|
WORKER CATEGORY | INITIAL | ANNUAL (REFRESHER) |
General site workers who remove hazardous substances or engage in activities that may expose them to hazardous substances (e.g., heavy equipment operators, fire fighters, search and rescue personnel, general laborers, etc.). | 40-hour initial off-site instruction
24-hour supervised field experience |
8 hours |
Occasional on-site workers who have specific tasks with unlikely exposure above permissible exposure limits (e.g., groundwater monitoring, land surveyors, etc.). | 24-hour initial off-site instruction
8-hour supervised field experience |
8 hours |
Regular site workers who are regularly on-site in areas where exposures are below exposure limits but not exposed to health hazards. Emergencies are not likely. |
24-hour initial off-site instruction 8 8-hour supervised field experience |
8 hours |
Occasional and regular site workers who become general site workers. |
16-hour additional off-site instruction 16-hour additional supervised field experience |
8 hours |
Occasional and regular site workers required to wear respiratory protection. |
16-hour additional off-site instruction 16-hour additional supervised field experience |
8 hours |
On-site manager and supervisors who are directly responsible for, or who supervise, workers engaged in hazardous waste operations. |
40-hour off-site instruction 24-hour of supervised field experience 8 additional hours specialized training at the time of job assignment in employer's safety and health related programs |
8 hours |
On-site managers and supervisors of regular site workers without likelihood of exposure (e.g., equipment operators, general laborers, etc.) or occasional site workers (e.g., groundwater monitoring, land surveying, etc.). |
24-hour off-site instruction 8-hour supervised field experience 8 additional hours specialized training at the time of job assignment in employer's safety and health related programs |
8 hours |
The employer is responsible for ensuring that workers can apply their training to the conditions at the site. Workers must know about the site hazards to which they may be exposed, how to recognize the hazards, and how to control the hazards. The best approach for learning is through a combination of classroom instruction, site-specific information, and supervised field experience. Appropriately train workers before they begin their work and give them a written certificate of competency, without which they cannot begin work at the site.
Train workers on:
- The names of those responsible for worker safety and health at the site,
- The site's safety and health hazards and hazard controls,
- How to use PPE to control exposure,
- How to minimize exposure risks,
- Medical surveillance requirements,
- Procedures for decontaminating clothing and minimizing exposure to hazardous substances,
- Procedures for responding to emergencies,
- Procedures for working in confined spaces, and
- Procedures for containing leaks and spills of hazardous substances.
Workers engaged in operations involving hazardous waste TSD facilities regulated under 40 CFR Parts 264 and 265 pursuant to RCRA make up the second category of work operations covered by 29 CFR 1910.120(p). Key provisions and employer requirements under paragraph (p) of HAZWOPER are summarized below.
Plan
Safety and Health Program [29 CFR 1910.120(p)(1)]
Develop, keep onsite, and implement a written safety and health program for workers involved in hazardous waste operations. Identify, evaluate, and control safety and health hazards to protect workers and respond promptly to emergencies. The program should address, as appropriate, site analysis, engineering controls, maximum exposure limits, hazardous waste handling procedures, and uses of new technologies.
Safety and Health Program components (29 CFR 1910.120, Appendix C, compliance guidelines):
- Policy statements of the line of authority and accountability for implementing the program, the objectives of the program and the role of the site safety and health officer or manager and staff;
- Means or methods for the development of procedures for identifying and controlling workplace hazards at the site;
- Means or methods for the development and communication to employees of the various plans, work rules, standard operating procedures and practices that pertain to individual employees and supervisors;
- Means for the training of supervisors and employees to develop the needed skills and knowledge to perform their work in a safe and healthful manner;
- Means to anticipate and prepare for emergency situations and;
- Means for obtaining information feedback to aid in evaluating the program and for improving the effectiveness of the program. The management and employees should be trying continually to improve the effectiveness of the program thereby enhancing the protection being afforded those working on the site.
