Ammonia Refrigeration eTool
Receiving and Storage » Storage of Ammonia in Vessels
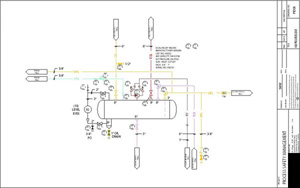
Sample piping and instrumentation diagram required by the Process Safety Management standard, 29 CFR 1910.119(d)(3)(i)(B), for a high pressure receiver.
In some installations, ammonia is refrigerated and stored in low-pressure tanks. If ammonia is stored inside, it is generally in a fire resistant structure, separated from work areas. It is important to keep storage areas dry and cool and away from steam pipes, heating devices, and tanks containing flammable liquids. Ammonia stored outside in an un-insulated tank must be painted with reflective paint, which controls rust or corrosion, and helps keep the temperature and internal pressure lower during hot weather.
Storing Ammonia in Vessels
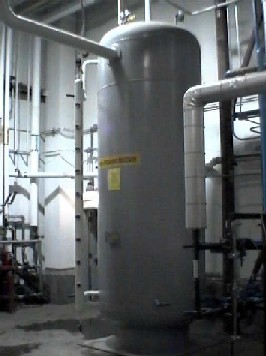
Potential Hazards
-
Release of ammonia as a result of vessel failure due to:
-
Improper design and installation (this can include improperly designed relief devices).
-
Thermal expansion or contraction.
-
Corrosion.
-
Overfilling.
-
External damage (for example, from a forklift).
-
Possible Controls
-
Provide information pertaining to the hazards of ammonia. [29 CFR 1910.119(d)(1)]
-
For additional information see Properties of Ammonia.
-
-
Design and install receiving/storage vessels according to generally accepted good engineering practices. [29 CFR 1910.119(d)(3)]
-
Ensure that Safety Relief Valves (SRVs) and relief systems for storage vessels are properly designed, installed in vapor space, and discharged to a safe location.
-
Place barriers around receiving and storage vessels and other equipment to protect them from impact.
-
-
Conduct a process hazard analysis. [29 CFR 1910.119(e)]
-
Provide Operating Procedures (29 CFR 1910.119(f)) to ensure proper operation of vessel, such as Standard Operating Procedures (SOP) and Technical Operating Specifications (TOS).
-
See an example of a High Pressure Receiver Vessel SOP.
-
See Guidelines for Writing Startup Procedures for additional information.
-
The International Institute for Ammonia Refrigeration (IIAR) recommends developing TOS that may include the following:
-
Desired operating ranges for temperature, pressure, level, flow, and so on.
-
Operating limits and consequences of deviation.
-
Pertinent alarms, instruments and controls and their set points.
-
Changes in operating controls and alarms during modes other than normal operation (start-up, shutdown, temporary operation, and so on.)
-
Safety devices associated with specific pieces of equipment or subsystems and their purpose and set-point(s).
-
-
-
Provide training specific to the operation of a receiver and storage vessel. [29 CFR 1910.119(g)]
-
Maintain proper oxygen and water content in vessels to avoid stress corrosion cracking (SCC) in welds of vessels.
-
-
Conduct a pre-startup safety review meeting prior to introducing ammonia when the equipment is new or modified significantly enough to require a change in the process safety information. [29 CFR 1910.119(i)]
-
Routinely inspect for corrosion of the receiving and storage vessel as part of a Mechanical Integrity Program. [29 CFR 1910.119(j)]
-
Develop written procedures to manually drain oil.
-
See the Oil Draining Guidelines listed in Additional Information below for procedures about safely draining oil from equipment.
-
-
According to IIAR Bulletin No. 110, maintenance for pressure vessels should include the following tasks performed on a weekly basis:
-
Check liquid level gauges for oil build up and drain if necessary.
-
Drain oil from vessel (only on vessels where the opportunity for continuous entrance of oil exists). Some systems will be equipped with an automated oil recovery scheme. For those systems it is not necessary to manually drain oil from the various vessels. It is however necessary that you periodically verify that the automated oil recovery system is functioning properly.
-
Inspect vessel and insulation for external appearance and note any departures from normal appearance in the system log. The conditions under insulated portions of the system should be inspected on a periodic basis.
-
Purge vessel of non-condensable gases. For those systems which operate under positive pressure, non-condensable gases are typically introduced during improper maintenance (failure to evacuate after opening the system) or improper charging procedures.
-
-
Ensure that draining and venting plugs, caps, and blind flanges are in place and closed.
-
Always pressure test any portion of the system opened for maintenance and before evacuation.
-
-
Issue a hot work permit for hot work operations conducted on or near the storage vessel. [29 CFR 1910.119(k)]
-
Establish and implement written procedures to manage changes to equipment, procedures, and facilities. [29 CFR 1910.119(l)]
-
Investigate incidents. [29 CFR 1910.119(m)]
-
Investigate accidents and near misses that could have resulted in a release of ammonia.
-
-
Establish and implement an emergency action plan in case of release. [29 CFR 1910.119(n)]
-
See Emergency Response for additional information.
-
Additional Information
-
Storage Vessel Design. Provides additional information by ASME, ANSI, IIAR, and ASHRAE about the design and installation of pressure vessels and associated equipment. [See the Table of Contents.]
-
Oil Draining Guidelines. International Institute for Ammonia Refrigeration (IIAR), (1996). Describes procedures for safely draining oil from equipment.
-
IIAR Process Safety Management Guidelines for Ammonia Refrigeration. International Institute for Ammonia Refrigeration (IIAR), (1998). Provides and overview of OSHA's Process Safety Management (PSM) Standard. [See the Table of Contents.]
-
Bulletin No. 110. Guidelines for Start-Up, Inspection, and Maintenance of Ammonia Mechanical Refrigerating Systems. International Institute for Ammonia Refrigeration (IIAR), (1993, March). Covers ammonia characteristics and hazards, inspection and maintenance of equipment, start-up issues, reference standards, safety equipment, and log book record-keeping. [See the Table of Contents.]