Powered Industrial Trucks (Forklift) eTool
Parts » Attachments
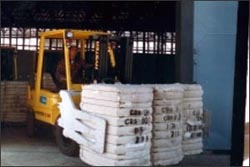
Powered industrial trucks often use various attachments in place of traditional forks. These attachments increase the versatility of the truck, but can present important safety considerations, including stability, capacity, and visibility.
Attachments
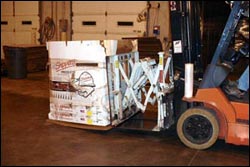
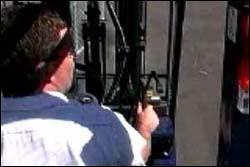
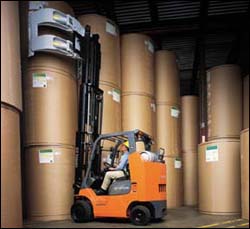
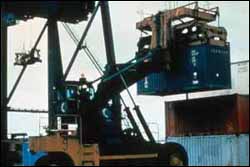
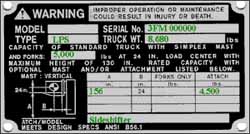
Some common attachments are:
-
Slipsheet attachments which avoid the use of pallets. (Figure 2)
-
Sideshifters shift the forks right and left. (Figure 3)
-
Container handlers designed to lift shipping containers.
-
Carton clamps equipped with a pressure valve to squeeze the load.
-
Cotton or pulp bale clamps that grab and hold bales.
-
Paper roll handlers.
-
Barrel clamps. (Figure 4)
-
Rotators that grab and rotate the load.
-
Extending or telescoping forks such as in reach and turret trucks. (Figure 5)
-
Personnel platforms specially designed for lifting personnel.
Operators must be trained in the proper use of attachments because they alter the performance of the forklift. Attachments affect the truck's performance by changing its center of gravity, visibility, and capacity.
Potential Hazards
-
Overloading. The weight of the attachment reduces the lifting capacity of the truck.
-
Tipover and falling loads. The attachment increases the load center by moving the load further away from the balance or fulcrum point.
Requirements
-
Train operators in the fork and attachment adaptation, operation, and use limitations. [29 CFR 1910.178(l)(3)(i)(G)]
-
Retrain an operator if a new attachment is added to the forklift. Consult the operator's manual for instructions on how to use the new equipment.
-
Do not exceed the rated capacity of the forklift/attachment combination.
-
Know the mechanical limitations of your forklift.
-
Change capacity, operation, and maintenance instruction plates, tags, or decals when a forklift truck is equipped with an attachment.
-
Treat an unloaded forklift with an attachment as partially loaded. [29 CFR 1910.178(o)(4)]
-
Include attachments in a scheduled maintenance and inspection program. Tailor inspection steps to the attachment.
-
Examine load-bearing components for deformation.
-
Examine load-bearing welds for cracks.
-
Inspect mechanical and hydraulic components and maintain in accordance with the manufacturer’s instructions.
-
-
If the truck is equipped with front-end attachments other than factory installed attachments, request the truck be marked to identify the attachments and show the approximate weight of the truck and attachment combination at maximum elevation with load laterally centered. [29 CFR 1910.178(a)(5)]
-
Modifications or additions that affect capacity or safe operation shall not be performed without prior written approval from the forklift truck manufacturer. Capacity, operation, and maintenance instruction plates, tags, or decals shall be changed accordingly. [29 CFR 1910.178(a)(4)]
-
If no response or a negative response is received from the manufacturer, written approval of the modification/addition from a qualified registered professional engineer is acceptable. A qualified registered professional engineer must perform a safety analysis and address any safety or structural issues contained in the manufacturer’s negative response before granting approval. The forklift nameplates must be changed accordingly.
-
See Forklifts: Free Rigging Requires Manufacturer's Approval, OSHA Standard Interpretation, (October 22, 1999). Free rigging is the direct attachment to or placement of rigging equipment (slings, shackles, rings, etc.) onto the forks of a powered industrial truck for a below-the-forks lift. This type of lift does not use an approved lifting attachment. Although free rigging is a common practice, it could affect the capacity and safe operation of a powered industrial truck.
-