Hazard Communication [29 CFR 1910.120(p)(2)]
An effective hazard communication program is a key element required of TSD facilities. Develop a policy that meets the requirements of the Hazard Communication standard, 29 CFR 1910.1200, and ensures that workers know about chemical hazards at the worksite, and how to protect themselves from hazards. Develop and implement the program, ensuring that workers know about chemical hazards at the worksite and appropriate protective measures. Include provisions for proper labeling of chemicals, access to safety data sheets, and appropriate worker training. Hazardous wastes are specifically excluded from the Hazard Communication Standard and, therefore, do not have to be included in the TSD's Hazard Communication program, but the program should include potential worker exposure to other hazardous "non-waste" chemicals at the facility.
Medical Surveillance [29 CFR 1910.120(p)(3)]
Provide regular medical examinations and consultations for workers potentially overexposed to hazardous substances during their work. For each worker, keep a record of the medical examination, including the worker's name and the physician's written opinion relating to the worker's ability to perform the required tasks or to wear a respirator. Table 6 outlines when medical examinations are required based on worker category. See 29 CFR 1910.120(f).
Worker Category | When a Medical Exam is Required |
---|---|
|
|
Key points about the medical examination:
- Medical examinations and procedures shall be performed by or under the supervision of a licensed physician,
- Provide the physician with information about the worker's duties, exposure levels, and PPE, and
- Provide the worker with a copy of the physician's written findings.
Decontamination [29 CFR 1910.120(p)(4)]
Develop, implement, and communicate to workers decontamination procedures before they enter a hazardous waste site. Workers potentially exposed to hazardous substances must know how to decontaminate themselves, and decontaminate or properly dispose of contaminated equipment, including PPE. Establish decontamination areas that will minimize the exposure of uncontaminated workers or equipment. Decontaminate, clean, launder, maintain, or replace PPE to retain its effectiveness. Do not permit workers to launder contaminated clothing at home.Inform external laundry establishments of the hazardous nature of the laundry and the potentially harmful effects of the hazardous substances involved. See 29 CFR 1910.120(k).
When a hazardous waste cleanup operation will take six months or longer to complete, provide workers with showers and change rooms that meet the requirements of 29 CFR 1910.141, Subpart J – General Environmental Controls (see also 29 CFR 1910.120(n)(7)). Workers must not remove their protective clothing or equipment from change rooms unless specifically authorized.
New Technology Programs [29 CFR 1910.120(p)(5)]
Evaluate equipment with new technologies aimed at improving the protection of workers at worksites. Such equipment may include new foams, absorbents, adsorbents, and neutralizers potentially used to decrease exposures. Evaluation is necessary to determine the effectiveness of worker protection before implementing new technologies on-site. Review manufacturer and supplier information as part of the evaluation. See 29 CFR 1910.120(o).
Handling Hazardous Materials [29 CFR 1910.120(p)(6)]
If drums or containers on the site (i.e., buried or above ground) need to be moved, inspect them for leaks or signs that they may fail. Consider unlabeled containers as containing hazardous materials, until chemical sampling verifies that their contents are not hazardous. Always use explosion-resistant equipment to handle containers in flammable atmospheres. See 29 CFR 1910.120(j).
Controlling leaks and spills. Train workers on procedures to contain leaks or spills and appropriate containment equipment. Provide salvage containers and absorbents at the site. Assess exposure risks before moving containers that show signs of weakness, bulging, or swelling, or containers that contain radioactive waste.
Opening hazardous waste containers. Use caution when opening containers with pressurized contents; open them from a remote location or use appropriate shielding. Workers not involved in opening such containers must keep a safe distance or be protected by a suitable shield. Allow only specially trained workers to open laboratory waste packs.
Shock-sensitive waste. Consider unidentified laboratory waste or any laboratory waste pack with crystallized material on the outside as shock-sensitive. When handling shock-sensitive waste, first evacuate all non-essential workers from the area, Use an employee alarm system to signal the start and completion of explosive waste handling activities. Use handling equipment that has explosion-resistant shields or barriers. Handlers must keep continuous communication with the site's safety and health supervisor.
Worker Training [1910.120(p)(7)]
Ensure workers know about the site hazards and the risk of potential exposure, decontamination procedures, how to prevent and minimize exposures using engineering controls and PPE, medical surveillance procedures, and response procedures for emergencies. Provide workers initial and annual refresher training. The required hours of training vary for new workers, current workers, and trainers. See the Train section.
