Ergonomics
Training and Assistance
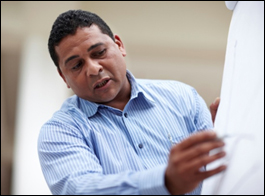
Training
Training is an important element in the ergonomic process. Training should be conducted in a language and vocabulary that all workers understand and is best provided by individuals who have experience with ergonomic issues in your particular industry. When training is effective workers will:
- Learn the principles of ergonomics and their applications.
- Learn about the proper use of equipment, tools, and machine controls.
- Use good work practices, including proper lifting techniques.
- Become more aware of work tasks that may lead to pain or injury.
- Recognize early symptoms of MSDs.
- Understand the importance of reporting and addressing early indications of MSDs before serious injuries develop.
- Understand procedures for reporting work-related injuries and illnesses, as required by OSHA's injury and illness recording and reporting regulation (29 CFR Part 1904).
Resources for Training
- Safe Patient Handling: Preventing Musculoskeletal Disorders in Nursing Homes. OSHA Publication 3708, (February 2014).
- OSHA's Directorate of Training and Education (DTE) provides training in a wide variety of occupational safety and health topics, including ergonomics. These training courses are delivered through the OSHA Training Institute (OTI) and the OTI Education Centers, which are located throughout the country. A schedule can be found on OSHA's Training Institute Education Center's Searchable Schedule page.
- Principles of Ergonomics Applied to Work-Related Musculoskeletal and Nerve Disorders, Course #2250. This course is offered to workers and employers to learn more about using ergonomic principles to recognize, evaluate and control work place conditions that cause or contribute to musculoskeletal and nerve disorders.
- Human Factors and Ergonomics Society Educational Resources tab, provides free resources, tips and links to education and training in the human factors/ergonomics (HF/E) field.
- Asian Immigrant Women Advocates. (2009). Developed basic ergonomic training materials through a Susan Harwood Grant from OSHA for workers in low-wage industries, such as dry cleaning, garment, packaging and food service. Training materials are available in English, Chinese and Korean.
- University of Louisville Research Foundation. (2008). Developed training materials for managers and workers in small business foundries through a Susan Harwood Grant from OSHA relating to the recognition, avoidance, and prevention of work related injuries. Materials include a student manual, and are available in English and Spanish.
- Restaurant Opportunities Centers United. (2009). Provided ergonomic training to workers and employers in small restaurants through a Susan Harwood Grant from OSHA. Training materials consist of three manuals. One manual is available in Spanish.
- Cal/OSHA Publications. Provides numerous outreach and training materials about ergonomics.
- Oregon OSHA: Ergonomics. Contains links to publications, resources and educational materials to reduce musculoskeletal injuries through outreach and the use of voluntary services. OR-OSHA offers a variety of ergonomics related services including conferences, on-site training, educational resources and consultation services to help Oregon employers implement solutions.
- Washington State Department of Labor and Industries: Sprains and Strains. Provides links to success stories, resources, tools and guidelines to help educate workers and employers on the importance of preventing ergonomic-related injuries and proper techniques they can use.
OSHA Help for Small and Medium Sized Businesses
OSHA offers the following cooperative programs under which businesses, labor groups and other organizations can work cooperatively with the Agency to help prevent ergonomic-related injuries.
- On-site Consultation Program offers free and confidential advice to small and medium-sized businesses in all states across the country, with priority given to high-hazard workstations. Consultants from state agencies or universities work with employers to identify ergonomic and other workplace hazards, provide advice on compliance with OSHA standards and assist in establishing safety and health management systems. For more information contact OSHA at 1-800-321-OSHA (6742).
- Safety and Health Achievement Recognition Program (SHARP). Worksites that receive SHARP recognition are exempt from programmed inspections during the period that the SHARP certification is valid.