Emergency Response [1910.120(p)(8)]
Include an emergency response plan (ERP) in the written program that ensures workers know what to do during an emergency at the facility. Employers who will evacuate their workers from the worksite location when an emergency occurs and do not permit any of their workers to assist in handling the emergency are exempt from developing an ERP. They must develop an Emergency Action Plan (EAP), required by 1910.38(a), with procedures for immediate evacuation and train their workers accordingly. If workers will remain on-site during an emergency or assist in responding to an emergency, include the following elements in an ERP:
- Planning and coordination with outside parties,
- Personnel roles, lines of authority, and communication procedures,
- Possible emergencies and how to prevent them,
- Safe distances and places of refuge,
- Site control and security,
- Evacuation routes and procedures,
- Emergency decontamination procedures,
- Emergency medical treatment and first aid,
- Emergency communication procedures,
- Necessary emergency equipment, including PPE, and
- ERP evaluation criteria.
Train
TSD workers involved in hazardous waste operations are required to complete initial training for 24 hours and refresher training for 8 hours annually. OSHA requires that workers exposed to hazardous substances at TSD facilities receive HAZWOPER training as part of the site's safety and health program to ensure the ability to conduct assigned operations in a safe manner. The best way for workers to learn is through a combination of classroom instruction, site-specific information, and supervised field experience. Appropriately train workers before they begin their work and give them a written certificate of competency, without which they cannot begin work at the site. Table 7 presents a summary of HAZWOPER training requirements for TSD facility workers.
TREATMENT STORAGE AND DISPOSAL OPERATIONS | ||
---|---|---|
WORKER CATEGORY | INITIAL | ANNUAL REFRESHER |
New worker | 24 hour initial training | 8 hours |
Current worker | None required if previous work experience and training is equivalent to the 24-hour training for new workers | 8 hours |
Trainers | Satisfactory completion of a training course for subjects expected to teach and competent instructional skills | Retain competency for subjects expected to teach |
Many businesses generate hazardous waste as a by-product of their production operations, store it for a short time, and then send it to a TSD facility for treatment, storage, or disposal. EPA classifies hazardous waste generators as large quantity generators, small quantity generators, and conditionally exempt small quantity generators. Large quantity generators can accumulate hazardous waste for up to 90 days before shipping it to a TSD facility. Small quantity generators can accumulate hazardous waste for 180 days before shipping it to a TSD facility (270 days if the nearest TSD facility is more than 200 miles away).
Employers who are conditionally exempt small quantity (hazardous waste) generators and other (waste) generators that accumulate hazardous waste for less than 90 days are exempt from 29 CFR 1910.120(p)(1)-(p)(7) requirements, but must comply with the emergency response requirements in 29 CFR 1910.120(p)(8). Excepted employers have the option of evacuating their workers from the facility under (p)(8)(i) unless the EPA or a state agency requires that those workers perform emergency response (see 29 CFR 1910.120(a)(2)(iii)(B)).
If the employer or a government agency (e.g., EPA or a state agency) requires workers at the site to respond to emergencies in areas where hazardous waste is stored, the employer must comply with 29 CFR 1910.120(p)(8). However, in other areas of the facility with the potential for emergencies caused by uncontrolled releases of hazardous substances (e.g., production areas), employers must comply with the emergency response program requirements at 29 CFR 1910.120(q). Because complying with 29 CFR 1910.120(q) meets the requirements of 29 CFR 1910.120(p)(8), an employer may apply 1910.120(q) in both the storage areas and production areas.
Employers who will evacuate their workers from the worksite location when an emergency occurs and who do not permit any of their workers to assist in handling the emergency are exempt from developing an emergency response plan (ERP). They must develop an emergency action plan (EAP), required by 29 CFR 1910.38(a), with procedures for immediate evacuation, and train their workers accordingly. For more information, see "How to Plan for Workplace Emergencies and Evacuations" or 29 CFR 1910.120(p)(8)(i).
Hazardous Waste Generator | HAZWOPER Standard |
---|---|
Manufacturing Facility with potential for an emergency to occur due to uncontrolled release of hazardous substance or raw material. | 29 CFR 1910.120(q)
Addresses emergency response without regard to location |
Conditionally Exempt Small Quantity Generators/Generators who store hazardous waste for less than 90 days. | 29 CFR 1910.120(p)(8) |
Manufacturing Facilities with hazardous waste storage areas:
|
Either 29 CFR 1910.120(p)(8) or 29 CFR 1910.120(q) |
Manufacturing facilities with potential for an emergency to occur due to an uncontrolled release of hazardous substances must comply with 29 CFR 1910.120(q). See the Workers in Emergency Response Operations section of this page for a detailed description of these specific HAZWOPER requirements.
Hazardous waste storage areas within manufacturing facilities have the option of following 29 CFR 1910.120(q), because the remainder of the manufacturing site must follow these requirements. However, the hazardous storage area(s) of these sites can follow 29 CFR 1910.120(p)(8) requirements as outlined below.
Employers who are conditionally exempt small quantity (hazardous waste) generators under 40 CFR 261.5, and other waste generators who are qualified under 40 CFR 262.34 for exemptions ("excepted employers"), are exempt from complying with 29 CFR 1910.120(p)(1)-(7). These employers must follow the emergency response provisions under 29 CFR 1910.120(p)(8) as outlined below.
In an emergency response operation addressing unknown or immediately dangerous to life and health (IDLH) atmospheres, use of a self-contained breathing apparatus (SCBA) is critical. See Appendix B of the HAZWOPER standard for SCBA requirements.
Non-mandatory Appendix B to HAZWOPER provides guidelines for selecting PPE and further discusses the levels of protection.
Plan
Manufacturing facilities with hazardous waste storage areas, conditionally exempt small quantity generators, and generators storing hazardous waste for less than 90 days must follow 29 CFR 1910.120(p)(8) of HAZWOPER, which requires development and implementation of an ERP. The ERP must include the same minimum requirements that apply to TSD facilities. See Emergency Response under the TSD Facility Operations section of this webpage.
Train
Training for emergency responders in manufacturing facilities with hazardous waste storage areas, conditionally exempt small quantity generators, and generators storing hazardous waste must occur prior to actually participating in real emergencies. Training topics must include:
- Elements of the ERP,
- Procedures for handling emergencies,
- PPE necessary for emergencies, and
- How to recognize hazards that may endanger responders.
Employers are required to certify that each worker has successfully completed the initial training and maintain records of all worker names and training dates. A copy of the certificate must be provided to the worker.
If employers use the following for emergency response:
- The employer has trained a smaller number of workers to control emergencies, and all other workers know how to recognize emergencies, summon the trained responders, and evacuate the affected area, or
- A trained off-site team will respond promptly to an emergency, and on-site workers know how to recognize emergencies and summon the responders,
Then all other workers not included in the above items should be trained on evacuation procedures.
HAZWOPER does not require hazardous waste refresher training for small quantity generators. However, OSHA strongly encourages an annual refresher training class to ensure all facility workers remain competent in recognizing hazards and responding to them appropriately.
Paragraph (q) of the HAZWOPER standard covers workers engaged in emergency response operations for releases of, or substantial threats of releases of, hazardous substances without regard to the location of the hazard. After an emergency release, it is often necessary to transition from an emergency response operation to a hazardous substances cleanup operation. In such cases, post-emergency cleanup begins when the individual in charge of the emergency response declares the site under control and ready for cleanup. The HAZWOPER standard includes provisions for emergency response and post-emergency response cleanup operations. Key provisions and employer requirements under paragraph (q) of HAZWOPER are summarized below.
Plan
Emergency Response Plan [29 CFR 1910.120(q)(1)–(2)]
Prompt, effective responses to emergencies do not just happen, but require carefully prepared, well-rehearsed plans. All employers who respond to releases of hazardous substances, no matter where they occur, must have a written emergency response plan (ERP). Employers already following a local or state emergency response plan do not need to create another one; however, the plan must cover all of the basic and critical elements listed below.
Basic elements
- Pre-emergency planning and coordination with off-site responders,
- Personnel roles, lines of authority, and communication procedures,
- Possible emergencies and how to prevent them,
- Safe distances and places of refuge,
- Site control and security,
- Evacuation routes and procedures,
- Emergency decontamination procedures,
- Emergency medical treatment and first aid,
- Emergency communication procedures,
- Necessary emergency equipment, including PPE, and
- ERP evaluation criteria.
Critical elements
- Incident command system,
- Training,
- Medical surveillance,
- Chemical protective clothing, and
- Post-emergency response operations.
Procedures for handling emergency response [29 CFR 1910.120(q)(3)]
An incident command system (ICS) is a standardized on-scene incident management concept designed specifically to allow responders to adopt an integrated organizational structure equal to the complexity and demands of any single incident or multiple incidents without hindrance by jurisdictional boundaries. One person, the Incident Commander (IC), is responsible for managing emergency response at a site and directing the activities through a chain of command to those responsible for carrying out specific emergency response tasks. Responsibilities of the IC are:
- Identifying hazardous substances or conditions at the site,
- Designating a safety official, who knows emergency procedures at the site, to assist in identifying and evaluating hazards with authority to alter, suspend, or cancel emergency response activities in conditions immediately dangerous to life and health (IDLH),
- Enforcing ICS procedures and ensuring that responders wear appropriate PPE,
- Determining when responders can remove positive-pressure, self-contained breathing apparatus,
- Keeping others away from the site except those who are performing emergency operations, and
- Implementing appropriate decontamination procedures after emergency operations.
Training [29 CFR 1910.120(q)(4)-(6)]
Employers must appropriately train workers who will respond to an emergency before participation in an actual incident. Training for emergency responders depends on their job function during an emergency. See the Train section below.
Skilled support and specialist workers are covered in 29 CFR 1910.120(q)(4) and (q)(5) of HAZWOPER. 29 CFR 1910.120(q)(6) requires training and competencies for emergency responders and 29 CFR 1910.120(q)(7) specifies qualifications for trainers. 29 CFR 1910.120(q)(8) specifies refresher training requirements.
Medical surveillance and consultation [29 CFR 1910.120(q)(9) and 29 CFR 1910.120(f)]
Provide regular medical examinations and consultations for workers potentially overexposed to hazardous substances during work. Keep a record of the medical examination and include the worker's name and the physician's written opinion regarding the worker's medical fitness to work or to wear a respirator. Table 9 outlines when medical examinations are required based on worker category.
Worker Category | When a Medical Exam is Required |
---|---|
|
|
Key points about the medical examination:
- Medical examinations and procedures shall be performed by or under the supervision of a licensed physician,
- Provide the physician with information about the worker's duties, exposure levels, and PPE, and
- Provide the worker with a copy of the physician's written findings.
Chemical Protective Clothing [29 CFR 1910.120(q)(10) and 29 CFR 1910.120(g)(3)-(g)(5)]
Provide designated HAZMAT team members and hazardous materials specialists with the appropriate protective clothing and other necessary equipment. Follow 29 CFR 1910.120(g)(3)-(g)(5) of HAZWOPER. Chemical protective clothing ranges from items such as gloves and face shields to totally encapsulating chemical protective suits and provides four levels of protection. See Appendices A and B of the HAZWOPER standard for more details. If workers use chemical protective clothing, ensure the ERP provides instructions for the following:
- Selecting clothing to protect workers against site-specific hazards,
- Proper maintenance and storage of equipment by workers,
- Ensuring workers understand the equipment's limitations,
- Proper decontamination and disposal of equipment,
- Training workers to use, wear, and inspect the equipment, and
- Ensuring properly sized equipment to fit workers who use it.
Post Emergency Response Operations [29 CFR 1910.120(q)(11)]
After an emergency release, it is often necessary to transition from an emergency response operation to a hazardous substances cleanup operation. The HAZWOPER standard defines post-emergency response as that portion of an emergency response that follows stabilization or elimination of the immediate threat of a release, with cleanup of the site initiated. Activities related to stopping or securing the source of an oil spill are an example of "emergency response" activities under HAZWOPER. The shoreline cleanup of the spilled oil is a "post-emergency response operation." Post-emergency cleanup begins when the individual in charge of the emergency response—the IC—declares the site under control and ready for cleanup.
Two basic groups of workers perform the post-emergency cleanup:
- Off-site workers (i.e., workers from off the site, who are separate from the group providing the initial response); or
- On-site workers (i.e., workers of the site who were part of the initial emergency response where the emergency release occurred).
If a group of off-site workers performs the cleanup operation, then the separate group of workers are considered to be performing post-emergency response and subject to 29 CFR 1910.120(q)(11). The employer conducting the cleanup must comply with all the cleanup requirements in 29 CFR 1910.120(b)-(o), including training in accordance with 29 CFR 1910.120(e). The requirements under 29 CFR 1910.120(e) specify a minimum of 24 hours of initial off-site training or 40 hours of initial off-site training, depending on the worker category and exposure potential.
If on-site workers perform post-emergency response, HAZWOPER considers that part of the initial response and not post-emergency response. On-site workers who perform post-emergency cleanup on plant property are familiar with the types of hazardous substances on-site, site conditions, and methods to appropriately protect themselves from the related hazards. As a result, these workers do not need to be trained in accordance with 29 CFR 1910.120(e). However, the employer must comply with any additional training requirements under 29 CFR 1910.38(a), 29 CFR 1910.134, and 29 CFR 1910.1200, as well as other appropriate training for the anticipated tasks. If workers are involved in post-emergency cleanup operations after responding to an emergency, the written program must describe worker protections.
Workers who do not work at the facility where the release occurred, and who arrive after the emergency is declared over, must meet the requirements of 29 CFR 1910.120(b)-(o) and be trained in accordance with 29 CFR 1910.120(e). HAZWOPER designates the participation of these workers in the post-emergency cleanup as a hazardous waste site cleanup operation.
Emergency responders, trained in accordance with 29 CFR 1910.120(q)(6), who took part in the initial emergency response can continue working through the cleanup operation without any additional training.
Post-emergency oil spill cleanup operations
Based on oil spills off the Gulf Coast and the coasts of Alaska and California, the hazards to workers can vary widely in severity of potential injury or illness. For job duties and responsibilities with a low magnitude of risk (e.g., shoreline cleanup of tar balls), fewer than 24 hours of training may be appropriate for these post-emergency oil spill cleanup workers. The number of hours of training may vary based on the particular job and tasks an employee must perform. Moreover, oil spills are unique in that many people who assist in the cleanup operations may not engage in this activity on a recurring basis. In addition, for maximum protection of the environment, oil spills dictate completion of cleanup as soon as possible. OSHA stakeholders have requested flexibility in the amount of worker training required for petroleum spill cleanups and other types of cleanup operations that follow emergency situations. The OSHA booklet entitled "Training Marine Oil Spill Response Workers Under OSHA's Hazardous Waste Operations and Emergency Response Standard," written for marine oil spill response employers and workers, describes the training that employers must provide workers under HAZWOPER to protect workers involved in oil spill response and cleanup operations.
Train
Training for Emergency Response Workers
In accordance with OSHA's Hazardous Waste Operations and Emergency Response (HAZWOPER) standard, 29 CFR 1910.120, all responders who enter a hazardous area, including an area where a hazardous substance is present, must receive certain training. Federal OSHA does not cover state and local government workers. Emergency responders employed by state or local governments are covered by either OSHA approved State plans (which must have standards that are at least as effective as Federal OSHA standards) or by the EPA's HAZWOPER standard, 40 CFR Part 311. (The EPA adopts OSHA's HAZWOPER standard by reference).
For personnel responding to incidents involving hazardous materials and weapons of mass destruction (WMDs), the U.S. Department of Homeland Security (DHS) adopted National Fire Protection Association (NFPA) standards. NFPA 472, Standard for Competence of Responders to Hazardous Materials/Weapons of Mass Destruction Incidents, describes competency levels for personnel responding to such incidents, and NFPA 473, Standard for Competencies for EMS Personnel Responding to Hazardous Materials/Weapons of Mass Destruction Incidents, addresses basic life support and advanced life support personnel in the pre-hospital setting. Workers need proper training to be able to demonstrate these competencies.
For hospital, field, and triage medical personnel, the U.S. Department of Homeland Security (DHS), Federal Emergency Management Agency (FEMA), Hazardous Materials Emergency Preparedness (HMEP) Grant Program provides guidelines for hazardous materials response, planning, and prevention training. See HazMat Guidelines for Hazardous Materials Response, Planning and Prevention/Mitigation Training.
The training requirements for emergency response workers depend upon the job function and duties of the worker during the emergency operation. As delineated in 29 CFR 1910.120(q)(8), there are five distinct levels of training: the First Responder Awareness Level; First Responder Operations Level; Hazardous Materials Technician; Hazardous Materials Specialist; and On-Scene Incident Commander (IC) training.
First Responder Awareness Level: An initial amount of training is required to enable this responder to identify emergency releases and notify emergency response teams/authorities. An annual refresher is required.
First Responders Operations Level (respond defensively to prevent the spread of and exposures to the hazardous substances being released) must have at least 8 hours of training plus "awareness level" competency. The training for first responders at the operations level must enable them to respond defensively to contain the release from a safe distance, keep it from spreading, and prevent exposures. An annual refresher is also required.
Hazardous Materials (HAZMAT) Technicians (respond aggressively to stop the release) must have 24 hours of training equal to the "operations level" and know how to implement the employer's plan and carry out decontamination. An annual refresher is also required.
HAZMAT Specialists (respond with and in support of HAZMAT technicians) must have 24 hours of training equal to the "technical level" and specific knowledge of the hazardous substances. An annual refresher is also required.
On-Scene Incident Commander (IC) (assumes control of the scene) must have 24 hours of training equal to the "operations level" and demonstrate competence in implementing the ICS, the employer's plan, and the state and local emergency response plans. Training must include how to implement all applicable ERPs and controls and manage the incident. An annual refresher is also required.
The annual refresher training for each of the emergency responder types listed above must be of sufficient content and duration to maintain their competencies, or the worker must demonstrate competency in those areas at least yearly. Table 10 outlines the training requirements for emergency response workers discussed in this section.
EMERGENCY RESPONSE OPERATIONS | ||
---|---|---|
WORKER CATEGORY | INITIAL TRAINING | REFRESHER |
First Responder Awareness Level (Witnesses or discovers a release of hazardous substances and is trained to notify the proper authorities). | Sufficient training to identify emergencies and initiate the response process and additional competencies. | Annual |
First Responder Operations Level (Responds to the release of hazardous substances in a defensive manner, without trying to stop the release). | 8-hour instruction that includes First Responder Awareness or the equivalent relevant experience and additional competencies. | Annual |
HAZMAT Technician (Responds aggressively to stop the release of hazardous substances). | 24-hour First Responder Operations level training and additional competencies. | Annual |
HAZMAT Specialist (Responds with and in support of HAZMAT technicians, and has specific knowledge of various hazardous substances). | 24- hour HAZMAT Technician level training and additional competencies. | Annual |
Incident Commander (IC) (Assumes full control of the scene beyond the first responder awareness level). | 24-hour First Responder Operations level and additional competencies. | Annual |
In addition to the training levels established in HAZWOPER for emergency response workers, employers must also be aware of OSHA requirements for additional briefings and trainings that provide specific information and training for skilled support and specialist workers.
Skilled support personnel are workers needed to temporarily perform immediate emergency support work and operate certain equipment, such as mechanized earth moving or digging equipment, or crane and hoisting equipment. Provide skilled support workers with an initial safety and health briefing at the response site covering PPE use, the chemical hazards involved, and the anticipated tasks. Skilled support workers may require additional qualifications based on other OSHA standards. See 29 CFR 1910.120(q)(4).
Specialist employees are workers who in the course of their regular job duties, work with, and are trained in the hazards of specific hazardous substances. Specialist workers may provide specialized task and/or technical advice, or assistance at a hazardous substance release incident. Examples of specialized tasks requiring training are heavy equipment operation, electrical work, lockout/tag out, firefighting, and vehicle operation. Annual refresher training or demonstration of competency in their specialty is required. See 29 CFR 1910.120(q)(5).
Training for the trainers who teach any of the HAZWOPER training subjects includes completing a course on the subjects the instructor will teach, or holding training and/or academic credentials and instructional experience to demonstrate competent teaching skills. See 29 CFR 1910.120(q)(7).
Worker Training Documentation
Employers are required to provide training certification with some form of documentation for recordkeeping. Instructors must certify all workers who have successfully completed their required off-site training and present them with a written certificate See 29 CFR 1910.120(e)(6) and 120(q)(8)(ii).
Equip
Designated HAZMAT team members and hazardous materials specialists must be provided with the appropriate protective clothing and other necessary equipment. Furthermore, employers must ensure that paragraphs (g)(3)-(g)(5) of HAZWOPER are followed, which cover the requirements for PPE selection, totally encapsulating chemical protective suits, and the PPE program. (Note: see the previous discussion on PPE at 29 CFR 1910.120(g)).
In emergency response operations addressing unknown or IDLH atmospheres, use of a self-contained breathing apparatus (SCBA) is critical. See Appendix B of the HAZWOPER standard for SCBA requirements.
Non-mandatory Appendix B to HAZWOPER provides guidelines for selecting PPE and further discusses the levels of protection.
Employers of emergency response and recovery workers are responsible for ensuring that their workers have and properly use personal protective equipment (PPE) when necessary. PPE can include respiratory protection, protective clothing, and protective barriers used to protect workers from exposure to chemical (including oil), biological, radiological and nuclear (CBRN) materials and other hazards. The selection of PPE is based on anticipated hazards and PPE selection may need to be modified as a result of monitoring and assessing actual working conditions. In planning for worker PPE needs, employers should consider the full range of a particular hazard a worker may experience (e.g., respirator cartridges suitable for both chemical and particulate exposures even if workers may only need protection from particulates most of the time).
Different types and levels of PPE may be used depending on the specific hazard or hazards present. PPE also may be needed to protect workers from other hazards, such as electric shock hazards or hazards associated with exposures to hazardous substances that may be encountered during emergency response and recovery operations.
The following are some of the important steps employers with emergency response and recovery workers, who may be affected by hazardous substances, need to take with respect to PPE:
- Conduct a hazard assessment to determine what safety and health hazards workers may encounter;
- Follow the hierarchy of controls—including elimination/substitution and engineering, work practice, and administrative controls—before relying on PPE to protect workers;
- Determine what PPE workers need;
- Provide the proper PPE to workers;
- Train workers in the proper use of PPE, including how to put it on and take it off correctly, and how to clean, maintain and dispose of it after or between uses;
- Ensure that PPE is used properly and whenever necessary;
- Provide medical exams and/or fit testing, as required by OSHA standards, prior to using certain types of PPE (e.g., respirators); and
- Regularly review and update the PPE program as hazards change.
It is crucial that employers plan in advance of an emergency for the PPE needs of their workers. During and immediately after an emergency, there may be limited supplies of PPE available for purchase, so it is important to have the necessary PPE on hand in advance. In an emergency situation, employers may have little or no time to train or fit workers (e.g., perform fit testing for respirators) for certain types of equipment, so it can be critical to have those tasks complete before an emergency occurs.
OSHA's Getting Started – PPE for Emergencies page provides information on PPE selection and use during emergency response and recovery operations.
OSHA and the National Institute for Occupational Safety and Health (NIOSH) have developed guidance on Chemical, Biological, Radiological, Nuclear (CBRN) PPE selection. The guidance includes PPE recommendations for CBRN-related emergency responders.
Exercise
HAZWOPER Training Exercises
Workers tasked with responding to a release of hazardous substances must be trained according to their response role prior to participating in an actual incident. Train workers to know about the potential exposure hazards at the site, how to recognize the hazards, and how to control the hazards and prevent or minimize exposures. HAZWOPER training that provides hands-on experience through a combination of instruction in the classroom and on-site supervised training exercises provides the opportunity to become familiar with equipment and safe practices in a non-hazardous setting. Workers receiving supervised training in the field will have the opportunity to practice site-specific responses that they may later be required to perform during an emergency. Hands-on training will ensure that workers have an opportunity to learn by experience and to assess whether they have mastered the necessary skills prior to an actual incident.